Christine Dulay Bradley
Senior Quality Assurance Engineer at Insulectro Printed Electronics- Claim this Profile
Click to upgrade to our gold package
for the full feature experience.
Topline Score
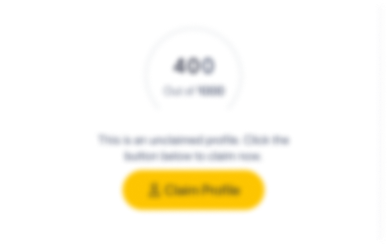
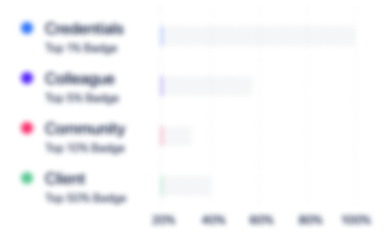
Bio
0
/5.0 / Based on 0 ratingsFilter reviews by:
Credentials
-
Certified Quality Management System Lead Auditor
IRCA | International Register of Certificated Auditors
Experience
-
Insulectro Printed Electronics
-
United States
-
Appliances, Electrical, and Electronics Manufacturing
-
1 - 100 Employee
-
Senior Quality Assurance Engineer
-
Oct 2022 - Present
Manage Customer Complaints and Vendor Claims (Root Cause Investigation/Corrective Actions/8D/Credit Processing/Material Disposition); Maintain QMS (Audits/ Management Reviews/ Document Reviews), Customer feedback and inquiries Manage Customer Complaints and Vendor Claims (Root Cause Investigation/Corrective Actions/8D/Credit Processing/Material Disposition); Maintain QMS (Audits/ Management Reviews/ Document Reviews), Customer feedback and inquiries
-
-
-
Thales
-
United States
-
Financial Services
-
1 - 100 Employee
-
Quality Assurance Specialist
-
May 2022 - Oct 2022
Acts as Agent for Boeing, issuing FAA form 8130-9 Statement of Conformities; Reviews Conformity Inspection packages from Suppliers; Reviews Engineering drawings and Test Plans; Conform Test Setups in Third Party Laboratories Acts as Agent for Boeing, issuing FAA form 8130-9 Statement of Conformities; Reviews Conformity Inspection packages from Suppliers; Reviews Engineering drawings and Test Plans; Conform Test Setups in Third Party Laboratories
-
-
-
Solvay
-
Belgium
-
Chemical Manufacturing
-
700 & Above Employee
-
QA Executive
-
May 2018 - Jan 2020
Manage company's QMS (FSSC 22000, ISO 9001, RSPO) and Product certifications under Kosher and Halal; Handle Customer Complaints and investigations; Conduct Supplier Qualification and audits; Train new hires; Manage and review documentation; Internal Auditor Manage company's QMS (FSSC 22000, ISO 9001, RSPO) and Product certifications under Kosher and Halal; Handle Customer Complaints and investigations; Conduct Supplier Qualification and audits; Train new hires; Manage and review documentation; Internal Auditor
-
-
-
Setsco Services Pte Ltd
-
Singapore
-
Industrial Machinery Manufacturing
-
300 - 400 Employee
-
QA Executive
-
Jul 2011 - Dec 2016
ITA/Third Party Inspections Project Management ( Structural Steelworks, Tank and Piping Inspection); Maintenance and Continuous Improvement of QMS (ISO 17020/17025/17065/9001) Implementation; Product Certification (ISO 17065) Administration; Manage project coordination for Inspection/Testing activities, Prepare and review Inspection and Test Plans, Review inspection reports Manage overall operations of SETSCO Certification Body-Product Certification Scheme under ISO 17065 Maintain and Review QA/QC Documents: Quality Manual, Standard Operating Procedures, Quality Plans, Inspection and Test Plans Advise solutions for Customer Complaints/Feedback and other Non-Conformities by assisting in Corrective Actions formulation; Lead preparation for New Testing and Calibration Laboratories and Inspection Body Accreditations Prepare Management Review Report, establish Divisional KPIs and formulate Annual Improvement Plans Administer Qualification of New Vendors and Subcontractors; Lead Annual Vendors and Subcontractors Evaluation Organize and Conduct Internal Quality Audits/Technical Audits (ISO 17025, ISO 17020, ISO 9001, ISO 29990) Conduct 3rd Party Audits (ISO 9001/17025/17020) to SETSCO Consultancy Pte Ltd clients including Shell, Exxon Mobil, Petrochemical Corp. of Singapore (PCS) , Singapore Turf Club , SETSCO Training Centre, SWS Training Centre Organize/Coordinate 3rd Party Quality Audits for Singapore Accreditation Council (ISO 17025, ISO 17020, ISO 17065) Conduct Quality Training (ISO 17025, ISO 17020, ISO 17065, Document Control) Show less
-
-
-
Victoria Court Hotels
-
Australia
-
Hospitality
-
Systems Improvement Officer
-
Feb 2010 - Jun 2011
Maintained a Quality and Service-Oriented Organization through continuous monitoring, evaluation and improvement of Check-In, Guiding-Out Standard Operating Procedures and Policies Prepared Management Review Report and formulate Annual Improvement Plans and KPIs Managed Internal Quality Audits (ISO 9001) and Room Inspection on Hotel Branches Lead investigation and resolution of Guest Feedback and Complaints Lead Customer Service Improvements based on Customer Feedback and Complaints Show less
-
-
-
Procter & Gamble
-
United States
-
Manufacturing
-
700 & Above Employee
-
Supply Chain Engineer
-
Sep 2005 - Jan 2010
Manufacturing - Quality Assurance, Quality Control,Machine Operation and Maintenance,Process Improvement,Subcontractor management,Product releasing Operated and Maintained Hi-Speed Machine (Diaper Converting Line, Automated Diaper Packaging Machine), Mixers, Transfer pumps, and Storage Tanks Lead various Work Process Improvement Projects (Changeover Wastage Recovery and Rework System, Batch Cycle Time Reduction) Maintained over-all working condition inside production line (quality, safety, GMP). Established methodologies and strategies in optimization of Machine operations and Maintenance Performed Testing on Finished Products prior to Releasing Conducted Quality Training for Technical Officers from other P&G Plants on Manufacturing Process & Quality Standards Resolved process-related Customer complaints and provide necessary feedback to R&D for product development Show less
-
-
-
Integrated Microelectronics Inc.
-
United States
-
Electrical/Electronic Manufacturing
-
1 - 100 Employee
-
QA Supervisor-Continuous Improvement Program Leader
-
Sep 2004 - Sep 2005
Quality Assurance-ISO 9001,14001, Business Unit Lead Auditor, Training Supervisor, Quality Circle and Six Sigma Project coordinator, Supplier Audits, 5S Champion Supervised and Trained QA and Training Staff (Training includes: Document Control, ISO 9001:2000, ISO 14001:2004 ) Prepared Section Objectives and Activity Plans and Direct Section in the attainment of Annual section objectives Reviewed QMS Procedures to sustain continuous improvement of the System Implemented Corporate-initiated EMS and Health and Safety Programs Supervised QMS and Manufacturing Line Audits Conducted 2nd Party Audits to Sub-contractors and Suppliers Managed CA/PA Reports on Non-Conformances Optimized Manpower scheduling of QA and Training Staff Facilitated Quality Circle and Six Sigma Groups Managed TQM Projects including Awards and Recognition Programs and Suggestion Program Conducted Training Needs Analysis for Manufacturing Supervisors and Technicians Show less
-
-
-
-
QA/QC Engineer, DCC Engineer
-
Mar 2002 - Sep 2003
Incoming, In-Process, and Outgoing Quality Control; QMS- DCC Engineer ISO 9001; Supplier Quality Management Supervised Manpower Scheduling of QA Staff and QC Inspectors Conducted Trainings to operators.(e.g.,5S, Basic ESD Principles, Quality Management System, Introduction to ISO 9001:2000 , Product Orientation and General Quality Management Practices) Managed Quality-related issues with Suppliers, Subcontractors, Customers, and Manufacturing Engineers Performed Subcontractor quality performance by periodical visits/audits and assisted them with resolution of quality issues Conducted Training Needs Analysis for Production Line Operators and QC Inspectors Reviewed Customer Documents on Product and Process Specification for New Models Facilitated Qualification of First Article Production and Inspection Verified Manufacturing Changes according to ECN/PCN Managed CA/PA, In-Charge of data handling for Customer Service (Yield Report, FA Report, Customer Complaints, Critical Parameters SPC Report) Managed Work Instructions, Standard Operating Procedures, Quality Plans, ECN/PCN Show less
-
-
-
ENGTEK PRECISION PHILIPPINES, INC.
-
Philippines
-
Appliances, Electrical, and Electronics Manufacturing
-
1 - 100 Employee
-
Failure Analysis Technician
-
May 2000 - Nov 2001
Planning and Implementation of Process Evaluations on Failure Analysis, Process and Quality Improvement on Plating Line and Sub-Assembly Line Handled Testing Equipment such as Liquid Particle Counter and Ion Chromatogram In-Charge of data handling for Customer Service (Yield Report, FA Report, Customer Complaints, Critical Parameters SPC Report) Prepared Work Instructions and Standard Operating Procedures. Managed CA/PA Reports Prepared Engineering and Evaluation Reports Planning and Implementation of Process Evaluations on Failure Analysis, Process and Quality Improvement on Plating Line and Sub-Assembly Line Handled Testing Equipment such as Liquid Particle Counter and Ion Chromatogram In-Charge of data handling for Customer Service (Yield Report, FA Report, Customer Complaints, Critical Parameters SPC Report) Prepared Work Instructions and Standard Operating Procedures. Managed CA/PA Reports Prepared Engineering and Evaluation Reports
-
-
Education
-
University of Santo Tomas
Bachelor of Engineering (B.Eng.), Chemical Engineering
Community
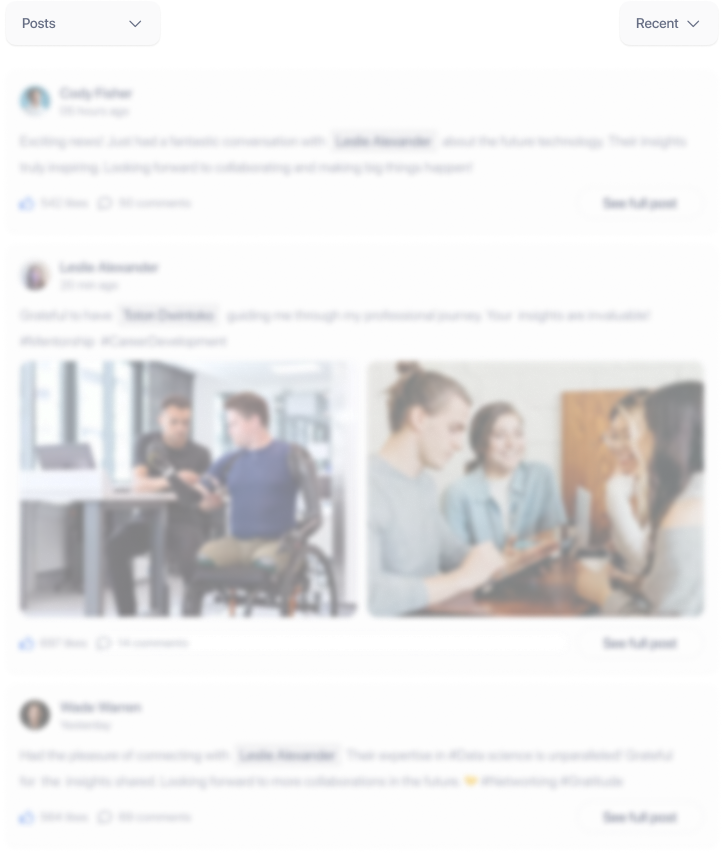