Chris Pahls
Nexcaliber Product Manager at Steel King Industries, Inc.- Claim this Profile
Click to upgrade to our gold package
for the full feature experience.
Topline Score
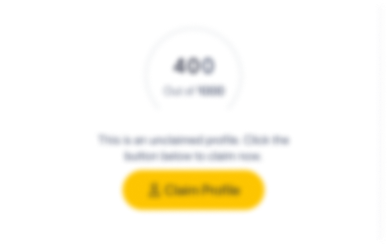
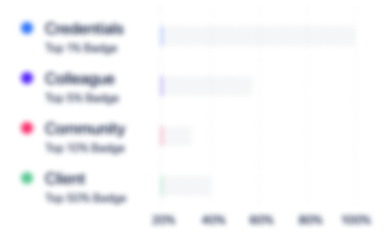
Bio


Credentials
-
OPOTA Certified
State of OhioAug, 2010- Nov, 2024
Experience
-
Steel King Industries, Inc.
-
United States
-
Transportation, Logistics, Supply Chain and Storage
-
100 - 200 Employee
-
Nexcaliber Product Manager
-
Jul 2020 - Present
-
-
-
Heartland Steel Products
-
United States
-
Warehousing and Storage
-
1 - 100 Employee
-
Executive Director Of Engineering
-
Jan 2019 - Mar 2020
Director of Engineering As a member of the executive team, managed an engineering staff of 20 individuals. Areas of responsibilities included: concept and estimating, project management, drafting, CAD programming, structural engineering and installed services spanning multiple product lines to include rack, safety guards, custom mezzanines/work platforms and means of egress products. Directed the integration of technical and engineering activities within projects with revenue values ranging from a few thousand to multi million dollars Provided professional and technical assistance to the sales and executive staff Maintained minimum margins for pricing structures on custom, finished good products and services Accomplishments: • Developed and implemented an automated, corporate-wide Engineering Change Request and Change Notice Program for drawing, BOM, routing, and resource group standards, resulting in more effective, efficient, and consistent change management practices. • Designed and implemented a formal change order and project tracker process used by project management and major customers, resulting in improved communication and accountability. • Managed the start up of an installed sales initiative, resulting in $500k sales revenue in the first quarter of existence.
-
-
-
Heartland Engineered Products
-
Harrison, Ohio, United States
-
Vice President & General Manager
-
Jun 2011 - Jan 2019
Vice President/General Manager Responsible for developing and managing all aspects (93 employee's) company to include: Sales, Concept and Estimating, Project Management, Structural Engineering, Operations, Materials Management, Human Resources, P&L budget, Capital Expenditure budget and strategic planning. Accomplishments: • Grew company revenue 4X over a period of five years. • Developed and managed P&L and Capital Expenditure budgets that fostered an average annual Sales growth of 42% and maintained an average 19.6% EBITDA • Set up subcontract suppliers as back up resources for added capacity of product outside of manufacturing scope, increased revenue which otherwise would not have been realized. • Developed and implemented a scheduling mechanism to manage the custom engineered steel structure product line while increasing revenue 2.5X; the system is still in use today. • Developed and implemented a capital project, resulting a 6-month ROI and $120k annual savings to operating budget. Project Scope: designed a 4 axis CNC machine that applies 16 holes in a steel tube with a cycle time less than 2 minutes and eliminated outsourcing • Secured and maintained a major safety products customer account with annual revenue of $4.5M • Initiated and managed fabricators certifications for the City of Los Angeles LADBS, Miami Dade County FL, and the City of Houston TX • Initiated and managed company CWB D1.1 weld certification • Managed regulator and compliance for EPA & OSHA
-
-
-
Hamilton County Sheriff Department
-
Cincinnati Metropolitan Area
-
Hamilton County Special Deputy
-
Sep 2011 - Jun 2018
Duties as as directed by the Sheriff Duties as as directed by the Sheriff
-
-
-
ASA CONTROLS, INC.
-
Facilities Services
-
1 - 100 Employee
-
Operations Manager
-
Mar 2011 - Jul 2011
Operations Manager Responsible for managing the day-to-day operations of the company. Developed schedules for engineering, programming, and field technician departments. Oversaw all job contracts by identifying specific tasks and monitoring rate of completion. Made recommendations to ownership regarding the hiring of new employees, current employee evaluations, and company process / procedures. Identified and developed plans of action for departmental improvement projects and assign tasks to individuals. Accomplishments: • Designed, developed and implemented a master schedule for all awarded contracts, resulting in increased consistency and efficiency in business operations with defined processes and resource assignments. • Designed, developed and implemented a company-wide time sheet system to track individual times by cost code per customer project, resulting in hard data used to drive more efficient resource allocations, reducing project costs. • Helped ownership identify company core processes and document them into a functional Gantt chart for each customer project, resulting in improved communication of schedules and milestones with clients. • Created standard company documentation used for hiring and process improvement activities; removed unnecessary variability from core processes thus improving efficiency and effectiveness. • Managed the development of a database (File Maker Pro) to capture and share specifications, “best practices” and general notes with all employees; improved cross-departmental communication.
-
-
-
Whitewater Building Products
-
Harrison, Ohio, United States
-
Architectural Design Engineer
-
Aug 2005 - Jan 2011
Architectural Designer / Engineer Involved in many aspects of company operations including: Estimating, Design, Engineering, Purchasing, & Production. Interacted with customers, office, and shop personnel regarding daily tasks such as quotations, fabrication material for shop, and final construction prints for customers and construction sites. Designed wall panels, roof trusses and their components, for commercial and residential housing, condos, apartments, and office buildings. Accomplishments: • Served as the first engineer in the company to learn and become proficient at operating wall panel and truss design software. • Wrote excel programs to improve many small tasks in both engineering and purchasing departments; improved efficiency in calculating landed cost and totaling materials units for BOM creation. • Created standard, layering, dimension, and scaling schemes through the use of model and paper space, along with simple macro buttons; improved Auto-CAD functionality and product presentation.
-
-
-
Torbeck Industries
-
Harrison, Ohio, United States
-
Engineering Manager/Project Manager/Shipping Manager
-
Oct 1988 - Aug 2005
Seventeen years of service with this employer which included several supervisory and management positions beginning at the shop floor level and working up to position of Engineering Manager. Engineering Manager Directed drafters, detailers, and structural engineers on a daily basis. Worked directly with other department supervisors and managers. Reported directly to C.E.O. of the company. Set and managed project schedules. Prepared and delivered customer presentations Conducted performance reviews. Project Manager Managed several customer projects ranging in value from $100,000 to over $1 million. Specific experience as a project manager included, creating the scope of preliminary design through to complete field install. Maintained project budgets, schedules, and aided customers in building permit processes. Became the “go to” PM for major orders due to my passion for delivery on-time and within budget. Managed the largest two level platform (200k SQ-FT) and grid structure (1 mile in length) from purchase order through install completion. Very well organized, multi-task oriented, and self-motivated. Shipping Manager Maintained freight carrier contracts and tariffs for LTL and Truck Load with service across the continental US, Mexico, and Canada Scheduled freight inbound and outbound with billing structures of PPD, 3rd Party, PPD and Add, resulting in an annual $200-350k profit Ensured safe packaging and loading practices for large, heavy structural product both FOB and Direct Shipment from suppliers
-
-
Education
-
Great Oaks Police Academy
BAS10-007, Criminal Justice/Police Science -
Dynamic Safety
10 Hour OSHA Compliance, OSHA Compliance -
Great Oaks Career Campuses
Leadership Skills -
Tetra Management Inc
Supervisory Leadership Development -
Ivy Tech Community College
Zenger Miller, Frontline Leadership -
La Salle Cincinnati
Industrial and Product Design
Community
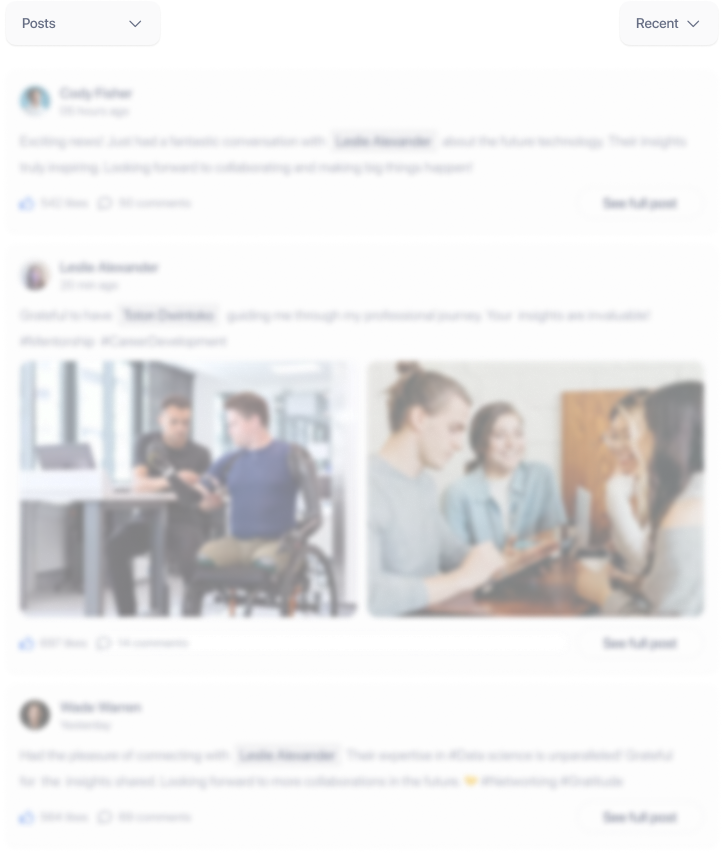