Chetan Bharadiya
QA Manager at KCI Bearings (India) PVT LTD- Claim this Profile
Click to upgrade to our gold package
for the full feature experience.
Topline Score
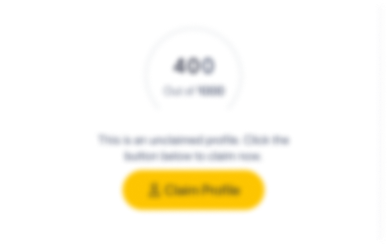
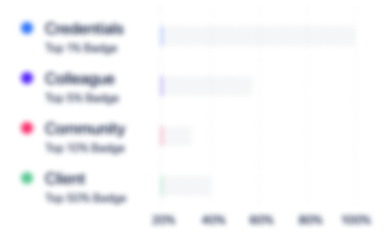
Bio


Experience
-
KCI Bearings (India) PVT LTD
-
India
-
Motor Vehicle Manufacturing
-
1 - 100 Employee
-
QA Manager
-
Sep 2021 - Present
-
-
-
TEXSPIN BEARINGS
-
India
-
Motor Vehicle Parts Manufacturing
-
300 - 400 Employee
-
Assistant Manager
-
Jan 2019 - Mar 2022
Managing overall quality functions within plant as SQA, Process quality, Customer complaint, Firewall inspection & TPI.SQA : Management of supplier quality performance(Rating), BOB & WOW supplier, supplier improvement plan, CFT member for New supplier development, PPAP & Run@rate, Co-ordination with SCM & development team, Supplier complaint handling, Quality improvement projects of Grinding stock reduction.IPQC : Ensuring that manufacturing process comply with standards. Controlling of In-process Quality assurance, FPA, Control plan, Process audit, Capability studies of machines, MIS reports, Monitoring of Gauges & calibration, Line problem solving, Product audit, Dock audit, Customer PPAP doc., NPD product quality monitoring, Monthly customer report submission.Firewall Insp. : Daily basis co-ordination with production dept for major rejection, Monthly rejection analysis, Improvement plans from respective dept.Customer complaint handling, Submission of 8D reports.TPI : Monitoring of TPI, Co-ordination for major defect with respective dept., Monthly reports & improvement plans.Quality improvement projects & Trainings to junior colleague for knowledge improvements.Core committee member for 5’s & Kaizen.
-
-
-
Shantam Engineering
-
United States
-
Telecommunications
-
1 - 100 Employee
-
Quality Control Manager
-
Nov 2017 - Dec 2018
Managing shop floor activities of Procurement, Planning, Production, Quality & Dispatch.Order scrutiny, Execution & dispatch schedules for smooth delivery to customers.Preparation of drawings from parts in case of customer drawing not available.Quality management & Audit handling.In-house 5’S maintenance. Managing shop floor activities of Procurement, Planning, Production, Quality & Dispatch.Order scrutiny, Execution & dispatch schedules for smooth delivery to customers.Preparation of drawings from parts in case of customer drawing not available.Quality management & Audit handling.In-house 5’S maintenance.
-
-
-
-
Asst. manager -FPP
-
Mar 2016 - Oct 2017
Looking after complete activities of FPP (Fired product Processing) & Packing Dept.Assisting team of 9 engineers & supervisors. Managing testing & packing activities with around 100 associates team who are working in all 3 shifts.Line improvements through 7’s & Kaizens.Achieving testing & packing targets as per company requirements. Working with CFT to reduce internal rejections. Skillfully implemented best 5’s practices inside the department. Looking after complete activities of FPP (Fired product Processing) & Packing Dept.Assisting team of 9 engineers & supervisors. Managing testing & packing activities with around 100 associates team who are working in all 3 shifts.Line improvements through 7’s & Kaizens.Achieving testing & packing targets as per company requirements. Working with CFT to reduce internal rejections. Skillfully implemented best 5’s practices inside the department.
-
-
-
FAG Bearings India Ltd (FAG)
-
India
-
Motor Vehicle Manufacturing
-
200 - 300 Employee
-
Executive
-
Mar 2012 - Feb 2016
Supplier Quality monitoring through Supplier performance rating, Supplier complaint handling & 8D reports, Improvements of WOW suppliers, Closely working with SCM, Supplier development & receiving inspection department.Monitoring during NPD product, sample development run, PPAP approval, APQP team member, process validation @ supplier end.Product/Sample development specialist.(Forging, Casting, machining, press component).Manufacturing feasibility with supplier.Perform supplier Qualification through supplier audits, Sample qualification process Supplier Performance Monitoring & Supplier Improvement action plan.Guiding supplier for Root-cause analysis, Poke-yoke implementation, 8D report, CAPA etc. for improvements.Training provide to supplier. Like 5s, 7QC Tools, 8D problem solving, PPAP doc. etc.
-
-
-
Rotex Automation Limited
-
India
-
Industrial Automation
-
100 - 200 Employee
-
Senior Quality Control Engineer
-
May 2008 - Feb 2012
Managing Receiving Department inspection activities of Incoming bought-out items, In-house machined components, Vendor Parts & Raw material testings & reports verification with team of Quality inspectors. Handling of Internal & External Calibration of various gauges, electrical and mechanical instruments, Salt Spray Test (as per the IS9000 Part-11)Internal rejection monitoring & rejection reduction planningControl of NC products, CAPA from internal departments.Internal assembly department complaints handling & necessary CAPA for future defect prevention.Customer complaint monitoring, Feedback, Analysis & submission of 8D reports to the customers.In house technical trainings to the production & Quality associates to improve their quality level.Accountable for Internal Rejection analysis, Internal assembly complains, Customer complaints, Supplier performance, Timely clearing of GRN, 5’S, Kaizen etc.Resolving issues through 8D Problem Solving Methods or 6 sigma methodology. Implementing CAPA, Poka-yoke on shop floor and Supplier end.Served as Internal Auditor and participated in various functions of organization as per ISO 2008
-
-
Education
-
L.D. College of Engineering
Bachelor of Engineering - BE, Mechanical Engineering
Community
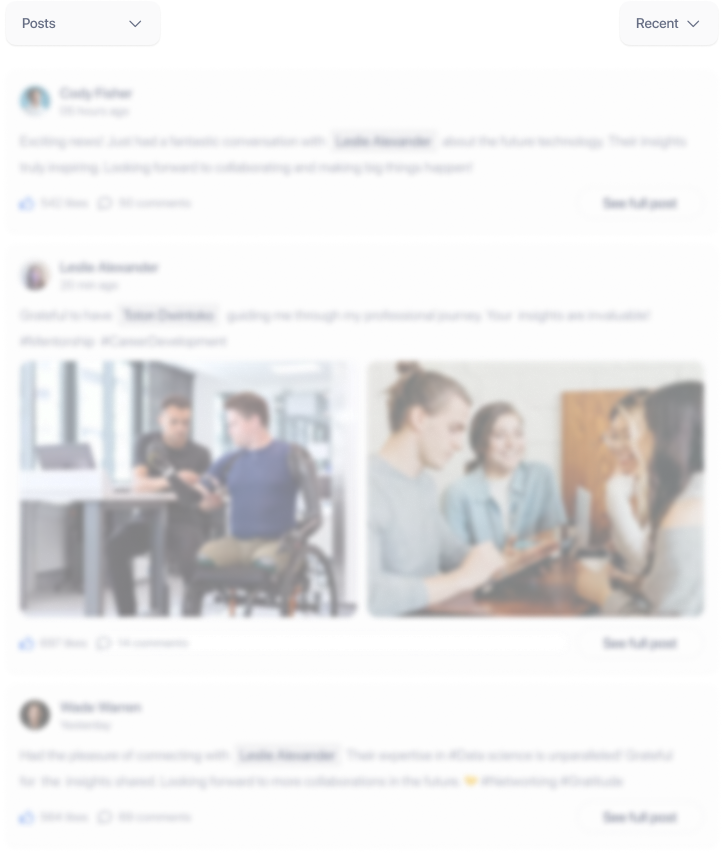