D.J. Gosch
Vice President of Operations at American Natural Processors- Claim this Profile
Click to upgrade to our gold package
for the full feature experience.
-
English -
-
Spanish -
-
German -
Topline Score
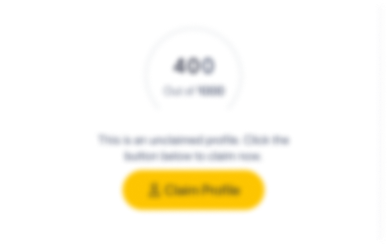
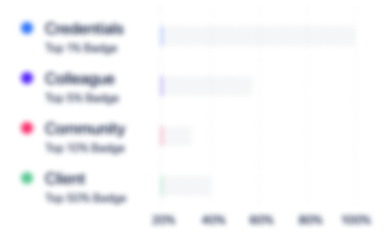
Bio


Credentials
-
HACCP Certified
-
Experience
-
American Natural Processors
-
United States
-
Food Production
-
1 - 100 Employee
-
Vice President of Operations
-
May 2021 - Present
-
-
-
Daybreak Foods, Inc.
-
United States
-
Food and Beverage Manufacturing
-
100 - 200 Employee
-
General Manager
-
Jun 2019 - Jun 2020
In this role, I provided strategic and tactical leadership holding full P&L accountability for Live Production, Further Processing, and Milling on an agricultural egg-production site. I executed, monitored, and drove processes, structures, and procedures to optimize and enhance work environment, and food safety, along with ensuring audit compliance. I also drove delivery of cost-efficiency through effective planning and management of labor, resources, and purchasing. Managed ethical animal husbandry practices, including cage density, barn mechanical condition and repair, humane euthanasia, feed, air, light, and water delivery. I maintained UEP and SQF certification. ➠ Inherited a site that had been without GM for over a year and was performing under par with low morale across the workforce. Transformed confidence and productivity by improving communications, reengaging teams, and more effectively tapping into talent. ➠ Defined, and steered implementation of initiatives that resulted in driving the site’s TRIR to zero, 50% reduction in NRs received, and a 100 SQF audit score (Level II). ➠ Delivered $1M+ in controllable cost-savings in first year, through labor, efficiency, yield, and purchasing improvements. Show less
-
-
-
Rembrandt Foods
-
United States
-
Food and Beverage Manufacturing
-
100 - 200 Employee
-
Sr. Director of Operations
-
Jun 2016 - May 2019
Here, I steered operations across 3 live sites with breaking plants and 3 processing facilities, along with holding responsibility for company Safety and Engineering departments. I held full accountability for P&L safety/food safety, labor utilization, yield performance, audit compliance, purchasing, maintenance, warehousing, and schedule management. Additionally, I managed a budget of $250M and led a team of 9 direct reports consisting of 3 site ops managers, 3 plant managers, an Offline Cage-Free Manager, a director of EHS, and a director of engineering. ➠ Steered implementations, management, and monitoring of processes, policies, and procedures to ensure all live operations sites adhered to ethical and humane animal husbandry practices and maintenance of outside certifications such as HFAC. ➠ Defined and steered implementation of initiatives that resulted in a 65% reduction in TRIR, 69% reduction in number of safety incidents, and significantly improved NRs received and SQF audit scores. ➠ Delivered over $10MM in controllable cost savings through labor, efficiency, yield, and purchasing improvements. ➠ Drove enhanced communication, transparency, and accountability, strengthening employee engagement along with championing improved work conditions and payment, resulting in a turnover reduction from 75% to 33%. Show less
-
-
-
Boulder Brands
-
Food & Beverages
-
1 - 100 Employee
-
Sr. Director of Operations
-
May 2014 - Jun 2016
Here, I was recruited to steer margin growth of the gluten-free group that included the largest gluten-free bakery in the U.S. I oversaw a budget of $150M, and a capital budget of $10M. Help responsibility for P&L, safety, quality, and productivity. I also led the development of strategies and initiatives to drive productivity and profitability. Additionally, I guided optimization of cost-efficiency and operational effectiveness across all areas and functions, including safety, food safety, labor utilization, yield performance, audit compliance, purchasing, maintenance, finished goods transfer, warehousing, and schedule attainment. ➠ Made multiple critical decisions to reform and rebuild management team, including replacing the maintenance manager leading to a 65% reduction in downtime and onboarded and new HR Manager resulting in a decrease in temp labor and turnover. ➠ Led renegotiation of contracts with external vendors and suppliers, including securing a 25% reduction in freight costs. ➠ Steered a 15% reduction in labor costs by conducting extensive analysis of labor to determine opportunities to improve labor utilization, along with reducing temporary labor reliance by 79%. ➠ Succeeded in achieving 20%+ improvement of TRIR for 2 consecutive years. Show less
-
-
-
Perdue Farms
-
United States
-
Food and Beverage Manufacturing
-
700 & Above Employee
-
Logistics Manager / Business Unit Leader
-
Oct 2005 - May 2014
In this position, I steered logistics for all the Coleman Natural Foods, free-range organic chicken, slaughter, package, and direct store delivery. I managed company employed drivers, company-owned truck, and trailers, and a 240K sq. ft distribution center. ➠ Captured a 42% cost-reduction for power electrical truck leases, by negotiating and entering a contract with a new equipment leasing company. ➠ Slashed contract freight expenses by bringing in new carriers to compete for routes resulting in a 33% reduction in costs. ➠ Steered reduction in labor costs by 60% while increasing lbs./mnhe in the Distribution Center by 25%. ➠ Reduced rental trailer fleet by 58% and eliminated all rental cargo storage containers, saving over $32K annually. Direct responsibilities included transportation/distribution functions across three sites; including safety, food safety, labor utilization, audit compliance, fleet purchasing, fleet maintenance, live haul, chick delivery, feed delivery, powered industrial truck purchasing and maintenance, and product distribution. Show less
-
-
-
Pilgrim's
-
United States
-
Food and Beverage Manufacturing
-
700 & Above Employee
-
Regional Planning Manager
-
Dec 2012 - Apr 2013
While in this role I was responsible for the planning, scheduling, and procurement of dry goods for three facilities within the region. ➠ Improved the correct and timely utilization of raw materials, led a project to eliminate excess trailer inventory, and implemented controls creating accurate daily inventories across 3 poultry processing plants. While in this role I was responsible for the planning, scheduling, and procurement of dry goods for three facilities within the region. ➠ Improved the correct and timely utilization of raw materials, led a project to eliminate excess trailer inventory, and implemented controls creating accurate daily inventories across 3 poultry processing plants.
-
-
-
Rembrandt Foods
-
United States
-
Food and Beverage Manufacturing
-
100 - 200 Employee
-
Operations Manager
-
May 2012 - Dec 2012
I was directly responsible for running all aspects of the 2nd shift of production for an egg processing facility which included dried whites, yolks, and whole egg, as well as liquid extended shelf life product packaged in bladders, totes, cartons, and tankers. ➠ Drove Improvement of GMP and Safety compliance through policy enforcement across liquid and dried egg production operations. I was directly responsible for running all aspects of the 2nd shift of production for an egg processing facility which included dried whites, yolks, and whole egg, as well as liquid extended shelf life product packaged in bladders, totes, cartons, and tankers. ➠ Drove Improvement of GMP and Safety compliance through policy enforcement across liquid and dried egg production operations.
-
-
-
Dakota Provisions
-
United States
-
Food and Beverage Services
-
1 - 100 Employee
-
Plant Manager
-
Apr 2010 - May 2012
➠ Drove Improvement of GMP and Safety compliance through policy enforcement across further-processed meat production operations, including fully cooked, slicing, dicing, and whole lobe production. ➠ Successfully brought 3 new production lines online and lead the plant through a 100% increase in volume. ➠ Dramatically enhanced efficiency and productivity through executing various initiatives, including the redesign of the further processing area, increasing efficiency by 50%. ➠ Reduced start-up downtime on the RTE side of the plant by 66%, and the RTE headcount by 5%. ➠ Delivered cost savings initiatives over $2M. Show less
-
-
Education
-
Simpson College
German and History / Business Management -
University of Phoenix
Business Management, 3.87 GPA
Community
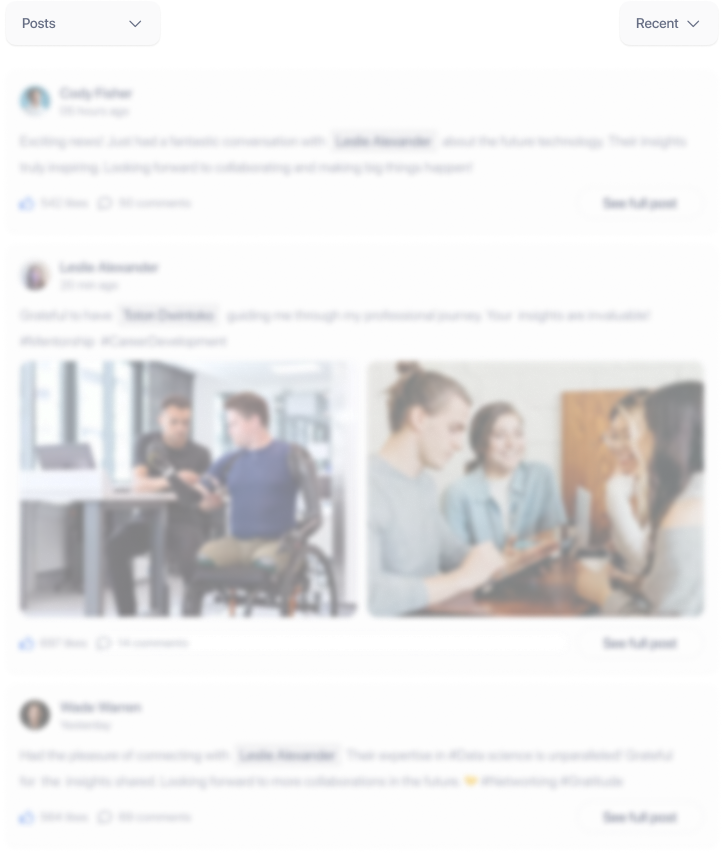