Chelan Burks-Andrews, MAcc, MSA
Budget and Human Resource Director for the Bureau of Local Government and School Services at Michigan Department of Treasury- Claim this Profile
Click to upgrade to our gold package
for the full feature experience.
Topline Score
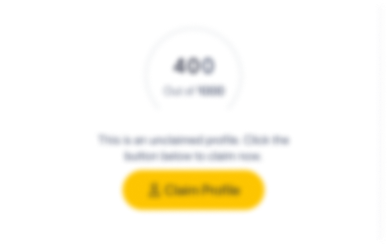
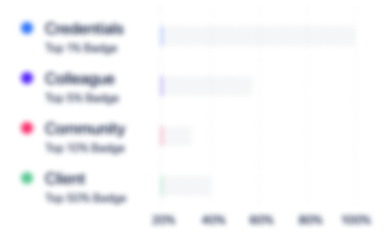
Bio


Experience
-
Michigan Department of Treasury
-
United States
-
Government Administration
-
100 - 200 Employee
-
Budget and Human Resource Director for the Bureau of Local Government and School Services
-
Apr 2021 - Present
-
-
Financial Specialist for the Detroit Financial Review Commission
-
Feb 2018 - Apr 2021
Executive Director and specialist for the Commission with sole responsibility and financial overview for the oversight of the Detroit Public Schools Community District.
-
-
-
Plante Moran
-
United States
-
Accounting
-
700 & Above Employee
-
Senior Assurance Staff
-
Jan 2015 - Feb 2018
Senior Auditor specialized in conducting financial statement audits, federal fund audits and 401k employee benefit plan audits for K-12 school districts/ academies, not for profits, manufacturing companies and financial institutions. Senior Auditor specialized in conducting financial statement audits, federal fund audits and 401k employee benefit plan audits for K-12 school districts/ academies, not for profits, manufacturing companies and financial institutions.
-
-
-
-
Accounting/ Finance Administrator
-
Jan 2009 - Jan 2018
Oversight of all financial transactions; reconciled bank accounts, prepared monthly journal entries, analyzed general ledger accounts, prepared quarterly and annual budgets and financial statements as required for lenders and internal purposes. Oversight of all financial transactions; reconciled bank accounts, prepared monthly journal entries, analyzed general ledger accounts, prepared quarterly and annual budgets and financial statements as required for lenders and internal purposes.
-
-
-
FCA Fiat Chrysler Automobiles
-
United Kingdom
-
Motor Vehicle Manufacturing
-
700 & Above Employee
-
Cost / Inventory Accountant
-
Jun 2014 - Jan 2015
Utilized FCA Mainframe (CHAMPS, ASCM, REGIONS) and SAP systems to research and resolve issues in error tables and variance account(s) that included quantity, standard costs, and unit of measure discrepancies. Prepared inventory reconciliations for 7 U.S., 2 Canadian and 3 Mexico plants as needed. Ensured SOX compliance for Manufacturing Group Assembly department by generating reports via Lotus Notes & Penta SAP of monthly transactions for Corporate Office, Accounting Management, and… Show more Utilized FCA Mainframe (CHAMPS, ASCM, REGIONS) and SAP systems to research and resolve issues in error tables and variance account(s) that included quantity, standard costs, and unit of measure discrepancies. Prepared inventory reconciliations for 7 U.S., 2 Canadian and 3 Mexico plants as needed. Ensured SOX compliance for Manufacturing Group Assembly department by generating reports via Lotus Notes & Penta SAP of monthly transactions for Corporate Office, Accounting Management, and Auditors’ review. Created massive journal entries via ART&MIS for management to review and approve for posting and performed monthly closing activities such as clearing suspense accounts, accruals, etc. Show less Utilized FCA Mainframe (CHAMPS, ASCM, REGIONS) and SAP systems to research and resolve issues in error tables and variance account(s) that included quantity, standard costs, and unit of measure discrepancies. Prepared inventory reconciliations for 7 U.S., 2 Canadian and 3 Mexico plants as needed. Ensured SOX compliance for Manufacturing Group Assembly department by generating reports via Lotus Notes & Penta SAP of monthly transactions for Corporate Office, Accounting Management, and… Show more Utilized FCA Mainframe (CHAMPS, ASCM, REGIONS) and SAP systems to research and resolve issues in error tables and variance account(s) that included quantity, standard costs, and unit of measure discrepancies. Prepared inventory reconciliations for 7 U.S., 2 Canadian and 3 Mexico plants as needed. Ensured SOX compliance for Manufacturing Group Assembly department by generating reports via Lotus Notes & Penta SAP of monthly transactions for Corporate Office, Accounting Management, and Auditors’ review. Created massive journal entries via ART&MIS for management to review and approve for posting and performed monthly closing activities such as clearing suspense accounts, accruals, etc. Show less
-
-
-
Plante Moran
-
United States
-
Accounting
-
700 & Above Employee
-
Assurance Intern
-
Jan 2014 - Apr 2014
Performed financial statement audits, compilations and reviews that assess the validity and reliability of financial information. Assessed system's internal controls and prepared tax returns including: individual, trust, corporate, partnership, and not-for-profit. Performed financial statement audits, compilations and reviews that assess the validity and reliability of financial information. Assessed system's internal controls and prepared tax returns including: individual, trust, corporate, partnership, and not-for-profit.
-
-
-
Mercedes-Benz Research and Development India
-
India
-
Motor Vehicle Manufacturing
-
700 & Above Employee
-
Division Controller Intern
-
Sep 2012 - Jan 2013
Approved purchase authorizations for R& D projects in excess of $1,000,000 and controlled costs by ensuring funds were allocated appropriately within the scope of the project (project management & controlling). Worked extensively in SAP tracking fund commitments against purchase requisitions, created invoices, tracked purchase orders and prepared year-end closing accruals on open purchase orders. Created ad hoc reports, presentations and spreadsheets for quarterly billing review and financial… Show more Approved purchase authorizations for R& D projects in excess of $1,000,000 and controlled costs by ensuring funds were allocated appropriately within the scope of the project (project management & controlling). Worked extensively in SAP tracking fund commitments against purchase requisitions, created invoices, tracked purchase orders and prepared year-end closing accruals on open purchase orders. Created ad hoc reports, presentations and spreadsheets for quarterly billing review and financial planning meetings with senior managers. Managed 2013 Capital Budget by tracking requests and expenditures in an effort to control approved budget for R&D projects, budget reduced from $2,350,000 to $1,720,000. Managed AUC Capital Assets, placing assets into service monthly and recording quarterly depreciation expense and prepared inter-company wire transfers to Detroit Diesel for equipment and rental expenses. Show less Approved purchase authorizations for R& D projects in excess of $1,000,000 and controlled costs by ensuring funds were allocated appropriately within the scope of the project (project management & controlling). Worked extensively in SAP tracking fund commitments against purchase requisitions, created invoices, tracked purchase orders and prepared year-end closing accruals on open purchase orders. Created ad hoc reports, presentations and spreadsheets for quarterly billing review and financial… Show more Approved purchase authorizations for R& D projects in excess of $1,000,000 and controlled costs by ensuring funds were allocated appropriately within the scope of the project (project management & controlling). Worked extensively in SAP tracking fund commitments against purchase requisitions, created invoices, tracked purchase orders and prepared year-end closing accruals on open purchase orders. Created ad hoc reports, presentations and spreadsheets for quarterly billing review and financial planning meetings with senior managers. Managed 2013 Capital Budget by tracking requests and expenditures in an effort to control approved budget for R&D projects, budget reduced from $2,350,000 to $1,720,000. Managed AUC Capital Assets, placing assets into service monthly and recording quarterly depreciation expense and prepared inter-company wire transfers to Detroit Diesel for equipment and rental expenses. Show less
-
-
-
-
Group Leader/ Production Supervisor
-
Oct 1994 - Dec 2008
Supervised production and maintenance operators, 30 machine operators and 5 sub assembly operators, performed process audits and planned production schedules, managed $500,000 department budgets and costs in such areas as labor, tooling, scrap reduction and overtime. Trained, coached and developed team leaders in improving machine cycle time, improving equipment effectiveness, team building, problem solving and business fundamentals. Conducted weekly presentations to upper level management… Show more Supervised production and maintenance operators, 30 machine operators and 5 sub assembly operators, performed process audits and planned production schedules, managed $500,000 department budgets and costs in such areas as labor, tooling, scrap reduction and overtime. Trained, coached and developed team leaders in improving machine cycle time, improving equipment effectiveness, team building, problem solving and business fundamentals. Conducted weekly presentations to upper level management regarding various process improvements, cost initiatives, smart manufacturing updates, department budgets, quality initiatives and scorecard reviews. Recognized for quality improvement initiative that generated a significant cost saving per year and selected to pilot and implement team based manufacturing (lean) in the machining departments throughout the facility. Show less Supervised production and maintenance operators, 30 machine operators and 5 sub assembly operators, performed process audits and planned production schedules, managed $500,000 department budgets and costs in such areas as labor, tooling, scrap reduction and overtime. Trained, coached and developed team leaders in improving machine cycle time, improving equipment effectiveness, team building, problem solving and business fundamentals. Conducted weekly presentations to upper level management… Show more Supervised production and maintenance operators, 30 machine operators and 5 sub assembly operators, performed process audits and planned production schedules, managed $500,000 department budgets and costs in such areas as labor, tooling, scrap reduction and overtime. Trained, coached and developed team leaders in improving machine cycle time, improving equipment effectiveness, team building, problem solving and business fundamentals. Conducted weekly presentations to upper level management regarding various process improvements, cost initiatives, smart manufacturing updates, department budgets, quality initiatives and scorecard reviews. Recognized for quality improvement initiative that generated a significant cost saving per year and selected to pilot and implement team based manufacturing (lean) in the machining departments throughout the facility. Show less
-
-
Education
-
Oakland University
Master's Degree, Accounting -
Central Michigan University
Master's degree, Business Administration/ Human Resource Administration
Community
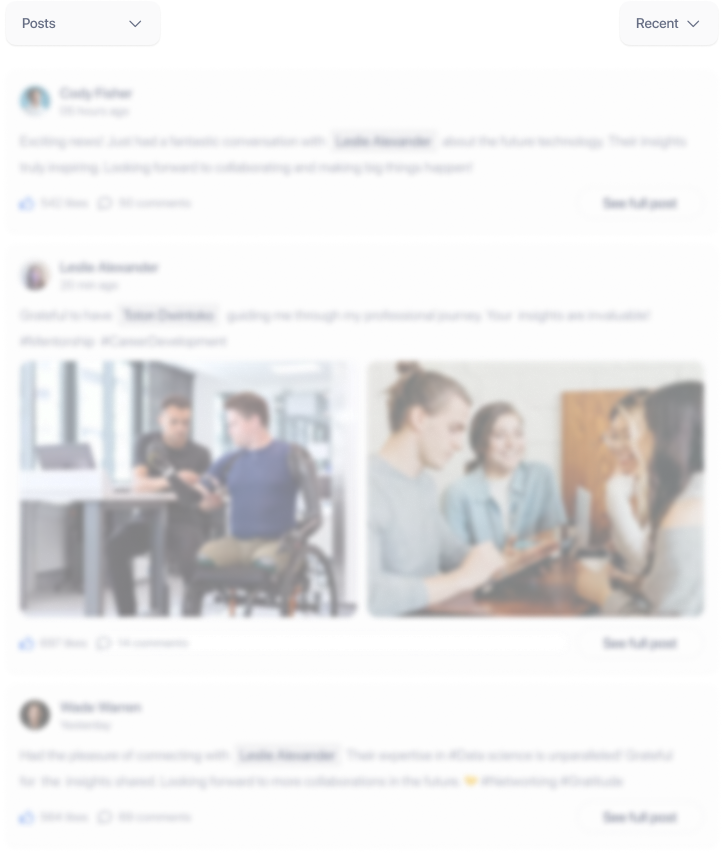