Christopher Koep - MS, CMQ-OE, CQE, SSGB, CQA, CSQP
Senior Quality Assurance Specialist, Auditor at MICRO- Claim this Profile
Click to upgrade to our gold package
for the full feature experience.
Topline Score
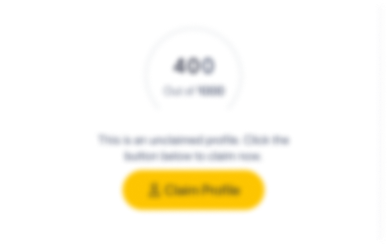
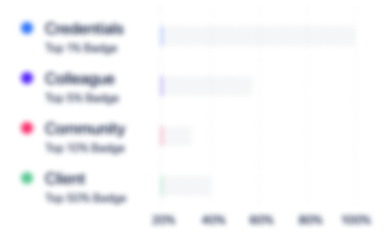
Bio

Jim Handzo
Chris reported directly to me and I must echo my colleague Michael Viscido's commendation of him as an "Engineer's Engineer". Chris is analytical and detail-oriented, following data, rather than opinion, to a conclusion. As a result, his recommendations work! And he does this in a fully collaborative way, always respectful of his co-workers. Chris is a consummate professional - experienced, knowledgeable, dedicated, mature, steady - and a lot of fun to work with! I heartily recommend Chris as a can't-miss teammate!

Michael V.
Chris has reported to my organization for over a year. I have always found him to be an excellent colleague. I hired Chris in to the Quality Engineering team and he made an impact right away. I find him to be smart, detail oriented and an outstanding problem solver. He is an

Jim Handzo
Chris reported directly to me and I must echo my colleague Michael Viscido's commendation of him as an "Engineer's Engineer". Chris is analytical and detail-oriented, following data, rather than opinion, to a conclusion. As a result, his recommendations work! And he does this in a fully collaborative way, always respectful of his co-workers. Chris is a consummate professional - experienced, knowledgeable, dedicated, mature, steady - and a lot of fun to work with! I heartily recommend Chris as a can't-miss teammate!

Michael V.
Chris has reported to my organization for over a year. I have always found him to be an excellent colleague. I hired Chris in to the Quality Engineering team and he made an impact right away. I find him to be smart, detail oriented and an outstanding problem solver. He is an

Jim Handzo
Chris reported directly to me and I must echo my colleague Michael Viscido's commendation of him as an "Engineer's Engineer". Chris is analytical and detail-oriented, following data, rather than opinion, to a conclusion. As a result, his recommendations work! And he does this in a fully collaborative way, always respectful of his co-workers. Chris is a consummate professional - experienced, knowledgeable, dedicated, mature, steady - and a lot of fun to work with! I heartily recommend Chris as a can't-miss teammate!

Michael V.
Chris has reported to my organization for over a year. I have always found him to be an excellent colleague. I hired Chris in to the Quality Engineering team and he made an impact right away. I find him to be smart, detail oriented and an outstanding problem solver. He is an

Jim Handzo
Chris reported directly to me and I must echo my colleague Michael Viscido's commendation of him as an "Engineer's Engineer". Chris is analytical and detail-oriented, following data, rather than opinion, to a conclusion. As a result, his recommendations work! And he does this in a fully collaborative way, always respectful of his co-workers. Chris is a consummate professional - experienced, knowledgeable, dedicated, mature, steady - and a lot of fun to work with! I heartily recommend Chris as a can't-miss teammate!

Michael V.
Chris has reported to my organization for over a year. I have always found him to be an excellent colleague. I hired Chris in to the Quality Engineering team and he made an impact right away. I find him to be smart, detail oriented and an outstanding problem solver. He is an

Credentials
-
Six Sigma Green Belt
ASQDec, 2013- Nov, 2024 -
Certified Seaman
United States Power SquadronsSep, 2009- Nov, 2024 -
Quality System Regulations (21 CFR 11 part 820)
Advancing Safety in Medical Technology (AAMI)Nov, 2014- Nov, 2024 -
ASQ - Certified Quality Engineer
ASQDec, 2011- Nov, 2024 -
Certified Manager of Quality - Operational Excellence
ASQOct, 2015- Nov, 2024 -
Certified Quality Auditor
ASQJun, 2016- Nov, 2024 -
Certified Supplier Quality Professional
ASQ - World HeadquartersNov, 2019- Nov, 2024 -
IPC-A-610
IPC-Association Connecting Electronics IndustriesFeb, 2015- Nov, 2024
Experience
-
MICRO
-
United States
-
Medical Device
-
200 - 300 Employee
-
Senior Quality Assurance Specialist, Auditor
-
Aug 2022 - Present
I am responsible for the Internal Audit process, scheduling and supervising regular internal audits, and shepherding any CAPAs generated from findings. Also becoming involved with coordinating Customer audits and cohosting regulatory audits. Working to improve various Quality processes, particularly GDP and associated training and general QMS awareness. I am responsible for the Internal Audit process, scheduling and supervising regular internal audits, and shepherding any CAPAs generated from findings. Also becoming involved with coordinating Customer audits and cohosting regulatory audits. Working to improve various Quality processes, particularly GDP and associated training and general QMS awareness.
-
-
-
Mallinckrodt Pharmaceuticals
-
Ireland
-
Pharmaceutical Manufacturing
-
700 & Above Employee
-
Senior Quality Specialist - Data Analytics and Data Integrity
-
2018 - 2022
Drafted into this new roll to help address FDA emphasis on Data Integrity compliance, getting specialized training to become one of a limited number of SMEs in the subject matter within the company. Also retained for my ability to analyze data and aid in complaint investigations.• Served as corporate Data Integrity (DI) SME, and as project manager for company wide Data Integrity assessment and remediation effort to prevent regulatory Data Integrity findings. Completed Phase I, II and III of long-term project. Developed methods and documentation to assess level of compliance. Also developed DI awareness training curriculum to educate employees based on their level of compliance responsibility, or specific impact on maintaining compliance. • Led Data Integrity assessment process for several manufacturing locations and functional areas to prepare for pre-production and other regulatory inspections. Guided other locations through process to successful remediation completion.• Worked with counterparts in Ireland to develop unified “Data Lake” for all reporting metrics. Utilized as a resource periodically for ad hoc reporting metrics for management leadership team as required because of my ability to extract, analyze and present data.• Analyzed Lot Release Testing (LRT) Data and Complaint data for Cellex product and linked issues experienced during LRT to customer complaints. Served as part of team effort to further improve product by digging deeper into underlying, difficult to pinpoint root causes of customer complaints.• Proposed to utilize LRT data to analyze CMO actions to clear alarms for insight into aiding product support actions and training.• Created searchable supplier and internal audit database and workbook to aid in additional management review data and metrics. Show less
-
-
Senior Quality Engineer
-
2017 - 2018
Mallinckrodt Quality representative to the CMOs producing components and kits for the Cellex Product line.• Analyzed Cellex Product complaint data and grouped into potential root cause categories to focus areas for potential improvement projects to reduce complaint rates, with analysis contributing to next generation of control software.• Gathered CMO performance metrics data for corporate metrics reporting. Compiled and presented customer returns/complaint data for tracking and trending of CMO investigation performance. Coached CMO investigators in proper documentation and root cause analysis.• Collaborated with existing CMO to develop them as second source for critical Drive Bowl Assembly components supporting Cellex kit production. Provided guidance, review, and approvals for validation activities as MNK corporate quality representative. Worked on site as needed to aid in troubleshooting quality issues, and failure analysis of returns.• Reconstructed and analyzed catastrophic field failure, and confirmed root cause, resulting in changes in production controls and design of ultrasonic weld to reduce incidence of failures significantly.• Performed supplier audits of MNK suppliers as needed in support of corporate supplier management process. Show less
-
-
-
B. Braun Medical Inc. (US)
-
United States
-
Medical Equipment Manufacturing
-
700 & Above Employee
-
Senior Supplier Quality Engineer - Class II Medical Device Manufacture
-
2016 - 2017
In my position at B. Braun Medical in Allentown as a Senior Quality Engineer for production support for the Kits and Pharmacy business unit, covering clean room manufacturing operations, Incoming inspection, outgoing Final Function, and I worked with the PIR group (complaints) resolving supplier corrective action requests linked to incoming material issues for those products within the business unit. I was also the QE for the Print Shop, where a large volume of labels are generated for use in production as lids for blister packs of a wide range of products shipped out of the Allentown facility. • Negotiated and executed 15 change / quality agreements with key suppliers in Q3 / Q4 2016, supporting quality plan of entering into agreements for all key suppliers by Q4 2017. • Reduced effort to calculate SCAN (supplier corrective action notification) quality data metrics by 80%, creating data workbook facilitating monthly and quarterly quality metrics and improving accuracy. • Supported Six Sigma green belt project in print shop, reducing non-conformances from six per month to less than one per month. • Led CAPA team and showed by analysis and careful experimentation that reducing upper limit of camera control value for one needle product by 18% did not affect overall process yield, detecting marginal needles resulting in customer complaints. Show less
-
-
-
St. Jude Medical
-
United States
-
Medical Equipment Manufacturing
-
700 & Above Employee
-
Senior Quality Engineer/Data Engineer - Class III Medical Device Manufacture
-
2010 - 2015
Quality Engineer for Final Assembly level IPGs (Implantable Pulse Generators for Pain control) and external products assembled in the Willow Grove location. Hired for my data analysis and metrics skills to address multiple items associated with extensive Form 483 findings and Warning Letter. • Investigated and processed non-conformances for final assembly level implantable pulse generators and related external products within 30 days, determining root cause and providing feedback and assigning actions to manufacturing, quality engineers, and supervisors. • Developed data collection and analysis processes, enabled tracking and trending of yields, rework, and scrap details from five different data collection systems, satisfying FDA finding. • Reduced future occurrences of defects by implementing improvements directly for items within quality assurance. • Implemented quality data review (QDR) process for New Jersey location, accepted and modeled in other locations. • Led continuous improvement team and implemented three projects, totaling over $150K in cost savings first year, transitioning to value stream teams by product area. • Served as CAPA coordinator and change request process disposition plan gate keeper, mentoring of entry level QEs and Six Sigma yellow belt candidates and quality representative to complaint review process. • Facilitated relocation activities for closing New Jersey location, writing, reviewing, and executing TMVs and PPQs, and becoming general quality resource for transfer activities as needed. Show less
-
-
-
Siemens
-
Germany
-
Automation Machinery Manufacturing
-
700 & Above Employee
-
Senior Quality Engineer/Project Manager - Class I Medical Device Manufacture
-
2002 - 2010
Started out as the Quality Liaison to R&D for new product development. Directed production of golden samples and laid out assembly details for new models to be sure they were suitable for manufacture and reliable from basic electrical design layout from R&D. Drafted into the newly formed Operational Excellence group (led by a Master Black Belt) when R&D was shifted to Germany. Served as Project Manager on numerous improvement efforts that contributed directly to the bottom line, improved device reliability, increased through put, etc. • Reduced headcount from 11 to seven and order fulfillment interval from 5.5 hours to 20 minutes by redesigning behind the ear (BTE) warehouse layout and picking process. Reconfigured factory floor layout of entire manufacturing area and coordinated movement of all equipment and processes, consolidating operations with negligible interruption of production, reducing floor space by more than 20% and allowing area utilization for other purposes. Increased customer satisfaction by reducing incidence of re-repair of in the ear (ITE) by 15% after analysis of data and repair process methods. Show less
-
-
-
Tyco Telecommunications - Now Known as SubCom -
-
Telecommunications
-
1 - 100 Employee
-
Other Work Experience
-
1994 - 2002
Component Engineer, Supplier Development Team Leader, Supervisor, Coupling Kit Product Line, 1994-2002. Determined and qualified suitable suppliers, providing high reliability mechanical piece parts consistent with 23-year life requirement for products in excess of $30M annually. Served as union-based factory floor supervisor of six direct reports, and analyzed and overhauled coupling kit production area, boosting production efficiency by 1,000%. Component Engineer, Supplier Development Team Leader, Supervisor, Coupling Kit Product Line, 1994-2002. Determined and qualified suitable suppliers, providing high reliability mechanical piece parts consistent with 23-year life requirement for products in excess of $30M annually. Served as union-based factory floor supervisor of six direct reports, and analyzed and overhauled coupling kit production area, boosting production efficiency by 1,000%.
-
-
Education
-
Carnegie Mellon University
Bachelor's degree, Mechanical Engineering/Biomedical Engineer -
Carnegie Mellon University
Master's degree, Mechanical Engineering
Community
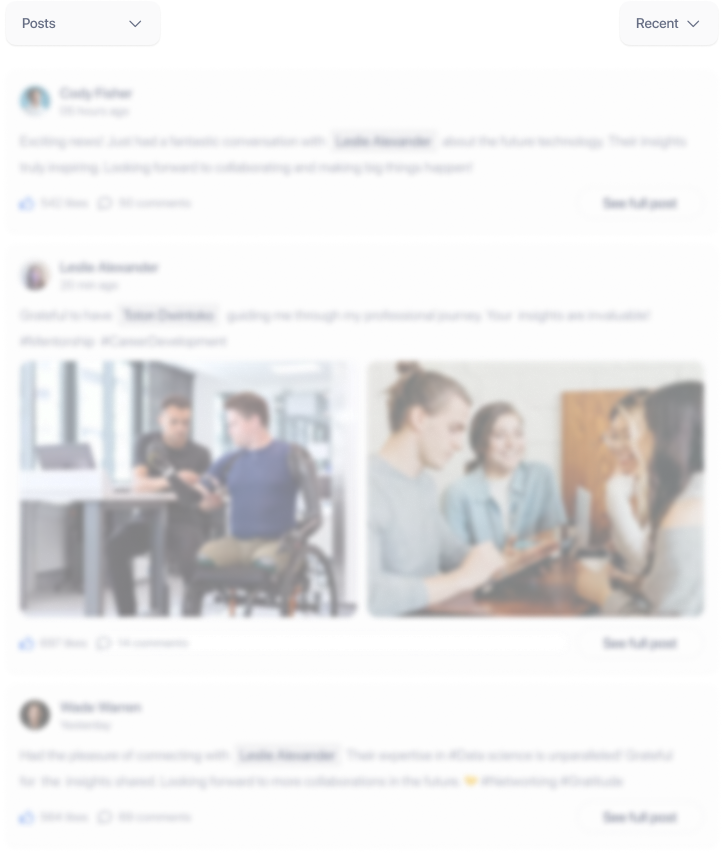