Charles Reed, PE
Process Discipline Manager at Century 3, Inc.- Claim this Profile
Click to upgrade to our gold package
for the full feature experience.
Topline Score
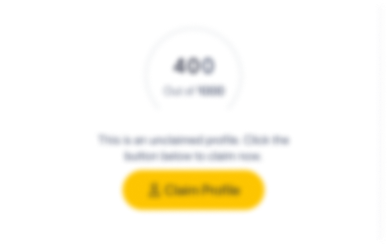
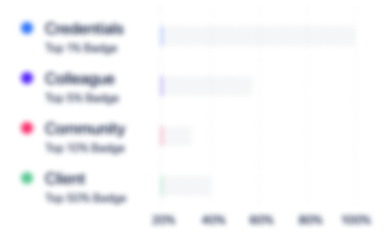
Bio


Credentials
-
Six-Sigma DMAIC Green Belt
Corning Incorporated
Experience
-
Century 3, Inc.
-
United States
-
Construction
-
100 - 200 Employee
-
Process Discipline Manager
-
Dec 2021 - Present
-
-
-
Renewal Consulting, LLC
-
Greenville, South Carolina, United States
-
Senior Manufacturing Consultant
-
Oct 2020 - Dec 2021
• Coaching executives, plant managers, and their teams for performance and scheduling improvements. • Interim plant manager and supply chain director in a GMP environment. • Certifying authority in Lean disciplines for plant leaders at 3 sites with a major confectioner. Led CI workshops across a wide range of functions and salary grades. • Authored proposal document and C-suite presentation for a renewable fuels company’s negotiations with a Fortune 125 power company. • Performed techno-economic modeling for the conversion of biomass to syngas intermediates and downstream fuels with proprietary technology. This included equipment sizing and linking process variables to financial performance. • Contract safety manager for a Tier 2 automotive supplier. Show less
-
-
-
Ingevity
-
United States
-
Chemical Manufacturing
-
700 & Above Employee
-
Process Engineer
-
Oct 2018 - Aug 2020
• Analyzed performance of the plant emissions system, then led a $750K capital project through the labor-intensive replacement of ceramic media. Results included improved thermal efficiencies and the ability to sustain higher production rates. • Startup and commissioning team member for the new Sawdust Dryer, a multimillion dollar capital project that enabled higher product throughput. Performed equipment checks and troubleshooting, and trained hourly staff on new SOPs. • Led root cause analysis of Extruder plant Strength performance, which uncovered dryer temperature setpoint as the process variable driving Strength. Implemented a new dryer setpoint and product yield increased 10%. • SME for self-heating carbon. Worked with the corporate technical team and production engineers to design, run, and document multiple plant trials. Applied findings to process setpoints for reduced risk in final product shipping. Show less
-
-
-
Daikin Applied Americas
-
United States
-
Industrial Machinery Manufacturing
-
700 & Above Employee
-
Manufacturing Engineer
-
Apr 2016 - Aug 2018
• Guided the AHT line to record performance in the 2017 peak season with inputs to staffing and planning. Weekly unit production went from 10 to 18. Organized and led a recognition event for shop floor workers. • Self-initiated experiment with Lean principles proved opportunities for a 60% reduction in the lead time of medium-ton chillers. Recommendations from this “best run” study were used by a Japanese Executive Team as their outline for reforming operations in the Staunton factory. • Championed a Six-sigma project with the Evacuation workstation. Proved that moisture in compressor refrigerant oil was the cause of extended times in the process bottleneck. Demonstrated the ability to reduce Evac times from 4+ hours to 20 minutes. • Implemented VKS (Visual Knowledge Share) for data gathering and visual SOPs on multiple production lines. This project succeeded because of strong working relationships with both upper management and the hourly union staff. • Overhauled the shop floor using 5S principles for improved organization and reduced waste. Show less
-
-
-
Corning Incorporated
-
United States
-
Glass, Ceramics and Concrete Manufacturing
-
700 & Above Employee
-
Senior Manufacturing Engineer
-
Jun 2000 - May 2005
• Resolved erratic PMD defects in Singlemode fiber with a “go and see” methodology and focused experimentation. Resolution of this critical quality issue solved a $20 million problem and restarted one third of the Wilmington site, which was previously quarantined for PMD defects. • Conducted defect mapping as part of a Six-Sigma project to show fiber breaks at the Draw were caused by a design error in the upstream process. Subsequent defect reductions gave multimillion dollar savings. • Key contributor to resolution of the handle breaks crisis, with a 99% reduction in breaks. Outcomes were improved safety, production, and morale. • Resolved stoichiometry of burner recipes and standardized troubleshooting in the Blankmaking step. These efforts brought production rate into statistical control. • Authored multiple technical reports, including a feasibility study for on-site distillation of the plant's primary base chemical. • Prior co-op and internship experience over multiple terms with Kimberly-Clark and Hoechst Celanese Corporation. Show less
-
-
Education
-
Georgia Institute of Technology
BS, Chemical Engineering -
Columbia Theological Seminary
Master’s Degree, Divinity/Ministry
Community
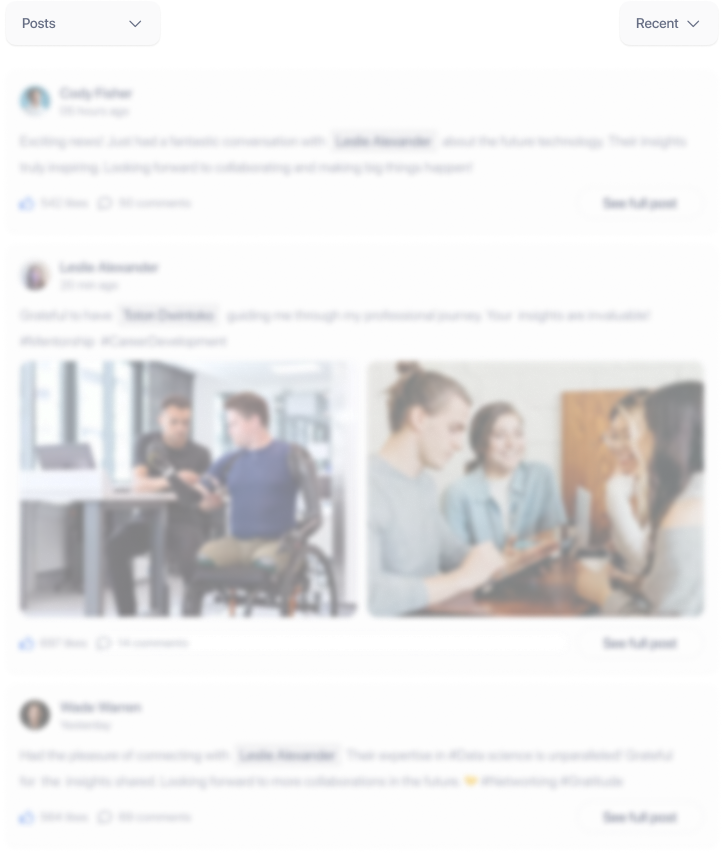