Chris Hopkins
Fabrication & Transport Manager at B R Hodgson Framing Ltd- Claim this Profile
Click to upgrade to our gold package
for the full feature experience.
Topline Score
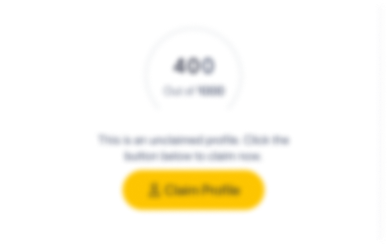
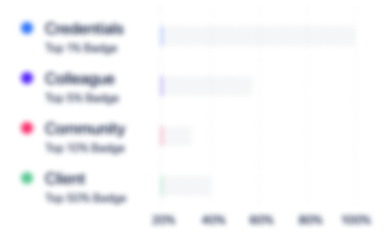
Bio


Experience
-
B R Hodgson Framing Ltd
-
United Kingdom
-
Construction
-
1 - 100 Employee
-
Fabrication & Transport Manager
-
Sep 2017 - Present
-
-
-
SYNCREON
-
United States
-
Truck Transportation
-
700 & Above Employee
-
Shift Manager/Junior Operations Manager
-
Aug 2016 - Sep 2017
Shift Manager/Junior Operations Manager for Syncreon working on the Jaguar Land Rover China contract. Sitting beneath the Operations Manager and alongside a Night Shift Manager, I am responsible for 2 of the 3 shifts overseeing 2 Supervisors, 4 Team Leaders and around 150 staff operating a 24/5 pattern. Shift Manager/Junior Operations Manager for Syncreon working on the Jaguar Land Rover China contract. Sitting beneath the Operations Manager and alongside a Night Shift Manager, I am responsible for 2 of the 3 shifts overseeing 2 Supervisors, 4 Team Leaders and around 150 staff operating a 24/5 pattern.
-
-
-
Sienna X
-
United Kingdom
-
Personal Care Product Manufacturing
-
1 - 100 Employee
-
Warehouse Coordinator
-
Feb 2014 - Jul 2016
Warehouse Coordinator for a market leading Spray Tan company supplying to direct customers via web and tele-sales as well as wholesale distributors. Warehouse Coordinator for a market leading Spray Tan company supplying to direct customers via web and tele-sales as well as wholesale distributors.
-
-
-
Spire Healthcare Group plc
-
United Kingdom
-
Hospitals and Health Care
-
700 & Above Employee
-
Warehouse Shift Manager
-
Oct 2013 - Feb 2014
Warehouse Shift Manager for a private Healthcare company. Responsible for 2 Team Leaders and 20 warehouse staff beneath them (employed and temporary) over an 8 hour shift, picking, packing and loading a fleet of 6 7.5tonne lorries and 4 vans ready for delivery to all 36 hospitals operating a 16/5 pattern. • Improved staff pick rates over 20% through introducing lean processes and altering existing procedures. • Introduced training to allow job rotation for staff and better holiday cover. • Created and implemented a way of monitoring staff productivity, and set targets. • Introduced better housekeeping procedures. • Responsible for overtime budget, managing 'bank staff' and temporary staff more efficiently to reduce overall staffing costs. • Responsible for health & safety of entire shift. • Introduced spot checks on picks to aide reduction of pick errors. • Managing HR and disciplinary issues with all relevant paperwork following company guidelines. • Introduced daily staff briefings at beginning/end of shifts and created a 'shift sheet' for the Team Leaders to track workload more effectively. • Working closely with Temporary Staff Agencies to continually meet business needs. • Primary keyholder, accountable for lock up and security of whole site.
-
-
-
DHL
-
Germany
-
Transportation, Logistics, Supply Chain and Storage
-
700 & Above Employee
-
Goods-In Supervisor (Warehouse)
-
Apr 2007 - Oct 2013
Goods-in Supervisor at a flagship DHL 3PL Warehouse which operates on a 24hour basis 5days a week. A varied and ever evolving role, but key objectives include overseeing the delivery of rail parts for the customer, Network Rail, in a fast paced and constantly adapting workplace to ensure inbound goods are inventory counted to stock while enforcing company ‘Standard Operating Procedures’ are adhered to within a target based environment.• Managing a team of up to 10 people daily.• Deputising Shift Managers, providing holiday/absence cover for shift of 20+ people across all departments.• Collating KPIs (Key Performance Indicators) daily and reporting them at management meetings.• Primary point of contact for all goods-in related queries & issue resolutions both face-to-face and via telephone/email.• Controlling the rate of deliveries via radio comm’s to ensure a smooth flow of workload throughout the day.• Show clear communication liaising with our outside business partners, as well as internal departments and other DHL sites, building rapport to suggest and implement solutions.• Introducing, reviewing and implementing new ‘Standard Operating Procedures’ to help streamline warehouse duties to increase overall productivity and exceed business targets.• Monitoring colleagues’ activities to ensure individual and company bonus related targets are achieved, understanding why and motivating those that fall behind.• Training new employees, evaluating their work and offering continual personal development.• Identification and storage of deliveries.• Using the bespoke web-based WMS to carry out every aspect of stock control from point of delivery through to despatch in real-time.• EDI Level 2 NVQ Certified Counterbalance & Reach truck driver.• Competent user of radio frequency & barcode technology to assist stock control duties.• Deliver company briefs to the staff as a group confidently.
-
-
Goods-In Administrator
-
Oct 2005 - Apr 2007
• Take deliveries of railway equipment and convert delivery notes into standardised forms using in-house ‘JBA’ computer system in order for warehouse staff to carry out their duties.• Liaise with suppliers via telephone/email to resolve problems delivery issues and arrange solutions.• Compiling KPI’s on a daily and weekly basis• Dealing with delivery drivers and couriers and signing relevant paperwork.• Filing and archiving of all paper records maintaining precision and accuracy.• Keep detailed records of work across various Microsoft functions such as Excel, Access/Word.• Worked with warehouse operatives, matching up & storing goods.
-
-
-
Texaco
-
Oil and Gas
-
700 & Above Employee
-
Stock Controller/Shift Team Leader
-
2003 - Oct 2005
• Crediting/invoicing deliveries on PC via the in-house ‘Prism’ package. • Compiling stock reports for management to view weekly/monthly sales, waste, income and expenditure figures. • Liaising with suppliers regarding order enquiries and delivery issues via telephone/e-mail. • Responsible for stock cycle on a monthly basis, involving auditing goods, compiling the data and keeping up to date records. • Reporting stock losses/gains information to management, with possible reasons for these providing solutions for future prevention. • Leading small team of 2 to run an 8 hour shift. • Customer facing role dealing with complaints in person or via telephone.
-
-
-
Door Panels Ltd
-
Industrial Machinery Manufacturing
-
1 - 100 Employee
-
Team Leader
-
2002 - 2003
• UPVC door production for one of the largest manufacturers in the UK. • Responsible for a team of 4 across an 8 hour shift. • Time management: prioritising work to meet factory demands. • Working to meet deadlines • UPVC door production for one of the largest manufacturers in the UK. • Responsible for a team of 4 across an 8 hour shift. • Time management: prioritising work to meet factory demands. • Working to meet deadlines
-
-
-
Severn Vale Services
-
United Kingdom
-
Motor Vehicle Manufacturing
-
Steel Fabricator/MIG Welder
-
2001 - 2002
• Production of domestic and industrial steel fabrications. • Producing detailed and accurate work to precise plans • Creating bespoke items from customer ideas. • On-site installations using a wide variety of tools. • Working to meet deadlines. • Production of domestic and industrial steel fabrications. • Producing detailed and accurate work to precise plans • Creating bespoke items from customer ideas. • On-site installations using a wide variety of tools. • Working to meet deadlines.
-
-
Education
-
Worcester College of Technology
City & Guilds (2360) Level 2 Certificates in Electrical Installation Theory & Practical Part One, Electrical/Electronics Equipment Installation and Repair, General -
Road Haulage Association
International Transport Manager CPC in Road Haulage -
IOSH
IOSH Managing Safely -
Hanley Castle 6th Form Centre
A-Levels (2), Grade C -
Hanley Castle High School
11 GCSE, Grades A*-C
Community
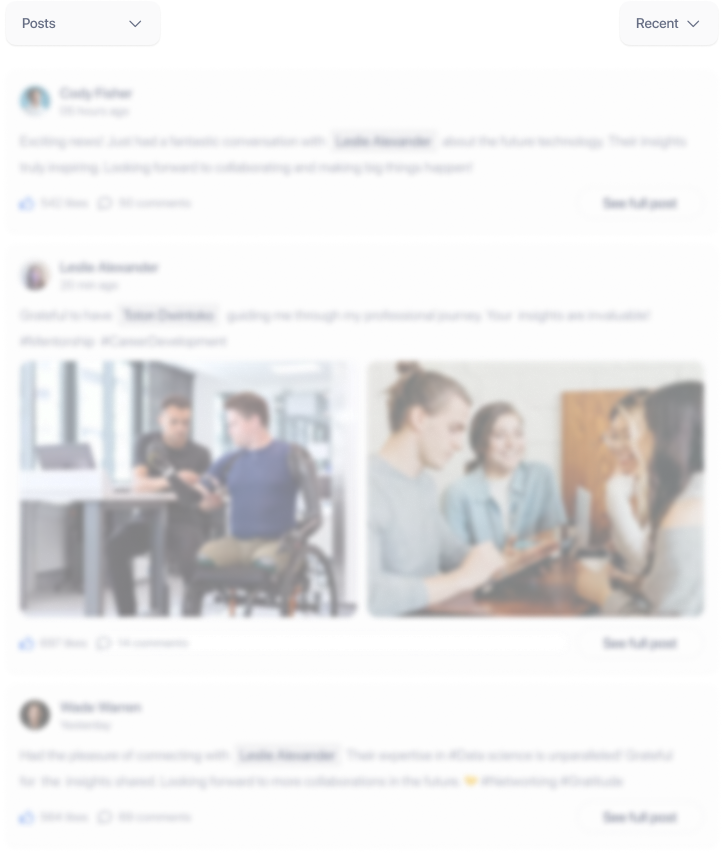