Crystal Taylor
Quality Control Service and Claims Manager at BlueScope Coated Products- Claim this Profile
Click to upgrade to our gold package
for the full feature experience.
Topline Score
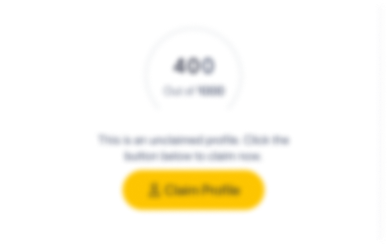
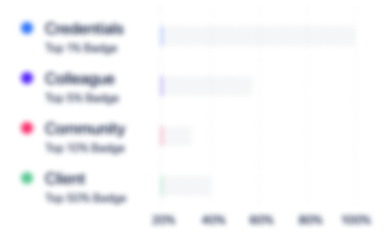
Bio


Experience
-
BlueScope Coated Products
-
Chemical Manufacturing
-
1 - 100 Employee
-
Quality Control Service and Claims Manager
-
Aug 2023 - Present
-
-
Quality Control Manager
-
Oct 2018 - Sep 2023
Provides leadership and oversight for a team of eight quality associates: two quality engineers, three quality control technicians, and three visual inspectors.Successfully reduced open customer complaints by 45% and increased time to closure from 90 days to less than 30 days.Administers the Quality Assurance and Technical Service requirements of BlueScope Coated Products; ensures product quality meet or exceed customer expectations via thorough audit and testing procedures and protocols.Analyzes KPI variables to diagnose chronic problems that result in poor quality, yield loss and field rejections of finished products.Develops and implements corrective actions to eliminate non-conformities or field rejections.Responsible for ensuring compliance for all aspects of the Quality Management System as well as ISO 9001 certification.Schedule project tasks and leads all APQP projects for new customers and products.Provides daily communication with operations and customer experience staff to ensure all customer orders are complete and accurate.Accesses critical resource needs: created new hourly position, Senior QC Lab Technician, to supply additional quality support across all shifts to aide in real-time problem resolution, job efficiency and training.Assesses contractor bids and confirm reasonable pricing; provide end to end support on the review and approval process of submitted bids/quotes for remediation.Leads customer facing review meetings, develop materials and presentations on quality performance metrics and corrective actions. Show less
-
-
-
Inalfa Roof Systems North America
-
United States
-
Motor Vehicle Parts Manufacturing
-
100 - 200 Employee
-
Senior Quality Engineer
-
May 2016 - Oct 2018
Maintained IAFT 16949 quality management system standards and achieved satisfactory status via rigorous testing and validation of quality controls and checkpoints Provided oversight of product quality and integrity to ensure complete customer satisfaction Served as primary OEM customer contact for FORD Motor Company and managed all programs activities Analyzed defective material rejected during manufacturing process to identify corrective action plans Managed new product introductions, PPAP approvals, and product quality performance Maintained all quality documentation including control plans, PFMEAs, and work instructions Implemented process improvements that resulted in a 50% improvement in customer scorecards Increased quality awareness throughout the organization, resulting in an 80% reduction in PPM over one year. Show less
-
-
-
The HON Company
-
United States
-
Furniture and Home Furnishings Manufacturing
-
300 - 400 Employee
-
Continuous Improvement Engineer
-
Jun 2012 - May 2016
Achieved $1M in cost savings through the reduction of scrap Simultaneously led multiple rapid quality continuous improvement project teams in new product and process implementation. Managed team members to ensure achievement of clear and measurable goals. Developed and conducted simulations to analyze production processes, collecting and analyzing data to identify ways to optimize processes and reduce costs Led five-member team responsible for implementing cost saving process changes Optimized materials and information flows resulting in a 10% reduction in waste Show less
-
-
-
MasterBrand, Inc.
-
United States
-
Wholesale Building Materials
-
700 & Above Employee
-
Manufacturing Quality Engineer
-
Feb 2008 - Jun 2012
Managed engineering quality at four sites throughout the U.S. Managed quality auditors across two shifts: collected internal and external quality data to identify and resolve inefficiencies and problems in the manufacturing process Improved production efficiency through the modification of machine setup, process steps, the implementation of new manufacturing processes, and the optimization of floor space Developed and managed project budgets and calculated manpower requirements Coordinated Kaizen events for staff and trained staff in Lean and Six Sigma principles and processes Led cross-functional teams in completion of $500K multi-facility expansion on time and within budget Reduced off-line processes by 20%, improving assembly efficiency by 10% Show less
-
-
Education
-
The University of Alabama
Bachelor of Science - BS, Industrial Engineering -
The University of Alabama
Bachelor of Science - BS, Industrial Engineering
Community
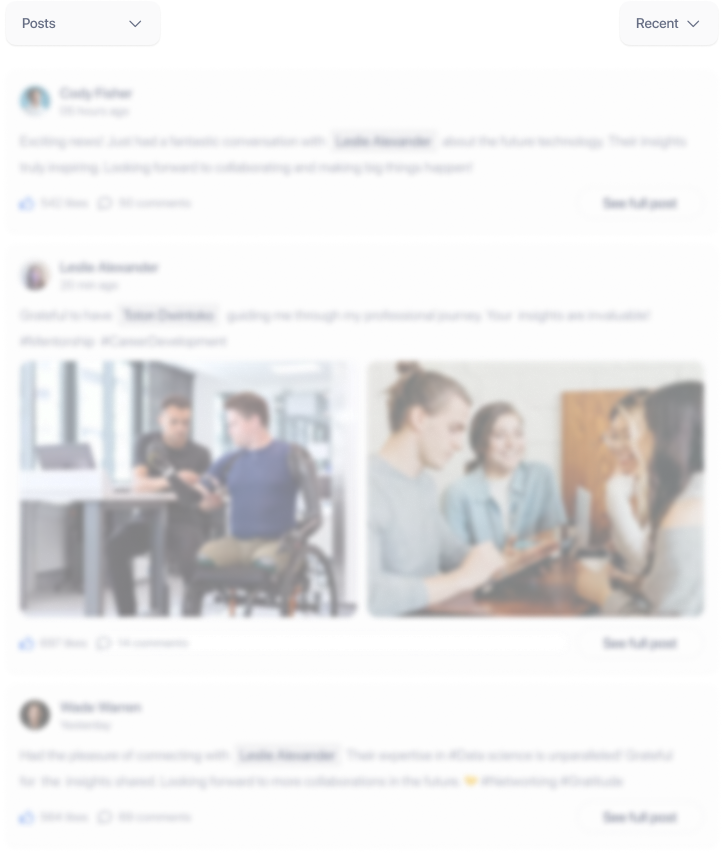