Charles Sherrod Jr.
Field Superintendant at Jindal Pipe USA, Inc.- Claim this Profile
Click to upgrade to our gold package
for the full feature experience.
Topline Score
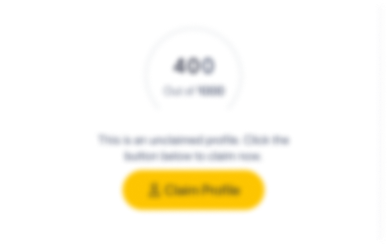
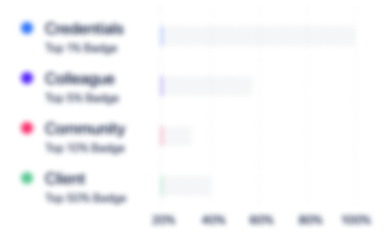
Bio
0
/5.0 / Based on 0 ratingsFilter reviews by:
Experience
-
Jindal Pipe USA, Inc.
-
United States
-
Manufacturing
-
1 - 100 Employee
-
Field Superintendant
-
Feb 2023 - Present
-
-
-
Terry Adams Inc
-
United States
-
Construction
-
1 - 100 Employee
-
Project Superintendent
-
Jan 2022 - Present
Liaiseda between field engineers and trade workers align construction projects with drawings and specifications • Supervised layout, assembly and installation of various sizes and types of drainage pipes • Used Microsoft Word and Excel along with other software tools to create documents and other communications • Assembled and secured pipes, tubes, fittings and related equipment according to project specifications • Reviewed and approved employee time reporting • Utilized equipment to excavate, install and backfill drainage pipes • Conducted critical pre-installation conferences with general contractors, subcontractors, consultants and manufacturer's representatives • Inspected all ship components and mechanisms for compliance with safety, operability and regulatory standards • Monitored inventory, budgeted supply use and ordered supplies to keep ship sufficiently stocked • Used welding equipment to fabricate, cut and bend metal components to be installed in ship • Reviewed and validated quality requirements for manufacturing planning, supplier purchase orders and engineering specifications to meet contract compliance regulations • Reviewing technical vessel design and construction plans of domestic vessels • Assisted drafters in developing structural design of products using drafting tools or computer-assisted design (CAD) or drafting equipment and software. • Verified construction documentation to meet client requirements and vision. • Completed accurate engineering calculations for weights, loads and other metrics using both manual and digital methods. • Helped prepare project budgets, maintain schedules and put together final documentation. • Created designs for temporary structures such as shores, vertical transportation solutions, employee access solutions and more. • Oversaw proposal and bidding phases of construction Show less
-
-
-
-
Project Superintendent
-
Nov 2018 - Aug 2021
Liaiseda between field engineers and trade workers align construction projects with drawings and specifications • Supervised layout, assembly and installation of various sizes and types of drainage pipes • Used Microsoft Word and Excel along with other software tools to create documents and other communications • Assembled and secured pipes, tubes, fittings and related equipment according to project specifications • Reviewed and approved employee time reporting • Utilized equipment to excavate, install and backfill drainage pipes • Conducted critical pre-installation conferences with general contractors, subcontractors, consultants and manufacturer's representatives • Inspected all ship components and mechanisms for compliance with safety, operability and regulatory standards • Monitored inventory, budgeted supply use and ordered supplies to keep ship sufficiently stocked • Used welding equipment to fabricate, cut and bend metal components to be installed in ship • Reviewed and validated quality requirements for manufacturing planning, supplier purchase orders and engineering specifications to meet contract compliance regulations • Reviewing technical vessel design and construction plans of domestic vessels • Assisted drafters in developing structural design of products using drafting tools or computer-assisted design (CAD) or drafting equipment and software. • Verified construction documentation to meet client requirements and vision. • Completed accurate engineering calculations for weights, loads and other metrics using both manual and digital methods. • Helped prepare project budgets, maintain schedules and put together final documentation. • Created designs for temporary structures such as shores, vertical transportation solutions, employee access solutions and more. • Oversaw proposal and bidding phases of construction Show less
-
-
-
Florida Department of Corrections
-
United States
-
Law Enforcement
-
700 & Above Employee
-
Project Superintendent/ Vocational Instructor
-
Mar 2016 - Oct 2018
Computer skills (Word, Excel,PowerPoint, etc.) Carbon steel (SA 53, SA 333), stainless steel (316 L and SS 304L) copper nickel piping (Distribution and Fusion of lines for tie-ins) Pipe Fitting, Boiler-making, Iron and Structural, Civil Construction QA/QC under the guidelines of API 1104, D1.1, B31.3, API SPEC Q1, ASME Codes Electrical layouts, Blueprints, Building codes BlueCielo, AutoCAD, Microsoft Excel and Word, Weld mapping and Fabrication Drawings Walk down prints and packages with P&ID reroute, demolition and new construction Redline, sketch, and details that include new dimensions, materials, and layouts Operate ground vehicles- Man lift, scissor lift, and forklift Replace, move, assemble, install or dismantle machinery Tool maintenance, assembly, repair, and proper stocking of items Manipulate rigging lines, hoists, and pulling gear to move or support materials according to weights and sizes Coordinate all site inspections with the site subcontractors Supervising multiple workers and crafts Inspection of repairs on bearing structures, wharfs, concrete and steel structures, tanks Cutting, threading, bolting up piping for water and chemical systems Structural piping/Skid fabrication/pump installation/pier and bridge repair Scheduling and planning various crews for any and all crafts Ensure all work is correctly prepared prior to any inspection being undertaken Show less
-
-
-
Chicago Bridge & Iron - Power
-
United States
-
Oil and Gas
-
1 - 100 Employee
-
Satellite Superintendent/ Field Supervisor
-
Aug 2014 - Feb 2016
• Set and managed budgets for capital, expense and cost improvement activities and defined and developed project specifications. • Balanced project priority and business demand and aligned resources to accomplish assignments, projects and continuous improvements. • Coordinated activities with other units of organizations to develop cross-functional strategic plans to enhance company performance. • Verified product and equipment design, specifications and processes to reduce costs while maintaining product quality and employee safety. • Developed positive working relationships with stakeholders to effectively coordinate work activities. • Coordinated sampling and analysis tasks to verify quality of finished products. • Reviewed technical drawings developed by CAD technicians and drafters. • Routed and integrated technical and electrical components for projects. • Prepared action plans for problematic processes and assets. • Conducted feasibility studies for proposed projects using potential ROI and risk management. • Developed cost estimates and project specifications for proposals. • Assessed current usage and future needs to determine expansion plans. • Created professional development plan to cultivate and advance skillsets of all employees. • Managed complete construction process to maximize quality, cost-controls and efficiency. • Set up and operated shielded metal arc and gas metal arc welding equipment. • Assembled structural forms such as boiler parts and pressure vessels. • Welded in flat, horizontal, vertical and overhead positions. Show less
-
-
-
H&S Constructors Inc.
-
United States
-
Construction
-
1 - 100 Employee
-
Quality Control Supervisor/ Field Technician
-
Sep 2012 - Jul 2014
• Reviewed and validated quality requirements for manufacturing planning, supplier purchase orders and engineering specifications to meet contract compliance regulations. • Utilized calibration software to detect and adjust variances in customer-facing products within prescribed tolerances. • Inspected raw materials and finished products to verify quality and disposed items that did not meet safety requirements. • Performed quality control audits on pre-production supply chain, verifying continuity of raw materials. • Developed and audited practices, programs and reporting system metrics for optimal efficiency. • Designed and performed product audits to verify quality control parameters were maintained across multiple production runs. • Adhered to federal guidelines for quality control inspection. • Directed technical and administrative staff involved in quality control tasks. • Integrated diagnostic automation to accelerate and sharpen post-production testing. • Supported quality team members during corrective action updates. • Executed operational audits and assessed company operations, compliance and other associated risks. • Escalated concerns about project and process quality, referring discovered issues to engineering manager for correction. • Reported on non-compliance issues and other negative factors discovered during production. • Inspected grounds, equipment and overall building to uphold safe and aesthetically pleasing standard. • Supervised facility crew and general maintenance schedules. • Reviewed and oversaw construction and renovation projects. • Reviewed drawings and code specifications to determine appropriate layouts for wiring installations in building automation systems. • Generated process models illustrating automation engineering progress, specifications and details. • Determined layouts for wiring installations in building automation systems through correct interpretation of drawing, diagrams and code specifications. Show less
-
-
-
J. M. Davidson, Inc.
-
United States
-
Construction
-
1 - 100 Employee
-
Quality Control Technician/ Field Manager
-
Oct 2011 - Aug 2012
• Streamlined QA processes by working closely with development teams and staying abreast of changing product demands. • Communicated with production team members about quality issues. • Completed precise measurements using special tools. • Created and deployed best practices to improve efficiency and reduce defects. • Monitored production processes to gain understanding of problematic steps and rectify issues. • Performed visual inspections and non-destructive tests where appropriate. • Used analyzers, multimeters and power supplies to conduct diagnostic procedures. • Evaluated components and final products against quality standards and manufacturing specifications. • Determined layouts to install wiring in automated systems based on drawings and code specifications. • Generated process models illustrating automation engineering progress, specifications and details. • Supported business needs dependent on location, working with staff at all levels to produce targeted solutions. • Tested, automated and whitelisted software to be used in secure environments. • Built sustainable procedures, defect plans and risk assessment systems with engineers and consultants. • Reviewed plans and inspected ongoing construction to keep work in line with project goals. • Designed courses to meet company requirements and help develop new leaders within organizational structure. • Evaluated employee performance and coached and trained to improve weak areas. • Delegated high volumes of work to empower team, build trust and assist with professional development. • Oversaw employee attendance record, handled payroll and ordered new materials for sites. • Handled issues with relative ease by implementing best practices and applying critical thinking skills to find best solutions. Show less
-
-
-
KELLOG BROWN & ROOT LLC
-
United States
-
1 - 100 Employee
-
Field Operations Supervisor
-
Jul 2010 - Jul 2011
• Liaised between field engineers and trade workers align construction projects with drawings and specifications • Supervised crews up to 250 to 500. Layout, assembly and installation of various sizes and types of drainage pipes • Used Microsoft Word and Excel along with other software tools to create documents and other communications • Assembled and secured pipes, tubes, fittings and related equipment according to project specifications • Assisted drafters in developing structural design of products using drafting tools or computer-assisted design (CAD) or drafting equipment and software • Reviewed and validated quality requirements for manufacturing planning, supplier purchase orders and engineering specifications to meet contract compliance regulations • Reviewing technical vessel design and construction plans of domestic vessels • Assisted drafters in developing structural design of products using drafting tools or computer-assisted design (CAD) or drafting equipment and software. • Completed accurate engineering calculations for weights, loads and other metrics using both manual and digital methods. • Created designs for temporary structures such as shores, vertical transportation solutions, employee access solutions and more. • Oversaw proposal and bidding phases of construction. • Coordinated paperwork and inspections required for each type of building to keep workflows running smoothly and to avoid backlog. • Supervised field crews to maximize quality and work efficiency. • Completed paperwork, recognizing discrepancies and promptly addressing for resolution. • Troubleshot, fixed and improved electrical controls. • Set up and operated shielded metal arc and gas metal arc welding equipment Show less
-
-
-
Quell Industrial Services LLC.
-
Construction
-
1 - 100 Employee
-
Construction Superintendent
-
May 2009 - Jul 2010
• Asserted control over material usage and contractor man-hours to keep projects in line with budgetary restrictions • Reviewing technical vessel design and construction plans of domestic vessels • Preparing briefing papers, technical analyses, and option evaluations • Training and assessing inspection qualifications and formally certifying completed portions of on job training for assigned civilian and military Marine Inspectors • Delegated assignments based on plans, project needs and knowledge of individual team members • Scheduled 250 subcontractors, consultants and vendors to coordinate completion of jobs and tasks • Computer skills (Microsoft Word, Excel, Teams • Monitored inventory, budgeted supply use and ordered supplies to keep ship sufficiently stocked • Completed frequent inspections, identified concerns and corrected problems independently. • Performed routine equipment inspections and maintained and completed corrective actions by referring to workbooks and technical publications to determine specifications. • Recorded inspection and maintenance actions using log books, computer terminals and other technical applications. • Monitored parts department and placed orders for maintenance supplies on consistent basis. • Hired, monitored and motivated subcontractors to keep to tight schedules and budgetary requirements. • Reworked positions and workflow based on individual abilities and production targets. • Created specific finishes on poured concrete. Show less
-
-
Education
-
Auburn University
Associates, Computer Science
Community
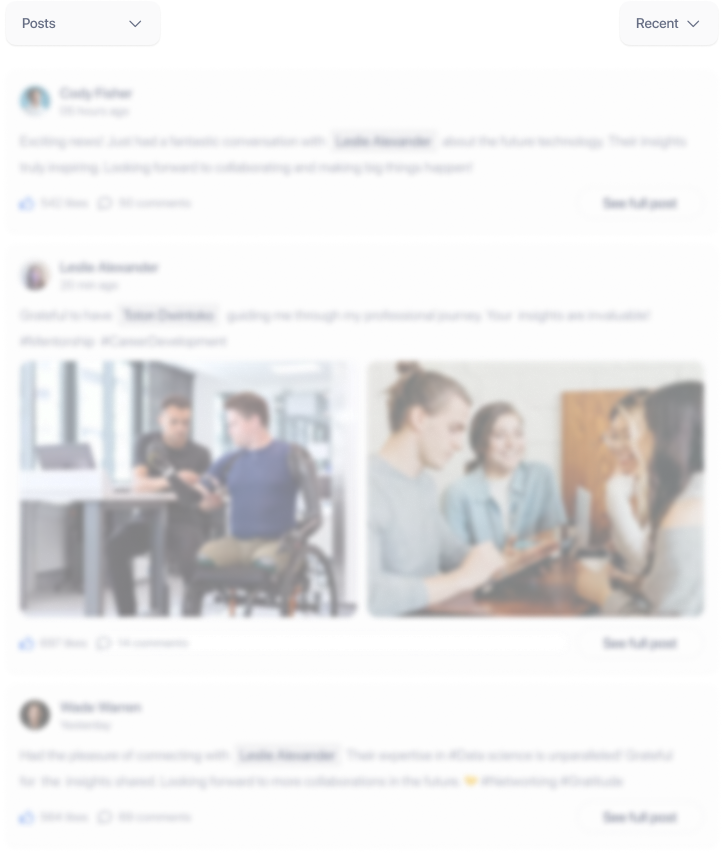