Cheryl Wilkinson
Product Manager at The Ethical Food Company Ltd.- Claim this Profile
Click to upgrade to our gold package
for the full feature experience.
Topline Score
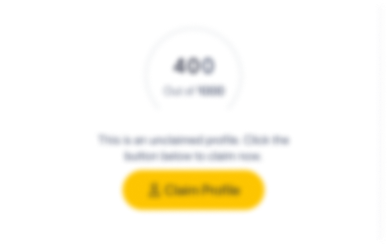
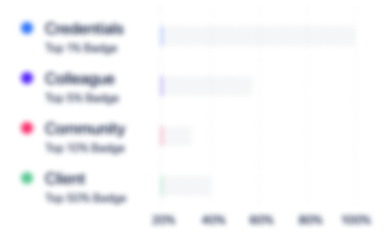
Bio

Fiona Barnard
Cheryl has excellent communication skills. In addition, she is extremely organized, reliable and computer literate. Cheryl can work independently and is able to follow through to ensure that the job gets done. She is flexible and willing to work on any project that is assigned to her. Cheryl was quick to volunteer to assist in other areas of company operations, as well.

Steve Belsey
Cheryl is a highly motivated and dedicated worker, attention to detail is excellent and she always has a bright and cheery nature which helps motivate colleagues around her.

Fiona Barnard
Cheryl has excellent communication skills. In addition, she is extremely organized, reliable and computer literate. Cheryl can work independently and is able to follow through to ensure that the job gets done. She is flexible and willing to work on any project that is assigned to her. Cheryl was quick to volunteer to assist in other areas of company operations, as well.

Steve Belsey
Cheryl is a highly motivated and dedicated worker, attention to detail is excellent and she always has a bright and cheery nature which helps motivate colleagues around her.

Fiona Barnard
Cheryl has excellent communication skills. In addition, she is extremely organized, reliable and computer literate. Cheryl can work independently and is able to follow through to ensure that the job gets done. She is flexible and willing to work on any project that is assigned to her. Cheryl was quick to volunteer to assist in other areas of company operations, as well.

Steve Belsey
Cheryl is a highly motivated and dedicated worker, attention to detail is excellent and she always has a bright and cheery nature which helps motivate colleagues around her.

Fiona Barnard
Cheryl has excellent communication skills. In addition, she is extremely organized, reliable and computer literate. Cheryl can work independently and is able to follow through to ensure that the job gets done. She is flexible and willing to work on any project that is assigned to her. Cheryl was quick to volunteer to assist in other areas of company operations, as well.

Steve Belsey
Cheryl is a highly motivated and dedicated worker, attention to detail is excellent and she always has a bright and cheery nature which helps motivate colleagues around her.

Experience
-
Ethical Food Company Ltd.
-
United Kingdom
-
Food and Beverage Retail
-
1 - 100 Employee
-
Product Manager
-
Jan 2018 - Present
-
-
-
-
Print Room and Calibration Supervisor
-
Jul 2003 - Present
Responsible for all activities and staff within the print room.Organising staff holiday, cover and sick cover.Responsible for ensuring that all staff working in the print room are fully trained to complete the job and, as the supervisor, ensure the support and advice is available as and when required.Setting up new products on the system for retailers and 3rd party customers on site, this requires extensive interaction with the latter.New label set up requires use and understanding of the main database using Vector data base / Data Guard and Clairsoft software. Additional equipment and programmes used include Axon Verifier for scanning barcodes, Stao and Tosihbas BXs5 and BXs6 printer. These are monitored, maintained through a servicing schedule organised by the supervisor.During all retailer visits and 3rd party audits including BRC and Tesco the position requires the labelling and printing function and control to be presented and explained to show full due diligence.As supervisor, all procedures and documentation in use needs to be regularly reviewed and updated accordingly. Any amendments will then be communicated to all staff and monitored to ensure compliance, Line Leaders documentation is checked daily for accuracy and refresher training given where discrepancies are found.As calibration supervisor, all equipment is registered, controlled and monitored for food safety compliance. Concise records are in place to show the controls and a servicing schedule ensures all equipment is fully functional and fit for purpose.All weighing equipment in monitored to ensure accuracy and all legal requirements are met.
-
-
Quality Controller
-
Aug 2011 - May 2013
Working in the BRC accredited packhouse responsible for customer quality, this included Tesco, Morrisons, Safeway, Sainsbury and Wholesale customers.Objectives were to ensure, through constant monitoring of the product lines, that the customer orders met the quality specification, this was achieved by inspecting the product and recording, documenting and reporting all non conformances, rejected product and quality issues raised during the inspections.This role required a level of support for the Line Leaders plus supervision and training for the packing staff to ensure the product met specification when despatched. Time restraints and vehicle slots often meant that rejection was seen as an inconvenience, in such situations confidence and ability to stand your ground on a decision was required.Class II monitoring to ensure the correct level of sorting by packers was achieved and to reduce unnecessary waste.
-
-
-
TRANSPAK DIRECT LIMITED
-
United Kingdom
-
Wholesale
-
1 - 100 Employee
-
Quality Manager
-
Sep 2017 - Jan 2018
-
-
-
ISS
-
Teynham, Kent, United Kingdom
-
Quality Assurance Supervisor
-
Jan 2015 - Aug 2017
-
-
-
-
Product Manager
-
Aug 2011 - Jun 2014
Currently based at Newma Fuits, as Product Manager, for Grapes and Top Fruit varities. Checking Fruit quality on intake, recording and documenting, defect levels to ensure pallets meet customer specifcation,Generating quality reports, taking photograpic evidence for the claims purposes, to asist the buyer. Allocating fruit for the packhouse to use for daily orders, Stock rotation. Advising the packhouse on the best use of the product for packing purposes.to maximise return on product.
-
-
Positive Quality Controller
-
Jul 2006 - Jul 2011
Based predominantly in the warehouse area, this role was the last quality and label check conducted before despatch.100% of pallets for various retailers and wholesalers were checked for quality, damage, labelling and any other issues before being despatched direct to the customer.This role required fast decisions on quality or any issues as prompt action on rejected and replacement product to ensure orders were met. Such decisions would be met with some objection from the despatch team, therefore confidence and ability to stand your ground was imperative.Due to the hours worked, health and safety and other compliance requirements were also monitored and reported back.
-
-
-
-
Senior Supervisor
-
Jan 2002 - Jan 2003
Coordinated and oversaw all line activities covering the supervisors for sick and holiday. Vast experience of running and managing citrus and punnet machinery from maintaining and operational issues through to ensure full productivity. Due to the nature of the business time restraints of vehicle slots resulted in pressure to have the customer orders completed to specification and to meet the despatch time. Coordinated and oversaw all line activities covering the supervisors for sick and holiday. Vast experience of running and managing citrus and punnet machinery from maintaining and operational issues through to ensure full productivity. Due to the nature of the business time restraints of vehicle slots resulted in pressure to have the customer orders completed to specification and to meet the despatch time.
-
-
-
-
Shift Manager
-
Nov 1999 - Nov 2002
Day to day running of the packhouse. Prioritizing customer orders. Attending and heading daily planning meetings to discuss production and arrange agency staff to cover the expected demands. Monitoring the team of supervisors on performance, setting them KPI's and following up on this. This position required good communications with all areas of the business including the sales teams through to the hygiene team and packers. Compiling, analysing and assessing the training needs of the operation.
-
-
Community
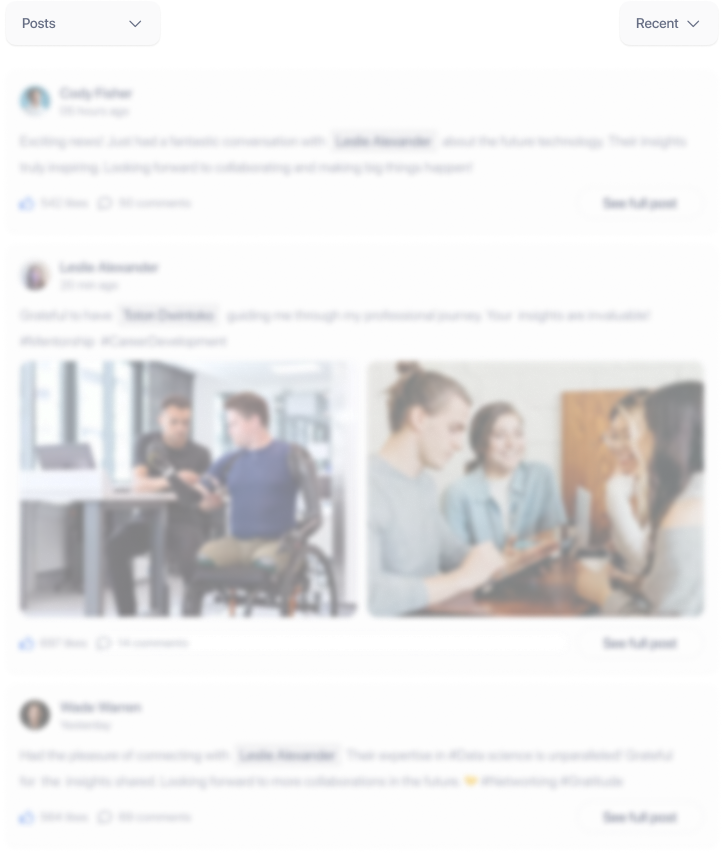