Connie Sue Whetstone
Master Production Scheduler at Royal Switchgear Manufacturing Co.- Claim this Profile
Click to upgrade to our gold package
for the full feature experience.
Topline Score
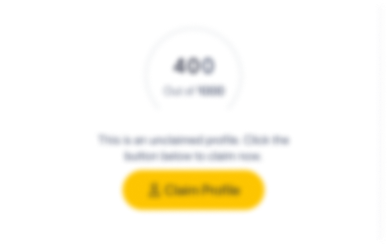
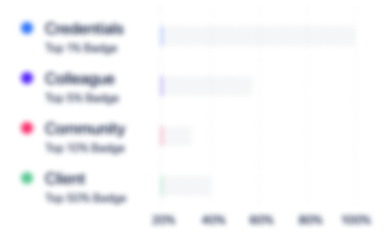
Bio

Kerstin Gerdes
I got to appreciate Connie Sue commitment and hands on work ethic during our time at SMP. She impressed me with her knowledge about logistics which complemented with her skills to set up for IATF certification. It was a pleasure to work with her because she would not only seek continuously for improvements but be a good example for others to follow her lead. I admired her soft skills to help an international and divers team to overcome conflicts because of cultural differences. Her attitude to treat everyone with respect reflected in the work results and accomplishments she had helping the company set up a greenfield plant.

Mark H. Kohler
Connie approaches her work with a high level of committment. Her strong materials systems experience gives her a quick grasp of the business operating systems to solve problems and make improvements. She is results oriented and fact based in her approach and continually looking for ways to improve her work.

Kerstin Gerdes
I got to appreciate Connie Sue commitment and hands on work ethic during our time at SMP. She impressed me with her knowledge about logistics which complemented with her skills to set up for IATF certification. It was a pleasure to work with her because she would not only seek continuously for improvements but be a good example for others to follow her lead. I admired her soft skills to help an international and divers team to overcome conflicts because of cultural differences. Her attitude to treat everyone with respect reflected in the work results and accomplishments she had helping the company set up a greenfield plant.

Mark H. Kohler
Connie approaches her work with a high level of committment. Her strong materials systems experience gives her a quick grasp of the business operating systems to solve problems and make improvements. She is results oriented and fact based in her approach and continually looking for ways to improve her work.

Kerstin Gerdes
I got to appreciate Connie Sue commitment and hands on work ethic during our time at SMP. She impressed me with her knowledge about logistics which complemented with her skills to set up for IATF certification. It was a pleasure to work with her because she would not only seek continuously for improvements but be a good example for others to follow her lead. I admired her soft skills to help an international and divers team to overcome conflicts because of cultural differences. Her attitude to treat everyone with respect reflected in the work results and accomplishments she had helping the company set up a greenfield plant.

Mark H. Kohler
Connie approaches her work with a high level of committment. Her strong materials systems experience gives her a quick grasp of the business operating systems to solve problems and make improvements. She is results oriented and fact based in her approach and continually looking for ways to improve her work.

Kerstin Gerdes
I got to appreciate Connie Sue commitment and hands on work ethic during our time at SMP. She impressed me with her knowledge about logistics which complemented with her skills to set up for IATF certification. It was a pleasure to work with her because she would not only seek continuously for improvements but be a good example for others to follow her lead. I admired her soft skills to help an international and divers team to overcome conflicts because of cultural differences. Her attitude to treat everyone with respect reflected in the work results and accomplishments she had helping the company set up a greenfield plant.

Mark H. Kohler
Connie approaches her work with a high level of committment. Her strong materials systems experience gives her a quick grasp of the business operating systems to solve problems and make improvements. She is results oriented and fact based in her approach and continually looking for ways to improve her work.

Credentials
-
Enhance Your Productivity with Effective Note-Taking
LinkedInOct, 2021- Sep, 2024 -
Excel: Creating a Basic Dashboard
LinkedInOct, 2021- Sep, 2024 -
Certified Leader 3
AIDTDec, 2020- Sep, 2024 -
Root Cause Analysis and Problem Solving
Alabama Technology NetworkNov, 2020- Sep, 2024
Experience
-
Royal Switchgear Manufacturing Co.
-
United States
-
Appliances, Electrical, and Electronics Manufacturing
-
1 - 100 Employee
-
Master Production Scheduler
-
Oct 2021 - Present
Manufacturing High voltage electrical switches for the transmission substations across North America. Moving power safely to all consumers. Manufacturing High voltage electrical switches for the transmission substations across North America. Moving power safely to all consumers.
-
-
-
SMP Automotive Global
-
Germany
-
Motor Vehicle Manufacturing
-
700 & Above Employee
-
Superintendent in Logistics
-
May 2018 - Apr 2021
SMP is a Greenfield plant to support MBUSI on 4 models. SOP (start of production) was 10/2018 on 1 model with the others following in 2019 and 2020. SMP is a Greenfield plant to support MBUSI on 4 models. SOP (start of production) was 10/2018 on 1 model with the others following in 2019 and 2020.
-
-
-
Engineered Plastic Components
-
Motor Vehicle Manufacturing
-
100 - 200 Employee
-
Production Control Manager & Logistics/Material Manager
-
Jul 2017 - May 2018
-
-
-
Yanfeng
-
China
-
Motor Vehicle Manufacturing
-
700 & Above Employee
-
Sr. Supply Chain Mgmt. Analyst
-
Dec 2011 - Jul 2017
JCIM, McCalla changed name to Yanfeng. I also was the Engineering Change Coordinator and Supplier Quality Engineer in 2016-17. JCIM, McCalla changed name to Yanfeng. I also was the Engineering Change Coordinator and Supplier Quality Engineer in 2016-17.
-
-
-
-
Field Representative
-
Mar 2009 - Mar 2012
FOS, Field Operations Supervisor with 10 Direct Crew Leaders and 130 enumerators. I have been in 8 operations for the decennial census. Address Canvassing, Update Leave, Enumerating Transitory Locations, Early Early NRFU, No Response Follow Up, NRFU-Vacant Delete Check, NRFU-Field Verification, NRFU-Residual. Currently doing the American Housing Survey and the Current Population Survey. FOS, Field Operations Supervisor with 10 Direct Crew Leaders and 130 enumerators. I have been in 8 operations for the decennial census. Address Canvassing, Update Leave, Enumerating Transitory Locations, Early Early NRFU, No Response Follow Up, NRFU-Vacant Delete Check, NRFU-Field Verification, NRFU-Residual. Currently doing the American Housing Survey and the Current Population Survey.
-
-
-
-
Temp Contract Material Supervisor
-
Nov 2010 - Mar 2011
-
-
-
-
Continuous Improvement & Retail Pkg Manager
-
Jul 2009 - Feb 2010
A plumbing distribution center supplying retail, hvac, oems and wholesale businesses. Retail and Packing Manager with 40 reports in 2 warehouses. Supervised shipping for all retail customers. Learned Enterprise 21 ERP system from TGI. Started as a Continuous Improvement Manager and delivered cost savings worth over $600,000 in 3 months. A plumbing distribution center supplying retail, hvac, oems and wholesale businesses. Retail and Packing Manager with 40 reports in 2 warehouses. Supervised shipping for all retail customers. Learned Enterprise 21 ERP system from TGI. Started as a Continuous Improvement Manager and delivered cost savings worth over $600,000 in 3 months.
-
-
-
Hubbell Power Systems
-
United States
-
Appliances, Electrical, and Electronics Manufacturing
-
700 & Above Employee
-
Procurement Manager
-
Aug 2007 - Aug 2008
Managed 4 engineers as directs in the Supplier Sourcing MCTO (Material Cost Take Out) projects and Supplier Service Improvement projects. Lead improvements to enhance the sourcing process which Hubbell Corporate is now adopting as standard work. Help to incorporate into the Ariba Sourcing software as standard templates to be used for project coordination. Worked with Global Sourcing Team to achieve a 2007 goal of 32 projects and $1.4 million mcto. Set 2008 goal of 35 projects & $1.5 million reduction in purchased products by sourcing with LCC’s. (Low Cost Countries) Assisted in closing down 3 plants. Completed supplier audits and certified domestic suppliers along with identifying alternate supply chain options.
-
-
-
Lear Corporation
-
United States
-
Motor Vehicle Manufacturing
-
700 & Above Employee
-
Materials Manager
-
Oct 2006 - May 2007
Materials Manager of a Tier 1 supplier to the automotive industry supplying DCX, Ford, Toyota as well as a Tier 2 to other customers. Managed 4 directs, 19 indirect and 52 UAW hourly employees in a 24/7 operational mode. Building area of 415,000 sq. ft. with annual sales of $153 million. Key platforms were DCX Minivan, Pacifica, Caliber, Compass, and Patriot: Toyota Sequoia, Tundra and the Ford Explorer. Manufacturing process included 72 Injection Molding presses, Vacuum Forming, Paint / Pad Print, Vibration & Sonic Weld, Heat stake and light assembly. Door panels were 77% of the sales. Active finished goods part numbers were 782, with over 150 suppliers. New systems learned were Mattec, Iprocure, PIC (product information center) database, and PTA (premium transportation authority). Dropped inventory levels by 2 million dollars within the first 60 days of employment, $3 million by year end. Responsibilities listed: Receiving Dept. (43 inbound trucks/day), Shipping Dept. (140 inbound + outbound/day), Sequential shipping of product to match customer broadcast, Returnable Container Program Management, Customer Service, EDI, Purchasing and Supplier Schedules, Plant Production Scheduling including customer broadcast for sequencing products, Capacity Planning, Service Dept. with off site warehouse and production facility, MRO and Tool Crib, Freight Utilization (reduced premium freight cost by 50%), 5-S, Kanban, Cycle Counting and Inventory Management and Control, Physical Inventory, Drive on development of Work Instructions, Employee Performance evaluations, goals, objectives and plans. Developing KPI’s for department system and process monitoring (Key Process Indicators). Improved upon Corporate road map instructions. Corrected ISO 14001 major infringements.
-
-
-
-
Material Manager
-
Jan 2003 - Sep 2006
Materials Leader (Manager) of a Tier 1 supplier to the automotive industry servicing Nissan, Honda, Ford, Mazda and Chrysler. Managed 6 direct and up to 30 indirect colleagues in a 3-shift operation. Company functions included receiving, shipping as well as chronological sequencing for vehicle models, customer service, supplier schedules, freight lane optimization, rapid material exchange, 5 – S functions, cycle counting, and physical inventory. Improved processes dealing with a Supplier Managed Warehouse which located purchased product within 5 miles of the Tower facility in Mississippi. Inventory accuracy above 98% and turns above 85 (highest achieved 98 turns). Premium Freight cost kept below $10k per year with a weekly budget of $60k. Training of unskilled labor with salary position task and jobs to reduce budget constraints on salaried positions. Exceeded the OTD of Customers to 100% with less than a days worth of finished goods inventory. The plant exceeded two years without a lost time accident and No OSHA violations. Helped the SOX conversion team and retraining implementation throughout the materials department in both plants with the segregation of duties. Lead the Materials Best practices as well as the Engineering Change process and implementation project for successful QAD ERP material harmony.
-
-
-
Dometic Corporation
-
IT Services and IT Consulting
-
1 - 100 Employee
-
Production Scheduler, Inventory Control, Purchasing
-
May 1990 - Dec 2002
May 2001 to November 2002: Production Scheduler/Shipping Coordinator. Completed automating the scheduling function with the shipping procedure to increase both "Build to Order" and “Fill to Truck load”. (Sequential Scheduling and Shipping) Worked with zero inventory in finished goods and maintain no less than 97% on time delivery. OEM deliveries rose from 94% to 99% on time. I was the Inventory Control Manager of finished goods.February 1999 to May 2001: Production Scheduler /Receiving /Materials. On time delivery increased to 95% from 92%.January 1997 to 1999: Purchasing/Production Scheduler.Developed the “Build to Order” scheduling technique. Eliminated over $900,000 of finished goods inventory and increase through put which moved “On Time Delivery” from 88% to 92%.June 1994 to December 1996: PA and Satellite Team Management Member: Was 1 of 4 people in charge of a Satellite Plant in Mishawaka, Indiana. The team handled all aspects of running the plant including and not limited to Budgets, Human resources, Supervision (40-70), Key punching, Quality, Material / Production / Shipping flow as well as plant maintenance. May 1990 to June 1994: Purchasing Agent. Helped moved purchasing function and production materials from Santa Ana, California plant to the Lagrange, Indiana facility. Cost savings and avoidance averaged $300,000 yearly not including metal future buys.
-
-
Education
-
Omnex Engineering & Mgmt. Inc.
IATF 16949 Internal Auditor Training -
AIDT
Leadership III Certified -
Thompson Lift Truck Company
Certificate of Completion, Train the Trainer - Warehouse Products & Sit down counterbalanced trucks -
Purdue University Fort Wayne
Materials and Purchasing -
Huntington College/University
BS, Business Administration & Business Education
Community
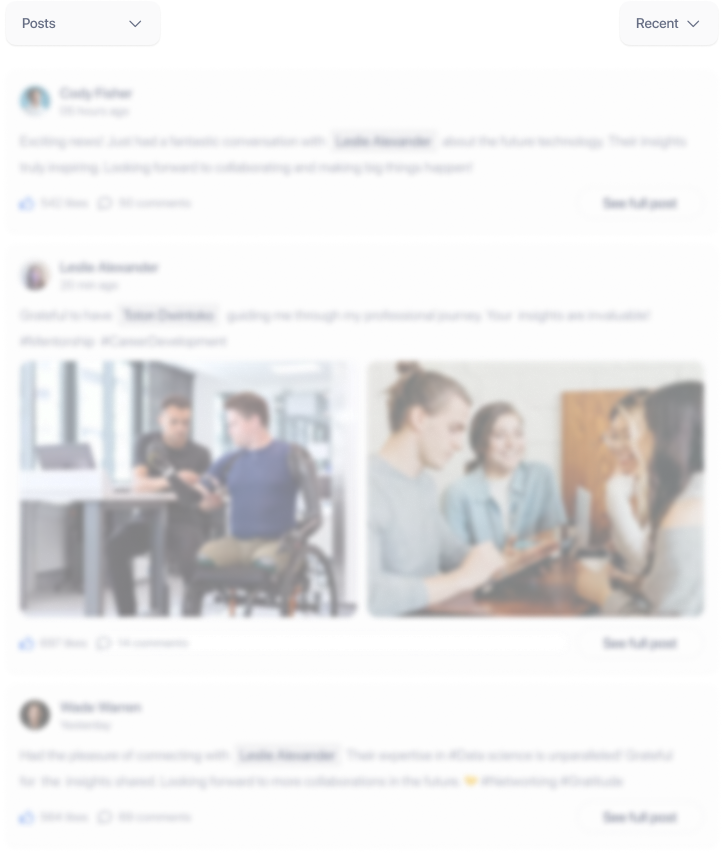