Daniel Aichinger
Process Engineering Lead at PBF Energy- Claim this Profile
Click to upgrade to our gold package
for the full feature experience.
Topline Score
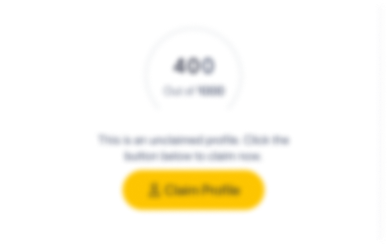
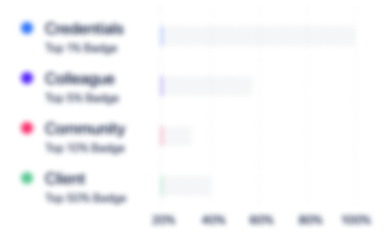
Bio


Experience
-
PBF Energy
-
United States
-
Oil and Gas
-
700 & Above Employee
-
Process Engineering Lead
-
Mar 2019 - Present
-
-
-
Philadelphia Energy Solutions, LLC
-
Architecture and Planning
-
100 - 200 Employee
-
Process Engineer
-
May 2015 - Mar 2019
FCC/LSG/Sulfuric Alky June 2017 - Present -FCC - 50,000 BPD KBR Resid* Unit -LSG - 70,000 BPD Exon Scanfiner Unit -Alky - 8,500 BPD Stratco Sulfuric Acid Unit Reformer/HDS/UDEX/Cumene May 2015 - June 2017 -Reformer - 40,000BPD Fixed Bed UOP Platformer -HDS - 30,000BPD Distillate Unit making 15MV1 -UDEX - 20,000BPD TTEG Unit -Cumene- 12,000BPD Exon/Badger Unit FCC/LSG/Sulfuric Alky June 2017 - Present -FCC - 50,000 BPD KBR Resid* Unit -LSG - 70,000 BPD Exon Scanfiner Unit -Alky - 8,500 BPD Stratco Sulfuric Acid Unit Reformer/HDS/UDEX/Cumene May 2015 - June 2017 -Reformer - 40,000BPD Fixed Bed UOP Platformer -HDS - 30,000BPD Distillate Unit making 15MV1 -UDEX - 20,000BPD TTEG Unit -Cumene- 12,000BPD Exon/Badger Unit
-
-
-
bp
-
United Kingdom
-
Oil and Gas
-
700 & Above Employee
-
Process Design Engineer
-
Jan 2013 - Apr 2015
• Process Design Area Lead for $400 Million Major Capital Project in Front End Engineering Design (FEED) phase for first-of-its-kind technology.• Led design efforts to scale up technology to commercial levels (18 million gallons per year).• Participated in Process Technology reviews and development of 3 patentable process technologies.• Provided assurance and direction to contractor and supplier/vendor teams in the development of $65 million worth of FEED deliverables. Challenged contractor and BP technological and engineering design to optimize capital and operating costs.• Eliminated $300,000+ worth of unnecessary equipment costs.• Championed and developed Risk Management philosophy and process for BP Highlands Ethanol and Lignocellulosic Brazil projects.• Worked with Design Engineers and Technology teams to develop over 100 Project Risks and created Excel tool to highlight risk profiles more effectively. Delivered Risk Updates to Leadership teams.• Developed fully integrated ASPEN+ Process model for first-of-its-kind Major Capital Project for use in process/mechanical designs and to insure overall technology optimization.• Saved $200,000+ through development and implementation of SharePoint based project action tracking utility to consolidate all project actions into unified web accessed portal.• Assisted in the Vivergo Fuels commissioning and startup (110 MMGY wheat to ethanol plant located in Hull, UK). Show less
-
-
Biofuels Challenger - Process Design
-
Jun 2012 - Jan 2013
-
-
-
ExxonMobil
-
Oil and Gas
-
700 & Above Employee
-
Research Associate Co-op
-
Sep 2010 - Mar 2011
Researched engine oil improvements by generating and analyzing data to be used in oil property performance models. Performed multiple industry quality tests on various personally blended formulations, which were sampled over time to determine oil composition. Determined oil composition through Gas Chromatography–Mass Spectrometry (GC-MS) and developed automated MatLab GC-MS analysis program to aid in analysis. Researched additive packs to prolong life of engine oil, which resulted in possible patentable discovery. Show less
-
-
-
Hovensa
-
Virgin Islands, U.S.
-
Oil and Gas
-
100 - 200 Employee
-
Operations Engineering Co-op
-
Sep 2009 - Mar 2010
Assisted Operations Engineering Group to improve unit monitoring and optimization by developing calculations for key unit parameters. Developed software that enhanced visual display of key plant parameters, such as hydrogen to feed ratios, hydrogen consumption, heat exchanger monitoring, and electronic load shed warning system. Participated in FCC Turn-a-round (plant shut down, maintenance and restart). Assisted Operations Engineering Group to improve unit monitoring and optimization by developing calculations for key unit parameters. Developed software that enhanced visual display of key plant parameters, such as hydrogen to feed ratios, hydrogen consumption, heat exchanger monitoring, and electronic load shed warning system. Participated in FCC Turn-a-round (plant shut down, maintenance and restart).
-
-
-
Sunoco LP
-
United States
-
Oil and Gas
-
700 & Above Employee
-
Energies and Utilities Co-op
-
Sep 2008 - Mar 2009
Developed energy reduction initiatives with Energy Engineer by conducting a comprehensive optimization study on production versus energy usage of distillation towers, boilers, and heaters. Developed energy reduction initiatives with Energy Engineer by conducting a comprehensive optimization study on production versus energy usage of distillation towers, boilers, and heaters.
-
-
Education
-
Drexel University
Master's degree, Chemical Engineering
Community
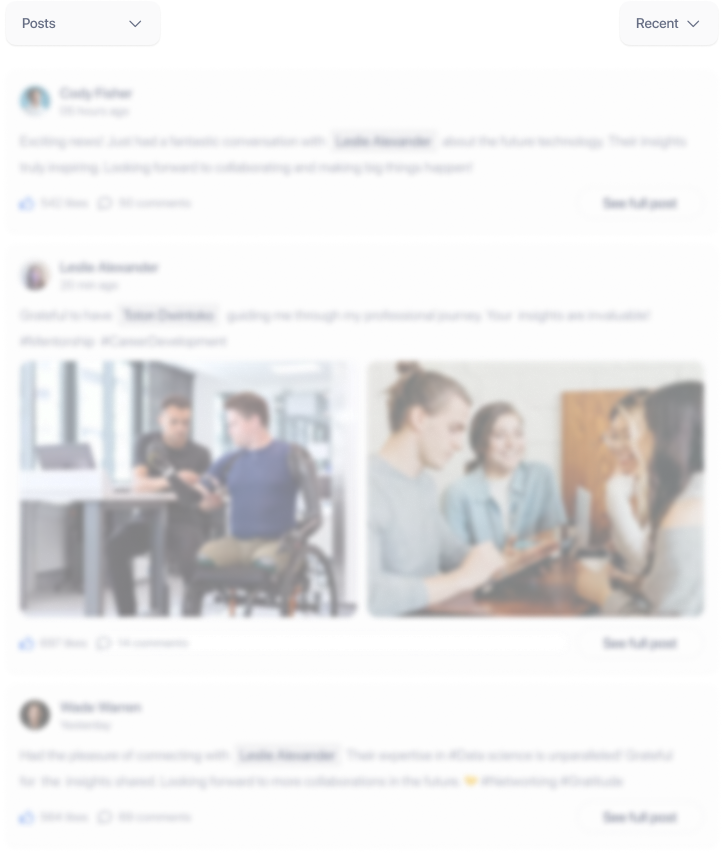