Chris Wernau
Manager of Environmental Health and Safety at Mando Corp.- Claim this Profile
Click to upgrade to our gold package
for the full feature experience.
Topline Score
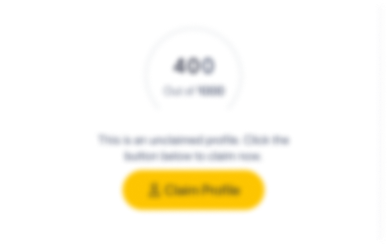
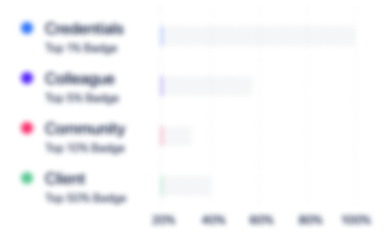
Bio


Experience
-
Mando
-
South Korea
-
Motor Vehicle Manufacturing
-
200 - 300 Employee
-
Manager of Environmental Health and Safety
-
May 2019 - Present
Manage EHS specialists and engineers at six facilities in Alabama, Georgia and Michigan.Maintain certifications for EMS and OHSAS standards. Support compliance for federal, state and local regulations.Evaluate aspects and impacts to improve material utilization and monitor waste streams.
-
-
Production Engineer
-
Apr 2016 - Apr 2019
Process engineering and continual improvement for automotive castings.Develop standard work and process controls for Melting, Refractory, Core shop, Green sand system, Finishing operations. Lead task force teams (TFT).Six Sigma Green Belt project for digital sand and resin control upgrades.Install tonnage sensors to prevent damage to trim press punch tooling and equipment.Upgrade facility from jib crane to overhead bridge crane to support increased productivity.Coordinate installation of storage racks to improve utilization of floor space for product and tooling storage and retrieval.Revise melting recipe to increase usage of gating and returns. Reduce purchased materials by 25%Develop common control plans for product families. Support ISO IATF quality systems and auditing.
-
-
Quality Engineer
-
Nov 2013 - Apr 2016
•Develop process controls and inspection methods for automotive ductile/nodular iron castings•Prepare APQP, PPAP, PFD, CP and PFMEA documents and samples•Implement destructive and nondestructive (NDT) testing requirements per industry standards•Participate and facilitate cross functional teams
-
-
-
Boyd
-
United States
-
Appliances, Electrical, and Electronics Manufacturing
-
700 & Above Employee
-
Quality Engineer
-
Jun 2012 - Nov 2013
•Coordinate the integration of products due to facility closure and submit inspection reports to customers•Develop bar code scanning system to detect and prevent mislabeling of products•Develop process for maintaining steel rule cutting dies and improving operator training and support •Coordinate the integration of products due to facility closure and submit inspection reports to customers•Develop bar code scanning system to detect and prevent mislabeling of products•Develop process for maintaining steel rule cutting dies and improving operator training and support
-
-
-
Gardner Denver
-
United States
-
Machinery Manufacturing
-
700 & Above Employee
-
Quality Supervisor
-
Feb 2005 - Dec 2011
•Conducted Kaizen to reduce warranty, scrap and rework for bearing failures due to contamination•Initiated project to standardize work instructions by product family•Prepare Advance Quality Planning (AQP), FMEA, control plans, and PPAP documents, and define process and quality standards (API, ASME, ASTM, AWS, ISO, SSPC). Develop Nondestructive Testing (NDT) criteria (MT, PT, UT, VT).•Established customer and supplier requirements, test limits and policies. •Participated in cross functional teams with manufacturing, engineering, sales and customers
-
-
-
Vernay
-
United States
-
Plastics and Rubber Product Manufacturing
-
100 - 200 Employee
-
Quality Engineer
-
Sep 1999 - Feb 2005
•Improved work cell productivity by 200% through automation •Conducted Kaizen activity that reduced external defects by 40%•Reduced material consumption on Viton elastomers by 20% through process controls.•Lean manufacturing: Kaizen, process mapping, poke-yoke mistake proofing, BOM•Statistical and quality tools: DOE, CpK, SPC, control charts, FMEA, AQP, PPAP, Gage R&R. •Improved work cell productivity by 200% through automation •Conducted Kaizen activity that reduced external defects by 40%•Reduced material consumption on Viton elastomers by 20% through process controls.•Lean manufacturing: Kaizen, process mapping, poke-yoke mistake proofing, BOM•Statistical and quality tools: DOE, CpK, SPC, control charts, FMEA, AQP, PPAP, Gage R&R.
-
-
Education
-
Northeastern University
Bachelor of Science (BS), Mechanical Engineering
Community
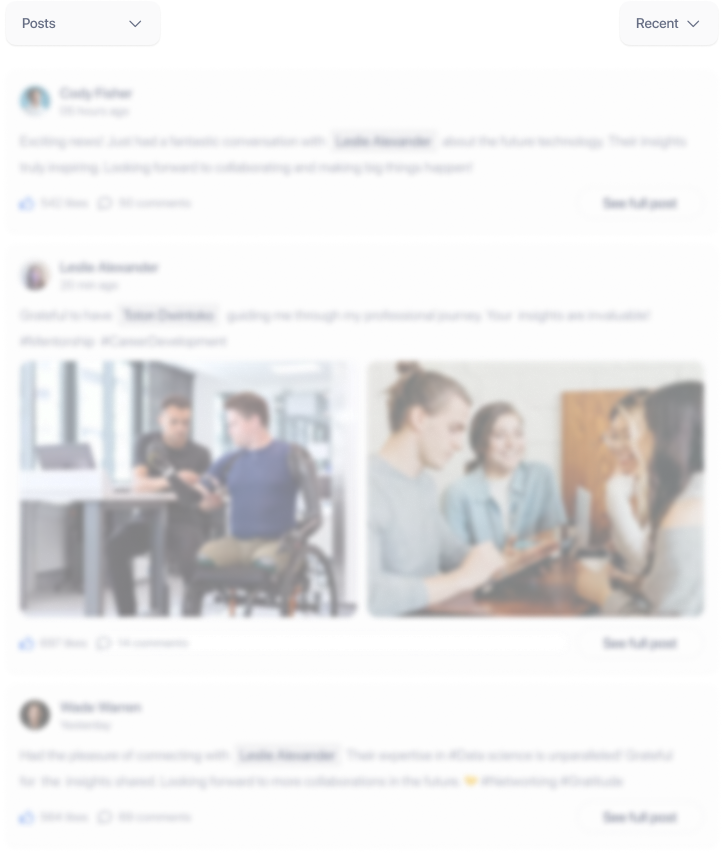