Cecil McCreery
Manager, Supply Chain Operations Analysis at American Soda LLP- Claim this Profile
Click to upgrade to our gold package
for the full feature experience.
Topline Score
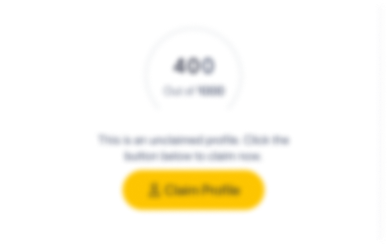
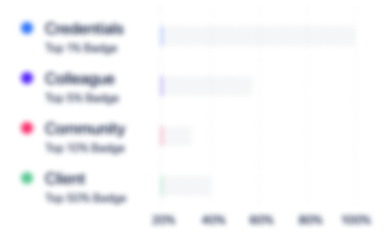
Bio

Curtis Bell
Cecil is a very dedicated and skilled professional in manufacturing with excellent systems skills. I worked with Cecil while implementing an ERB system (SAP) and found him to be very collaborative and an essential resource to making the implementation successful. I recommend Cecil to employers and would gladly be a reference. Regards, Curtis.

Bill Doyle
While working with Cecil I found him to be a seasoned professional, very knowledgable with the ERP system (SAP) that was used and a highly motivated team member.

Curtis Bell
Cecil is a very dedicated and skilled professional in manufacturing with excellent systems skills. I worked with Cecil while implementing an ERB system (SAP) and found him to be very collaborative and an essential resource to making the implementation successful. I recommend Cecil to employers and would gladly be a reference. Regards, Curtis.

Bill Doyle
While working with Cecil I found him to be a seasoned professional, very knowledgable with the ERP system (SAP) that was used and a highly motivated team member.

Curtis Bell
Cecil is a very dedicated and skilled professional in manufacturing with excellent systems skills. I worked with Cecil while implementing an ERB system (SAP) and found him to be very collaborative and an essential resource to making the implementation successful. I recommend Cecil to employers and would gladly be a reference. Regards, Curtis.

Bill Doyle
While working with Cecil I found him to be a seasoned professional, very knowledgable with the ERP system (SAP) that was used and a highly motivated team member.

Curtis Bell
Cecil is a very dedicated and skilled professional in manufacturing with excellent systems skills. I worked with Cecil while implementing an ERB system (SAP) and found him to be very collaborative and an essential resource to making the implementation successful. I recommend Cecil to employers and would gladly be a reference. Regards, Curtis.

Bill Doyle
While working with Cecil I found him to be a seasoned professional, very knowledgable with the ERP system (SAP) that was used and a highly motivated team member.

Experience
-
American Soda LLP
-
United States
-
Chemical Manufacturing
-
1 - 100 Employee
-
Manager, Supply Chain Operations Analysis
-
Jan 2015 - Present
Supply Chain Operations Analysis - coordinates with the Supply Chain team and executive management to get a firm handle on supply chain spending. Develop and publish monthly spend detailing logistics fixed and variable costs, budget vs. actual, and SG&A expenses. Enhanced and publish daily the NA GBU "story board" illustrating plant production, open and filled customer orders, plan vs. actual. Review, validate, and publish operational metrics, SC Spend, OTD, Perfect Order, dwell, production/shipments actual vs. forecast, safety, customer complaint, detention invoice track, plant loading reports, and executive dashboards. - Maintain a firm handle on Supply Chain operation costs. Recommend changes/improvements (project team member to improve SAP cost visibility to be able to provide management with cost to serve analysis. - Develop, prepare, and maintain Supply Chain fixed operating budget and BFR updates (quarterly). - Manage month end closing activities for Supply Chain logistics fleet. Multi-step process that takes place all month long cumulating to the three final steps on the first three days of each month. Develop, prepare, publish, and maintain Supply Chain metrics. Sample attached. Show less
-
-
-
Nalco Champion
-
United States
-
Oil and Gas
-
700 & Above Employee
-
Senior Supply Chain Analyst
-
May 2013 - Dec 2014
This position is a continuation of the Global Supply Chain Analyst II position with Champion Technologies after the purchase and merge with Nalco Champion.
-
-
Global Supply Chain Analyst II
-
Feb 2012 - May 2013
My position manages the gathering and reporting of the Global Supply Chain KPIs and external benchmarking information to Nalco Champion stakeholders (such as product delivery metric series, competitive product cost, optimum inventory). I perform periodic reviews of the Global Supply Chain capabilities and identify high value improvement opportunities. I partner with business users to understand and analyze business problems and define business needs for new products, services, or business processes. I also provide analytical support through data extraction and interpretation from various data sources and work with IT to develop and implement best-in-class software tools (such as Tableau Software, BW) to distribute and communicate critical information. I provide coaching and mentoring of less experienced analysts. Show less
-
-
Global Production Planner
-
May 2010 - Apr 2012
* Providing planning, analysis, scheduling, control and direction necessary at a strategic, global level to ensure product requirements, schedules and performance/improvement targets are met.*Using Super-User level SAP knowledge, perform and manage material requirements planning, capacity planning, production order creation and management, demand management and long term planning along with inventory management.* Researches seasonality and sales trends for production forecast, helps in the creation of the S&OP process, apprises upper management on material and capacity constraints, develops standard operation procedures and daily and weekly production plans and schedules to meeting company objectives. Show less
-
-
-
-
Unemployed
-
2008 - 2010
-
-
-
Thermo Fisher Scientific
-
United States
-
Biotechnology Research
-
700 & Above Employee
-
Operations Control Analyst
-
2003 - Oct 2008
Analyst responsible for manufacturing cost controls, manufacturing and supply chain process improvements, performance metrics, SAP user support, training and documentation, SAP implementations and upgrades, SAP process improvement and interface, data analysis and lean manufacturing. • Dramatically reduced production order cost variances by 448%, $224,000 to $50,000, the first month after operations planning and finance teams were trained on what production order cost variances were and how to correct and monitor them prior to month end reporting. • Supply chain subject matter expert – covering SAP modules MM/PP/VC/CO/IM. Cross-functionally supported the SD/SM/FI/QM modules as they impacted the supply chain. • Implemented forecast tracking report used to eliminate unused forecasts that negatively impacted inventory levels. • Documentation – created over 100 SAP business process, specifications and critical function procedures. Created and processed more than 70 SAP ECC 6.0 upgrade scripts as the supply chain team lead. • Tracked, analyzed and reported 25 performance metrics used to improve end-to-end processes and benchmark against corporate goals. • Project manager leading a team to transfer manufacturing and sourcing of a product to a facility in Shanghai, China. • Supply chain team lead for full life cycle SAP version 4.6c implementation – completed in three months with revenue generated on go live; supply chain team consultant for full life cycle implementation for second business unit site; team lead for merging two plant codes into one; supply chain team lead for corporation’s version upgrade to ECC 6.0. • Created the process, purchased and set up the equipment and trained all impacted personnel on SAP Kanban. Process applied to the lean manufacturing assembly lines that helped reduce component shortages and improved assembly times. Show less
-
-
-
-
Director of Manufacturing Texas Operations
-
2001 - 2002
Responsible for the leadership and direction of the manufacturing, planning and shipping functions for this $40+ million facility.• Supply chain team leader for the corporation’s first SAP implementation – 100% of all goals achieved with revenue generated on the go-live date.• Coordinated the move of three Thermo satellite plants into main facility, reducing the corporation’s square footage by 218,462. • Implemented manufacturing cells to replace existing assembly bays - improved product throughput and efficiency resulting in a reduction in cycle time and an improvement in on time deliveries. Show less
-
-
Operations Manager
-
Jan 2000 - Dec 2000
Hands-on Operations Manager with strong people and team-building skills who helped produce revenues of $8,000,000.• Re-designed the production floor layout to improve product flow from the warehouse, thru production to shipping resulting in a reduction in manufacturing cycle time.
-
-
-
-
Inside Sales Manager
-
1995 - 2000
-
-
Education
-
West Texas A&M University
MS, Industrial Technology -
West Texas A&M University
BS, Industrial Technology
Community
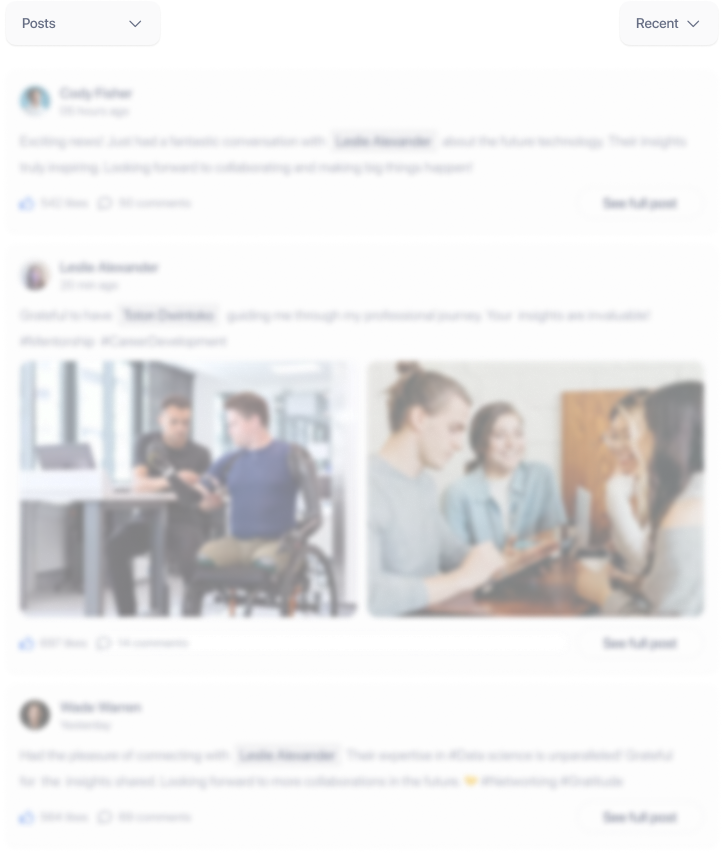