
Craig Feeler
Quality/Project Specialists at Hantover- Claim this Profile
Click to upgrade to our gold package
for the full feature experience.
Topline Score
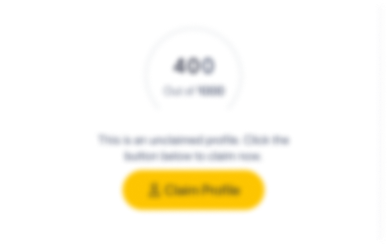
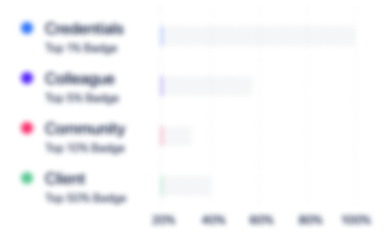
Bio


Experience
-
Hantover
-
United States
-
Wholesale
-
1 - 100 Employee
-
Quality/Project Specialists
-
Jan 2021 - Present
-
-
-
-
Operations Manager
-
Jan 2020 - Dec 2020
-
-
-
-
Operations Manager
-
May 2012 - Jan 2020
Responsible for all facets of operations including production profit and loss, purchasing, customer service, quoting and estimating, production efficiency, plant and equipment maintenance, employee relations, shipping & receiving, and scheduling. Proficient in the use of 2D autocad and engineering re-design of customer product for marketing and engineering improvement. Responsible for all facets of operations including production profit and loss, purchasing, customer service, quoting and estimating, production efficiency, plant and equipment maintenance, employee relations, shipping & receiving, and scheduling. Proficient in the use of 2D autocad and engineering re-design of customer product for marketing and engineering improvement.
-
-
-
-
Plant Manager
-
Mar 2010 - Mar 2012
Responsible for all aspects of Plant operation with a 2 shift operation and 23 employees in the division. Responsible for all aspects of Plant operation with a 2 shift operation and 23 employees in the division.
-
-
-
-
Plant Manager, Quality Manager, Process Improvement
-
May 1990 - Sep 2010
Manage up to 75 hourly production employees and supervisors on three shiftsMonitor and Schedule productionEvaluate and schedule maintenance of production equipmentRecommend, justify, and allocate production equipmentValue stream map production processes where improvements are needed resulting in 3% savings overallConduct lean manufacturing training resulting in time and labor savingsImplement and maintain 5S programOrganize and lay out plant equipment locationManage 3 quality inspectorsDevelop and document complete ISO 9000 certified quality systemDevelop and document training classes on Blueprint and measurement equipment usageTrain all shop personnel in quality and measurement system usagePlan and conduct internal auditsAudit supplier’s quality systemsConduct monthly quality and safety meetingsDevelop and document safety programsReview all new product shop routings and time estimates in the Global Shops system, assign part numbers and build inventory bills of material for new products, advise production and engineering of needed change in process steps and time allocation.Responsible for training of all shop floor employees concerning operations of manufacturing, machine operation, Global Shops software, Lean Manufacturing, and improvement on efficiency.
-
-
Education
-
University of Central Missouri
Bachelor of Science - BS, Industrial Management
Community
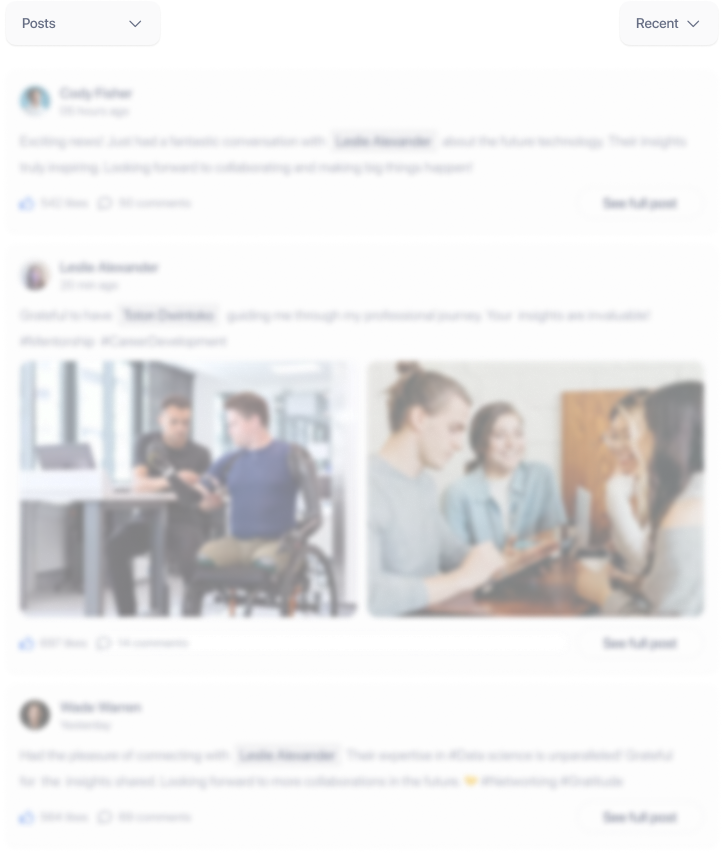