Cody Blankenship, MBA
Vice President Performance Improvement at Mary Washington Healthcare- Claim this Profile
Click to upgrade to our gold package
for the full feature experience.
Topline Score
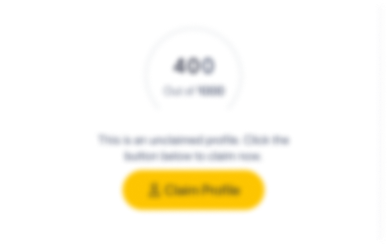
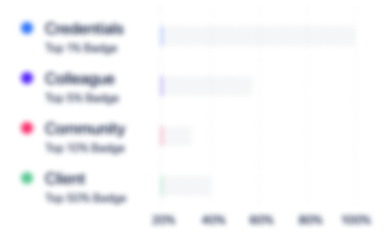
Bio

James Pearman
Cody is a very focused and talented individual. He plans his actions and does what is necessary to carry out his plan. He maintains a balance between his work and his family as both are very important to him. I recommend him for his systems and business consulting.

Phil Bride
It's been a real pleasure working with Cody over the last several months. I've worked with Cody through people development processes such as focusing on what's most important in projects: communication, getting focused on the desired outcomes, listening to the wants and needs of customers and effectively addressing those needs. Cody has an excellent sense of how to understand people's perspectives. These are all crucial elements in developing and implementing innovative strategies to improve performance and efficiency.

James Pearman
Cody is a very focused and talented individual. He plans his actions and does what is necessary to carry out his plan. He maintains a balance between his work and his family as both are very important to him. I recommend him for his systems and business consulting.

Phil Bride
It's been a real pleasure working with Cody over the last several months. I've worked with Cody through people development processes such as focusing on what's most important in projects: communication, getting focused on the desired outcomes, listening to the wants and needs of customers and effectively addressing those needs. Cody has an excellent sense of how to understand people's perspectives. These are all crucial elements in developing and implementing innovative strategies to improve performance and efficiency.

James Pearman
Cody is a very focused and talented individual. He plans his actions and does what is necessary to carry out his plan. He maintains a balance between his work and his family as both are very important to him. I recommend him for his systems and business consulting.

Phil Bride
It's been a real pleasure working with Cody over the last several months. I've worked with Cody through people development processes such as focusing on what's most important in projects: communication, getting focused on the desired outcomes, listening to the wants and needs of customers and effectively addressing those needs. Cody has an excellent sense of how to understand people's perspectives. These are all crucial elements in developing and implementing innovative strategies to improve performance and efficiency.

James Pearman
Cody is a very focused and talented individual. He plans his actions and does what is necessary to carry out his plan. He maintains a balance between his work and his family as both are very important to him. I recommend him for his systems and business consulting.

Phil Bride
It's been a real pleasure working with Cody over the last several months. I've worked with Cody through people development processes such as focusing on what's most important in projects: communication, getting focused on the desired outcomes, listening to the wants and needs of customers and effectively addressing those needs. Cody has an excellent sense of how to understand people's perspectives. These are all crucial elements in developing and implementing innovative strategies to improve performance and efficiency.

Credentials
-
Lean Six Sigma Black Belt
University of MichiganOct, 2013- Nov, 2024 -
Business Coach
Resource Associates Corporation -
IMX Assessment Tools
Innermetrix International -
Lean Six Sigma Green Belt
ITT
Experience
-
Mary Washington Healthcare
-
United States
-
Hospitals and Health Care
-
700 & Above Employee
-
Vice President Performance Improvement
-
Jan 2017 - Present
More than 100 years ago, Mary Washington Healthcare began as an eight-room hospital in Fredericksburg, Virginia. Today, it has evolved into a not-for-profit regional system of two hospitals and 28 healthcare facilities and wellness services. Our Board of Trustees is made up of community leaders who serve in a volunteer capacity to guide our direction. Our mission to our community is clear. Mary Washington Healthcare exists to improve the health of the people in the communities we… Show more More than 100 years ago, Mary Washington Healthcare began as an eight-room hospital in Fredericksburg, Virginia. Today, it has evolved into a not-for-profit regional system of two hospitals and 28 healthcare facilities and wellness services. Our Board of Trustees is made up of community leaders who serve in a volunteer capacity to guide our direction. Our mission to our community is clear. Mary Washington Healthcare exists to improve the health of the people in the communities we serve. As a not-for-profit corporation, we invest our profits back into the organization through such activities as upgrading our technology, developing new services and hiring new staff. The result is continuous improvement in the scope and quality of care we’re able to provide to the community. In addition to investing in our organization, we invest heavily in our community. Show less More than 100 years ago, Mary Washington Healthcare began as an eight-room hospital in Fredericksburg, Virginia. Today, it has evolved into a not-for-profit regional system of two hospitals and 28 healthcare facilities and wellness services. Our Board of Trustees is made up of community leaders who serve in a volunteer capacity to guide our direction. Our mission to our community is clear. Mary Washington Healthcare exists to improve the health of the people in the communities we… Show more More than 100 years ago, Mary Washington Healthcare began as an eight-room hospital in Fredericksburg, Virginia. Today, it has evolved into a not-for-profit regional system of two hospitals and 28 healthcare facilities and wellness services. Our Board of Trustees is made up of community leaders who serve in a volunteer capacity to guide our direction. Our mission to our community is clear. Mary Washington Healthcare exists to improve the health of the people in the communities we serve. As a not-for-profit corporation, we invest our profits back into the organization through such activities as upgrading our technology, developing new services and hiring new staff. The result is continuous improvement in the scope and quality of care we’re able to provide to the community. In addition to investing in our organization, we invest heavily in our community. Show less
-
-
-
Utility One Source
-
Lynchburg, Virginia Area
-
General Manager
-
Feb 2016 - Jan 2017
Beginning in February of 2015, three family-owned and operated companies (Custom Truck & Equipment, Utility Fleet Sales and Forestry Equipment of VA) joined together to form what is now Utility One Source. Shortly after its inception, UCO Equipment became a part of the UOS family along with TNT Equipment six months later. In December 2015, UOS welcomed its sixth company under its brand, Load King, a leading manufacturer of high-quality and customizable trailers. The announcement of the… Show more Beginning in February of 2015, three family-owned and operated companies (Custom Truck & Equipment, Utility Fleet Sales and Forestry Equipment of VA) joined together to form what is now Utility One Source. Shortly after its inception, UCO Equipment became a part of the UOS family along with TNT Equipment six months later. In December 2015, UOS welcomed its sixth company under its brand, Load King, a leading manufacturer of high-quality and customizable trailers. The announcement of the partnership represented the platform's collective commitment to the continued growth and dominance of each legacy company's individual offerings, now compounded to leverage the expertise of the team and, ultimately, better serve loyal UOS customers all over the world. UOS will build upon the market positions of each legacy company, while serving as a single source supplier of specialty equipment and services for the utility and heavy equipment industries. Show less Beginning in February of 2015, three family-owned and operated companies (Custom Truck & Equipment, Utility Fleet Sales and Forestry Equipment of VA) joined together to form what is now Utility One Source. Shortly after its inception, UCO Equipment became a part of the UOS family along with TNT Equipment six months later. In December 2015, UOS welcomed its sixth company under its brand, Load King, a leading manufacturer of high-quality and customizable trailers. The announcement of the… Show more Beginning in February of 2015, three family-owned and operated companies (Custom Truck & Equipment, Utility Fleet Sales and Forestry Equipment of VA) joined together to form what is now Utility One Source. Shortly after its inception, UCO Equipment became a part of the UOS family along with TNT Equipment six months later. In December 2015, UOS welcomed its sixth company under its brand, Load King, a leading manufacturer of high-quality and customizable trailers. The announcement of the partnership represented the platform's collective commitment to the continued growth and dominance of each legacy company's individual offerings, now compounded to leverage the expertise of the team and, ultimately, better serve loyal UOS customers all over the world. UOS will build upon the market positions of each legacy company, while serving as a single source supplier of specialty equipment and services for the utility and heavy equipment industries. Show less
-
-
-
Vitality Business Group
-
Roanoke, Virginia
-
Managing Director
-
Sep 2014 - Feb 2016
Principle process improvement consultant of boutique consulting firm focused on delivering operational strategy solutions and implementation support. Worked with small and mid-sized businesses across several industries helping them improve financial health and strategic positioning. Increased revenue growth and organizational capabilities through strategic partnerships. Principle process improvement consultant of boutique consulting firm focused on delivering operational strategy solutions and implementation support. Worked with small and mid-sized businesses across several industries helping them improve financial health and strategic positioning. Increased revenue growth and organizational capabilities through strategic partnerships.
-
-
-
Exelis (Now part of Harris Corporation)
-
Defense and Space Manufacturing
-
700 & Above Employee
-
Operations Engineering Manager
-
Jul 2008 - Aug 2014
Fast-paced manufacturing environment with responsibility to continuously evolve manufacturing operations to meet market demands and new product development requirements with favorable operating expense; Utilized data collection, industrial process automation, machine vision, and robotic integrations to continuously improve throughput and quality while reducing labor, rework and scrap; Oversaw transition to configurable manufacturing architecture across many value streams; Lead multiple projects… Show more Fast-paced manufacturing environment with responsibility to continuously evolve manufacturing operations to meet market demands and new product development requirements with favorable operating expense; Utilized data collection, industrial process automation, machine vision, and robotic integrations to continuously improve throughput and quality while reducing labor, rework and scrap; Oversaw transition to configurable manufacturing architecture across many value streams; Lead multiple projects to support operational turnaround for defense contractors manufacturing night vision and communication systems while managing daily manufacturing operations. Oversaw $1,106,700 combined annual operational cost savings for 2014 continuous improvement projects. • Increased Assembly capacity 30% through multiple CI projects encompassing full spectrum of Lean Six Sigma tools and methodologies. • Reduced training time for clean room spot welding from 4 weeks to 3 days through process re-design. • Reduced operational demand on engineering resources 75% through automated visual factory and statistical process controls. • Improved part assembly yield process 5% through development of automated assembly process. • Decreased component parts cost 35% by leading suppliers through DMAIC improvement projects. • Minimized cost of hermetic metal-glass seal 40% through process redesign and supplier collaboration. • Curtailed assembly operations footprint requirement 20% and reduced footprint of classified area 75% through Kaizen event. • Improved downstream yield for high-cost operations 5% through development of fully integrated and automated quality control test. Networked database used extensively to improve process performance. Show less Fast-paced manufacturing environment with responsibility to continuously evolve manufacturing operations to meet market demands and new product development requirements with favorable operating expense; Utilized data collection, industrial process automation, machine vision, and robotic integrations to continuously improve throughput and quality while reducing labor, rework and scrap; Oversaw transition to configurable manufacturing architecture across many value streams; Lead multiple projects… Show more Fast-paced manufacturing environment with responsibility to continuously evolve manufacturing operations to meet market demands and new product development requirements with favorable operating expense; Utilized data collection, industrial process automation, machine vision, and robotic integrations to continuously improve throughput and quality while reducing labor, rework and scrap; Oversaw transition to configurable manufacturing architecture across many value streams; Lead multiple projects to support operational turnaround for defense contractors manufacturing night vision and communication systems while managing daily manufacturing operations. Oversaw $1,106,700 combined annual operational cost savings for 2014 continuous improvement projects. • Increased Assembly capacity 30% through multiple CI projects encompassing full spectrum of Lean Six Sigma tools and methodologies. • Reduced training time for clean room spot welding from 4 weeks to 3 days through process re-design. • Reduced operational demand on engineering resources 75% through automated visual factory and statistical process controls. • Improved part assembly yield process 5% through development of automated assembly process. • Decreased component parts cost 35% by leading suppliers through DMAIC improvement projects. • Minimized cost of hermetic metal-glass seal 40% through process redesign and supplier collaboration. • Curtailed assembly operations footprint requirement 20% and reduced footprint of classified area 75% through Kaizen event. • Improved downstream yield for high-cost operations 5% through development of fully integrated and automated quality control test. Networked database used extensively to improve process performance. Show less
-
-
-
O'Neal Steel
-
United States
-
Mining
-
500 - 600 Employee
-
Inventory Control Specialist
-
Oct 2006 - Jul 2008
Cross-functional responsibilities focusing primarily on improving inventory control through process improvement and supply chain management. Played critical role in the selection and conversion of core operations business system. • Reduced 1st year annual physical inventory variance 90% through continuous improvement and new technology deployment. • Lowered raw material footprint 40% and facilitated mixed part initial stage processing through collaborative project which led to redesign of… Show more Cross-functional responsibilities focusing primarily on improving inventory control through process improvement and supply chain management. Played critical role in the selection and conversion of core operations business system. • Reduced 1st year annual physical inventory variance 90% through continuous improvement and new technology deployment. • Lowered raw material footprint 40% and facilitated mixed part initial stage processing through collaborative project which led to redesign of raw materials purchasing, consumption and processing. •Reduced 1st year annual physical inventory variance 90% by developing and deploying inventory control program based upon mapping of virtual business system and manufacturing processes. •Lowered raw material footprint 40% and facilitated mixed part initial stage processing through collaborative project, including PMs and Operations, which led to redesign of raw materials purchasing and processing. Show less Cross-functional responsibilities focusing primarily on improving inventory control through process improvement and supply chain management. Played critical role in the selection and conversion of core operations business system. • Reduced 1st year annual physical inventory variance 90% through continuous improvement and new technology deployment. • Lowered raw material footprint 40% and facilitated mixed part initial stage processing through collaborative project which led to redesign of… Show more Cross-functional responsibilities focusing primarily on improving inventory control through process improvement and supply chain management. Played critical role in the selection and conversion of core operations business system. • Reduced 1st year annual physical inventory variance 90% through continuous improvement and new technology deployment. • Lowered raw material footprint 40% and facilitated mixed part initial stage processing through collaborative project which led to redesign of raw materials purchasing, consumption and processing. •Reduced 1st year annual physical inventory variance 90% by developing and deploying inventory control program based upon mapping of virtual business system and manufacturing processes. •Lowered raw material footprint 40% and facilitated mixed part initial stage processing through collaborative project, including PMs and Operations, which led to redesign of raw materials purchasing and processing. Show less
-
-
-
Marine Corps Recruiting
-
Armed Forces
-
700 & Above Employee
-
Aviation Life Support Technician
-
Jul 1997 - Jul 2002
Held E-5 rank; served in 3 overseas deployments. • Recipient of Afghanistan Campaign Medal and Navy Achievement Medal. Held E-5 rank; served in 3 overseas deployments. • Recipient of Afghanistan Campaign Medal and Navy Achievement Medal.
-
-
Education
-
University of Virginia Darden School of Business
Master of Business Administration (M.B.A.), Business Administration and Management, General -
Cheung Kong Graduate School of Business
International Executive Leadership -
University of Virginia
Bachelor's Degree, Business Administration, Management and Operations
Community
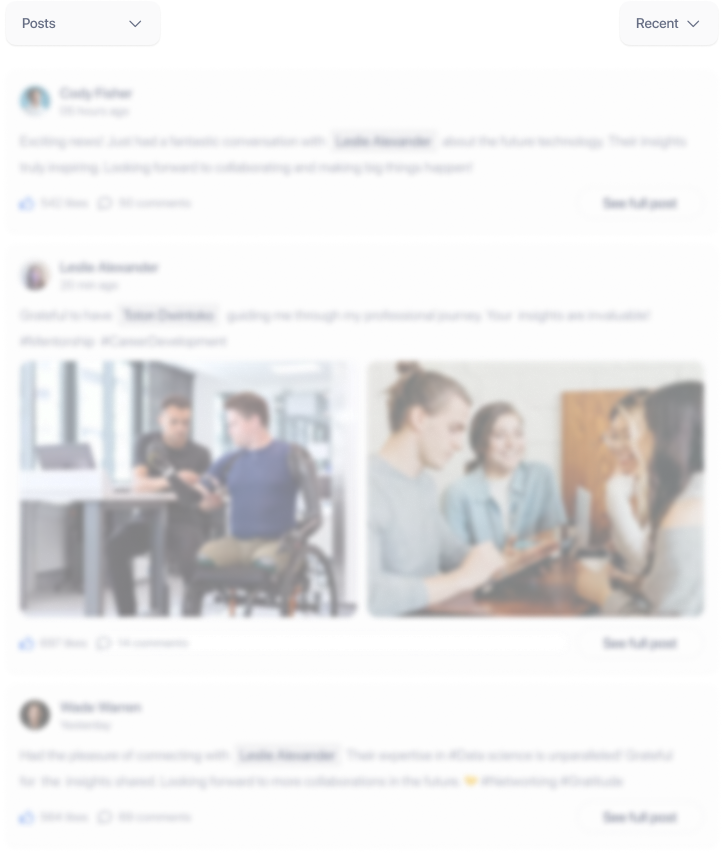