CHUCK KOERNER
Facilitator of semiconductor gas delivery systems at NSTAR Global Services- Claim this Profile
Click to upgrade to our gold package
for the full feature experience.
Topline Score
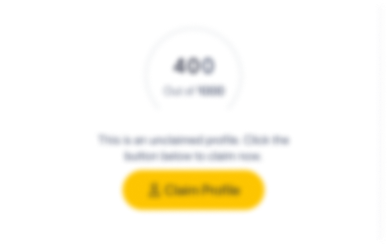
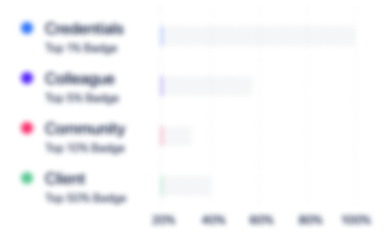
Bio
0
/5.0 / Based on 0 ratingsFilter reviews by:
Experience
-
NSTAR Global Services
-
Semiconductor Manufacturing
-
100 - 200 Employee
-
Facilitator of semiconductor gas delivery systems
-
Aug 2017 - Present
-
-
-
-
AUTOMOTIVE MECHANIC, and RESTORER
-
Sep 1990 - Present
• Mechanic on cars, boats, and motorcycles. • Performed full restorations on eight vehicles. • Skills as follows: Engines, Transmissions, Differentials, Suspension and front ends, bodywork, paint, upholstery, glass, and electrical systems. • Mechanic on cars, boats, and motorcycles. • Performed full restorations on eight vehicles. • Skills as follows: Engines, Transmissions, Differentials, Suspension and front ends, bodywork, paint, upholstery, glass, and electrical systems.
-
-
-
Micron Semiconductor
-
China
-
Business Consulting and Services
-
Senior Manufacturing Equipment Technician
-
Sep 2015 - Jul 2016
Maintained production equipment by supporting manufacturing requirements. Responded to daily production equipment issues, implemented solutions, reduced costs, and improved yield. Identified and resolved defect issues, audited recipes, assisted area technicians with routine maintenance, improved preventative maintenance procedures. Communicated with engineering and production personnel. Monitored, analyzed and addressed SPC issues on a daily basis. • Performed scheduled preventative… Show more Maintained production equipment by supporting manufacturing requirements. Responded to daily production equipment issues, implemented solutions, reduced costs, and improved yield. Identified and resolved defect issues, audited recipes, assisted area technicians with routine maintenance, improved preventative maintenance procedures. Communicated with engineering and production personnel. Monitored, analyzed and addressed SPC issues on a daily basis. • Performed scheduled preventative maintenance. Responded immediately to down equipment. When required, completed changeovers to run a different product line. Installed and removed equipment when needed, while working with facilities and equipment engineering. • Worked on the following systems: Ultra high vacuum, electronic and mechanical troubleshooting, water pumps, high voltage power supplies, pneumatics, linear and rotary motors, encoders and stepper motors, compressed gas delivery systems, and robotic handlers. • Utilized test equipment to determine the quality of product. Monitored SPC charts to verify equipment was running per production specifications. Show less Maintained production equipment by supporting manufacturing requirements. Responded to daily production equipment issues, implemented solutions, reduced costs, and improved yield. Identified and resolved defect issues, audited recipes, assisted area technicians with routine maintenance, improved preventative maintenance procedures. Communicated with engineering and production personnel. Monitored, analyzed and addressed SPC issues on a daily basis. • Performed scheduled preventative… Show more Maintained production equipment by supporting manufacturing requirements. Responded to daily production equipment issues, implemented solutions, reduced costs, and improved yield. Identified and resolved defect issues, audited recipes, assisted area technicians with routine maintenance, improved preventative maintenance procedures. Communicated with engineering and production personnel. Monitored, analyzed and addressed SPC issues on a daily basis. • Performed scheduled preventative maintenance. Responded immediately to down equipment. When required, completed changeovers to run a different product line. Installed and removed equipment when needed, while working with facilities and equipment engineering. • Worked on the following systems: Ultra high vacuum, electronic and mechanical troubleshooting, water pumps, high voltage power supplies, pneumatics, linear and rotary motors, encoders and stepper motors, compressed gas delivery systems, and robotic handlers. • Utilized test equipment to determine the quality of product. Monitored SPC charts to verify equipment was running per production specifications. Show less
-
-
-
Sonoscan
-
Hospitals and Health Care
-
1 - 100 Employee
-
Field Service Engineer
-
Jan 2012 - Mar 2015
Performed Customer Service on C-Mode scanning Acoustic Microscopes. • Installed, diagnosed, repaired, performed preventive maintenance and re-calibrated Sonoscan systems at customer sites throughout the western United States. • Used manufacturing and field service documentation to complete upgrades to equipment already in place. • Provided positive customer experiences by listening to, and resolving their equipment issues. Performed Customer Service on C-Mode scanning Acoustic Microscopes. • Installed, diagnosed, repaired, performed preventive maintenance and re-calibrated Sonoscan systems at customer sites throughout the western United States. • Used manufacturing and field service documentation to complete upgrades to equipment already in place. • Provided positive customer experiences by listening to, and resolving their equipment issues.
-
-
-
-
Field Service Support Engineer
-
Jun 2010 - Apr 2011
Contracted to decontaminate and remove manufacturing production equipment. Coordinated and with the Facilities team to shutoff and disconnect compressed gasses, water, and electrical and exhaust systems. • Interfaced with Applied Materials to meet Intel’s specified procedures and timelines. • Completed Intel’s and Applied Material’s intense safety training classes. • Complied with all safety procedures and consistently demonstrate safety as a value. Contracted to decontaminate and remove manufacturing production equipment. Coordinated and with the Facilities team to shutoff and disconnect compressed gasses, water, and electrical and exhaust systems. • Interfaced with Applied Materials to meet Intel’s specified procedures and timelines. • Completed Intel’s and Applied Material’s intense safety training classes. • Complied with all safety procedures and consistently demonstrate safety as a value.
-
-
-
-
Senior Manufacturing Equipment Technician
-
Jun 1993 - Feb 2009
Maintained production equipment by supporting manufacturing requirements. Responded to daily production equipment issues, implemented solutions, reduced costs, and improved yield. Identified and resolved defect issues, audited recipes, assisted area technicians with routine maintenance, improved preventative maintenance procedures. Communicated with engineering and production personnel. Monitored, analyzed and addressed SPC issues on a daily basis. • Performed scheduled preventative… Show more Maintained production equipment by supporting manufacturing requirements. Responded to daily production equipment issues, implemented solutions, reduced costs, and improved yield. Identified and resolved defect issues, audited recipes, assisted area technicians with routine maintenance, improved preventative maintenance procedures. Communicated with engineering and production personnel. Monitored, analyzed and addressed SPC issues on a daily basis. • Performed scheduled preventative maintenance. Responded immediately to down equipment. When required, completed changeovers to run a different product line. Installed and removed equipment when needed, while working with facilities and equipment engineering. • Worked on the following systems: Ultra high vacuum, electronic and mechanical troubleshooting, water pumps, high voltage power supplies, pneumatics, linear and rotary motors, encoders and stepper motors, compressed gas delivery systems, and robotic handlers. • Utilized test equipment to determine the quality of product. Monitored SPC charts to verify equipment was running per production specifications. Show less Maintained production equipment by supporting manufacturing requirements. Responded to daily production equipment issues, implemented solutions, reduced costs, and improved yield. Identified and resolved defect issues, audited recipes, assisted area technicians with routine maintenance, improved preventative maintenance procedures. Communicated with engineering and production personnel. Monitored, analyzed and addressed SPC issues on a daily basis. • Performed scheduled preventative… Show more Maintained production equipment by supporting manufacturing requirements. Responded to daily production equipment issues, implemented solutions, reduced costs, and improved yield. Identified and resolved defect issues, audited recipes, assisted area technicians with routine maintenance, improved preventative maintenance procedures. Communicated with engineering and production personnel. Monitored, analyzed and addressed SPC issues on a daily basis. • Performed scheduled preventative maintenance. Responded immediately to down equipment. When required, completed changeovers to run a different product line. Installed and removed equipment when needed, while working with facilities and equipment engineering. • Worked on the following systems: Ultra high vacuum, electronic and mechanical troubleshooting, water pumps, high voltage power supplies, pneumatics, linear and rotary motors, encoders and stepper motors, compressed gas delivery systems, and robotic handlers. • Utilized test equipment to determine the quality of product. Monitored SPC charts to verify equipment was running per production specifications. Show less
-
-
Education
-
Idaho State University
Associate’s Degree, Electronic Systems Technology -
Boise State University
Certificate in Auto Mechanics, Auto Mechanics
Community
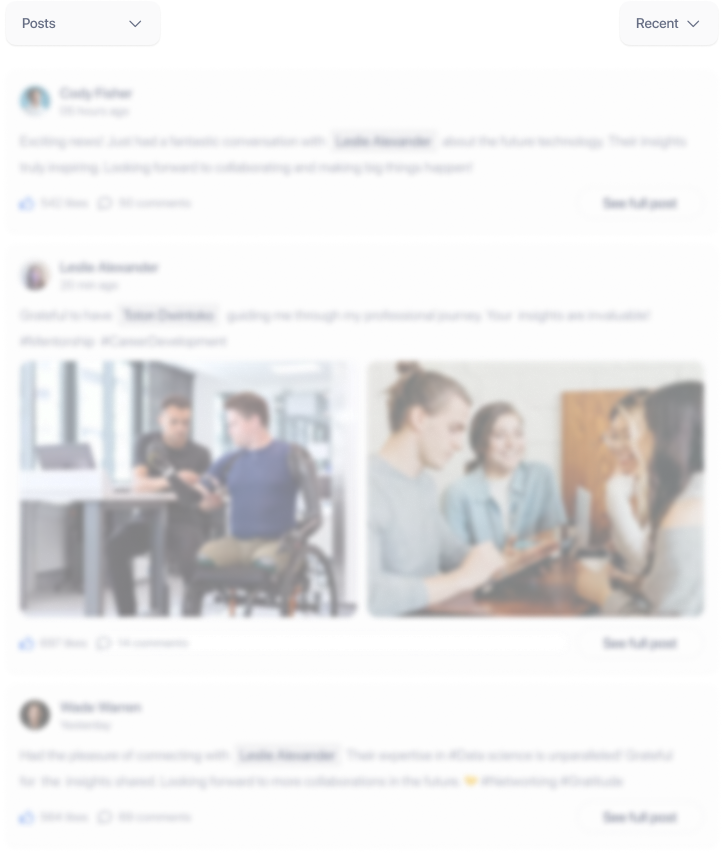