Clayton Mills
Operations Manager at Universal Logistics Holdings, Inc.- Claim this Profile
Click to upgrade to our gold package
for the full feature experience.
Topline Score
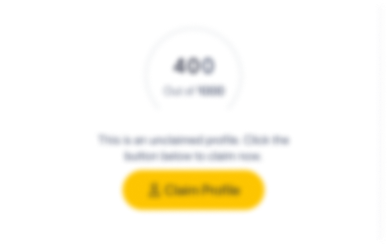
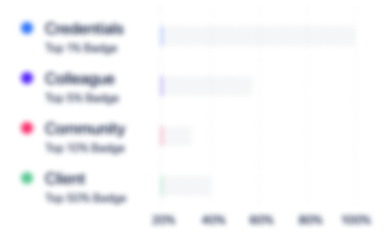
Bio


Experience
-
Universal Logistics Holdings, Inc.
-
United States
-
Truck Transportation
-
700 & Above Employee
-
Operations Manager
-
May 2022 - Present
Ripon, Wisconsin, United States
-
-
-
-
Owner / Broker
-
Feb 2018 - Present
-
-
-
Green Valley Enterprises Inc
-
United States
-
Hospitals and Health Care
-
1 - 100 Employee
-
Director - Campus Services
-
Aug 2020 - May 2022
-
-
-
-
Operations Production & Sales Manager
-
Sep 2019 - Jul 2021
Beaver Dam, Wisconsin https://www.greenvalleyinc.org
-
-
-
Arrowhead Conveyor LLC
-
United States
-
Industrial Automation
-
1 - 100 Employee
-
Shipping Supervisor
-
Feb 2016 - Feb 2019
Oshkosh, Wisconsin Area Managed the logistics of customer order shipments across the globe. Led a team of shipping attendants in the crating, packaging, organization, shipping, and storage of customer orders. Organized the shipping storage, layout, and operations of the off-site satellite facility. Created standard operating procedures for crating various types of conveyor. Negotiated vendor discount rates with freight brokers alongside the Supply Chain Manager. Arrowhead Systems, Inc. is the industry leader in… Show more Managed the logistics of customer order shipments across the globe. Led a team of shipping attendants in the crating, packaging, organization, shipping, and storage of customer orders. Organized the shipping storage, layout, and operations of the off-site satellite facility. Created standard operating procedures for crating various types of conveyor. Negotiated vendor discount rates with freight brokers alongside the Supply Chain Manager. Arrowhead Systems, Inc. is the industry leader in providing conveyor, packaging machinery and line productivity solutions to customers in the food, beverage, personal care, container manufacturing, household products, pharmaceutical and many other industry sectors. • Constructed a shipping TMS brokerage plan that would have saved $79,000/year in outbound shipping costs if used • Redesigned shipping crate bottoms to save 146 labor hours a year in crating construction • Created a 26-point pre-inspection checklist to reinsure the integrity and safety of crated customer orders before leaving • Generated 12 new Standard Operating Procedures to standardize shipping procedures Show less
-
-
-
Richelieu Foods
-
United States
-
Food and Beverage Manufacturing
-
100 - 200 Employee
-
Logistics Supervisor
-
Feb 2015 - Sep 2015
Beaver Dam, Wisconsin Responsible for the shipping, receiving, line service, and warehousing activities of the plant supply chain. Managed 3 leads and up to 25 hourly employees and delegate responsibilities to their teams to meet daily production goals. Maintained the integrity of 19 forklifts, 9 electric pallet jacks, 2 yards tractors, and 11 trailers. Coordinated the flow and storage space of materials in the plant and two satellite warehouses. Richelieu Foods is the manufacturer behind many of the nation’s… Show more Responsible for the shipping, receiving, line service, and warehousing activities of the plant supply chain. Managed 3 leads and up to 25 hourly employees and delegate responsibilities to their teams to meet daily production goals. Maintained the integrity of 19 forklifts, 9 electric pallet jacks, 2 yards tractors, and 11 trailers. Coordinated the flow and storage space of materials in the plant and two satellite warehouses. Richelieu Foods is the manufacturer behind many of the nation’s top retailers’ corporate brand of frozen pizza. •Eliminated 18 months and $50,000 of past due invoices since taking over the forklift/pallet jack/tractor program • Micromanaged the supply chain invoice approval process in excess of $500,000 Show less
-
-
-
Oshkosh Defense
-
United States
-
Defense and Space Manufacturing
-
700 & Above Employee
-
PFEP - Materials Analyst - Team Coordinator
-
Apr 2014 - Nov 2014
Oshkosh, Wisconsin Area Coached a team of 10+ material coordinators in a union environment with their daily responsibilities to complete production goals. Led an operations and materials team of 10-25 employees on Saturdays to meet increased customer demand when necessary. Coordinated the layout, flow, and setup of materials in the E-Coat Facility using JD-Edwards ERP software. Collaborated with operations, engineering, purchasing, safety, and finance to complete projects and update KPI. Oshkosh Defense is a… Show more Coached a team of 10+ material coordinators in a union environment with their daily responsibilities to complete production goals. Led an operations and materials team of 10-25 employees on Saturdays to meet increased customer demand when necessary. Coordinated the layout, flow, and setup of materials in the E-Coat Facility using JD-Edwards ERP software. Collaborated with operations, engineering, purchasing, safety, and finance to complete projects and update KPI. Oshkosh Defense is a tactical vehicle manufacturer. Every day they strive to meet or exceed the customers’ ever-changing needs with next-generation defense technologies and advanced systems. • Skyrocketed the growth of Oshkosh Finishing Services to $1.37 million in annual revenue its first year • Created a warehouse elimination plan that cut over $420,000 a year in warehousing, equipment, and labor costs • Slashed daily open Kanban deliveries to South Plant by 75% through process improvement and analysis • Strengthened the work without lost time record at E-Coat from 139 days to 287 days Show less
-
-
-
Millenium Information Systems
-
United States
-
Financial Services
-
1 - 100 Employee
-
Field Inspector
-
May 2012 - Apr 2014
Itasca, Illinois Performed third-party audit and inspection services for an insurance underwriting company. Analyzed, reviewed, and uploaded 40 orders per week with review notes for underwriters to evaluate. Performed on-site surveys and measurements, photographed homes, documented hazards and liabilities. Gained self-management skills to set route, and complete customer orders independently. Millennium Information Services, Inc. is a national provider of property inspection services and innovative process… Show more Performed third-party audit and inspection services for an insurance underwriting company. Analyzed, reviewed, and uploaded 40 orders per week with review notes for underwriters to evaluate. Performed on-site surveys and measurements, photographed homes, documented hazards and liabilities. Gained self-management skills to set route, and complete customer orders independently. Millennium Information Services, Inc. is a national provider of property inspection services and innovative process management solutions for property and casualty insurance companies. • Diminished average personal completion time per residential home by 50% from job inception to finish • Extended workload volume of home inspections by 400% from May 2012 to April 2014 • Surged management territory by 300% by adding Green Lake, Waushara, and Adams Counties Show less
-
-
-
TW DESIGN
-
Brazil
-
Advertising Services
-
1 - 100 Employee
-
Supply Chain Intern
-
Jul 2011 - Feb 2012
Montello, Wisconsin Created cost/benefits analysis comparing various sub-contracting vendors. Developed remediation plans for vendors falling behind on purchase orders to ensure timely delivery. Revised office supplies re-order form in Excel to increase order accuracy and improve efficiency. Sent out and compared vendor RFQ’s on customer parts to acquire highest quality and lowest price. TW Design is a full service CNC machine shop that is dedicated to quality arts, and on-time delivery of precision CNC milled… Show more Created cost/benefits analysis comparing various sub-contracting vendors. Developed remediation plans for vendors falling behind on purchase orders to ensure timely delivery. Revised office supplies re-order form in Excel to increase order accuracy and improve efficiency. Sent out and compared vendor RFQ’s on customer parts to acquire highest quality and lowest price. TW Design is a full service CNC machine shop that is dedicated to quality arts, and on-time delivery of precision CNC milled and turned parts for small quantity, service or prototype parts, large volume blanket orders and temporary outsourcing of customer needs. • Mentored a team of up to 5 employees to take inventory of thousands of parts in 45 days • Collaborated with over 60 employees on ensuring customer orders were met in a timely manner • Solidified customer orders amounting to over $7 million in gross revenue
-
-
CNC Operator
-
Jul 2009 - Jul 2011
-
-
-
-
Contract Specialist
-
May 2008 - Sep 2009
-
-
-
-
Sales Associate
-
Oct 2008 - Jun 2009
-
-
Education
-
West Texas A&M University
Master of Business Administration - MBA, Business Administration and Management, General -
University of Wisconsin-Oshkosh
Bachelor's Degree, Supply Chain and Operations Management -
University of Wisconsin-Whitewater
Bachelor of Business Administration (B.B.A.), Logistics, Materials, and Supply Chain Management
Community
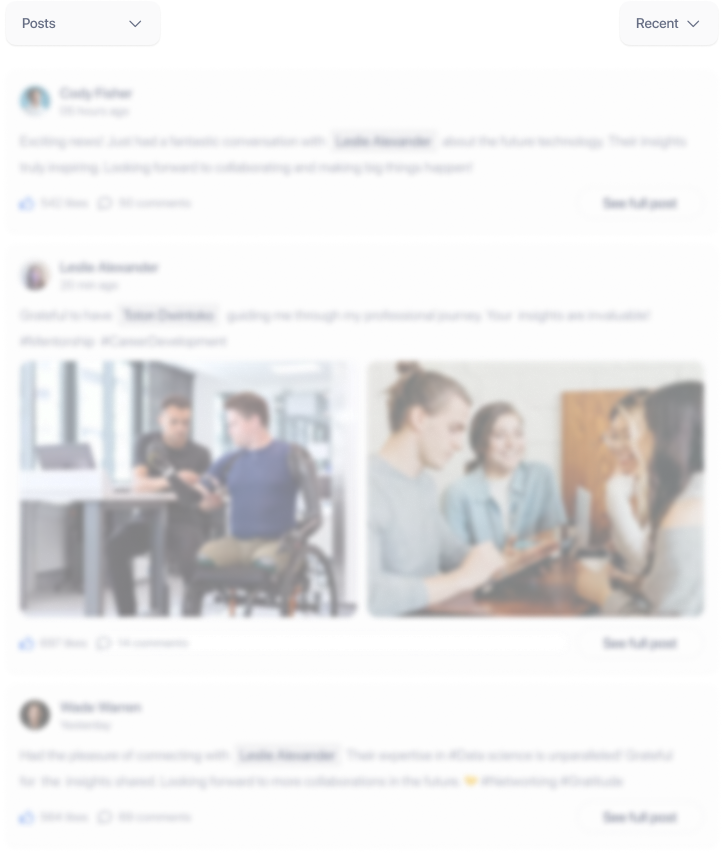