Chris Scocco
Assistant General Manager at Arma Container Corp- Claim this Profile
Click to upgrade to our gold package
for the full feature experience.
-
Spanish Limited working proficiency
-
English Native or bilingual proficiency
Topline Score
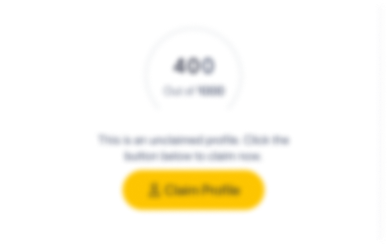
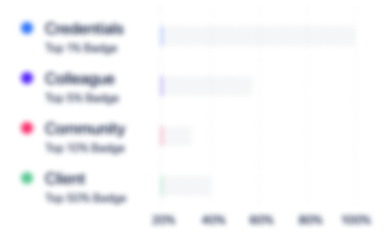
Bio

Adam Hollander
Chris is by far one of the most capable, dependable and resourceful people I've ever had the pleasure of working with. Through his leadership the company has been more focused, effective, better-structured and more profitable. His precise attention to detail and ability to manage the company's day-to-day operations in conjunction with special projects places him in an ultra-critical role; one in which he continues to excel at and perform. Approachable and easy-going with a knack for concentrating the efforts of many, his qualities make him a joy to work with.

Adam Hollander
Chris is by far one of the most capable, dependable and resourceful people I've ever had the pleasure of working with. Through his leadership the company has been more focused, effective, better-structured and more profitable. His precise attention to detail and ability to manage the company's day-to-day operations in conjunction with special projects places him in an ultra-critical role; one in which he continues to excel at and perform. Approachable and easy-going with a knack for concentrating the efforts of many, his qualities make him a joy to work with.

Adam Hollander
Chris is by far one of the most capable, dependable and resourceful people I've ever had the pleasure of working with. Through his leadership the company has been more focused, effective, better-structured and more profitable. His precise attention to detail and ability to manage the company's day-to-day operations in conjunction with special projects places him in an ultra-critical role; one in which he continues to excel at and perform. Approachable and easy-going with a knack for concentrating the efforts of many, his qualities make him a joy to work with.

Adam Hollander
Chris is by far one of the most capable, dependable and resourceful people I've ever had the pleasure of working with. Through his leadership the company has been more focused, effective, better-structured and more profitable. His precise attention to detail and ability to manage the company's day-to-day operations in conjunction with special projects places him in an ultra-critical role; one in which he continues to excel at and perform. Approachable and easy-going with a knack for concentrating the efforts of many, his qualities make him a joy to work with.

Credentials
-
Certified IPC Specialist
IPC-Association Connecting Electronics IndustriesJan, 2016- Oct, 2024
Experience
-
Arma Container Corp
-
United States
-
Packaging & Containers
-
1 - 100 Employee
-
Assistant General Manager
-
Jan 2017 - Present
Overall P&L responsibility for Manufacturing, Quality, Warehousing, Maintenance, Logistics and Delivery. Finance – Collaborate with General Manager to prepare annual budgets for all organization areas. Provide monthly progress against budgets and review the overall financial health of the company with ownership. Utilizing Budget information and KPI data, work with consultants to update the cost model and pricing matrix in our ERP system (Encore/Amtech). Manufacturing – Lead the Manufacturing and Production Planning teams. Establish goals and provide feedback on key performance indicators including volume (MSF Produced), changeover times, machine speeds and quality. Identify training needs and provide and/or coordinate training activities. Work with employees at all organizational levels to improve quality and efficiency. Safety – Drive the Safety initiatives for the company and participate as a member of the Safety Committee and First Aid and CPR Certified Team. Quality – Review quality issues to determine root cause and corrective action. Develop tools, techniques and procedures to reduce and potentially eliminate errors. Logistics and Delivery – Negotiate Lease agreements for equipment including fork-lifts, tractors and trailers. Approve HUT and IFTA filings, review driver logs (ELDs). Define and acquire appropriate mobile assets to support customer requirements. Establish and maintain a Fleet Safety Program. Information Technology – Identify and coordinate the selection, procurement, implementation and maintenance of all hardware and software needs for the organization. Human Resources – Prepare job listings, review applicants and set-up interviews with qualified individuals. Conduct interviews, hire and oversee the onboarding and training of new hires. Prepare and deliver employee performance reviews and recommend wage increases, bonuses and other employee recognition initiatives. Show less
-
-
-
Accusonic Voice Systems
-
United States
-
Telecommunications
-
1 - 100 Employee
-
Vice President Operations
-
Mar 2009 - Dec 2016
Operations – Effectively manage the Operation of as many as three company sites including Product Design and Development, Manufacturing, Quality, Distribution and other supporting functions. Setup new processes and equipment and validate their adequacy for operational improvement. Implement Lean Manufacturing principles and Visual Management tools throughout the organization. Business Development and Sales - Perform inside, outside and Government Sales activities (foreign and domestic) including establishment of new customers as well as development and expansion of existing accounts. Attend and exhibit at trade shows. Negotiate pricing, terms of sale, and inventory stock levels for all incoming orders. Identify and respond to opportunities on DIBBS. Obtained and manage a GSA Contract and perform all activities related to it. Product Development - Identify new product opportunities and direct engineering in the design and development of new products. Lead the product realization process and ensure the performance of adequate validation activities. Developed the first to market Multi-Function Tactical ancillaries with a team of Engineers acting as Product/Project Manager and Customer Liaison. Obtained a Patent for a Ruggudized Military Handset. Quality – Established and maintain an ISO 9000 compliant Quality Management System. Perform all duties of the Management Representative including Internal Auditing, QMS maintenance and registrar audits. Planning and Scheduling - Perform material and resource planning as well as production scheduling activities for all sites. Oversee procurement of materials to support production schedules. Negotiate pricing, terms and long-term purchase agreements Finance - Prepare budgets, forecasts and strategic plans for all operating units. Present actual results versus plans to Ownership. Implement changes as needed in order to accomplish set strategic initiatives. Show less
-
-
-
GKN Aerospace
-
United Kingdom
-
Aviation and Aerospace Component Manufacturing
-
700 & Above Employee
-
787 Program Management Team
-
2007 - 2009
Worked as part of a four person team who handled all aspects of the Boeing 787 Program from sales and order processing through manufacturing and quality to delivery and payment. Primarily responsible for all “Quality” related functions including systems and procedures, product verification and documentation packages. Designed, developed and implemented an automated system to prepare Quality Performance Metrics for presentation to local and corporate management as well as customers. Nominated for a GKN International, Corporate Excellence Award in Information Technology for work on this project. Implemented Lean Manufacturing and Visual Management tools in order to improve product flow. Traveled internationally to develop customer relations and resolve disputes. Worked directly with supply chain to develop plans and procedures for the on-time delivery of conforming product to support contract requirements. Also worked at Monitor Aerospace 1997-1998 Show less
-
-
-
Cypress Group
-
Belgium
-
Real Estate
-
1 - 100 Employee
-
Management Consultant
-
2005 - 2006
Prepared and delivered training and consulting services on Management, Operations and Quality Assurance topics for clients including, ISO 9000, AS 9100, Lean Manufacturing and Process Improvement Teams. Developed Workflow, Procedural, Technical and Operational documentation for clients. Delivered training to clients under NYS Training Grants obtained through SUNY Stony Brook. Also worked for Cypress Group from 1994-1997 Prepared and delivered training and consulting services on Management, Operations and Quality Assurance topics for clients including, ISO 9000, AS 9100, Lean Manufacturing and Process Improvement Teams. Developed Workflow, Procedural, Technical and Operational documentation for clients. Delivered training to clients under NYS Training Grants obtained through SUNY Stony Brook. Also worked for Cypress Group from 1994-1997
-
-
-
-
Director, Quality Assurance
-
2002 - 2005
Ensured the development and effective implementation of an ISO 9000 compliant Quality Management System, for as many as three organizational divisions and manufacturing facilities. Lead process improvement initiatives to reduce over-head costs while increasing productivity, quality, on-time delivery and overall customer satisfaction. Assisted Sales in winning new accounts as well as account preservation and development through periodic visits and fulfillment of quality requirements. Responsible for the setup, operation and maintenance of an on-site Product Testing Laboratory, personally achieving Certified Testing Lab status from Estee Lauder. Dispatched to customer facilities to trouble-shoot and resolve product related difficulties. Implemented and maintained a Customer Complaint and Resolution Process. Show less
-
-
-
Southern Container
-
United States
-
Truck Transportation
-
Quality Manager
-
2000 - 2002
Responsible for product and process quality at two manufacturing facilities. Assisted Sales in winning new accounts as well as account preservation and development through periodic visits and fulfillment of quality requirements. Responsible for the justification and resolution of customer credits as well as the collection of unauthorized deductions; deductions recovered ranged up to 100% of the original invoice value. Dispatched to customer facilities to trouble-shoot and resolve product related issues. Show less
-
-
-
-
Quality Coordinator
-
1998 - 2000
Responsible for the effective maintenance of an ISO 9000 compliant Quality Management System. Re-established the DZUS Motorsports Product Line. Created new products and established sales for the line. Worked closely with Sales office located out of state to ensure Quality Management System documentation addressed any and all Customer Specific Requirements. Responsible for the effective maintenance of an ISO 9000 compliant Quality Management System. Re-established the DZUS Motorsports Product Line. Created new products and established sales for the line. Worked closely with Sales office located out of state to ensure Quality Management System documentation addressed any and all Customer Specific Requirements.
-
-
Education
-
Saint Joseph's College
Bachelor's Degree, Business Administration and Management, General -
SUNY Oswego
-
St. Anthony's High School
Regents Diploma, College Prep -
TechniGraphics
CATIA V5 Aerospace Fundamentals
Community
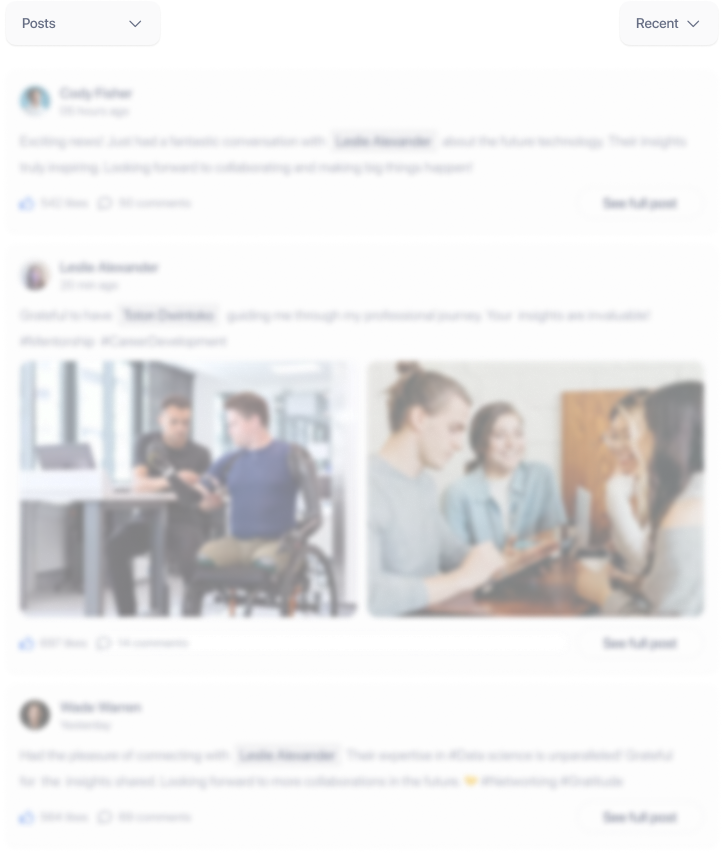