
Craig Lockman
Director of Quality, Safety & Continuous Improvement at Pindel Global Precision, Inc.- Claim this Profile
Click to upgrade to our gold package
for the full feature experience.
Topline Score
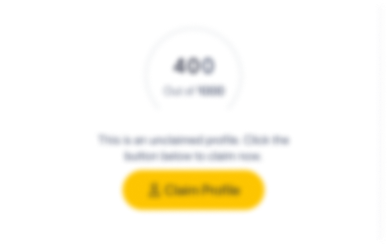
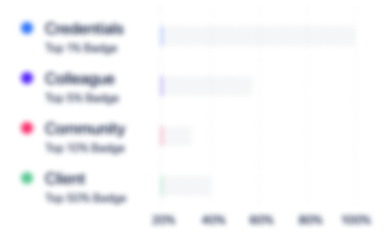
Bio

Joseph Montalto
I had the opportunity to work with Craig Lockman during my time at Adaptive MicroSystems. During this time I was the Director of Operations and worked indirectly with Craig in our continous improvment drive to "Manufacturing Excellence" within the company. Even through the challenging times of changing a culture, Craig always moved forward with a positive attitude and combining that with his knowledge led us on the path to success. It is with great pleasure that I write this recommendation to an individual who played a vital role in assisting in the success of our efforts. Joseph Montalto V.P. of Operations

Joseph Montalto
I had the opportunity to work with Craig Lockman during my time at Adaptive MicroSystems. During this time I was the Director of Operations and worked indirectly with Craig in our continous improvment drive to "Manufacturing Excellence" within the company. Even through the challenging times of changing a culture, Craig always moved forward with a positive attitude and combining that with his knowledge led us on the path to success. It is with great pleasure that I write this recommendation to an individual who played a vital role in assisting in the success of our efforts. Joseph Montalto V.P. of Operations

Joseph Montalto
I had the opportunity to work with Craig Lockman during my time at Adaptive MicroSystems. During this time I was the Director of Operations and worked indirectly with Craig in our continous improvment drive to "Manufacturing Excellence" within the company. Even through the challenging times of changing a culture, Craig always moved forward with a positive attitude and combining that with his knowledge led us on the path to success. It is with great pleasure that I write this recommendation to an individual who played a vital role in assisting in the success of our efforts. Joseph Montalto V.P. of Operations

Joseph Montalto
I had the opportunity to work with Craig Lockman during my time at Adaptive MicroSystems. During this time I was the Director of Operations and worked indirectly with Craig in our continous improvment drive to "Manufacturing Excellence" within the company. Even through the challenging times of changing a culture, Craig always moved forward with a positive attitude and combining that with his knowledge led us on the path to success. It is with great pleasure that I write this recommendation to an individual who played a vital role in assisting in the success of our efforts. Joseph Montalto V.P. of Operations

Credentials
-
ASQ Certified Quality Auditor
ASQ - World Headquarters
Experience
-
Pindel Global Precision, Inc.
-
United States
-
Automation Machinery Manufacturing
-
1 - 100 Employee
-
Director of Quality, Safety & Continuous Improvement
-
Dec 2018 - Present
-
-
-
Liberty Precision Manufacturing Technologies
-
United States
-
Defense and Space Manufacturing
-
1 - 100 Employee
-
Director of Quality, Safety and Continuous Improvement
-
Dec 2020 - Present
-
-
-
PRODx - Production Expediting Technologies
-
United States
-
Automation Machinery Manufacturing
-
1 - 100 Employee
-
Director of Quality, Safety and Continuous Improvement
-
Feb 2021 - Present
-
-
-
CTDI
-
United States
-
Telecommunications
-
700 & Above Employee
-
Quality and Safety Manager
-
May 2018 - Nov 2018
As a member of the management team, in charge of ensuring quality of refurbished set top boxes (STB), cable modems, and safety of employees. CTDI has over 14,000 employees throughout more than 90 locations worldwide with the headquarters located in West Chester, PA. • As part of the initial branch start-up management team created, coordinated and implemented start-up and quality actions including developing processes, for both sides of the business—technician materials and customer provided equipment (CPE). • Implement processes for ISO 9001:2015 and TL 9000 V R6.1/R5.5 certifications. • Drive all safety requirements set forth by local, national and CTDI including power industrial truck (PIT), accident/injury reports, morning meetings, monthly safety meetings, monthly safety audits, fire extinguisher checks, and education/training. • In charge of cosmetic parts inventory to ensure branch has proper inventory of parts for refurbishment of set top boxes (STB) and cable modems.
-
-
-
Premier Aluminum
-
United States
-
Automation Machinery Manufacturing
-
1 - 100 Employee
-
Quality Manager
-
Jul 2017 - May 2018
As a member of the management team, responsible for quality assurance processes, from procurement of materials to manufacture and shipment of permanent aluminum mold castings in a facility running 24/7.• Lead team of 4 CMM Technicians and 1 Quality Engineer • Saved estimated $3,800 on first year’s calibration costs while also increasing turn-around time and decreasing over-due gages. • Drive PPAP, Capability Studies and Corrective Actions, as required by customer, to completion on schedule.• Successfully completed changeover from ISO 9001:2008 to ISO 9001:2015 in just seven (7) months.• Successfully ensured all Quality Assurance requirements were properly implemented for company wide implementation of Plex Manufacturing ERP system.
-
-
-
Avidity Science - Americas
-
United States
-
Pharmaceutical Manufacturing
-
1 - 100 Employee
-
Quality Manager
-
Jan 2008 - Jul 2017
Responsible for quality assurance processes, from procurement of materials to manufacture, delivery, install and service of company products. Lead of team of five talented individuals. • November of 2012, acquired responsibilities for Document Control, Media Room (printing of sale brochures, product manuals, customer documentation, etc.) and Water Quality Engineer. Manage strategic direction of Quality Assurance department. • Led organization in successful transition from ISO 9001:2008 to ISO 9001:2015 standard including the development and education of risk based thinking; only the third company from this registrar. • Oversee customer returned valve analysis process, including customer onsite root cause analysis, and water quality analysis by providing documented root cause, corrective action and customer education of best practices for product use via an 8D report. • Responsible for resolution of all issues at customer sites.• Drive supplier development process through onsite audits, first article inspections and communication of requirements, including supplier quality manual and top 25 suppliers risk assessment. • Initial implementation of Quality Management System (QMS) for initial certification of ISO 9001:2008 including auditing of internal processes and creation of process documentation.• Management of supplier development through supplier audits and driving corrective action for product specific issue resolution—utilized for supplier rating system.• Participated in SWOT analysis on Edstrom product lines for strategic planning recommendations. • Led switchover of SPC from GE Proficy to InfinityQS ProFicient in machining area.• Decreased internal nonconforming material and rework costs from 0.48% to 0.15% of sales.• Management of calibration program (over 1500 gages); changed from in-house to complete outsource of calibration to ensure accuracy and on-time calibration of gauging.
-
-
Quality Assurance Engineer
-
Jan 2007 - Jan 2008
Responsible for quality assurance processes related to the design, manufacture, and service of product. · Determine true root cause and providing 8D reports as customer responses to corrective actions. · Management of the Engineering and Manufacturing corrective action process allowing leverage of the problem solving tools to make improvements to processes. · Improved SPC process in machining area to be statistically more accurate and less time consuming for the operators. · Implementation of Layered Audit program to ensure conformance to process and prevention of process creep. · Creation of 4-Panel charts to provide visual indication of key process and communication to entire organization.
-
-
-
Adaptive Micro Systems, a TAPCO Company
-
United States
-
Appliances, Electrical, and Electronics Manufacturing
-
1 - 100 Employee
-
Associate Quality Engineer
-
Feb 2002 - Jan 2007
Manage Product and Supplier Quality Assurance · Contribute to the Marketing Requirement Specification (MRS) by adding the customer requirements of Mean-Time-Between-Failures (MTBF) to Serviceability and Maintainability section · Involved in the Idea Creation and Concept phases (upstream) of product management by communicating with both internal and external customers, as well as, suppliers to provide input into the New Product Development process resulting in successful product launches of RoadStar and BetaBrite Prism · To achieve the market requirement of a two week lead time, coordinated the events required to yield a 40 hour reduction in testing time, resulting in an increase of $158,000
-
-
Education
-
Cardinal Stritch University
Master of Business Administration -
University of Wisconsin-Platteville
Bachelor of Science, Business Administration - Management
Community
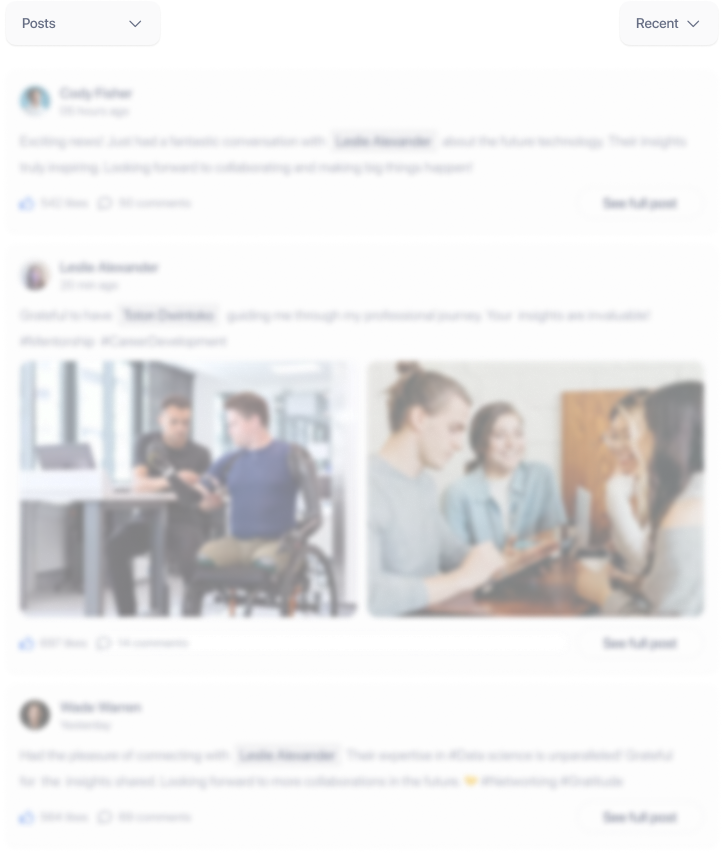