Chirag Shah
Quality Engineer at Tiercon Corp.- Claim this Profile
Click to upgrade to our gold package
for the full feature experience.
Topline Score
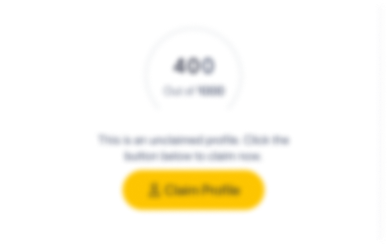
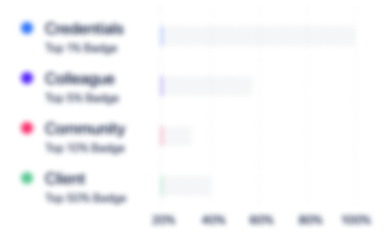
Bio


Experience
-
Tiercon Corp.
-
Canada
-
Automotive
-
100 - 200 Employee
-
Quality Engineer
-
Dec 2017 - Present
Tracked, monitored and analysed quality performance data for internal and more than 10 supplier using MS Office and Customer portals Created incoming inspection criteria and performed incoming inspection on raw material and provided direction to incoming quality personnel Created training documents and specification for incoming and in-process material and provided training to cross function teams As a part of APQP team, proactively participated in product, tool, gage and… Show more Tracked, monitored and analysed quality performance data for internal and more than 10 supplier using MS Office and Customer portals Created incoming inspection criteria and performed incoming inspection on raw material and provided direction to incoming quality personnel Created training documents and specification for incoming and in-process material and provided training to cross function teams As a part of APQP team, proactively participated in product, tool, gage and process design reviews on site and at customer Reviewed OEM and customer specific requirements and implemented necessary process and document changes to meet all requirements Created, maintained and implemented process control plans, PFMEAs and process flow by leading cross functional team of mfg engineers, design engineers and production leaders As a certified IATF-16949 internal auditor, performed system and process audit in-house and at supplier and completed non-conformance report Created Design and Process validation test plan to complete PPAP in order to meet project milestones Lead quality team to develop quality implementation plan for New product launches and engineering changes as a part of APQP Monitored and reported production performance for NPI and implemented corrective and preventive process changes as a part of corrective actions Planned, organized and completed all PPAP activities and obtained PPAP approval for NPI launches and model year engineering changes Lead proactive review of PFMEA and Control Plan to identified potential failure modes and deficiencies and implemented permanent process controls Show less Tracked, monitored and analysed quality performance data for internal and more than 10 supplier using MS Office and Customer portals Created incoming inspection criteria and performed incoming inspection on raw material and provided direction to incoming quality personnel Created training documents and specification for incoming and in-process material and provided training to cross function teams As a part of APQP team, proactively participated in product, tool, gage and… Show more Tracked, monitored and analysed quality performance data for internal and more than 10 supplier using MS Office and Customer portals Created incoming inspection criteria and performed incoming inspection on raw material and provided direction to incoming quality personnel Created training documents and specification for incoming and in-process material and provided training to cross function teams As a part of APQP team, proactively participated in product, tool, gage and process design reviews on site and at customer Reviewed OEM and customer specific requirements and implemented necessary process and document changes to meet all requirements Created, maintained and implemented process control plans, PFMEAs and process flow by leading cross functional team of mfg engineers, design engineers and production leaders As a certified IATF-16949 internal auditor, performed system and process audit in-house and at supplier and completed non-conformance report Created Design and Process validation test plan to complete PPAP in order to meet project milestones Lead quality team to develop quality implementation plan for New product launches and engineering changes as a part of APQP Monitored and reported production performance for NPI and implemented corrective and preventive process changes as a part of corrective actions Planned, organized and completed all PPAP activities and obtained PPAP approval for NPI launches and model year engineering changes Lead proactive review of PFMEA and Control Plan to identified potential failure modes and deficiencies and implemented permanent process controls Show less
-
-
-
Vuteq Canada Inc. Tier 1 supplier to Toyota and GM
-
Woodstock, Ontario, Canada
-
Quality Engineer
-
Oct 2015 - Dec 2017
Worked with OEM partners to understand Project Requirements, actively participated in APQP for engineering changes and executed work with highest accuracy to meet customer requirement Lead and managed quality functional teams to successfully implement OEM directed engineering work orders for model year and dimensional changes Conducted, participated and managed meetings between stake holders and cross functional team to track project quality performance and managed tasks… Show more Worked with OEM partners to understand Project Requirements, actively participated in APQP for engineering changes and executed work with highest accuracy to meet customer requirement Lead and managed quality functional teams to successfully implement OEM directed engineering work orders for model year and dimensional changes Conducted, participated and managed meetings between stake holders and cross functional team to track project quality performance and managed tasks and duties as required Presented, reported and discussed project quality performance with key stake holders and senior managers, took required actions and readjusted project plan Proactively analyzed processes using the process flow, Control Plan and PFMEA and brainstormed ideas to ensure negative risks are mitigated, removed or transferred and positive risks were exploited Self-Motivated to work with cross-functional teams of engineers, designers, production, maintenance and quality to install poke yoke, process control validation and inspection criteria to increase quality of the parts Adopted best practices from different production lines and suppliers and implemented on production line to increase cost saving and eliminate redundancy in processes Performed supplier and internal system audits to validate TS 16949 and BIQS requirements Measured dimensions of the sub-component, assembled product and raw material using various gages and implemented dimensional and cosmetic Inspection Standards with customer consultations to improve product quality Confidently made judgement calls on the cosmetic defect and created samples and provided training to team member to support production Analysed the dimensional reports using SPC and implemented corrective action to correct out of spec condition Tracked warranty claims for vehicle, analyzed vender defects and implemented necessary process changes to eliminate defects or to increase detection of the defects Show less Worked with OEM partners to understand Project Requirements, actively participated in APQP for engineering changes and executed work with highest accuracy to meet customer requirement Lead and managed quality functional teams to successfully implement OEM directed engineering work orders for model year and dimensional changes Conducted, participated and managed meetings between stake holders and cross functional team to track project quality performance and managed tasks… Show more Worked with OEM partners to understand Project Requirements, actively participated in APQP for engineering changes and executed work with highest accuracy to meet customer requirement Lead and managed quality functional teams to successfully implement OEM directed engineering work orders for model year and dimensional changes Conducted, participated and managed meetings between stake holders and cross functional team to track project quality performance and managed tasks and duties as required Presented, reported and discussed project quality performance with key stake holders and senior managers, took required actions and readjusted project plan Proactively analyzed processes using the process flow, Control Plan and PFMEA and brainstormed ideas to ensure negative risks are mitigated, removed or transferred and positive risks were exploited Self-Motivated to work with cross-functional teams of engineers, designers, production, maintenance and quality to install poke yoke, process control validation and inspection criteria to increase quality of the parts Adopted best practices from different production lines and suppliers and implemented on production line to increase cost saving and eliminate redundancy in processes Performed supplier and internal system audits to validate TS 16949 and BIQS requirements Measured dimensions of the sub-component, assembled product and raw material using various gages and implemented dimensional and cosmetic Inspection Standards with customer consultations to improve product quality Confidently made judgement calls on the cosmetic defect and created samples and provided training to team member to support production Analysed the dimensional reports using SPC and implemented corrective action to correct out of spec condition Tracked warranty claims for vehicle, analyzed vender defects and implemented necessary process changes to eliminate defects or to increase detection of the defects Show less
-
-
-
BlackBerry
-
Canada
-
Software Development
-
700 & Above Employee
-
Technical Administrator
-
Jul 2010 - Jul 2015
Maintained regulatory and carrier specific label requirements on device, Point of Sale and master carton labels for more than 200 carriers; designed new label format for the NPI products, supported product managers with region specific label requirements, supported manufacturing plants with label print application and participated in supply chain projects to reduce redundancy and increase efficiency. • To improve existing engineering change process; conceptualized, drafted and presented… Show more Maintained regulatory and carrier specific label requirements on device, Point of Sale and master carton labels for more than 200 carriers; designed new label format for the NPI products, supported product managers with region specific label requirements, supported manufacturing plants with label print application and participated in supply chain projects to reduce redundancy and increase efficiency. • To improve existing engineering change process; conceptualized, drafted and presented project charters to Quality, Software and Product management teams and successfully completed project that reduced workload by 35% without affecting quality of work produced • To avoid down time and reduce production cost; tracked and analysed production error rate and implemented tools and process changes that has increased efficiency and accuracy of work from 65% to 99% • To improve and standardize process among colleagues as team increased from 3 to 8 people; developed SOP and check-lists for each task, created and maintained departmental training material which eliminated inconsistency and increase department efficiency by 20% • Initiated and implemented necessary changes in SAP to support carrier SKU reduction from 250 to less than 100 without affecting final carrier requirements • To support changes in manufacturing and quality process, drafted training materials and delivered training to outsourcing quality, manufacturing and configuration teams of more than 50 people located in different regions which has increased efficiency by 35% • Continuously brainstormed and implemented changes in processes and tools to remove redundancy and improve efficiency in daily task and reduced workload as team down sized from 8 to 2 without affecting quality of work • Initiated, validated and supported SAP changes for supply chain to improve packing and shipping process that reduced error rate by 80%
-
-
Quality Technician
-
Jan 2008 - Jul 2010
Organised, re-organised and scheduled work of 5 quality inspectors to inspect more than 12 packing lines and more than 5,000 units at various stages of production on daily basis in order to meet customer and shipping deadlines. Evaluated, organised, reported and discussed quality findings in production meetings, performed root cause analysis and implemented corrective and preventive actions with manufacturing and engineering teams. • To support quality inspection of new touch devices, media… Show more Organised, re-organised and scheduled work of 5 quality inspectors to inspect more than 12 packing lines and more than 5,000 units at various stages of production on daily basis in order to meet customer and shipping deadlines. Evaluated, organised, reported and discussed quality findings in production meetings, performed root cause analysis and implemented corrective and preventive actions with manufacturing and engineering teams. • To support quality inspection of new touch devices, media and camera features; drafted and maintained inspection training documents and provided training to quality inspectors and production line workers which has resulted in product conformance to 95% • To standardized inspection process, created and maintained work instructions, inspection samples, training guides, training records and audit check sheets; preformed Guage R&R study for team of inspectors to eliminate inconsistency To investigate root causes on production defects, extensively used Quality Tools (control charts, histogram, flow chart, cause and effect) and Techniques(7Step problem solving, 5 whys, QFD) and implemented corrective actions Performed testing on material, process or product at different stages of production to investigate defects in final product using various measuring tools, templates, designed documents and CMM • To prevent use and shipment of non-conforming materials; applied Q-blocks in SAP, worked with warehouse team for segregation, drove disposition on the non-conforming goods and implemented stop ship in system as required • To support ISO 9001 and ISO 14001 audit process; updated process flow, trained and certified inspectors, performed preparation audit on other shifts • To successful launch of new product visited outsourcing plants in Mexico and provide expert knowledge on PILOT builds, FAI activities and ongoing inspection process to reduce defects
-
-
Quality Inspector
-
Sep 2005 - Dec 2007
• Performed inspection on finish product, semi-assembly, raw material and shipping audits with high accuracy using various measuring tools, gauges and understanding of CMM • Performed accurate pilot and FAI audit based on Customer Product Requirements and Bill Of Material and reported BOM inconsistency to configuration and packing teams for correction • Executed SAP blocks on non-conforming material and facilitated rework for non-conforming products • Prioritized and… Show more • Performed inspection on finish product, semi-assembly, raw material and shipping audits with high accuracy using various measuring tools, gauges and understanding of CMM • Performed accurate pilot and FAI audit based on Customer Product Requirements and Bill Of Material and reported BOM inconsistency to configuration and packing teams for correction • Executed SAP blocks on non-conforming material and facilitated rework for non-conforming products • Prioritized and worked with manufacturing, quality and shipping teams to meet shipping deadlines • Suggested and implemented improvement in audit processes at QA outgoing to reduce failure and rework • Identified defects though audit process, reported to large group with root cause analysis and suggested Corrective and Preventive actions
-
-
Electronic Assembler
-
Aug 2004 - Nov 2005
• Assembled BlackBerry with high precision as per Bill Of Material and disassembled BlackBerry to repair assembly issues • Lead packing lines of more than 12 employees as a subject matter expert with minimum rejects and high efficiency • Trained temporary and full time employees with different process to assemble and pack as per BOM • Ensured production quality and achieving and surpassing production targets on regular basis • Performed SAP transaction on rework… Show more • Assembled BlackBerry with high precision as per Bill Of Material and disassembled BlackBerry to repair assembly issues • Lead packing lines of more than 12 employees as a subject matter expert with minimum rejects and high efficiency • Trained temporary and full time employees with different process to assemble and pack as per BOM • Ensured production quality and achieving and surpassing production targets on regular basis • Performed SAP transaction on rework material, to order material and finished goods • Trained new and existing employees as per work instruction
-
-
Education
-
Project Management institute
Certified Project Management Professional, PMI -
American Society for Quality
Certified Quality Engineer, Quality Control -
American Society for Quality
Certified Quality Technician (CQT) -
Conestoga College
Project Management Professional, Project Management -
Gujarat University
Bachealor of Scince-Physics
Community
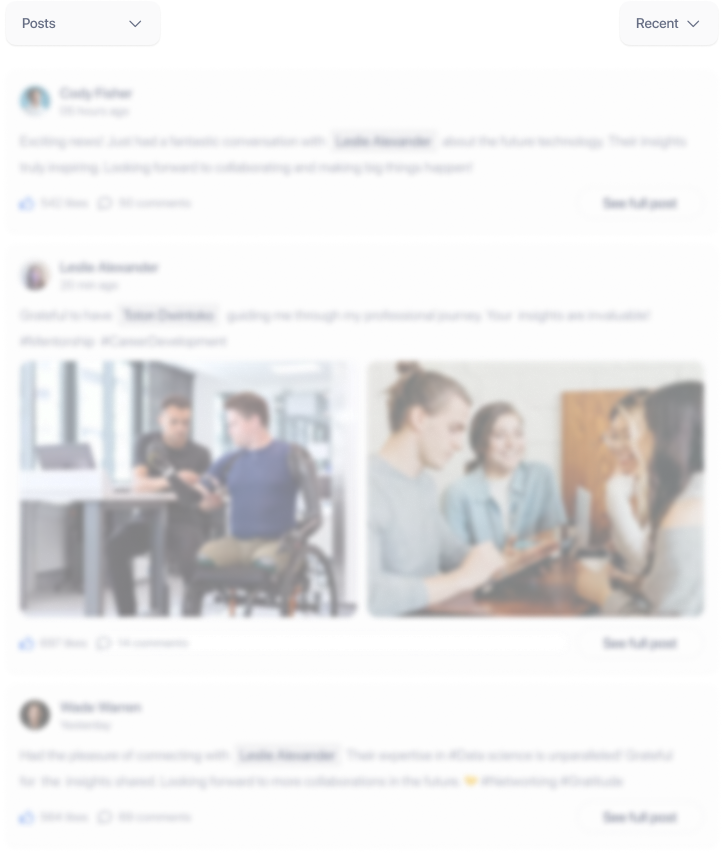