Christopher Cuddy
Sourcing and Supply Chain Specialist at GT Medical Technologies, Inc.- Claim this Profile
Click to upgrade to our gold package
for the full feature experience.
Topline Score
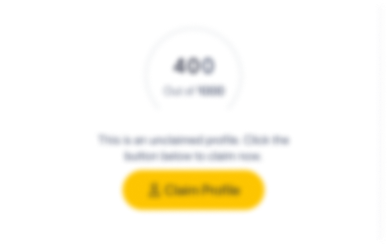
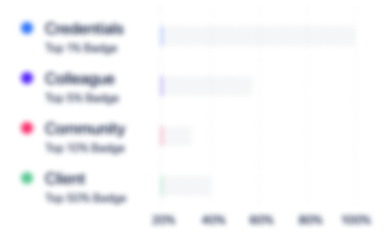
Bio
0
/5.0 / Based on 0 ratingsFilter reviews by:
Credentials
-
Lean Six Sigma Green Belt Certification
GoLeanSixSigma.comJul, 2016- Sep, 2024 -
Notary Public
North Carolina Department of the Secretary of StateOct, 2019- Sep, 2024
Experience
-
GT Medical Technologies, Inc.
-
United States
-
Medical Equipment Manufacturing
-
1 - 100 Employee
-
Sourcing and Supply Chain Specialist
-
Sep 2023 - Present
• Assist in managing the supplier database, ensuring it is accurate and up to date. • Develop working relationships with suppliers and internal customers and train them on proper requisition and PO issuance procedures. This may include leading business reviews with relevant suppliers. • Collaborate with suppliers to produce better savings and further value for spend, as well as identifying and addressing opportunities for lead time improvements. This may include reviewing supplier contracts and assisting negotiations as appropriate. • Identify and deliver cost savings through material assessments • Assist in developing detailed sourcing and category plans to maximize effectiveness and efficiency. • Manage second source projects to have alternate materials qualified and reduce the supply chain risk. This includes working cross functionally with a team to manage resource, time, and cost constraints. • Update quality-controlled component specifications and Standard Operating Procedures as needed. • Work with R&D and technical operations to understand sourcing and supplier relationship needs for upcoming new products. • Own the ERP production order transactions from order issuance through fulfillment, for both manufacturing orders and engineering studies. • Update the shipping transactions for manufacturing orders in the ERP system as the product ships to the sterilizer through Fed-ex, UPS and other freight manifest systems as required. Show less
-
-
-
Norsk Hydro
-
Norway
-
Mining
-
700 & Above Employee
-
Customer Account Manager
-
Jul 2022 - Sep 2023
• Primary point of contact for Tesla. • Responsible for conducting contract review on all incoming customer purchase orders. • Processes customer orders, credits, complaints, returns and other inquiries. • Prepares customer delivery reports by collecting, analyzing and summarizing information to proactively communication potential late deliveries. • Coordinates with quality, engineering and production operations to ensure 100% customer on-time delivery is achieved by establishing and monitoring schedules to proactively identify and address any issues. • Runs daily pulse calls with customer Show less
-
-
-
TE Connectivity
-
Switzerland
-
Appliances, Electrical, and Electronics Manufacturing
-
700 & Above Employee
-
Supply Chain Analyst II
-
Jul 2019 - Jul 2022
•Create and release work orders/production schedules for manufacturing as required to ensure on-time delivery to customers and meet inventory goals•Develop a production schedule that prioritizes manufacturing operations based on customer needs and operational efficiencies. Optimize the use of the MRP system for increased efficiency across multiple levels of the organization•Proactively review material supply and demand to determine push/pull actions appropriate to impact manufacturing MPS and supply MRP exception messages•Coordinates with purchasing, production, engineering, quality, and customer programs to achieve customer required delivery dates•Implemented a digital maintenance system on the Joint Strike Fighter assembly line to promote Total Productive Maintenance (TPM) Show less
-
-
Supply Chain Rotation Associate
-
Jun 2017 - Jun 2019
• Understand the functional areas of procurement, materials planning, commodity management, operations and finance and how they support the global supply chain• Perform internal and external audits and analyses of processes to strengthen the supply chain• Gather quotations, review and complete purchase orders, contact suppliers to place orders and expedite the delivery of purchased items to meet delivery schedules• Obtain quotes from suppliers and assist in negotiating most suitable prices, terms and delivery schedules• Assist in the evaluation of suppliers and participate in plant surveys to evaluate and recommend prospective suppliers• Apply lean principles as it relates to supply chain and operations Show less
-
-
-
PITT OHIO
-
United States
-
Truck Transportation
-
500 - 600 Employee
-
Operations Summer Intern
-
May 2016 - Aug 2016
• Served as a customer liaison, responding to inquiries and troubleshooting for PITT OHIO, a $500 million provider of transportation solutions which offers supply chain, ground, LTL, and truckload services. • Prepared price proposals, special rates, and volume quotes for East Coast and Midwestern customers. • Analyzed rack trailer locations daily and compiled Excel spreadsheets for management review. • Utilized Time Definite and Fast Track industry tools to provide customers with specialty services. • Acquired a working knowledge of the linehaul lanes system and the evening set up of the terminal. • Participated with management in the planning process related to execution of daily operations. • Contributed to Pitt Ohio’s summer internship group “Community Involvement Project” with the goal of enhancing the company’s culture of “giving back.” Show less
-
-
-
-
Order Management Intern, Supply Chain Department
-
May 2015 - Aug 2015
• Evaluated customer needs and managed the customer experience from sales order processing through product delivery, including resolving issues, and addressing special circumstances and requests. • Utilized SAP software to document, maintain, and modify customer purchase orders, and to create deliveries and cancel orders. • Collaborated with various Bayer departments, including planning, marketing, sales, and warehouse to arrange orders and to ensure that they would be shipped according to specifications. • Responded to customer inquiries, including those regarding chemical imports. • Expedited orders, documented returns, and provided solutions for complaints as necessary. • Planned logistics and contacted Menlo Logistics personnel to schedule deliveries, track shipments, and verify their proper execution. • Acted as an intermediary between customers and distribution services. • Communicated delivery information and times to customers. • Disseminated chemical Safety Data Sheets, invoices, pack lists, and Certificate of Analysis Reports which relayed specifications of chemical inquiries and chemical orders. • Assisted experienced Order Management team members with various projects. Show less
-
-
Education
-
University of Dayton
Bachelor of Science in Business Administration, Major: Operations and Supply Management, Minor: Finance
Community
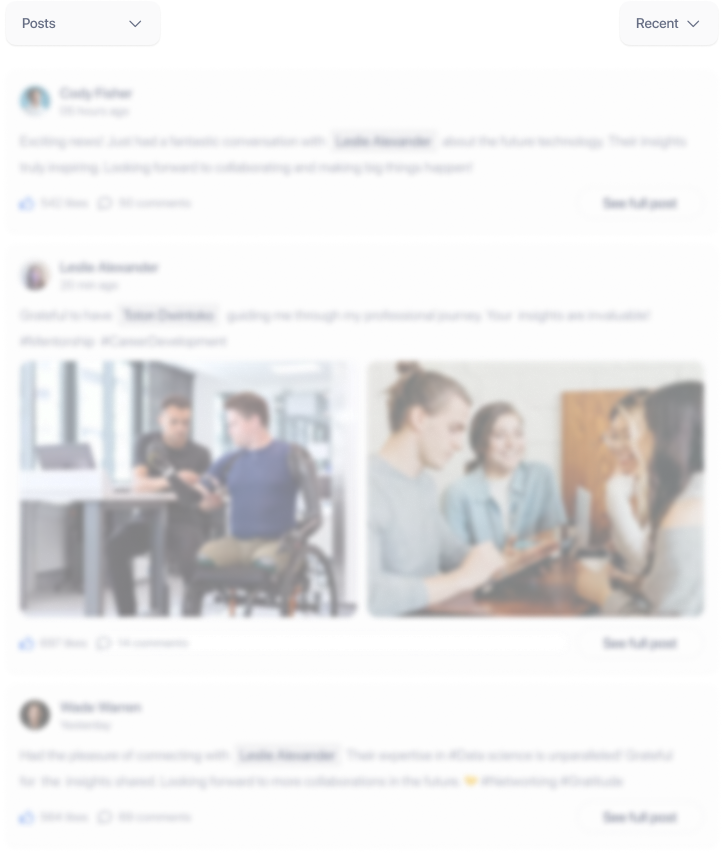