Dael Eller
Operations Manager at Goodness Gardens, Inc- Claim this Profile
Click to upgrade to our gold package
for the full feature experience.
Topline Score
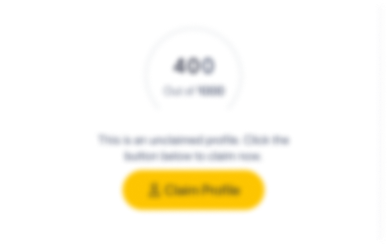
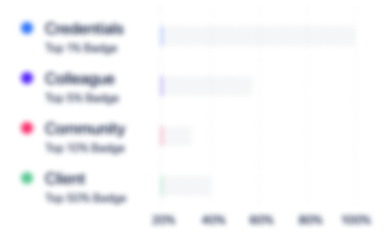
Bio


Experience
-
Goodness Gardens, Inc
-
United States
-
Food and Beverage Manufacturing
-
1 - 100 Employee
-
Operations Manager
-
Feb 2023 - Present
United States -Operate activities of multiple facilities across the country. -Formulate operational strategies to boost facility-wide efficiency and productivity. -Ensure adherence to regulatory and safety standards. -Coordinate with sales, marketing, and finance teams for seamless interdepartmental collaboration. -Manage budgets for all operations, optimizing cost-effectiveness. -Administer inventory and supply chain systems, sustaining efficient operations. -Nurture relationships with… Show more -Operate activities of multiple facilities across the country. -Formulate operational strategies to boost facility-wide efficiency and productivity. -Ensure adherence to regulatory and safety standards. -Coordinate with sales, marketing, and finance teams for seamless interdepartmental collaboration. -Manage budgets for all operations, optimizing cost-effectiveness. -Administer inventory and supply chain systems, sustaining efficient operations. -Nurture relationships with suppliers for timely material delivery. -Mentor a diverse team of managers and supervisors. -Use Lean Six Sigma to optimize production and eliminate wasteful practices. -Lead continuous improvement initiatives throughout manufacturing operations. -Implement robust quality control metrics for product consistency and customer satisfaction. “DPMO” -Conduct facility construction improvements & projects. -Enforce policies and procedures for consistent performance across facilities. -Design employee training programs to foster technical and leadership skills. -Analyze performance metrics for continual improvement and corrective action. -Manage tracking and reporting systems for key performance indicators. -Participate in long-term strategic planning. -Conduct risk assessments and develop mitigation strategies.
-
-
Production Manager
-
Sep 2021 - Feb 2023
New Hampton, New York, United States - Led a team of 150+ employees across all departments in a plant, achieving improved efficiency, quality, waste reduction, and consistency using lean six sigma principles such as the DMAIC methodology. - Developed key performance indicators and dashboards for operations departments, utilizing linked software applications to set new goals and create a positive financial impact across all facilities. - Implemented data collection systems to gather metrics and measurements of performance… Show more - Led a team of 150+ employees across all departments in a plant, achieving improved efficiency, quality, waste reduction, and consistency using lean six sigma principles such as the DMAIC methodology. - Developed key performance indicators and dashboards for operations departments, utilizing linked software applications to set new goals and create a positive financial impact across all facilities. - Implemented data collection systems to gather metrics and measurements of performance, conducting business data analysis and planning using Microsoft Excel. - Maintained continuous communication in Portuguese, English, and Spanish to ensure success. - Established effective training and development programs for employees, utilizing mentoring and Individual Development Plans. - Utilized Business Management software tools such as Produce Pro, NetSuite, and Paychex for process planning and strategy formulation. - Monitored the process flow and project implementation, handling employee promotions, demotions, recruitments, and terminations. - Updated safety procedures in line with OSHA guidelines and ensured that company policies and legal procedures were followed. - Enforced systems, procedures, and policies, while also handling customer concerns requiring managerial intervention.
-
-
Production Supervisor
-
Feb 2020 - Sep 2021
New Hampton, New York - Managed and directed a team of over 100 employees engaged in production activities, ensuring timely completion and quality output. - Coordinated production planning and scheduling meetings to ensure smooth operations. - Facilitated effective communication in English, Spanish, or Portuguese to achieve project success. - Conducted training sessions on 5S and GMP for the company's management team, resulting in certification and improved work environment. - Utilized various Business… Show more - Managed and directed a team of over 100 employees engaged in production activities, ensuring timely completion and quality output. - Coordinated production planning and scheduling meetings to ensure smooth operations. - Facilitated effective communication in English, Spanish, or Portuguese to achieve project success. - Conducted training sessions on 5S and GMP for the company's management team, resulting in certification and improved work environment. - Utilized various Business Management software such as Production Pro, NetSuite, Spindle, and Paychex for process planning and strategy development. - Monitored and controlled process flow and project implementation for efficient and effective production. - Conducted employee recruitment and termination as necessary while adhering to company policies and legal procedures. - Implemented and enforced systems, procedures, and policies for optimal production operations. - Managed customer concerns that may require escalation to ensure customer satisfaction.
-
-
Production Coordinator
-
Sep 2020 - Feb 2021
New Hampton, New York, United States - Developed and maintained production schedules based on sales forecasts, demand, and available resources. - Analyzed and evaluated inventory levels to ensure adequate materials and supplies were available for production. - Collaborated with customer service to ensure timely delivery of products to customers. - Prioritized the scheduling of production runs based on changing demands and available resources. - Monitored production processes to ensure adherence to schedule and quality… Show more - Developed and maintained production schedules based on sales forecasts, demand, and available resources. - Analyzed and evaluated inventory levels to ensure adequate materials and supplies were available for production. - Collaborated with customer service to ensure timely delivery of products to customers. - Prioritized the scheduling of production runs based on changing demands and available resources. - Monitored production processes to ensure adherence to schedule and quality standards. - Implemented and maintained production metrics and KPIs (key performance indicators) to track progress and identify areas for improvement. - Communicated regularly with the production manager and other departments to ensure effective planning and coordination of production activities. - Worked with project managers to plan and coordinate production runs for seasonal and holiday products. - Continuously sought out opportunities to improve production efficiency and reduce costs.
-
-
Production Lead (Planning)
-
Oct 2019 - Sep 2020
New Hampton, New York, United States
-
-
Production Lead (Labeling)
-
Oct 2018 - Oct 2019
New Hampton, New York, United States
-
-
Machine Operator
-
Dec 2016 - Oct 2018
New Hampton, New York, United States
-
-
Case packer
-
Sep 2016 - Dec 2016
New Hampton, New York, United States
-
-
-
-
Foreign Exchange Trader
-
Feb 2020 - Present
United States
-
-
Education
-
Harvard Business School
Financial Accounting, Complete -
Villanova University
Lean Six Sigma Black Belt, Complete -
Harvard Business School
Leadership Principles, Complete
Community
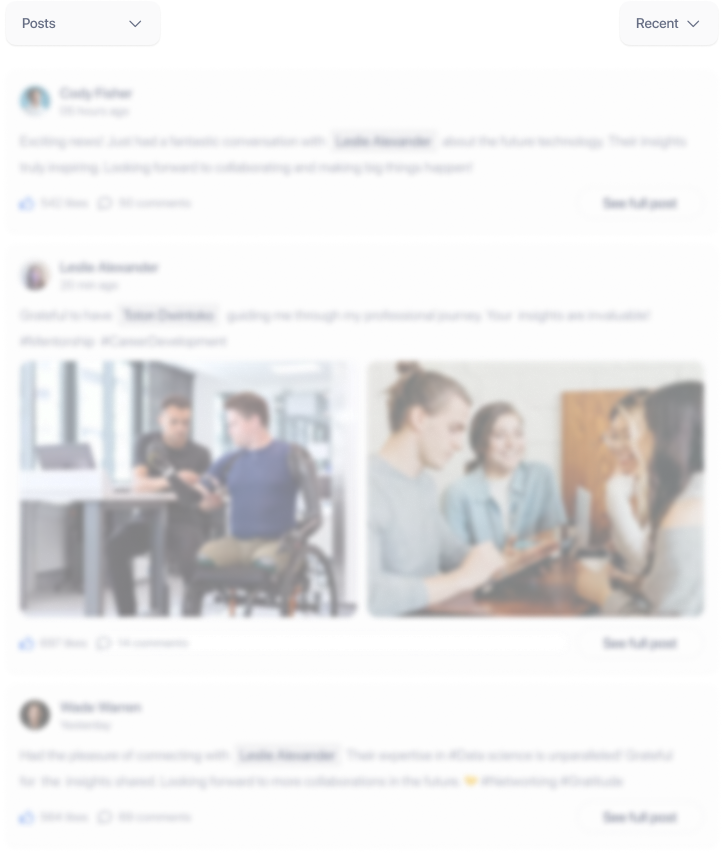