Christine Wyche
CO-FOUNDER OF COLLECTIVE POWER, LLC. at Collective Power- Claim this Profile
Click to upgrade to our gold package
for the full feature experience.
Topline Score
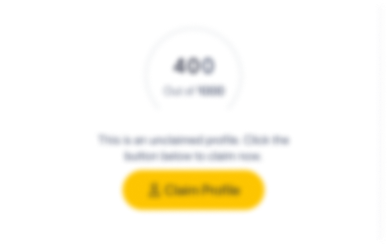
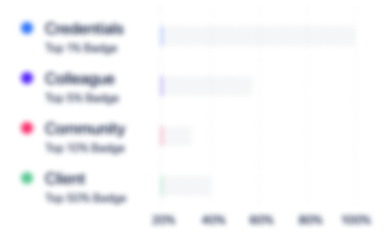
Bio

Amir A. Razelan
I had the honor of working for Christine for over 5 years, a creative leader who motivates people to deliver. A hands-on manager who guides and lets our creativity work.

Mark Warriner
Christine is a truly exceptional and dynamic executive. I was fortunate enough to work for or support Christine for the past twelve years. In addition to possessing an encyclopedic knowledge of quality, she ensures that her employees succeed and that they grow in their knowledge and abilities. Each day working for her was a priviledge and a rewarding experience. I would not enjoy the successes I have had over the past twelve years without her guidance. My recommendation to any organization desiring success: Employ Christine.

Amir A. Razelan
I had the honor of working for Christine for over 5 years, a creative leader who motivates people to deliver. A hands-on manager who guides and lets our creativity work.

Mark Warriner
Christine is a truly exceptional and dynamic executive. I was fortunate enough to work for or support Christine for the past twelve years. In addition to possessing an encyclopedic knowledge of quality, she ensures that her employees succeed and that they grow in their knowledge and abilities. Each day working for her was a priviledge and a rewarding experience. I would not enjoy the successes I have had over the past twelve years without her guidance. My recommendation to any organization desiring success: Employ Christine.

Amir A. Razelan
I had the honor of working for Christine for over 5 years, a creative leader who motivates people to deliver. A hands-on manager who guides and lets our creativity work.

Mark Warriner
Christine is a truly exceptional and dynamic executive. I was fortunate enough to work for or support Christine for the past twelve years. In addition to possessing an encyclopedic knowledge of quality, she ensures that her employees succeed and that they grow in their knowledge and abilities. Each day working for her was a priviledge and a rewarding experience. I would not enjoy the successes I have had over the past twelve years without her guidance. My recommendation to any organization desiring success: Employ Christine.

Amir A. Razelan
I had the honor of working for Christine for over 5 years, a creative leader who motivates people to deliver. A hands-on manager who guides and lets our creativity work.

Mark Warriner
Christine is a truly exceptional and dynamic executive. I was fortunate enough to work for or support Christine for the past twelve years. In addition to possessing an encyclopedic knowledge of quality, she ensures that her employees succeed and that they grow in their knowledge and abilities. Each day working for her was a priviledge and a rewarding experience. I would not enjoy the successes I have had over the past twelve years without her guidance. My recommendation to any organization desiring success: Employ Christine.

Credentials
-
ASQ Certified Quality Engineer; PROSCI certified Change Manager
ASQ
Experience
-
Collective Power
-
Nigeria
-
Electrical Equipment Manufacturing
-
1 - 100 Employee
-
CO-FOUNDER OF COLLECTIVE POWER, LLC.
-
Jun 2021 - Present
-
-
-
Duke Energy Corporation
-
United States
-
Utilities
-
700 & Above Employee
-
GENERAL MANAGER OF TECHNOLOGY PERFORMANCE
-
Jan 2020 - Jun 2021
As a result of an enterprise level reorganization, the Grid Solutions team was eliminated, and I was moved back to my previous role leading the Technology Performance Organization. This team continues to support distribution technologies and now supports the Enterprise Asset Management (EAM) portfolio which included over 75 applications. In 2018, this team which includes a support organization and agile durable team transition to Technology Performance following closure of the Enable project. Customer systems are no longer in scope for this organization. Services are now provided to a full spectrum of users within Distribution, Transmission, Natural Gas Operations, Supply Chain, Finance, Vegetation Management, and the Fleet organization. Beneficiaries span from field performers to the executive staff at the jurisdictional level. Responsible for the efficiency and effectiveness of hundreds of technology applications and interfaces/integrations to other systems. Show less
-
-
GENERAL MANAGER OF ADVANCED SYSTEMS AND COMMUNICATIONS INFRASTRUCTURE
-
Jan 2018 - Jan 2020
Key member of the Grid Solutions organization whose purpose is to execute the Duke Energy Enterprise mission to “Building a Smart Energy Future” by investing 25 Billion over 10 year to modernize Duke’s energy grid, which is the LARGEST in the U.S. with 295K line miles. Responsible for the Advanced Distribution Management System (ADMS) program, second largest technology project within the Customer Experience and Services organization at Duke Energy. Responsibilities include planning and implementing Duke Energy’s investment in grid technology that will enable enhanced operational performance and improved reliability including enhanced restoration results. In addition, these investments will enable future capabilities expected by our customers such as the ability to handling 2-way power flow generated by DER and our ability to operate in the world of big data. The >5-year scope of work includes: program activities and purchases valued at ~$300-500 M, redesigning and streamlining business processes, and building functionality that does not exist today in anticipation of the future needs for the electric grid as well as to achieve step-level changes in workforce efficiency and grid performance. Enterprise communications responsibilities included developing and maintaining the enterprise-wide communications strategy supporting the Duke Energy Road Ahead Initiative, bringing the company into a new era of enhanced technology and operation, with improvements in automation, security and grid control of communication networks. The Enterprise Communications Improvements portfolio enhances technology and communication with increased bandwidth, interoperability and reliability across service areas, jurisdictions and the entire Duke Energy network for now and in the future. Annual investment plans ranged from $300-400 M. Show less
-
-
GENERAL MANAGER OF TECHNOLOGY PERFORMANCE
-
Jan 2016 - Jan 2018
Lead the Technology Performance Organization whose Mission is to: Ensure reliable technology to support Duke Energy’s corporate priorities and strategic initiatives by collaborating with Business, IT and Vendor partners.Services are provided to a full spectrum of users within Distribution, Transmission, Gas Operations. Customer Operations, Customer Solutions, Customer Communications & Channels, Distributed Energy Resources and Grid Solutions. Beneficiaries span from field performers to the executive staff at the jurisdictional level. Responsible for the efficiency and effectiveness of hundreds of technology applications and interfaces/integrations to other systems. Show less
-
-
GENERAL MANAGER OF CUSTOMER SATISFACTION & ENGAGEMENT
-
Nov 2014 - Jan 2016
Responsible for internal and external measurement of Customer Satisfaction using both J.D. Power and an internal proprietary model to measure both customer perception and transactional performance. Accountable for the improvement of Customer experience both traditional and digital. Social Media and Digital channel team provide a new channels for customer engagement. Completed an 8 month extensive customer journey mapping engagement using an outside consultant to define current state and identify customer pain points. Worked with State Presidents to define and execute on both enterprise and local improvement opportunities. Developed and obtained board approval for an enterprise wide customer satisfaction incentive target for 2015.During the first year in this role, our J.D. Power performance results show significant overall improvement for the company, with an increase of 15 points in overall satisfaction from the first quarter of 2015. (The average increase for utilities nationally was a 10-point gain.) Given the reputation issues the company has faced over the past few years, this is significant. Show less
-
-
DIRECTOR OF SUPPORT SERVICES
-
Jul 2012 - Nov 2014
Responsible for the Corporate Travel Program, Event Planning and Event Technical Services, Print Services, Mail Distribution Services and Documentation, Records and Research. As a result of the merger with Progress Energy, major initiatives have included consolidation of the corporate travel programs, office supply and stationary programs and printer optimization across the new organization.
-
-
-
Progress Energy
-
United States
-
Utilities
-
700 & Above Employee
-
Director of Distribution Performance Support
-
Sep 2009 - Jul 2012
Lead and direct the Distribution Performance Support team and provide Technology Support, Project Management expertise and Continue Business Excellence (CBE) direction to the Progress Energy Carolina (PEC) organization. Drive Lean Six Sigma initiatives, Business Planning efforts, Process Development and Governance over site and Technology planning and User support. From 2010-2012: Assigned to Merger Integration team to complete analysis of Duke and Progress business practices with an end product of a business plan or organizational design for the new company. Key Accomplishments: Provided guidance and support for the launch of the PEC CBE 3 year plan which included Rapid Improvement Events, Value Stream Analysis and Enterprise Planning Sessions. Initiated a Process Model Revitalization effort to expand on previous work completed to drive the EDC management team to focus on a bias to Process Centric versus Functional organization operations. Led efforts to improve process alignment and process adherence. Show less
-
-
-
Qimonda, North America
-
Semiconductor Manufacturing
-
1 - 100 Employee
-
Quality Director
-
Apr 2004 - Sep 2009
Lead and direct the North America quality team and provide support to both local and global customers in product qualifications, credits and returns, failure analysis, and problem solving. Attend quarterly business meetings to drive continuous improvement. Hired and trained quality team of 15 for US Sales and Marketing Organization. Spearhead and administer diverse groups and committees including System Working Group, Business Council, and Customer Service Council. Coordinate multiple staff improvements and trainings such as systems / process training for sales team, quality training for design center engineers, FMEA training, as well as training for new employee orientation. Manage customer audits of manufacturing facilities and internal audits of distribution centers and HUBS. Show less
-
-
-
Infineon Technologies
-
Germany
-
Semiconductor Manufacturing
-
700 & Above Employee
-
Director of Quality
-
Mar 1999 - Apr 2004
Oversaw and coordinated RQA department for high volume semiconductor manufacturing facility. Served as TS 16949 management representative and ensured the suitability and effectiveness of site quality systems to maintain certification status. Provided support to timely qualification of new products. Held accountability to all customer audits, returns, complaints, and interfaces. Oversaw and coordinated RQA department for high volume semiconductor manufacturing facility. Served as TS 16949 management representative and ensured the suitability and effectiveness of site quality systems to maintain certification status. Provided support to timely qualification of new products. Held accountability to all customer audits, returns, complaints, and interfaces.
-
-
-
WhiteOak Semiconductor
-
Appliances, Electrical, and Electronics Manufacturing
-
Manufacturing Quality Section Manager
-
Oct 1997 - Mar 1999
Developed and implemented various quality systems leading to successful ISO 9000 certification. Systems developed include: Control of Non-conforming Product, Corrective and Preventive Action and Process Control. Chair of the SPC Council and the Material Review Board (MRB). Supported the various product qualifications with focus on manufacturing readiness. Developed and implemented various quality systems leading to successful ISO 9000 certification. Systems developed include: Control of Non-conforming Product, Corrective and Preventive Action and Process Control. Chair of the SPC Council and the Material Review Board (MRB). Supported the various product qualifications with focus on manufacturing readiness.
-
-
-
White Oak Semiconductor
-
Appliances, Electrical, and Electronics Manufacturing
-
Quality Systems Support Section Manager
-
Apr 1997 - Oct 1997
Developed and implemented a Documentation System, Change Control Process and various manufacturing systems for start-up of the DRAM manufacturing facility. Lead facility to successful completion of corporate goal to develop 325 operating, recipe and incoming material specification. Developed and implemented a Documentation System, Change Control Process and various manufacturing systems for start-up of the DRAM manufacturing facility. Lead facility to successful completion of corporate goal to develop 325 operating, recipe and incoming material specification.
-
-
-
International Paper
-
United States
-
Paper and Forest Product Manufacturing
-
700 & Above Employee
-
Operations Control Manager
-
Aug 1994 - Apr 1997
Managed the Customer Service, Quality Control and Production Scheduling functions for this Rotogravure folding carton facility. Developed customer partnerships that resulted in doubling volume of business and expanding production capabilities. Facilitated the development of Quality Systems and Process Improvement initiatives resulting in 40% reduction in complaints/rejections. Reduced facility working capital cost by implementation of effective inventory control systems. Managed the Customer Service, Quality Control and Production Scheduling functions for this Rotogravure folding carton facility. Developed customer partnerships that resulted in doubling volume of business and expanding production capabilities. Facilitated the development of Quality Systems and Process Improvement initiatives resulting in 40% reduction in complaints/rejections. Reduced facility working capital cost by implementation of effective inventory control systems.
-
-
-
-
Quality Assurance Engineering Manager
-
Mar 1991 - Aug 1994
QA measurement and testing of high pressure decorative laminate. Product development responsibility working with designers and specification reps. Product Improvement initiatives to improve yields and optimize production output.
-
-
Research Engineer
-
Aug 1988 - Mar 1991
-
-
-
-
Statistical Process Control Coordinator/Process Engineer
-
Jun 1982 - Aug 1988
-
-
Education
-
University of Delaware
BChE, Chemical Engineering
Community
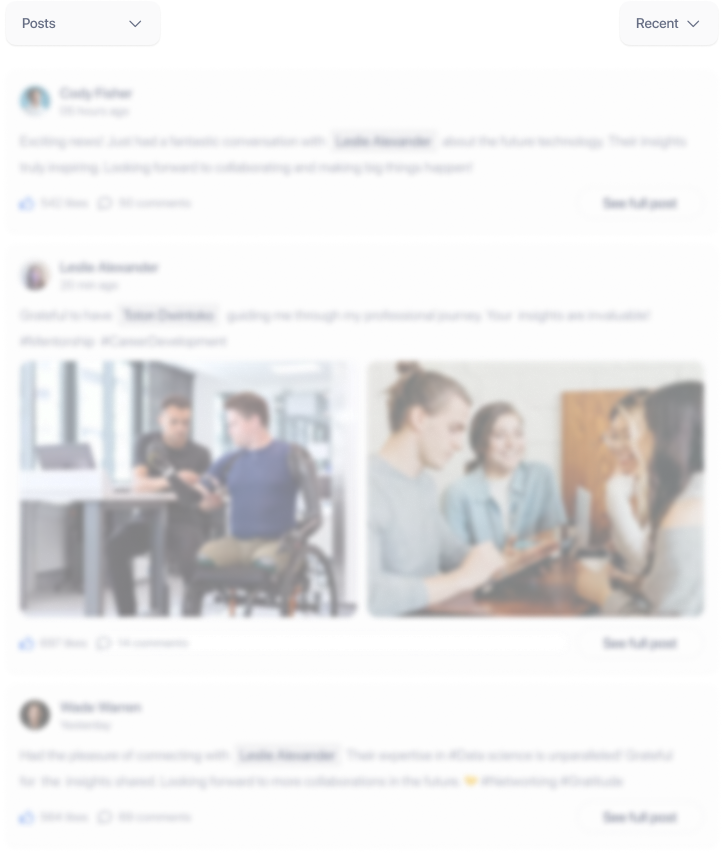