Cole Thrasher
Operations Engineer and Onboarding Specialist at ALOM- Claim this Profile
Click to upgrade to our gold package
for the full feature experience.
Topline Score
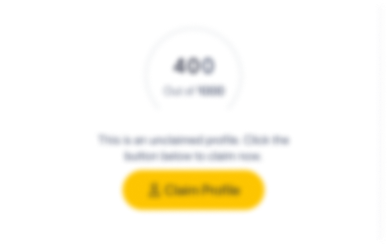
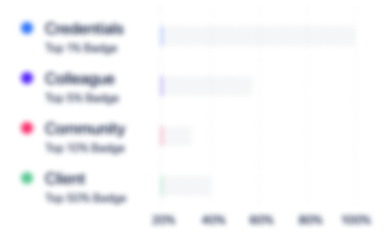
Bio


Experience
-
ALOM
-
United States
-
Truck Transportation
-
1 - 100 Employee
-
Operations Engineer and Onboarding Specialist
-
May 2022 - Present
•Acted as program manager for a new facility launch by collaborating with all stakeholders and ensuring the timeline was met • Lead company-wide Innovation Team that utilized technology from simple jigs to completely autonomous robotics improving overall efficiency, quality, and profit margins •Utilized 3D AutoCAD to create assembly improvement jigs along with 2D drafting AutoCAD to design blueprints of production and storage areas •Developed assembly line maps along with inventory, FTE, cycle time, and information systems requirements to create scalable operations •Leveraged SQL database to build dashboards with PowerBI that provided Operations with real time data •Overhauled and improved customer forecasts with Excel by creating nested IF functions while also utilizing VLOOKUP and pivot tables to provide accurate employee headcounts required for production Show less
-
-
-
-
Manufacturing Analyst Intern
-
Jan 2022 - May 2022
•Empowered and facilitated consulting team of three to capitalize on Six Sigma and Lean methodologies to improve quality of automotive production line for 150 completed parts daily •Utilized Microsoft Visio to create value stream maps of integrated production line for four different parts •Created and utilized production maps and time charts to demonstrate where supply lines are inefficient •Identifyed problems and possible solutions by acting as the point of contact for the client •Empowered and facilitated consulting team of three to capitalize on Six Sigma and Lean methodologies to improve quality of automotive production line for 150 completed parts daily •Utilized Microsoft Visio to create value stream maps of integrated production line for four different parts •Created and utilized production maps and time charts to demonstrate where supply lines are inefficient •Identifyed problems and possible solutions by acting as the point of contact for the client
-
-
-
Magna International
-
Canada
-
Motor Vehicle Manufacturing
-
700 & Above Employee
-
Materials/ Business Analyst Intern
-
Jan 2022 - May 2022
•Developed, implemented, and evaluated system utilizing vendor barcodes providing automated inventory updates in SAP ERP •Disseminated and coordinated with 230 vendors to supply barcodes on received shipments •Designed and documented SOPs on newly implemented systems and training 22 employees to utilize •Mapped receiving system to provide an accurate and up to date visual representation to locate inefficiencies •Developed, implemented, and evaluated system utilizing vendor barcodes providing automated inventory updates in SAP ERP •Disseminated and coordinated with 230 vendors to supply barcodes on received shipments •Designed and documented SOPs on newly implemented systems and training 22 employees to utilize •Mapped receiving system to provide an accurate and up to date visual representation to locate inefficiencies
-
-
-
Sweetwater
-
United States
-
Musicians
-
700 & Above Employee
-
Project Manager Intern
-
Sep 2021 - May 2022
•Facilitated consulting team of four as project lead to determine software, hardware, and technology solutions to increase distribution efficiency, improve order packing process, and reduce employee turnover by creating stable same-day shipping times •Streamlined four unique processes to increase distribution center daily operational capacity by 25% •Developed risk analysis, process models, and data flow charts to map production numbers and identify bottlenecks •Reengineered scope to achieve project expectations in a set 8-month time frame Show less
-
-
-
Village Pantry
-
United States
-
Retail
-
1 - 100 Employee
-
Assistant Manager
-
Jun 2018 - Aug 2019
•Facilitated team of 8 •Ensured that store inventory was maintained •Fielded customer complaints and interacted with them daily •Arbitrated employees arguments •Defined management's desires to team members •Facilitated team of 8 •Ensured that store inventory was maintained •Fielded customer complaints and interacted with them daily •Arbitrated employees arguments •Defined management's desires to team members
-
-
-
-
Buyer Intern
-
Aug 2017 - Jun 2018
•Implemented QR code system for improved inventory accuracy and efficiency within SAP ERP •Transformed SAP and SQL data into a dashboard in PowerBI that forecasted and planned when new materials and equipment would need to be purchased new materials and equipment would need to be purchased •Negotiated with 12 suppliers to purchase operational supplies used in manufacturing and achieved a cost-cutting goal of $7000 per year •Completed three inventory and distribution projects to streamline inventory systems Show less
-
-
-
-
Duty Supervisor
-
May 2014 - Aug 2017
•Supervised and trained incoming employees, taking on a leadership role to ensure quality control over operations •Cultivated inventory to more conveniently store and access materials •Completed daily tasks and organized responsibilities •Supervised and trained incoming employees, taking on a leadership role to ensure quality control over operations •Cultivated inventory to more conveniently store and access materials •Completed daily tasks and organized responsibilities
-
-
Education
-
Ball State University
Bachelor of Science - BS, Computer Information Systems | Business Administration | Six Sigma -
Vincennes University
Associate's degree, Business Management
Community
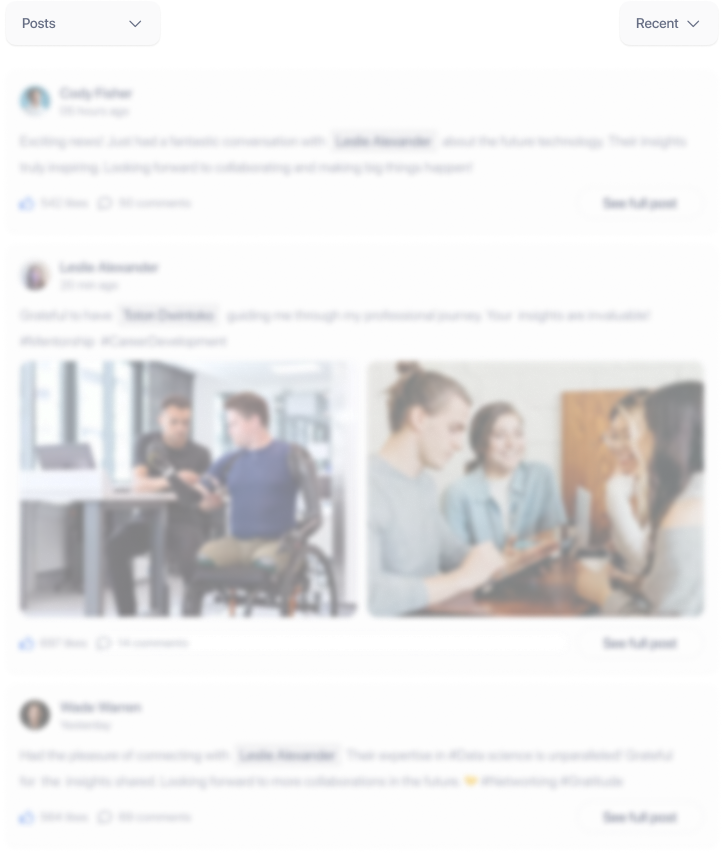