Christy Hardin
Quality Assurance Manager at DeepHealth- Claim this Profile
Click to upgrade to our gold package
for the full feature experience.
Topline Score
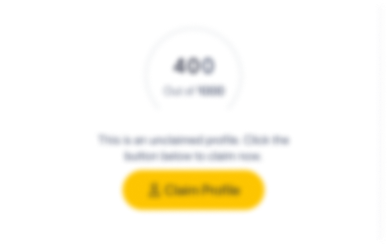
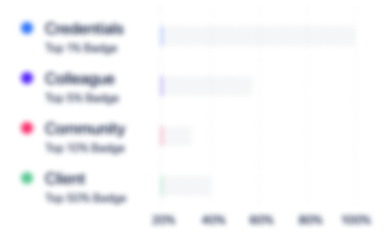
Bio


Experience
-
DeepHealth
-
United States
-
Hospitals and Health Care
-
1 - 100 Employee
-
Quality Assurance Manager
-
Nov 2021 - Present
-
-
-
Olympus Veran Technologies
-
United States
-
Medical Equipment Manufacturing
-
1 - 100 Employee
-
Quality System Manager / Quality Assurance Manager
-
Mar 2017 - Nov 2021
Responsible for all aspects of supporting and maintaining the quality assurance of products, processes, and services throughout the organization. Ensuring the ongoing suitability and effectiveness of the quality management system that meets FDA Quality System Requirements, Medical Devices Directive, and ISO 13485 Quality System standards.• Develop, implement, maintain, and improve quality management system procedures, work instructions, and associated forms in accordance with applicable standards and regulations (ISO 13485, FDA QSR, EU MDD, etc.).• Manage a team of 3 direct reports and 5 consultants.• Manage the complaint system that averages about 600 complaints a year. Complete activities related to Medical Device Reports (MDRs) and files with the FDA.• Manage corrective and preventative action (CAPA) related activities.• Manage internal quality system audits to ensure compliance to applicable standards and regulations (ISO 13485, FDA QSR, EU MDD, etc).• Quality representative for FDA inspections and Notified Body audits (surveillance, re-certification, and unannounced).• Manage document control and product acceptance activities, including nonconforming product, servicing, and return material.• Manage, create, and implement the training program on the quality system requirements across all departments, including new hires, process revisions, and training related to corrective actions.• Member of the design team for new product development and legacy products. Assists in the design process, label reviews, and provides guidance to product development teams throughout the product development process, including risk management, to ensure compliance to the required deliverables, resulting in the development of safe and effective medical devices.• Assist in the evaluation and qualification of suppliers including supplier audits, review of SCAR activities and effectiveness, and the creation of Supplier Quality Agreements. Show less
-
-
Quality Assurance Specialist
-
Feb 2015 - Mar 2017
• Provides Quality Engineering guidance to product development teams throughout the product development process to ensure compliance to the required deliverables, resulting in the development of safe and effective medical devices to include verification and validation activities.• Develop, implement, maintain, and improve quality management system procedures, work instructions, and associated forms in accordance with applicable standards and regulations (ISO 13485, FDA QSR, EU MDD, etc.).• Participates in complaint activities and corrective and preventive action (CAPA) related activities.• Complete internal audits and communicates significant issues or developments identified during internal audits and provide recommended improvements.• Analyzes data from various sources including but not limited to nonconformances, complaints, etc. to drive decision-making and effective corrective and preventative actions.• Reviews and approves work for inclusion in Medical Device Reports (MDRs) and provides support in the investigations of MDRs.• Managed and implemented the UDI labeling process.• Managed and implemented RoHS requirements for all manufactured products.• Recommends, leads, and/or supports projects for improvements to the Quality System.• Manages, creates, and implements the training program on the quality system requirements across all departments, including new hires, process revisions, and training related to corrective actions.• Assists in the evaluation and qualification of suppliers including supplier audits, review of SCAR activities and effectiveness, and the creation of Supplier Quality Agreements.• Manages company documents while also ensuring their accuracy, quality, and integrity. Show less
-
-
Quality Assurance Associate
-
Aug 2011 - Mar 2017
• Develop, implement, maintain, and improve quality management system procedures, work instructions, and associated forms in accordance with applicable standards and regulations (ISO 13485, FDA QSR, EU MDD, etc.).• Complete internal audits and communicates significant issues or developments identified during internal audits and provide recommended improvements.• Manages, creates, and implements the training program on the quality system requirements across all departments, including new hires, process revisions, and training related to corrective actions.• Complete incoming inspection, in-process inspection, and final review of all finished medical devices, including labeling, for release into inventory.• Interpret engineering documentation and interface with engineering and operations personnel by identifying and offering solutions to simple engineering problems.• Identified nonconforming parts, materials, and finished products, initiate the nonconforming product process, and participate in determining the disposition of the nonconforming product.• Managed company documents while also ensuring their accuracy, quality, and integrity. Show less
-
-
Executive Assistant
-
Oct 2008 - Aug 2011
Responsible for managing the day-to-day operations of the office which includes but is not limited to travel and meeting arrangements, inventory of office supplies, and customer service.
-
-
Education
-
University of Missouri-Saint Louis
Community
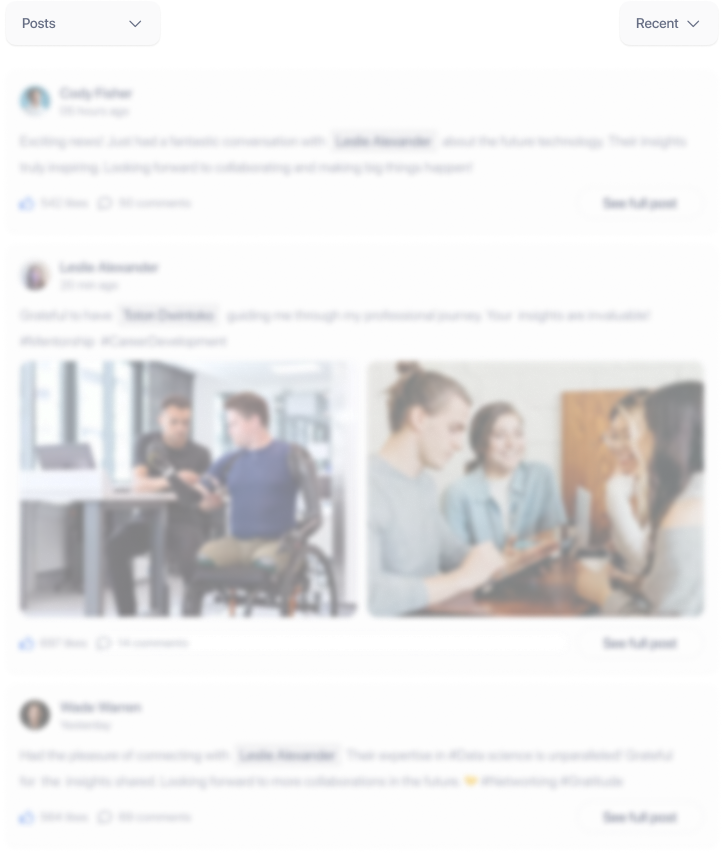