Christian O'Mara
Project Manager at WJ Groundwater Canada- Claim this Profile
Click to upgrade to our gold package
for the full feature experience.
Topline Score
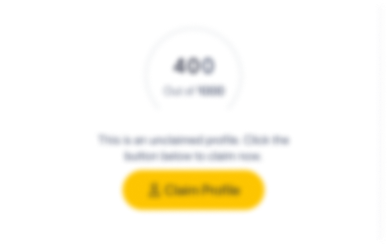
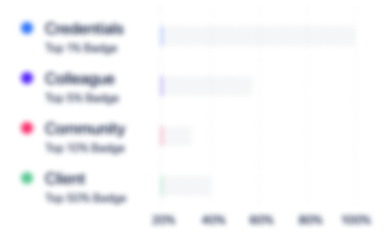
Bio


Experience
-
WJ Groundwater Canada
-
Canada
-
Construction
-
1 - 100 Employee
-
Project Manager
-
Oct 2022 - Present
Provide overseeing of up to seven dewatering projects for the construction of high-rise buildings tunneling, ground remediation with budgets between $220,000 – $800,000. I’m responsible for organizing all operations activities during the project life cycle. Responsible for documenting and communicating all matters pertaining to technical and commercial activities. Acts as the main point of contact with the client. Provide and assist on the resolution of issues pertaining to change of ground or site conditions, change or incorporation of new scope or system performance. Review project drawings (Civil, Architectural, servicing, shoring) for dewatering system deployment to suit specific project requirements (Wellpoints, Eductors, deep well systems) Responsible for the sizing, selection and management of complete dewatering system including pump, piping, valves, electrical feed, generator monitoring equipment and automation. Coordinate meetings with other trades and maintain constant communication with General contractor and project owners during the project lifecycle. Prepare and coordinate execution plan involving site logistics, equipment mobilization, manpower, and material kit list for drilling, equipment installation and electrical requirements. Prepare and maintain up to date dewatering system drawings, equipment electrical supply and heat trace setup. Responsible for the submittal of commercial documentation such as monthly AFPs (authorization for payments) change orders, new quotes. Create POs and review and authorize suppliers invoicing. Prepare HSE packages, including risk assessments, method statement, SDS (safety data sheets), employee training. Responsible for requesting, reviewing locates to assess buried infrastructure risks prior to drilling operations. Review and submit daily PSA, toolbox talk, borehole logs and well schedules. Submit to the MOE well records, discharge setup documentation and monthly discharge logs. Show less
-
-
Field Engineer
-
Jun 2021 - Sep 2022
As a field engineer, I was responsible for the coordination for up to 4 sites, all activities related to instructing site foreman’s daily duties, coordinate with site supers, project managers and other trades, logistics pertaining to site access, storage area, weekly activities schedules and work related issues. Ensured drilling and operations activities were performed according to the system and equipment specification. During this time, I was able to provide a more technical and professional communication and coordination between the company and the client for site related operations. Optimized daily operation’s performance and improved the utilization of resources on site impacting positively the project budged while also projecting a positive perception of the work performed, helping to retain company’s reputation for current and future projects. Served as a point of technical support to site foremen for the resolution of site equipment underperformance or failure. This includes dual piston vacuum pumps, liquid ring vacuum pumps, submersible pumps, sump pumps, dosing pump, vertical multistage pumps, and filtration equipment. Provided internal consultancy and planning in conjunction with panel suppliers for the construction of new control panels for the operation of dewatering systems. Prepared and recorded all information pertaining to well schedules, discharge logs and daily site progress. Provided coordination with site project manager and supervisor for all activities, addressing any changes of scope, schedules or site issues. Served as part of the safety committee and assisting on the improvement or correction to site specific HSE issues. Show less
-
-
-
TeamWork General Contracting
-
Canada
-
Construction
-
Project Coordinator
-
Oct 2020 - Jun 2021
Responsible for coordinating multiple renovation projects with budgets of up to $140,000. Coordinate and interface with customers and trades all concerning issues regarding the scope of work. Ensure that materials and workmanship comply with customers’ expectations and building code compliance. Met with clients or stake holder to evaluate projects requirement and scope of work. Performed material and labor calculations according to project scope. Elaborated a project schedule and coordinated sequence of events with contractors and material suppliers. Performed site inspections and clarified or solved electrical, plumbing, HVAC and other contractors any technical issues or changes of scope. Assured that all construction is being performed complies to construction codes and to correct quality finishes. Maintained and summited a detailed budget report for each project. Created drawings of floor plants for estimation and trades guide and 3D rendering for customers review. Show less
-
-
-
Hidraulica Hebron
-
Venezuela
-
Appliances, Electrical, and Electronics Manufacturing
-
1 - 100 Employee
-
Project Manager
-
Jun 2019 - Oct 2020
Provided the company with project portfolio management through an assigned group of 20 people comprised of engineers, sales agents, field, and in-shop technicians. Responsible for creating customers relationships and building strategic alliances with product providers to strengthen company revenues and increase strategic customer portfolio. Responsible for scheduling and project budget. Provided support during meetings with stakeholders to define or resolve issues that arise during the project life cycle. Successfully introduced into the company new technology and products that produced and increase of 60% of net sales. Supervised daily operations with project engineers and technicians to ensure that project milestones were met according to project outline. Provided field engineers with feedback for systems or components failures and suggested fixes. Show less
-
-
Technical Sales
-
Jan 2016 - May 2019
Responsible for creating and developing a new business branch in Peru comprise of a team of 5 members. Successfully introduced a new brand of submersible pumps and constant pressure systems manufactured in Venezuela into the Peruvian market. Performed a market evaluation and analysis of current equipment and equipment providers. Developed a market strategy based on the products and a list of potential customers. Provided company and product presentation to potential distributors and customers. Completed on-site inspection and review project’s drawing to determine customers’ requirements. Performed hydraulic calculations to design pumping systems including product selection, pump and pipe size, valves, generators, monitoring equipment and automation. Elaborated detailed engineering quotes and reports on system performance, conditions, and proposed upgrades of all electromechanical components of end suction pumping system, fire extinguishing system and submersible pumping systems. Met with customers and evaluated possible jobs opportunities in new or outdated pumping systems and control panels and developed technical and economic reports pointing to advantages and return of investment. Performed water well borehole inspections to evaluate conditions structural conditions of wells and/or evaluated dropped submersible equipment to design and evaluate retrieval tools and techniques. Show less
-
-
Field Engineer
-
Jan 2010 - Dec 2015
Provided support to field and in-shop operations in a variety of settings and applications in high rise buildings pumps, food processing plants, fire protection systems, irrigation, water wells, and water treatment. Acquired in-depth knowledge in concepts of hydraulic theory applied to pump curves, pipe dimensioning, flow control and measuring components. Solid understanding of concepts related to the pumping industry such as pressure, flow, velocity, fluid density, solid handling, and water quality. Carried design and implementation of constant pressure and hydro pneumatic systems including pump sizing, control panel design including programing, selection of measurement and control components. Performed pre installation onsite visits to coordinate and inspect with site engineers and trades that electrical supply lines and water inlet for water riser lines in machine room had been properly placed prior to installation. Responsible for commissioning pumping systems evaluating proper system operation and programing of system to avoid over/under pressure, water hammers. Coordinated with site engineers to determine possible problems such as water leakage, pipe obstructions or water regulation valve problems. Performed trouble shooting and root cause analysis (RCA) and repair of electromechanical equipment’s such as controls panels, motors, pumps, measuring and control devices and filters. Supervised in-shop pumps disassembly and performed evaluation, diagnostic and probable causes of failure of its mechanical components. Show less
-
-
-
Kasa Companies
-
United States
-
Automation Machinery Manufacturing
-
1 - 100 Employee
-
Control Engineer
-
Jan 2009 - Dec 2009
Designed internal layout and component sizing and selection for motor control panels. Troubleshooted and diagnosed automation equipment including panel components, input sensors and output components such as ac motor, servo motors, solenoids, and alarms. Elaborated BOM for purchasing department. Developed and inspected electrical prints. Assisted clients with customer support and product training. Performed PLC programing and HMI design based on Allen Bradley Technology. Assisted with project commissioning. Show less
-
-
Education
-
Pittsburg State University
Bachelor of Applied Science - BASc, Electrical and Electronics Engineering -
Crowder College
Digital Communication Specialist, Computer and Information Sciences and Support Services
Community
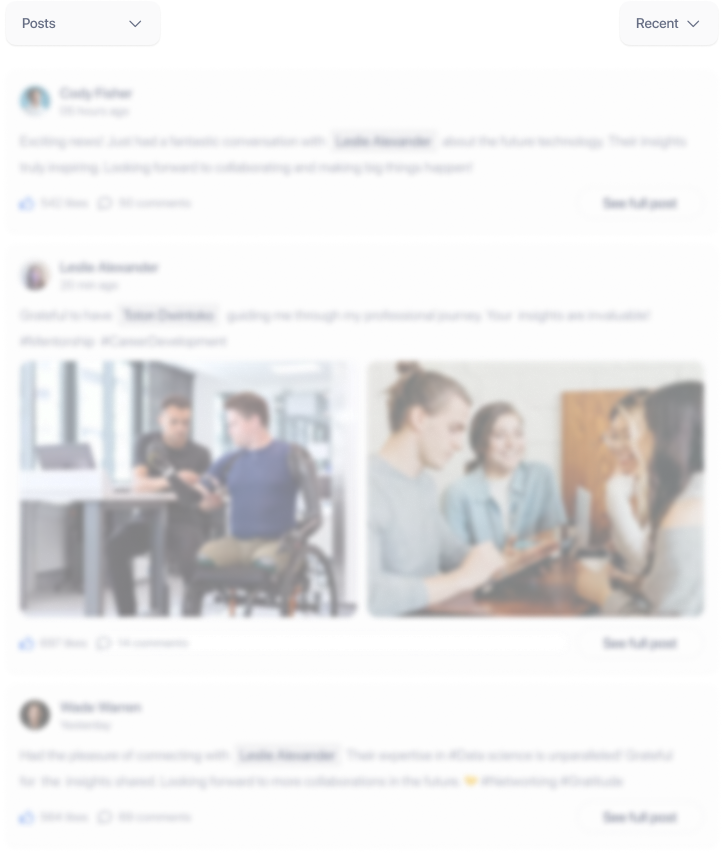