
Chris Gill
Site Planner at RPC Group Plc- Claim this Profile
Click to upgrade to our gold package
for the full feature experience.
Topline Score
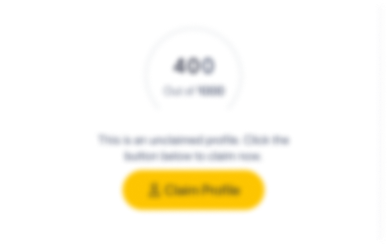
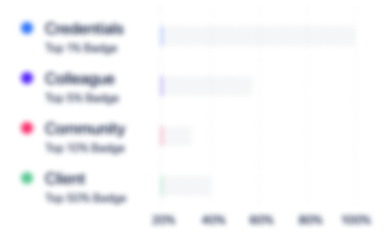
Bio


Experience
-
RPC Group Limited
-
United Kingdom
-
Plastics Manufacturing
-
300 - 400 Employee
-
Site Planner
-
Jul 2017 - Present
Production planner for over 50 separate production lines. Working with over 300 tools across several hundred customers. Demand is presented in a range of formats from stock maintenance on standard items, made to order goods and products on long term forecasts requiring a range of planning methods to be used in parallel. Particular focus on monitoring efficiencies of lines and identifying problems as they occur to maximise the companies ROI.Responsible for producing KPI reports and performing data analysis to identify areas where there are financially viable options for continuous improvement. Additional tasks include internal audits, continuous improvement projects, product traceability exercises, pivot table reports, database queries, labour management and producing the quarterly budget pack.
-
-
Warehouse Administrator
-
Feb 2016 - Jul 2017
Responsible for all outgoing traffic from a busy 24 hour warehouse, Primarily dealt with through the production of a daily load plan, dealing with booking collections and organising deliveries with customers. Additionally responsible for stock takes and overall stock accuracy within the warehouse.Time management was the top priority. With a limited number of vehicles able to be on site at once and dealing with both customer collections and our own team of contracted drivers, every aspect of the day had to be built into the load plan. With redundancy for any unexpected time loss as delays would cause knock-on effects throughout the day, not just for ourselves, but our customers. As we dealt with a variety of Incoterms the role was customer facing, deliveries had to be booked in with our customers and collections needed to be allocated timeslots. This meant a high level of professionalism and customer service was required along with the ability to deliver bad news in a positive light.The ability to work in a team was crucial, particularly with the goal of maintaining high stock accuracy. This was solved through ensuring we had procedures for every aspect of the warehouse and ensuring all members of the warehouse team were working from them. In addition I developed several pivot tables from database extractions in order to regularly check stock holdings, total capacity and any egregious receipts.
-
-
Floorman
-
Nov 2014 - Feb 2016
Responsibilities included the supply of raw materials from stores to production, movement, wrapping and receipting of finished goods production from production to the warehouse and factory break relief.Given the financial implications of mistakes accuracy was highly important for all stock movement both into and out of production. Being able to follow the IT systems and verify that each action had gone through successfully was crucial.Floormen serviced the entire factory rather than individual departments meaning we had no direct supervision. As a result self-motivation and good time management was required. Production both consumed raw material and completed finished goods at varying rates meaning you had to have an understanding of when each line would need attention, with over 50 separate lines you could not afford to waste time checking an area that did not need anything doing.As you were working in an active warehouse a good knowledge of the health & safety risks of operating around a forklift and the correct way of moving bulky item’s such as pallets was necessary.
-
-
Production Operator
-
Mar 2014 - Nov 2014
Encompassed various roles including Product Assembly, Line Operator and Quality Assurance.On assembly lines time management and teamwork were key as for some products you were part of an assembly sequence meaning what you did directly affected everything other process further down the assembly line. Shift quotas were in place which required the ability to work efficiently under pressure. Working on the machine lines required an understanding of the products as you were responsible for doing regular quality assessments. An ability to understand the procedures behind the quality checks as well as the ability to understand the product specifications were a must. Due to the large number of different products produced you were often working multiple lines with different product mixes requiring you to be highly flexible in your routine.
-
-
-
St Barnabas Hospice
-
United Kingdom
-
Hospitals and Health Care
-
1 - 100 Employee
-
Van Assistant
-
Nov 2013 - Dec 2013
Collections from stores across Lincolnshire and general manual labour. Teamwork required to unload and sort items into item types on a tight unloading schedule. Learned to identify items which would be quick to sell and prioritise these items for sorting. Collections from stores across Lincolnshire and general manual labour. Teamwork required to unload and sort items into item types on a tight unloading schedule. Learned to identify items which would be quick to sell and prioritise these items for sorting.
-
-
Education
-
De Aston
A Levels -
De Aston
GCSE
Community
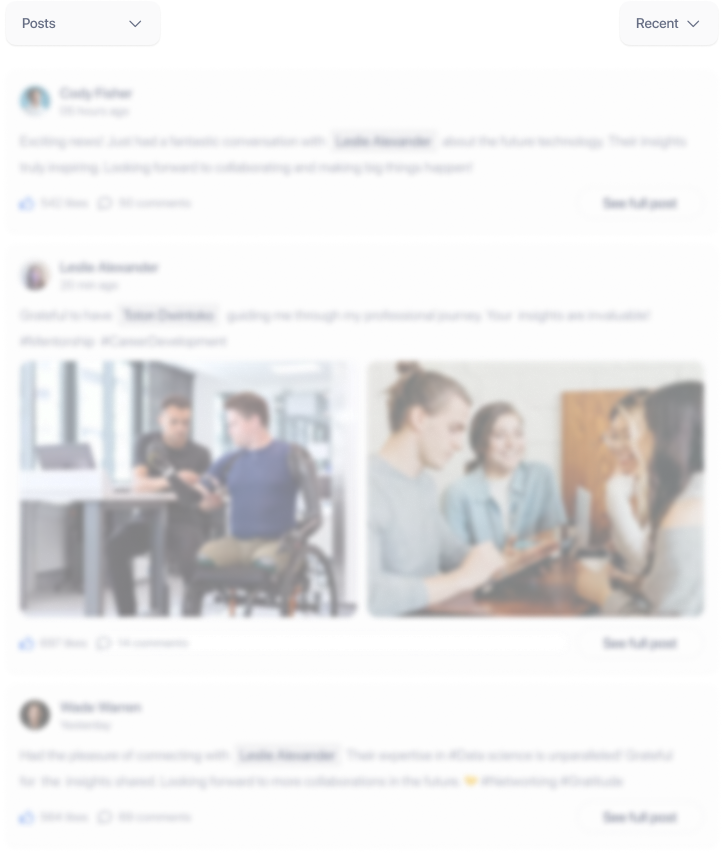