Cher Block
Quality System Manager at DCW Casing LLC- Claim this Profile
Click to upgrade to our gold package
for the full feature experience.
Topline Score
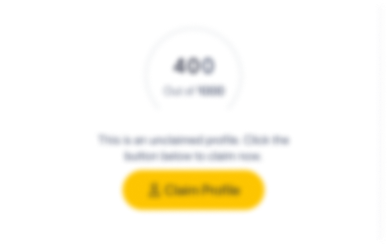
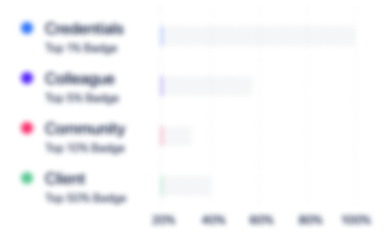
Bio
0
/5.0 / Based on 0 ratingsFilter reviews by:
Experience
-
DCW Casing LLC
-
United States
-
Facilities Services
-
1 - 100 Employee
-
Quality System Manager
-
Feb 2018 - Present
-
-
-
NantPharma
-
United States
-
Pharmaceutical Manufacturing
-
1 - 100 Employee
-
Quality Systems Manager
-
Feb 2015 - Feb 2018
Oversee all aspects of the quality system including but not limited to document change control, process change control, in-process and final product release testing, calibrations, customer and regulatory audits, and quality related investigations (i.e. deviations, customer complaints, out of specification investigations).
-
-
Quality Manager
-
Mar 2009 - Feb 2018
-
-
Operations Manager
-
Feb 2009 - Feb 2015
Responsible for managing production team and delegating production tasks. As a new start up facility I was actively involved in all aspects of the manufacturing process which included learning and understanding the process as well as developing and writing standard operating procedures for all manufacturing positions and training employees. Additional responsibilities included managing PTO, payroll, purchasing, interviewing and hiring, managing the safety program, and ensuring good documentation and good manufacturing practices are followed to ensure the high quality product is being produced.
-
-
-
Tyson Fresh Meats Team
-
Food Production
-
1 - 100 Employee
-
Operations Supervisor
-
Feb 2008 - Feb 2009
Production Supervisor Responsible for delegating daily responsibilities to individuals to meet departmental needs.Responsible for supervising 20-40 production team members. Responsible for developing a working relationship with the UDSA and ensuring employees follow USDA requirements. Responsible for conducting quality audits and working with the quality department to ensure high quality standards are maintained. Conduct daily safety audits to ensure a safe work environment. Responsible for setting departmental goals and achieving them. Monitor team members work performance and ensure all company policies and procedures are being followed. Prepare daily reports. Issued disciplines and corrective actions when needed. Schedule vacations and prepare daily payroll.
-
-
Employment/Human Resources Admin
-
Feb 2004 - Feb 2008
Process applications and prepare all new hire paperwork including I-9’s, W-4, and 8850 work credit forms. Work with Iowa Workforce to post job openings. Prepare, post, and track all internal job postings.Review all internal interview questionnaires and Affirmative Action Plan sheets to ensure compliance.Conduct weekly and monthly audits on I-9’s and tear sheets to ensure compliance. Prepare all promotional management and management support paperwork. Schedule interviews, health assessments and other needed appointments. Prepare weekly staffing reports, referral bonus checks, orientation roster, internal movement tracking, and submitting Basic Pilot Verification information to verify work authorization. Data entry, filing and other general office duties.
-
-
Operation, Offline Safety and Ergonomic Monitor
-
Feb 1997 - Feb 2004
Performed a over 20 different jobs throughout production. Safety Representative responsible for orientating new team members to the production floor, submitting and following up on work orders, conducting equipment checks and safety walks on regular basis, communicating concerns with upper management, addressing and assisting team members with safety concerns, involved in accident and injury investigations, implemented, tracked, and updated corrective action checklist program, involved with ensuring MSDS books were up to date and in compliance with company policy, attended weekly and monthly safety meetings, assisted in creating and updating several safety sign off’s. Monitored and tracked the safety measurement scores, filled in for safety clerk due to vacation or personal time off. Ergonomic committee member responsible for attending monthly meetings, conducting job studies, completing monthly HAV’s questionnaires, annual vibration testing, evaluated jobs and interacted with the team members performing the jobs to reduce stressors and develop better techniques to perform their jobs. Recognized by management as a reliable team member. Assist where ever needed.
-
-
Community
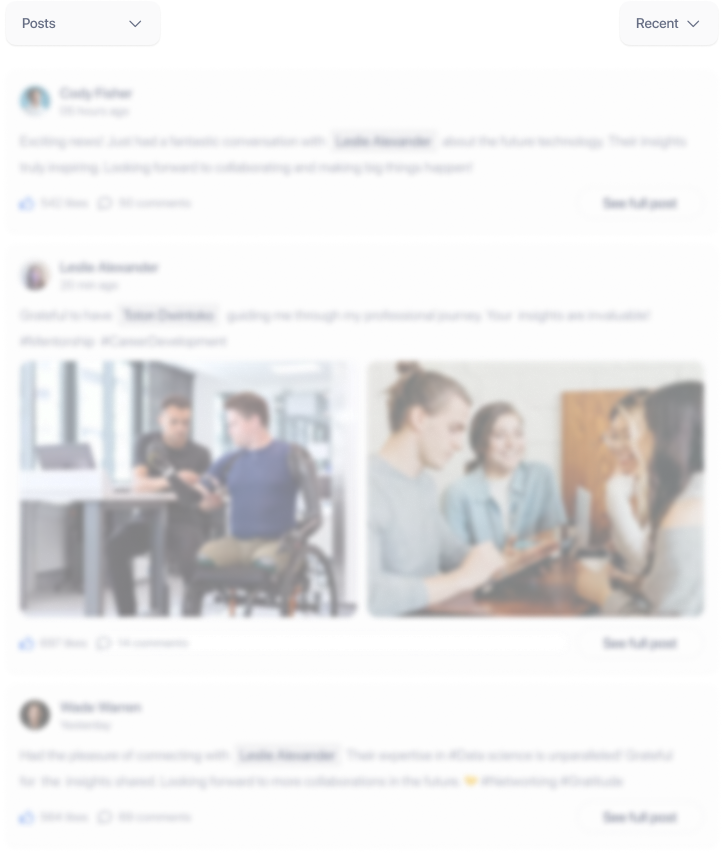