Cheryl Monique Coleman
Quality Manager at Dakkota Integrated Systems- Claim this Profile
Click to upgrade to our gold package
for the full feature experience.
Topline Score
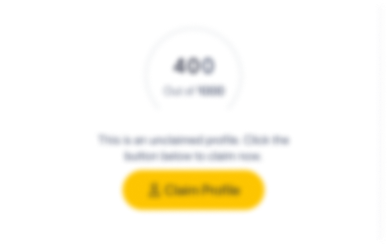
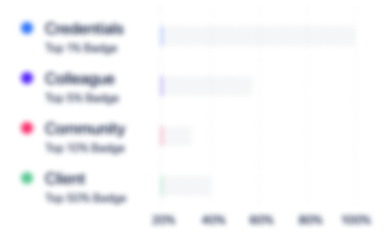
Bio


Credentials
-
Lean Six Sigma Green Belt Certification
International Standard for Lean Six Sigma (ISLSS)
Experience
-
Dakkota Integrated Systems
-
United States
-
Motor Vehicle Manufacturing
-
500 - 600 Employee
-
Quality Manager
-
Jun 2022 - Present
-
-
-
Holland, L.P.
-
United States
-
Railroad Equipment Manufacturing
-
200 - 300 Employee
-
Lean Manufacturing Production Manager/Facilities Manager
-
Oct 2017 - Jun 2022
Provide lean manufacturing and quality leadership to a team of 27 skilled and general personnel, including maintenance technicians; coordinate workflow and delegate responsibilities within high-volume production environments across two ISO 9001 certified facilities. Accountable for project scheduling, facilities maintenance and staff training to meet goals for production volume, quality, reliability, safety, compliance and profitability. Member of the Diversity Advisory Council and Supplier Quality Council. * Lead Gemba walks with quality, engineering and other support groups to ensure safety, quality, lean manufacturing and maintenance revisions are made to facilitate value-driven work settings. * Apply six sigma methodology to plan and coordinate data-driven quality and efficiency enhancements across all production phases and facility maintenance programs. * Partner with engineering and production leads to drive continuous improvement in processes, cycle times, tool life, product flow and safety via engineering change requests. Highlights: > Achieved the company’s highest performance rating (100% scores) for leading and lagging indicators across safety, quality, cost control and customer satisfaction. > Created and launched the updated Quality Operating System, leveraging six sigma strategies to successfully earn the TDX award, AAR certification and ISO 9001 certification. > Established a strategic lean manufacturing program that yielded a 250% increase to gross revenue, far ahead of all goals and projections. > Instituted safety training and best practices that achieved two consecutive years of accident-free performance. > Led multiple capital improvements and major projects, including reconfiguring the shop floor to assimilate the Virginia plant’s HoTT division into the University Park facility. Show less
-
-
-
Advertising Resources, Inc.
-
Alsip, Illinois, United States
-
Operations Manager
-
Nov 2014 - Oct 2017
Full P&L accountability for labor usage, order fulfillment, inventory management, contract administration, account services, plant safety and other KPIs at this CPG warehouse/distribution center. Directed all plant operations to meet goals for production, sanitation, compliance (OSHA, GMPs, etc.) and profitability. * Oversaw performance management, scheduling, training and labor contract administration for a 170-person team; subcontracted outside agencies to supplement pickers, forklift drivers and other staff. * Planned and implemented annual physical and account-specific inventories, along with daily cycle counts with system-generated schedules and random location inventories. * Monitored performance of transportation carriers to ensure adherence to service level agreements; administered annual budgets for material handling, maintenance, supplies and vendor services. * Investigated and resolved problems with inventory discrepancies, shipment tracking irregularities, personnel conflicts, billing rates, budget deviations, labor usage and other persistent issues. Highlights: > Successfully identified and resolved key cost inefficiencies and quality deviations by implementing process improvements via lean methodology. Show less
-
-
-
Anixter
-
United States
-
Wholesale
-
700 & Above Employee
-
General Manager
-
Mar 2007 - Nov 2009
Oversaw the development and implementation of operational controls, process mapping, gap analysis, policies and best practices for a 200,000 sq. ft. Illinois warehouse and 100,000 sq. ft. Tennessee warehouse, both ISO 9000 certified facilities. Accountable for safety, inventory, labor, cycle and cost controls, along with client service delivery for Anixter’s largest accounts (including a major $35 million client). * Analyzed area-wide efficiency, load analysis, delivery cycle, quality (loss/damage and invoice accuracy), safety and other metrics to plan short-term and long-range operations. * Strategized with senior management and participated in various committees to drive performance and processes; developed performance incentives to motivate managers and team members. * Oversaw the development of staffing plans, maintenance schedules and other resource utilization to ensure a profitable bottom line without sacrificing quality of service. Highlights: > Consolidated two shifts into a single shift while increasing productivity (representing cost savings and profit growth) by implementing lean six sigma methodologies. > Led the successful completion of a ISO 9000 audit and TL 9000 audit, as well as a comprehensive inventory audit with 95% accuracy. > Developed and implemented new best practices and procedures that achieved a 50% reduction of plantwide utility spending while boosting productivity within six months. Show less
-
-
-
Ford Motor Company
-
United States
-
Motor Vehicle Manufacturing
-
700 & Above Employee
-
Superintendent Manager
-
Sep 1993 - Apr 2007
Advanced through a series of progressively responsible production, quality and operations management positions at this Fortune 50 auto manufacturing company, including production supervisor, industrial engineer, general foreman, paint area superintendent, quality control manager, final area superintendent, incoming quality manager and superintendent manager. Managed all plans for production scheduling, budget management and staff development while developing performance and quality improvements. * Oversaw and directed hundreds of union operators, engineers, supervisors and other staff to maintain maximum levels of production and quality within multiple manufacturing departments. * Determined required resources, planned and scheduled workloads, developed and monitored schedules, and directed all production operations through plant supervisors and daily shift meetings. * Facilitated ongoing staff training, tracking and improvement of all performance objectives encompassing safety, quality, customer service, waste reduction and efficiency. * Coordinated lean six sigma programs to reduce production waste and associated costs; also implemented ISO 9001 quality and sustainability standards and led the Sarbanes-Oxley audit. * Managed 278 suppliers and enforced both internal (plantwide) and external compliance to Ford’s quality operating system and quality improvement objectives. Highlights: > Achieved $1.9 million in single-year revenue, setting the highest benchmark in the company; recipient of numerous performance awards over 13+ years, including two J.D. Power Awards. > Spearheaded the launch of new production lines for the Ford 500, Ford Freestyle and Mercury Montego vehicles, exceeding the launch curve by six months. > Developed and implemented action plans that improved production 57%, reduced scrap 100% and achieved major reductions in lost time accidents and other safety incidents. > Successfully obtained ISO 9000 and ISO 9001 certifications for the plant. Show less
-
-
Education
-
St. Ambrose University
Bachelor of Science - BS, Industrial Engineering
Community
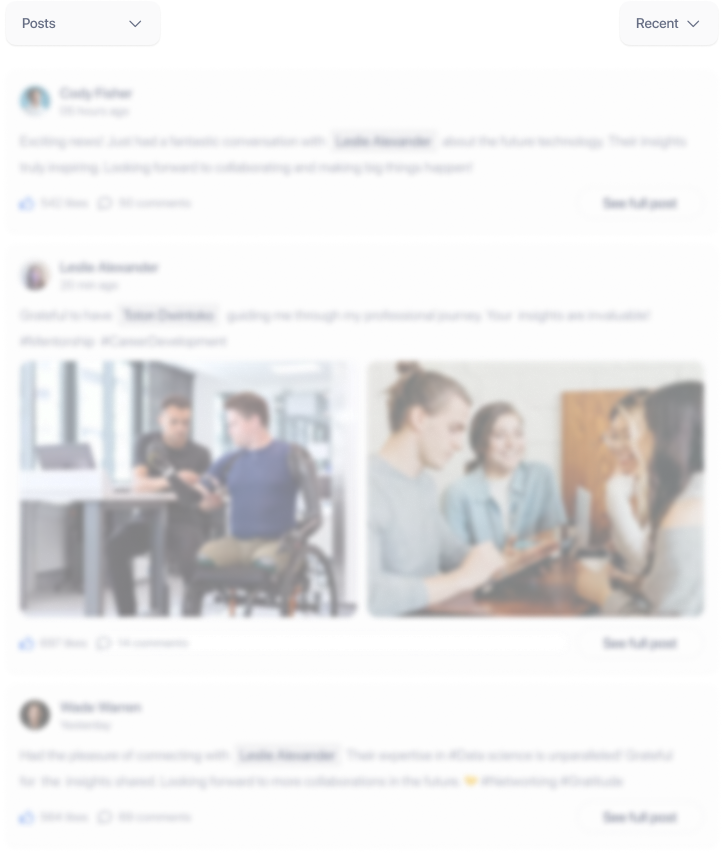