Corey Andrus
Deputy Project Manager at Chugach Alaska Corporation- Claim this Profile
Click to upgrade to our gold package
for the full feature experience.
Topline Score
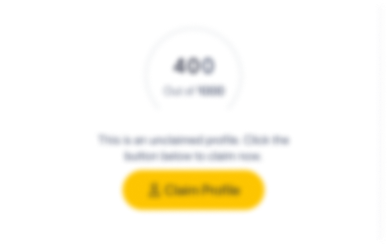
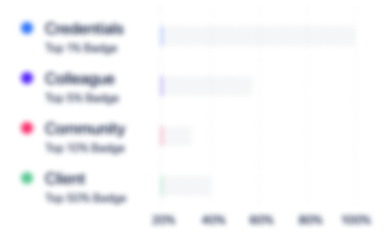
Bio

Colin MacGray
Corey is a very detail oriented Quality Manager. We spent time together launching a $70 million sales / year factory to support the Dodge Durango plant in Delaware. This was a huge undertaking, not only logistically, but to ensure we defined and maintained quality product. Corey can operate not only at the level required to develop the plan, but also can get into the detail with all levels to ensure the detailed plans are defined and appropriate. This was critical for the launch we undertook, since we had much hiring to do and were often understaffed. Corey made sure the job got done. Would love to have an opportunity to get him to work for me again.

LinkedIn User
Corey and I worked together at Smiths Detection while he was in the role of Quality Manager for the Edgewood Manufacturing Operation. Immediately following his hire, Corey was appointed to our Global SAP implementation team, and headed up the implementation project for our SAP quality module across the enterprise. Corey did an outstanding job leading the development of our critical quality processes for all the manufacturing and administrative sites (8 manufacturing plants and 2 major administrative sites world-wide), and brought forward an effective implementation timeline covering necessary workflows, training, roll out, and post go-live change management. Corey successfully restructured the Edgewood quality system, and brought the needed discipline and criteria required for an effective and meaningful ISO 9001 management review. During his service, Corey was faced with many challenges with his team, and was able to raise the bar on his organization’s productivity. Most notable was his team’s effort navigating the changes in DCMA QAR representatives. Under the leadership of Corey, the quality team successfully maintained the strong relationship and confidence through a time of several changes. Corey is an effective leader, and a key contributor to the leadership team. I highly recommend him for and leadership position in Quality within a Manufacturing Operations environment.

Colin MacGray
Corey is a very detail oriented Quality Manager. We spent time together launching a $70 million sales / year factory to support the Dodge Durango plant in Delaware. This was a huge undertaking, not only logistically, but to ensure we defined and maintained quality product. Corey can operate not only at the level required to develop the plan, but also can get into the detail with all levels to ensure the detailed plans are defined and appropriate. This was critical for the launch we undertook, since we had much hiring to do and were often understaffed. Corey made sure the job got done. Would love to have an opportunity to get him to work for me again.

LinkedIn User
Corey and I worked together at Smiths Detection while he was in the role of Quality Manager for the Edgewood Manufacturing Operation. Immediately following his hire, Corey was appointed to our Global SAP implementation team, and headed up the implementation project for our SAP quality module across the enterprise. Corey did an outstanding job leading the development of our critical quality processes for all the manufacturing and administrative sites (8 manufacturing plants and 2 major administrative sites world-wide), and brought forward an effective implementation timeline covering necessary workflows, training, roll out, and post go-live change management. Corey successfully restructured the Edgewood quality system, and brought the needed discipline and criteria required for an effective and meaningful ISO 9001 management review. During his service, Corey was faced with many challenges with his team, and was able to raise the bar on his organization’s productivity. Most notable was his team’s effort navigating the changes in DCMA QAR representatives. Under the leadership of Corey, the quality team successfully maintained the strong relationship and confidence through a time of several changes. Corey is an effective leader, and a key contributor to the leadership team. I highly recommend him for and leadership position in Quality within a Manufacturing Operations environment.

Colin MacGray
Corey is a very detail oriented Quality Manager. We spent time together launching a $70 million sales / year factory to support the Dodge Durango plant in Delaware. This was a huge undertaking, not only logistically, but to ensure we defined and maintained quality product. Corey can operate not only at the level required to develop the plan, but also can get into the detail with all levels to ensure the detailed plans are defined and appropriate. This was critical for the launch we undertook, since we had much hiring to do and were often understaffed. Corey made sure the job got done. Would love to have an opportunity to get him to work for me again.

LinkedIn User
Corey and I worked together at Smiths Detection while he was in the role of Quality Manager for the Edgewood Manufacturing Operation. Immediately following his hire, Corey was appointed to our Global SAP implementation team, and headed up the implementation project for our SAP quality module across the enterprise. Corey did an outstanding job leading the development of our critical quality processes for all the manufacturing and administrative sites (8 manufacturing plants and 2 major administrative sites world-wide), and brought forward an effective implementation timeline covering necessary workflows, training, roll out, and post go-live change management. Corey successfully restructured the Edgewood quality system, and brought the needed discipline and criteria required for an effective and meaningful ISO 9001 management review. During his service, Corey was faced with many challenges with his team, and was able to raise the bar on his organization’s productivity. Most notable was his team’s effort navigating the changes in DCMA QAR representatives. Under the leadership of Corey, the quality team successfully maintained the strong relationship and confidence through a time of several changes. Corey is an effective leader, and a key contributor to the leadership team. I highly recommend him for and leadership position in Quality within a Manufacturing Operations environment.

Colin MacGray
Corey is a very detail oriented Quality Manager. We spent time together launching a $70 million sales / year factory to support the Dodge Durango plant in Delaware. This was a huge undertaking, not only logistically, but to ensure we defined and maintained quality product. Corey can operate not only at the level required to develop the plan, but also can get into the detail with all levels to ensure the detailed plans are defined and appropriate. This was critical for the launch we undertook, since we had much hiring to do and were often understaffed. Corey made sure the job got done. Would love to have an opportunity to get him to work for me again.

LinkedIn User
Corey and I worked together at Smiths Detection while he was in the role of Quality Manager for the Edgewood Manufacturing Operation. Immediately following his hire, Corey was appointed to our Global SAP implementation team, and headed up the implementation project for our SAP quality module across the enterprise. Corey did an outstanding job leading the development of our critical quality processes for all the manufacturing and administrative sites (8 manufacturing plants and 2 major administrative sites world-wide), and brought forward an effective implementation timeline covering necessary workflows, training, roll out, and post go-live change management. Corey successfully restructured the Edgewood quality system, and brought the needed discipline and criteria required for an effective and meaningful ISO 9001 management review. During his service, Corey was faced with many challenges with his team, and was able to raise the bar on his organization’s productivity. Most notable was his team’s effort navigating the changes in DCMA QAR representatives. Under the leadership of Corey, the quality team successfully maintained the strong relationship and confidence through a time of several changes. Corey is an effective leader, and a key contributor to the leadership team. I highly recommend him for and leadership position in Quality within a Manufacturing Operations environment.

Credentials
-
Project Management Professional (PMP)
Project Management InstituteDec, 2021- Nov, 2024 -
Certified Manager of Quality / Organizational Excellence
ASQ - World HeadquartersMar, 2013- Nov, 2024 -
Certified Quality Auditor
ASQ - World HeadquartersDec, 2010- Nov, 2024 -
Certified Quality Engineer
ASQ - World HeadquartersJan, 2000- Nov, 2024 -
Certified Six Sigma Green Belt
ASQ - World Headquarters
Experience
-
Chugach Alaska Corporation
-
Executive Offices
-
400 - 500 Employee
-
Deputy Project Manager
-
May 2021 - Present
Responsible for multiple departments, project budget, and overall performance of our various teams on a large government contract.
-
-
Quality Program Manager
-
Jan 2015 - May 2021
>Led a department of 1 Quality Supervisor, 1 Quality Control Inspectors, 1 Quality System Administrator, 2 Auditors and 2 Document & Record Specialists including hiring, professional development, work assignments, and technical direction.>Developed KPI system with 30 metrics across 7 departments, integrating tracking spreadsheet into departmental KPI workbooks that tabulate and graph KPI outputs.>Developed an internal audit program establishing an audit procedure, checklists, schedule, tracking log for “to schedule” and “percent conforming requirements”, training of staff, and recruiting an auditor to ensure compliance to 2 Gov’t contracts with 3 statements of work.>Developed new document control procedure, trained key personnel, simplified process and improved participation. >Restructured records system reducing electronic folder structure to simplify storage locations and facilitate document tech engagement to process; developed MS Access database to improve retrieval of records and track hard and softcopy records added to and removed from the system.>Collaborated with operational groups developing corrective actions to resolve systemic issues and to investigate and apply corrective actions for customer impacting events.>Led weekly QC meeting with Gov’t to review CMMS worklog compliance and participated with Project Manager and functional managers in monthly Gov’t COR meetings.>Developed Master List and active schedule to track delivery timeliness, provide 30 day reminder window, and calculate monthly performance on over 60 Contract Data Items.
-
-
-
SYNCREON
-
United States
-
Truck Transportation
-
700 & Above Employee
-
Quality Manager
-
Nov 2013 - Jan 2015
>Led a department of 20 salaried and 33 hourly employees including hiring, professional development, performance evaluations, merit increases, disciplinary actions, work assignments, and technical direction.>Managed definition of department roles and responsibilities, allocation of physical and human resources, and departmental procedures and instructions.>Serve as ISO 9001 Management Representative and hold a shared responsibility with the Corporate Quality team for ISO 9001 program controlling all local processes, procedures, internal auditing, Management Review, training, document control, record control, etc.>Conducted daily team and management board meetings, weekly senior management deck reviews, weekly Harley Davidson deck reviews, monthly Quality Council reviews, and ISO Management Reviews reporting various quality metrics including PPM, CPH, external and internal escapes, Nonconforming Material process tracking (facility produced 175,000 units per week), CAPA status, Layered Process Audit status, ISO 9001 internal audit and Problem Alert status, weekly and month to date scrap, customer returns, etc.>Participated in new Model Year product development and cross functional launch teams planning prototype builds, preproduction and launch, and equipment, manning, packaging, and facility needs to support the new products.
-
-
-
-
Senior Principal Engineer Quality Assurance
-
Jul 2009 - Nov 2013
>Served as Quality Subject Matter Expert for the Joint Product Manager Biological Defense Systems (JPMBDS).>Conducted 2nd party Quality Management System and process audits.>Observed laboratory and field testing of newly developed and/or modified equipment.>Oversaw Failure Reporting and Corrective Action System (FRACAS) conducted by prime contractor.>Served on two JPMBDS product Configuration Control Boards.>Developed and assessed requirements for SOWs and performance specifications.>Evaluated program Contract Data Requirements List documents including Quality Assurance Program Plans, Test Plans, Test Reports, Configuration Management Plans, Master Program Schedules, Engineering Change Proposals, NORs, Systems Engineering Management Plans, Performance Specifications, design documents, design review documents, etc.>Developed Line Replaceable Unit incoming inspection program.>Participated in product design reviews, ESIP (engineering) efforts, program performance reviews, First Article Test reviews, Test Readiness Reviews, Product Acceptance Tests and reviews, etc.>Updated Government Technical Data Package documents for correctness and accuracy.>Developed and maintained data analysis as well as trend and Pareto charting for field maintenance activities.
-
-
-
Smiths Detection
-
United Kingdom
-
Security Systems Services
-
700 & Above Employee
-
Quality Manager
-
Aug 2007 - Jul 2009
>Led a department of 13 employees including hiring, professional development, performance evaluations, merit increases, disciplinary actions, work assignments, and technical direction.>Managed department budget, definition of department roles and responsibilities, allocation of physical and human resources, and departmental procedures and instructions.>Served as ISO 9001 Management Representative and Business Continuity Manager.>Developed and implemented performance metrics, SAP driven nonconformance and corrective action system, and monthly defect trend and Pareto analysis by product.>Coordinated planning activities, developed system configuration with consultants, developed training material, unit tested, integration tested, trained, and served as Quality Super User for SAP implementation that included nine plants in five countries.>Developed and modified QMS documents to accommodate the implementation of SAP.>Established a new supplier quality program, documented the processes, added a SQ Engineer, updated records, integrated delivery ratings, implemented new supplier approvals with coordination to purchasing process and added continuing assessments process.>Improved calibration process with upgraded software, standardized notification process to equipment owning departments to increase equipment capture, brought simple calibrations in house for $3k annual savings, updated procedure to add process changes and report out to Quality Manager for lost equipment and equipment failing calibration.>Implemented escalation process to drive completion of activities assigned in Quality Notifications.>Registered facility to ISO 9001: 2008 standard 6 months ahead of schedule.>Assisted in the implementation of an OHSAS 18001 safety system by conducting audits and updating procedures manual.>Served as ISO 14001 internal auditor and backup ISO 14001 trainer for new employees.
-
-
-
Collins & Aikman
-
Motor Vehicle Manufacturing
-
1 - 100 Employee
-
Quality Manager
-
Jul 2003 - Aug 2007
>Led a department of as many as 36 employees including hiring, professional development, performance evaluations, merit increases, disciplinary actions, work assignments, and technical direction.>Managed department budget, definition of department roles and responsibilities through development of a standardized work document, allocation of physical and human resources, and departmental procedures and instructions for two manufacturing sites.>Developed, implemented, registered, and maintained a TS-16949 QMS.>Developed and managed error proofing program to reduce assembly machine failures.>Developed, implemented, and maintained a layered audit process.>Served as TS-16949 Management Representative and Lead Auditor.>Managed dimensional lab with coordinate measuring machine, various dimensional measuring devices, over 50 holding fixtures and the calibration of all equipment.>Established clearly marked Quality Hold area and the material review board process to ensure proper disposition and documentation. >Developed, implemented, and managed a supplier quality process which included data collection and reporting to the Corporate office, nonconformance tracking, corrective action process, and coordinating with accounting on chargebacks for costs incurred from scrap and labor. >Drove customer PPM from a rolling 6 month average of 4500 to 52.
-
-
-
-
Quality Engineer
-
Oct 1998 - Jul 2003
-
-
-
Textron Systems
-
United States
-
Defense and Space Manufacturing
-
700 & Above Employee
-
Engineering Technician
-
Jul 1997 - Oct 1998
-
-
-
-
Customer Engineering Liaison
-
Apr 1996 - Jul 1997
-
-
Education
-
University of New Hampshire
BA, English
Community
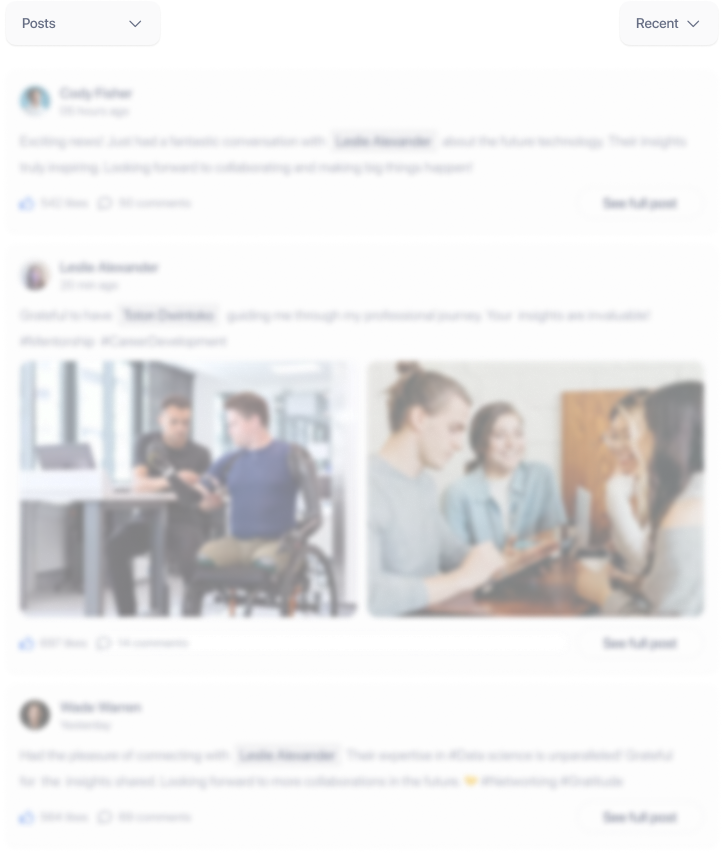