Christine Baldwin
Senior Procurement Analyst at Winland Foods- Claim this Profile
Click to upgrade to our gold package
for the full feature experience.
-
English Full professional proficiency
-
German Native or bilingual proficiency
-
Spanish Limited working proficiency
Topline Score
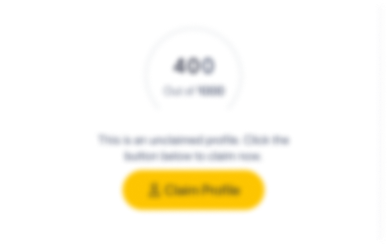
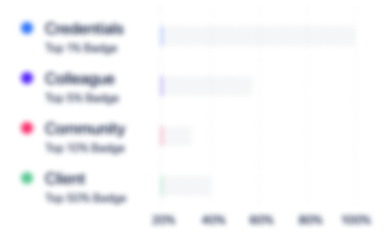
Bio


Credentials
-
Lean Six Sigma Green Belt
University of Southern CaliforniaJun, 2023- Nov, 2024 -
Foundations of Distribution and Logistics
Association for Supply Chain ManagementFeb, 2023- Nov, 2024 -
ECDL/ ICDL certification
ECDL / ICDL CertificationJan, 2014- Nov, 2024 -
Crucial Accountability
VitalSmarts -
Crucial Conversations
VitalSmarts -
Feedback that Works
Center for Creative Leadership
Experience
-
Winland Foods
-
United States
-
Food and Beverage Manufacturing
-
200 - 300 Employee
-
Senior Procurement Analyst
-
Aug 2023 - Present
-
-
-
Ferrara
-
United States
-
Manufacturing
-
700 & Above Employee
-
International Logistics Compliance Analyst
-
Jun 2021 - Apr 2023
Coordinate 2000+ international shipments annually, negotiate rates with carriers, and manage documentation. Ensure audit compliance with FMC regulations and corporate policies. Oversee import process, including preparation of documents to US, MX, CA, EU, Asia, BZ, and other Customs agencies. Communicate with customer service department, carriers, vendors, and regulatory to support international distribution. Review supplier/vendor performance and address issues with carriers. Maximized efficiency, minimized international shipment costs, and achieved compliance with customs regulations by providing expert recommendations on methods and strategies. Cut past due invoices by $150K by implementing financial audits and creating billing process SOPs. Coordinated logistics operations through managing large volume of over 2000 shipments per year and handling billing and invoicing. Ensured exceptional quality of service by single-handedly overseeing end-to-end management of 10 vendors, from interview and review processes to monitoring performance, negotiating rates and resolving billing issues. Transformed operations process by creating Standard Operating Procedures (SOPs), sharing file locations to track KPIs, and streamlining workflows. Increased visibility and captured cost savings by creating Microsoft Excel tracker that allowed multiple departments to see status of shipments. Contributed to successful launch of two new products by developing shipping process that included finding carriers, developing processes, and writing SOPs. Show less
-
-
-
Schweitzer Engineering Laboratories (SEL)
-
United States
-
Electric Power Transmission, Control, and Distribution
-
700 & Above Employee
-
Production Lead: Admin and Production Planner
-
Jun 2019 - Mar 2021
Oversaw production planning process to drive smooth and efficient operations. Ensured production schedules were created and adhered to, while meeting production targets within specified time frames. Achieved compliance with safety and quality standards. Collaborated closely with production teams. Drove 18% lead time reduction and 20% increase in capacity through creating Microsoft Excel file that led to massive cost savings and additional capacity. Successfully purchased over 2,000 unique items for startup of new manufacturing facility and arranged arrival and distribution of items within 6-week time period Improved sourcing capabilities by building relationships with 20+ vendors and ordering $5K in equipment and supplies through indirect material buyers each week. Boosted efficiency in product flow, reduced feedback loops, and increased space utilization through collaborating with leaders on floor layout changes. Achieved 99% parts availability by working with inventory management to set up 2 bin Kanban system. Forged alignment across all sites by collaborating with factory managers of 3 manufacturing facilities on process improvements for panning, shipping, and receiving. Led onboarding of new hires, served as part of interview/hiring team for new assemblers, and coordinated/trained 15-20 professionals in one manufacturing department. Show less
-
-
Senior Assembler
-
Jan 2017 - Aug 2019
o Coordinating and training a manufacturing department. Creating daily schedules as well as planning work loads, setting daily goals and providing continuous training. o Support manufacturing floor layout changes from departments to world class manufacturing flow lines. o Implementing process improvements for manufacturing processes in alignment with World Class manufacturing (Lean manufacturing, Six Sigma, and Kaizen) as well as updating appropriate documentation.o Facilitating tours for new employees and visitors through the different manufacturing departments explaining processes and different product types.o Reorganizing department floor layout to improve production flow and reduce bottle necks in production. Show less
-
-
-
DMG MORI
-
Germany
-
Machinery Manufacturing
-
700 & Above Employee
-
Customer Service Help Desk
-
Apr 2015 - Jul 2015
-
-
-
DMG MORI
-
Germany
-
Machinery Manufacturing
-
700 & Above Employee
-
Business Development Assistant
-
Aug 2014 - Oct 2014
-
-
Education
-
University of Southern California
Master of Science - MS, Global Supply Chain Management -
Washington State University - Carson College of Business
Bachelor's degree, International Business -
Lewis-Clark State College
Associate's degree, Business Administration with Accounting emphasis -
Ludwig-Maximilians-Universität München
Bachelor's degree, Physics
Community
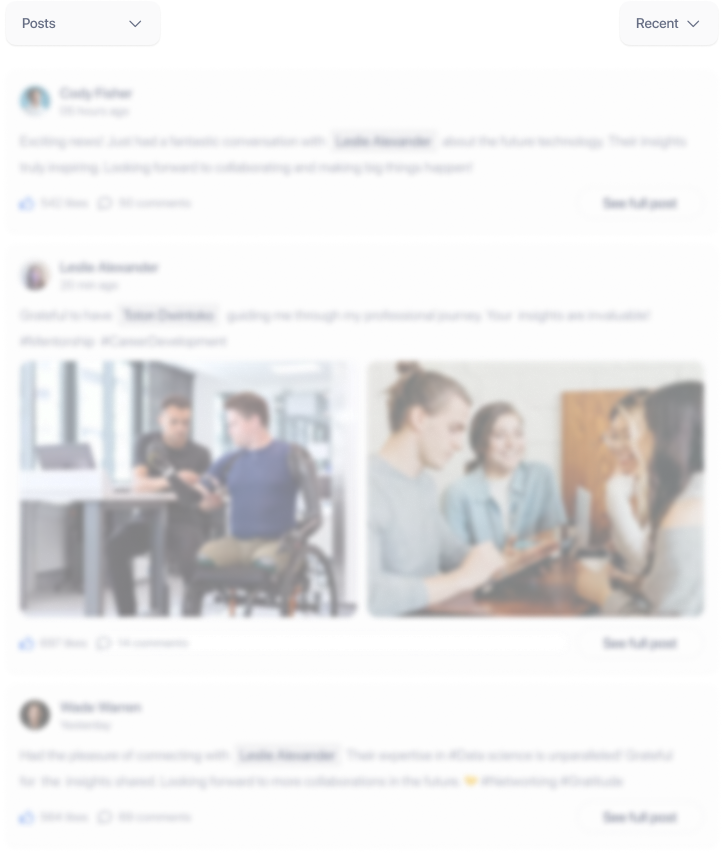