Christine (Novack) Durecka
Materials Manager at TREMEC- Claim this Profile
Click to upgrade to our gold package
for the full feature experience.
Topline Score
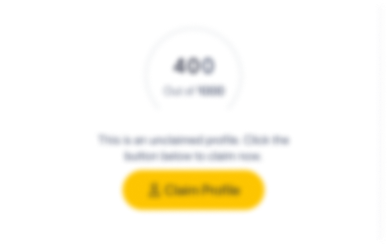
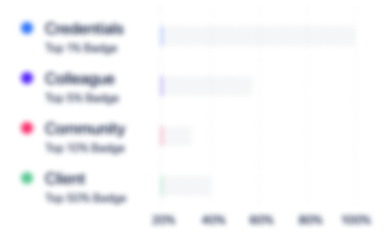
Bio


Experience
-
TREMEC
-
Motor Vehicle Manufacturing
-
500 - 600 Employee
-
Materials Manager
-
Oct 2018 - Present
-
-
-
General Motors
-
United States
-
Motor Vehicle Manufacturing
-
700 & Above Employee
-
Global Lean Manager (GMS) - Engineering Operations and Processes
-
May 2016 - Oct 2018
• Responsible for leading/coaching Lean Principles (GMS) for global lab operations, pre-production operations, and proving grounds locations in 4 regions.• Responsible for developing/aligning business plans for Global Director and Regional Directors• Responsible for developing/implementing standard lean processes with respect to People Involvement, Standardization, Quality, Responsiveness, and Cost.
-
-
GRx Transmission Materials Launch Lead
-
Apr 2014 - May 2016
• Responsible for leading/coaching the GSC team in an efficient launch of the GRx Transmission.• Responsible for maintaining the plant’s part budget.• Responsible for all GSC office activities, including procuring MRO parts, PFEP, and supplier readiness.• Assist in production activities including simulations, buffers, FIFO, layouts, and GMS processes.
-
-
HFV6 Launch Team, GSC – Office
-
Aug 2013 - Apr 2014
• Responsible for part readiness process resulting in an efficient launch of the HFV6 Engine.• Analyzed suppliers’ readiness and develop a process for high risk suppliers to Romulus Engine.• Assisted in part follow-up and transportation.• Assisted in the implementation of GSC floor launch activities including layout, buffers, manpower, and all GMS processes.
-
-
GSC Floor Manager
-
Jan 2012 - Aug 2013
• Improved IPPM below 20,000 (98% FTQ) on the V8 Assembly line by initiating a dunnage debris elimination project resulting in a regular dunnage cleaning process at vendor locations.• Implemented a repack team eliminating the need to outsource repack operations saving over $200,000 per year.• Improved efficiency of dock teams by 50% by designing 2 man teams, improving driver staging/storing time saving over $200,000 per year.• Improved sending parts back to suppliers by weighing empty dunnage for high loss parts and engaging team members to implement visual empty dunnage initiatives at waterpumps and belt tensioners.• Increased GSC involvement and accountability for blocked/started robots at V8 Block Line OEE meeting resulting in a 5% improvement on constraints through team involvement.• Maintained a departmental GMS score of 98% by implementing weekly departmental GMS reviews, BPD board reviews, department GMS basketweave process, and problem solving workshops while focusing teams on standardized work and JIT.• Led a seamless and smooth transition regarding storage and inbound transportation for V8 Assembly and Machining as a result of an increase in production from 1600/day to 2100/day. All shipments and build to plans have held at 100%. Show less
-
-
Lean Manufacturing Coordinator
-
Oct 2007 - Jan 2012
• Support, advise, and assist Area Managers and their personnel in the implementation of QN/GMS/Lean Manufacturing initiatives. Improved GMS Calibration score by 33%.• Led in the development and implementation of the following processes for production, materials and maintenance: problem solving, standardized work development and improvement, job instruction training, work place organization, raise the bar layered audit, and weekly focus walks to enhance people recognition.• Implemented and support the GMS wall process to teach and coach lean manufacturing concepts daily on a plant wide basis.• Encourage, lead and support continuous improvement initiatives on sufficient GMS processes to drive better business results in the future.• Subject Matter Expert for team concept and GMS during the 2011 local negotiation process. Show less
-
-
-
-
Industrial Engineering Supervisor
-
Sep 2006 - Oct 2007
• Developed, analyzed, and presented project information to improve hours per unit from 3.75 to 3.42. • Coordinated the implementation of consumption based scheduling on the floor resulting in a reduction in buffer sizes while maintaining current schedules. Supporting an overall reduction of $6 million in inventory. • Coordinated and coached the implementation of the Overall Equipment Effectiveness process (OEE) improving throughput by an average of 5% in 3 machining departments. • Assisted in establishing operational methods and work standards to improve quality of work and the quality of the product. First Time Quality improved from 81% to 89%. • Analyzed existing operations, developed cost-justified rebalance opportunities, and implemented floor challenges that reduced manpower by 12%. Show less
-
-
-
-
Senior Throughput Analyst
-
Jun 2004 - Sep 2006
• Performed and coordinated throughput simulation projects to support current plant operations and future Powertrain programs. Achieved an average result of 10-15% throughput improvement from baseline. • Team Leader responsible for elevating layout and throughput issues in manufacturing operations. • Utilized value steam mapping as a tool to visualize throughput improvement opportunities in a team based atmosphere. • Responsible for providing technical support to other team members performing throughput analysis and simulation projects. • Communicated results of analyses and lessons learned to plant and divisional leadership. Show less
-
-
-
General Motors
-
United States
-
Motor Vehicle Manufacturing
-
700 & Above Employee
-
Manufacturing Shift Leader
-
Oct 2001 - Jun 2004
• Achieved shift metrics while derating product line to support new business.• Developed flexible crews to improve productivity approximately12%.• Independently managed a third shift operation with over 400 team members.• Supported/trained/coached group leaders to become shift leaders, including how to administer the discipline/grievance procedures.
-
-
Senior Quality Analyst
-
Apr 2001 - Oct 2001
• Led product team to maintain and improve quality metrics by analyzing and implementing process improvements to reduce various product defects. • Consistently maintained standard processes as a liaison between outsource finishing company and final product customers. • Developed, maintained, and improved QS 9000 documents.• Analyzed complex manufacturing process and solved quality issues..
-
-
Manufacturing Group Leader
-
Jul 1999 - Apr 2001
• Responsible for daily operation of core room processes. • Focused on manpower utilization, process improvements, uptime, product diversity and production scheduling while meeting and exceeding product line metrics related to safety, people, quality, responsiveness, and cost.
-
-
Industrial Engineer
-
Nov 1997 - Jul 1999
• Responsible for jointly managing the Saginaw Metal Castings Operations industrial ergonomics program with a United Auto Worker partner resulting in no cases open for > 30 days.• Analyzed work processes to eliminate/reduce cumulative trauma risk factors.• Developed and maintained an injury tracking system plant wide.• Assisted with work hardening and new hire orientation program.• Designed new job processes, and conducted/developed training programs.
-
-
-
-
Specialist
-
Jun 1992 - Nov 1997
• Managed the State Farm office ergonomic program for over 70,000 employees at 1,100 facilities. • Analyzed and redesigned work processes to reduce stress and improve productivity. • Conducted and developed applicable safety and health training for maintenance employees and stock operators. • Maintained a high level of knowledge related to current ergonomic research while participating on a research committee consisting of large companies and top universities. • Assisted in the modernization and implementation of 3 new warehouse operations which improved team member response time by an average of 20% and order accuracy improved from 80% to 98%. Show less
-
-
Education
-
University of Michigan-Flint
Master, Business Administration -
Western Michigan University
B.S, Industrial Engineering
Community
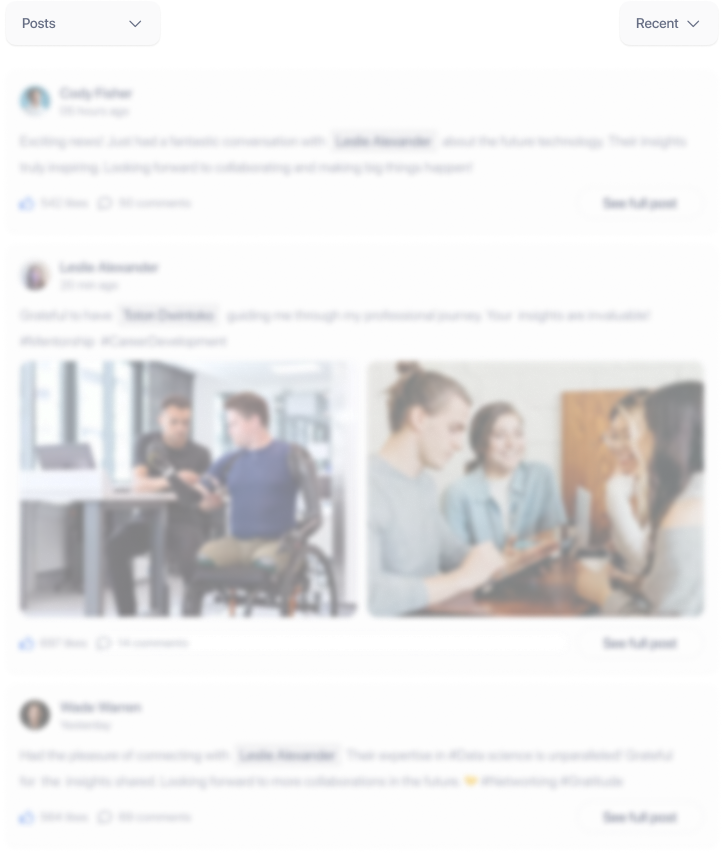