Clint Ditmore
Director of TRP Development & Special Markets at PACCAR Parts- Claim this Profile
Click to upgrade to our gold package
for the full feature experience.
Topline Score
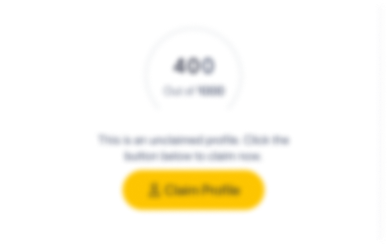
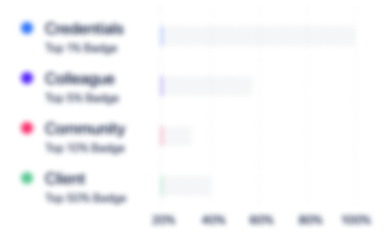
Bio

LinkedIn User
I had the opportunity and pleasure to work together with Clint Ditmore on the same project and it was really a great experience. He has a knowledge and domain regarding PACCAR requirements, besides being an easy person to deal and focused on the goal.

LinkedIn User
I had the opportunity and pleasure to work together with Clint Ditmore on the same project and it was really a great experience. He has a knowledge and domain regarding PACCAR requirements, besides being an easy person to deal and focused on the goal.

LinkedIn User
I had the opportunity and pleasure to work together with Clint Ditmore on the same project and it was really a great experience. He has a knowledge and domain regarding PACCAR requirements, besides being an easy person to deal and focused on the goal.

LinkedIn User
I had the opportunity and pleasure to work together with Clint Ditmore on the same project and it was really a great experience. He has a knowledge and domain regarding PACCAR requirements, besides being an easy person to deal and focused on the goal.

Experience
-
PACCAR Parts
-
United States
-
Truck Transportation
-
500 - 600 Employee
-
Director of TRP Development & Special Markets
-
Mar 2021 - Present
Responsible for the centralization and execution of all TRP functions including TRP sales, new TRP store expansion, TRP store support and program development for the US and Canada. Responsible for developing strategic initiatives to drive brand loyalty and increasing the overall breadth of product of the brand. Responsible for leading the development and execution of the Special Markets program including developing strategic initiatives, increasing sales and dealer engagement.
-
-
TRP Development Manager
-
Aug 2019 - Mar 2021
TRP Development Manager responsible for the centralization and execution of all TRP functions including TRP sales, new TRP store expansion, TRP store support, sourcing and program development. Responsible for developing strategic initiatives to drive brand loyalty and increasing the overall breadth of product of the brand.
-
-
Sr. Product Director
-
Mar 2016 - Aug 2019
Senior Product Director for PACCAR Parts responsible for managing the Options and Accessories Strategic Business Unit responsible by identifying market requirements, managing product offerings, managing supplier relationships, determining distribution and pricing strategies, and developing promotion and advertising plans to help achieve established profit and sales objectives.
-
-
-
PACCAR
-
United States
-
Motor Vehicle Manufacturing
-
700 & Above Employee
-
SAP Materials Manager
-
Jul 2014 - Mar 2016
SAP Materials Manager responsible for the creation and governance of the SAP Materials Global Template. Led the North American Materials Team during the initial go-live, ramp up and stabilization of the Brasil Assembly Plant in Ponta Grossa, Brasil. Managed a team of 10 members located in five different locations in the United States, Canada and Mexico. Responsible for the successful implementation of SAP modules MM, PP, YM and WM and post go-live stabilization support. Responsible for all day to day activities for the North American Materials Team as well as planning and forecasting for future SAP implementations. • Liaison between Operations and ITD• Responsible for European supplier EDI implementation • Traveled extensively to Brasil • Led the change management process in Brasil with both the SAP Business teams and with the organization in Brasil• Managed the Plan to Make team to complete the Realization phase throughout the first half of the year while making all key milestones and go live for SAP as per the approved timeline Show less
-
-
Acting Director SAP Materials
-
Jul 2013 - Jun 2014
Acting Director SAP Materials responsible for leading the North American Materials Team during the initial go-live and ramp up of the Brasil Assembly Plant. Led a team of 10 members located in five different areas in the United States, Canada and Mexico. Responsible for the successful implementation of SAP modules MM, PP, YM and WM and post go-live stabilization support. Responsible for all day to day activities for the NAMS team as well as planning and forecasting for future SAP implementations. • Coordinated communication with all business units • Led communication with the Brasil Assembly Plant• Traveled extensively to Brasil in this effort• Led the change management process in Brasil with both the SAP Business teams and with the organization in Brasil• Managed the P2P team to complete the Realization phase throughout the first half of the year while making all key milestones and go live for SAP as per the approved timeline Show less
-
-
Manager
-
Oct 2011 - Jul 2013
SAP Product Manager
-
-
SAP Business Analyst
-
Oct 2007 - Oct 2011
- Gathered and developed business requirements for the Columbus Engine Factory. This was a continuous process as the requirements as well as the scope of the project changed frequently.- Assisted in the configuration of the SAP WM module to meet the needs of the business- Developed training materials for the WM process- Developed scripts to accurately test the SAP system to ensure it was performing as designed- Worked directly with the users during UAT (User Acceptance Testing) to ensure they were properly trained and understood the system functionalities and capabilities- Developed material handling standard operating procedures for green field plant. - Traveled to the Netherlands and Mississippi to ensure multi team cohesion and cooperation Show less
-
-
Assistant Materials Manager
-
May 2006 - Sep 2007
- Responsible for a four shift, 117 person staff covering a 24 hours a day seven days a week operation (both salaried and union employees)- Liaison between materials and all other departments. Developed and implemented policies and procedures for material handing operations, resulting in standardized processes- Responsible for succession planning and employee development of entire department - Served as Operations Lead for High Impact Kaizen Event (HIKE)
-
-
Area Manager - Material Handling
-
Nov 2005 - May 2006
- Responsible for first shift Material Handling Operations including shipping, receiving and warehousing- Worked directly with the production and quality departments to mitigate shortages and quality issues- Responsible for all first shift material handling operations and personnel- Managed staff of three salaried members and 60 plus union members- Responsible for the development and administration of material handling union advancement testing procedures ensuring proper adherence to the union contract Show less
-
-
Unit Manger - Material Handling
-
Feb 2005 - Nov 2005
- Responsible for 23 union direct reports in the Frame Department- Worked directly with my production supervisor counterpart to mitigate shortages and ensure outstanding customer service was delivered- Implemented the largest company outsourced kitting and sequencing program for the Frame Floor - Worked directly with the department ME's to develop more efficient and safer material handling equipment and procedures
-
-
-
-
Production Supervisor
-
May 2002 - Feb 2005
- First shift Production Supervisor including Quality Control and - Managed daily activities for a staff of 45 plus union members - Departmental Safety Element Leader for emergency evacuation procedures for Seattle facility - Responsible for interviewing and hiring all seasonal and full time production employees - Worked directly with the production planner to accurately forecast production plans to satisfy volumes - First shift Production Supervisor including Quality Control and - Managed daily activities for a staff of 45 plus union members - Departmental Safety Element Leader for emergency evacuation procedures for Seattle facility - Responsible for interviewing and hiring all seasonal and full time production employees - Worked directly with the production planner to accurately forecast production plans to satisfy volumes
-
-
-
PepsiCo
-
United States
-
Food and Beverage Services
-
700 & Above Employee
-
Product Availability Supervisor
-
May 2000 - May 2002
- Second shift Product Availability Supervisor responsible shipping and receiving activities - Departmental Safety Coordinator - Managed daily activities for a staff of 30 plus union members - Responsible for on time and accurate deliveries for 75K case per night operation - Responsible for interviewing and hiring all seasonal and full time production employees - Second shift Product Availability Supervisor responsible shipping and receiving activities - Departmental Safety Coordinator - Managed daily activities for a staff of 30 plus union members - Responsible for on time and accurate deliveries for 75K case per night operation - Responsible for interviewing and hiring all seasonal and full time production employees
-
-
-
PACCAR
-
United States
-
Motor Vehicle Manufacturing
-
700 & Above Employee
-
Unit Manger Material Handling
-
Aug 1998 - Mar 2000
- Responsible for first shift shipping and receiving operations for a volume of 105 trailers per week - Managed daily activities for a staff of 13 plus union members - Directed activities to control $12.5M of warehouse inventory - Improved Statistical Audit results from 94.1% to 97.2% - Responsible for first shift shipping and receiving operations for a volume of 105 trailers per week - Managed daily activities for a staff of 13 plus union members - Directed activities to control $12.5M of warehouse inventory - Improved Statistical Audit results from 94.1% to 97.2%
-
-
-
-
Job Site Coordinator
-
Apr 1995 - Aug 1998
- Managed subcontractors on multiple sites throughout the Puget Sound region - Responsible for managing overall project costs ensuring profit margins were obtained - Ensured all jobs were completed on time, within budget and to customers satisfaction - Managed subcontractors on multiple sites throughout the Puget Sound region - Responsible for managing overall project costs ensuring profit margins were obtained - Ensured all jobs were completed on time, within budget and to customers satisfaction
-
-
-
-
Director of Operations
-
Jul 1996 - Aug 1997
- Responsible for all daily operational procedures - Responsible for hiring, orientating and training of all staff members - Responsible for forecasting sales and ordering supplies in order to meet market needs - Maintained all company financial records - Responsible for all daily operational procedures - Responsible for hiring, orientating and training of all staff members - Responsible for forecasting sales and ordering supplies in order to meet market needs - Maintained all company financial records
-
-
-
-
Assistant Manager
-
Jun 1994 - Jul 1996
Responsible for scheduling of 25 person staff - Responsible for hiring, orientating and training of all staff members - Expedited $160K in weekly deliveries ensuring overstock was at a minimum in order to maintain quality assurance standards Responsible for scheduling of 25 person staff - Responsible for hiring, orientating and training of all staff members - Expedited $160K in weekly deliveries ensuring overstock was at a minimum in order to maintain quality assurance standards
-
-
-
US Navy
-
United States
-
Armed Forces
-
700 & Above Employee
-
Petty Officer 3rd Class
-
Jun 1991 - Jun 1994
- Played instrumental role in preparing for Board of Inspection and Survey resulting in certification of the Sales and Services Division - Responsible for collection of cash and maintaining of all records from operation sources - Honorable Discharge with impeccable service record and three Letters of Appreciation - Played instrumental role in preparing for Board of Inspection and Survey resulting in certification of the Sales and Services Division - Responsible for collection of cash and maintaining of all records from operation sources - Honorable Discharge with impeccable service record and three Letters of Appreciation
-
-
Education
-
City University
Masters, Business
Community
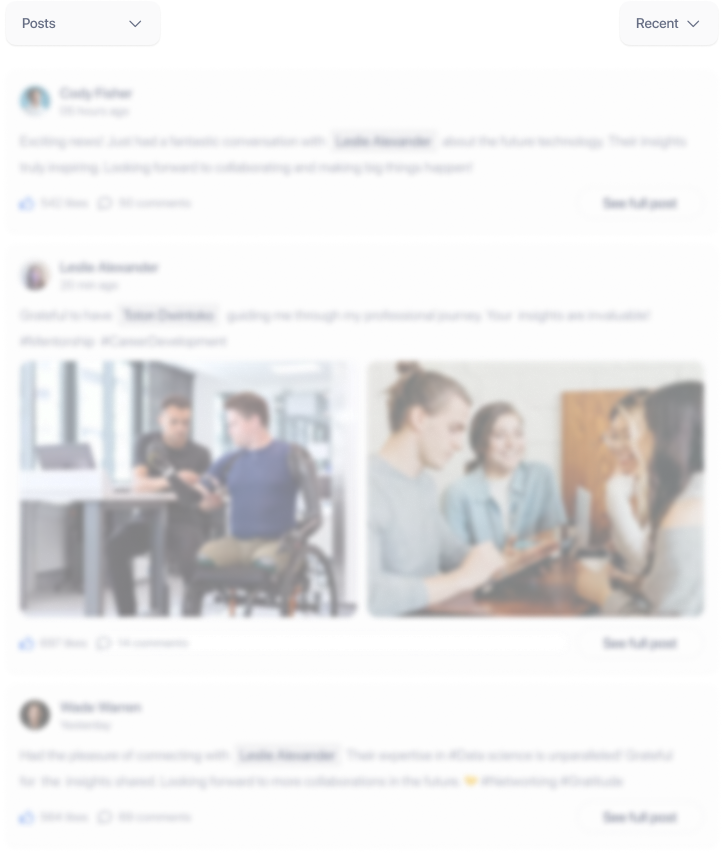