Christina Perez
Director of Quality and Operations at ANACAPA Micro Products, Inc.- Claim this Profile
Click to upgrade to our gold package
for the full feature experience.
-
Spanish Full professional proficiency
-
English Native or bilingual proficiency
Topline Score
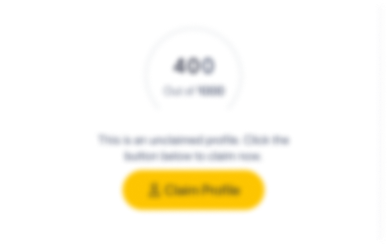
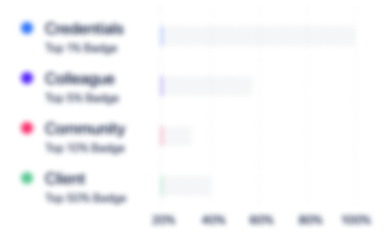
Bio


Credentials
-
AS9100 Certified Lead Auditor
ASQ - World HeadquartersJul, 2021- Oct, 2024 -
IPC/WHMA-A-620 Requirements & Acceptance for Cable & Wire Harness Assemblies certified trainer
IPCJun, 2020- Oct, 2024
Experience
-
ANACAPA Micro Products, Inc.
-
United States
-
Software Development
-
1 - 100 Employee
-
Director of Quality and Operations
-
Oct 2022 - Present
-
-
-
AERO QMS
-
Ventura, CA
-
ISO 9001, AS9120, and AS9100 Consultant
-
Aug 2014 - Oct 2022
Helping business create and manage Quality Management Systems to Aerospace, Military, and Defense standards Helping business create and manage Quality Management Systems to Aerospace, Military, and Defense standards
-
-
-
Communications & Power Industries (CPI)
-
United States
-
Appliances, Electrical, and Electronics Manufacturing
-
700 & Above Employee
-
Quality Engineer
-
Mar 2020 - Jun 2021
-
-
-
ANACAPA Micro Products, Inc.
-
United States
-
Software Development
-
1 - 100 Employee
-
Quality Manager
-
Mar 2015 - Mar 2020
• Lead operations in all quality objectives • Apply risk mitigation strategies throughout sales, purchasing, and operations • Ensure Government contract compliance for SEWP, CIO-CS, First Source II • Continuously monitor and measure operational performance and customer satisfaction • Initiate and implement actions where desired results are not achieved • Conduct contract review to align operations with contractual requirements • Create marketing material for the QMS to utilize in contracts, bids, and proposals • Conduct internal audits • Lead third party audits (Boeing, Raytheon, Lockheed Martin, L-3, General Dynamics, as well as our ISO 9001/AS9120/AS9100 registrar • Create methods for standard operations for departments outside of Quality (Marketing, Accounting, and Business Development) • Lead and conduct follow-up audits for corrective action plans and/or findings • Manage non-conforming product processes • Oversee QC inspectors and lead the Logistics team • Conduct daily spot checks of quotes, sales orders, purchase order, and customer drawings to validate accuracy and initiate additional training where needed • Interpret customer drawings for procurement,/ manufacturing integration planning • Align and support operational changes to support sales growth • Create and manage document control system to support organizations key processes, contractual requirements, and customer requirements. • Manage secure supply chain and counterfeit risk mitigation strategies • Lead source inspections for the Federal System Integrators • Utilize CRM Database (Netsuite) to generate reporting systems that provide transparency to Executive Management on the organizational performance by department and / or individual performance Show less
-
-
Operations and Partner Alliance Manager
-
2013 - Mar 2020
-
-
-
-
Quality Assurance Manager
-
Jun 2013 - Oct 2014
• Quality Management Representative • Managed the organizations AS9100/ ISO 9001 Quality Management System • Responsible for AS, ISO, Safety, DPAS, FOD Training • Internal /External Audits • Monthly/ Quarterly Performance Metrics of key processes and customer satisfaction • Conduct and manage non-conforming product reporting • Blueprint Reading, interpretation for contract review and inspection of final product • GD&T: Utilize calipers, micrometers and test reports against blueprints to conduct First Article Inspections (AS9102) • Oversee Boeing DPD/ MBD Audits • Maintaining Boeing MBD/DPD Internal QMS • Inspection Tool Calibration • Conduct Management Reviews • Managed purchasing and control of product transferred for of outside processes (anodize, paint, heat treat) • Managed inventory control and product trace-ability • Evaluate customer/ vendor RFQ’s • Receiving/ logging/ verifying certification of Military Standard Processes Show less
-
-
-
Workrite Uniform Company
-
Oxnard,CA
-
Quality Assurance Administrative Assistant
-
Nov 2007 - Jun 2013
• Creating and maintaining reports and logs for all nonconformances reported within the company • When nonconformities are reported, I am responsible for enforcing policies and processes in order to correct the issue • Maintain records of revisions for ISO 9001 documentation. • Create work instructions, processes, and forms; registering documentation for ISO 9001 and obtaining necessary approvals. • Assisting in ISO audits (Certified Internal Auditor) • Creating samples and maintaining documentation for UL certified garments for Oxnard, and all 5 contractors in Mexico. • Inspecting raw material, garments, and trims for nonconformities. • Evaluating weekly color swatches from our suppliers to determine color shade match and fabric weight. Responsible for approving or rejecting rolls based on swatches. • Conduct testing and obtaining reports for new fabric evaluations. • Reporting monthly Metrics to Director of OPS • Taking all minutes for Quality Alliance Meetings, typing and distributing. • Maintaining reports for all incoming defective rolls of raw material • Creating and maintaining supervisor’s monthly expense reports and submitting to finance. • Re-certifying UL Certified garments annually. • Conducting internal UL testing. • Conducting weekly conference calls with contractors in Mexico to review any quality issues. • Controlled quarantine inventory levels and responsible for reducing this inventory by 60% annually. Show less
-
-
-
Anthem, Inc.
-
United States
-
Hospitals and Health Care
-
700 & Above Employee
-
Benificiary Inquiry Representative
-
Aug 2001 - Mar 2003
Worked in a large call center for Medicare to explain benefit information to beneficiaries. Used ICD-9 coding to evaluate workmans compensation claims and billing. Worked in a large call center for Medicare to explain benefit information to beneficiaries. Used ICD-9 coding to evaluate workmans compensation claims and billing.
-
-
Community
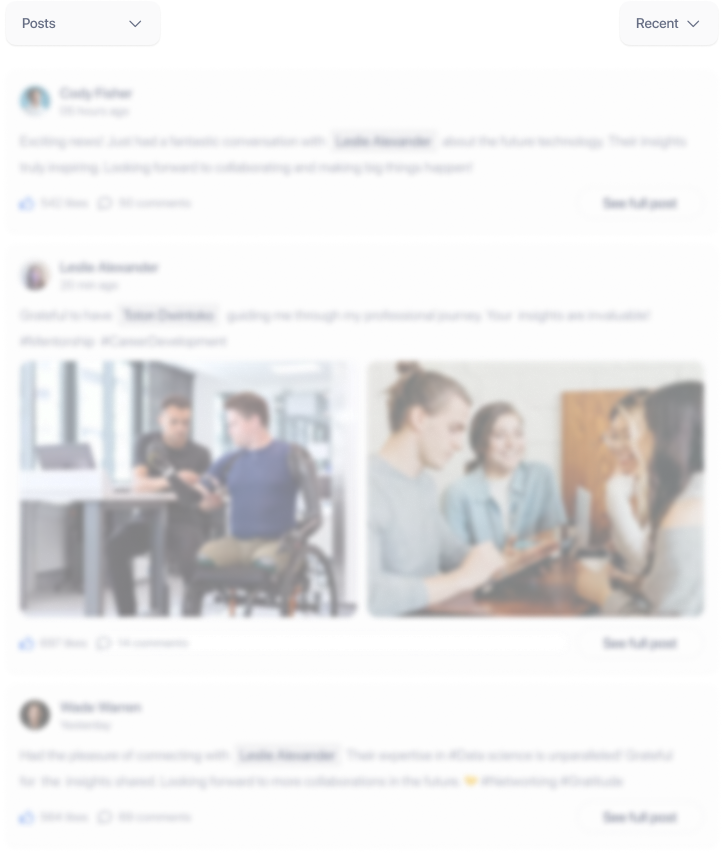