CHAI Chun Khong
Purchasing Executive at Times Printers Pte Ltd- Claim this Profile
Click to upgrade to our gold package
for the full feature experience.
Topline Score
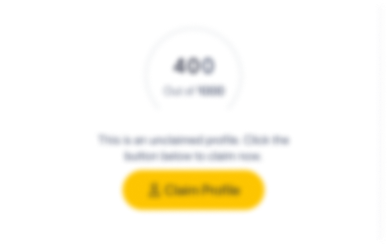
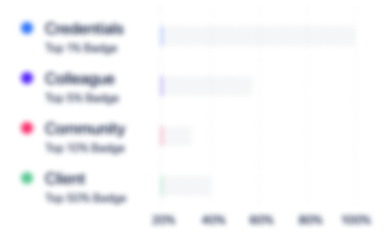
Bio
0
/5.0 / Based on 0 ratingsFilter reviews by:
Experience
-
Times Printers Pte Ltd
-
Singapore
-
Printing Services
-
1 - 100 Employee
-
Purchasing Executive
-
Jul 2019 - Present
Supplier/Vendor Sourcing - Perform market sourcing worldwide and benchmark with multiple suppliers. - Re-sourcing and localization activities to mitigate potential supply disruption (due to Covid/War), and price advantage. Supplier Evaluation and Negotiation - Source min. of 3 potential suppliers and perform evaluation on the product specification, pricing, payment term, delivery lead time and etc. for main and alternative supplier selection. - Periodically review on pricing, payment term and delivery lead time to meet company expectation of cost savings and quality assurance. Supply Chain Planning/ Tender - Monitor minimum stock level and replenishment for key products’ critical materials to ensure supply continuity to support operations. - Execute tender (Supply Contract) for high usage and high value materials like inks and plate to secure supply continuity and achieve cost savings for company. - Strategize supply chain model (geographically and volume) to achieve cost savings, contingency plan especially in current market supply situation (COVIDs, war, logistic) and shipping mode options. Build strong supplier/vendor relationship - Annual supplier performance review. - Establish positive and long term relationship with supplier as partnership for better cooperative, supports, improve efficiency and effectiveness of operations, timely delivery, and competitive pricing advantage. Claim Negotiation with supplier - Work with internal department on the claim negotiation with supplier (goods replacement, man lost cost, machine down time cost, raw material cost). - Work closely with supplier to get mutual understanding and agreement on the solution with maintain both party partnership and interest. Audit & Record - Maintain approved vendors list, PO record, evaluation report, supplier quotation and contract for ease of retrieve and for audit purposes. - Weekly ad-hoc purchase report, monthly spending report MRP/ERP – EFI Show less
-
-
-
-
Production cum Demand Planner
-
Apr 2018 - Jun 2019
Worldwide Demand Planning Specialist -Oversee worldwide demand requirement for central planning. -Analyse demand trend from worldwide regions based historical and forecasting data for material prioritization and production scheduling. -Strategic planning on safety stock and replenishment level to maximize sales revenue generation for the company. -Liaise with colleagues from worldwide region (US, Germany, Spain, Malaysia) with updated information (order qty, shipment ETD/ETA) to fulfill sales operation requirement. Stock Replenishment and Control -Propose safety stock for high runner products according to new production introduction, market trend, and seasonal business cycle. -Adjust and review safety stock level based on market demand to avoid over-stock and slow running turnover. -Converting monthly consumption data (raw material, chemical, packaging material) for Monthly Forecast Report generation. -Material planning based on MOQ, raw material shelf life, delivery lead time; ensure order placement with approval in timely manner to meet production requirement and launch date. Production Management -Organised re-occurrence team meeting with stakeholders to align on the production planning, reshuffle based on urgent order prioritization. -Delivery top-down decision and direction from management for timely execution. -Keep track on daily sales order issuance and highlight on customer’s special requirement to ensure execution by production team. Item Code Creation & BOM Maintenance -Create item code for new product and customer brand box & label. -Design coding for differentiation & identification for production execution according to customer requirements (eg. unique packaging design). -Setup BOM & routing for production to define production processed, assign usage for chemical material, foil and packaging material. Data Reporting -Compile related reports into comprehensive month end report for company management & stakeholders’ review. Show less
-
-
-
Ho Printing Singapore Pte Ltd
-
Singapore
-
Printing Services
-
1 - 100 Employee
-
Production Executive cum Planner
-
Dec 2016 - Apr 2018
Printing Job Design & Analysis - Design and analyse every printing job including paper material selection, process sequencing, machine selection, printing method, finishing involved to ensure the printing production can be proceed smoothly without interruption and efficient. Production Schedule Planning - Production planning based on order quantity, process and finishing required, production lead time, capacity utilization to meet shipment commitment. Dealing with Sub-contractor. - Sub-contractor selection and price negotiation ensure quoted price is within budget and monitor to ensure the job done within the agreed time frame. Quality Assurance - Worked closely with QA team to ensure in-house production and sub-contractor achieve excellence quality and meet quality inspective requirement before shipment to customers. Order fulfilment - Monitor production schedule closely to ensure timely order processing and liaise with production schedule in meeting customer required and expected delivery. Any production issue will be discussed and resolved immediately without delayed. Handle and response promptly to customer complaint - Organize meeting with relevant departments to identify root cause, problem analysis, corrective action and improvement plan and preventive action. Undertake any duties as assigned from time to time. Show less
-
-
-
-
Account Management Executive
-
Apr 2014 - Nov 2016
Account Management -Managed company's key customer accounts including handle new quotation and order processing as per customer requirement. Business Development -Explored new business opportunities from existing customers and growing the customer base and sales revenue. Quotation -Provided quotation as per customer requirement, specification and meet customers' expected quality. Sourcing -Involved in sourcing (sub-contractor, outsource special finishing process, die cut, etc.) as per customers' requirement. Quality Assurance -Worked closely with QA team to ensuring in-house and sub-contractor quality control can be met before delivery to customer. Order fulfillment -Ensure timely order processing and liaise with production schedule in meeting customer required and expected delivery. Customer Service -Maintain good service relationship with customers and provide excellent customers services in professional technical solution. Gather customer’s feedback against our company service and product quality for continuous improvement. Handle and response promptly to customer complaint - Organised meeting with relevant departments to identify root cause, problem analysis, corrective action and improvement plan and preventive action. -Ensure proper filing of all relevant documents from customers such as printing sample, approval artwork AI file, QC verification form and Corrective Action Request form (CAR). Show less
-
-
Education
-
Olympia College
Bachelor's Degree in Business Management, Business, Management, Marketing
Community
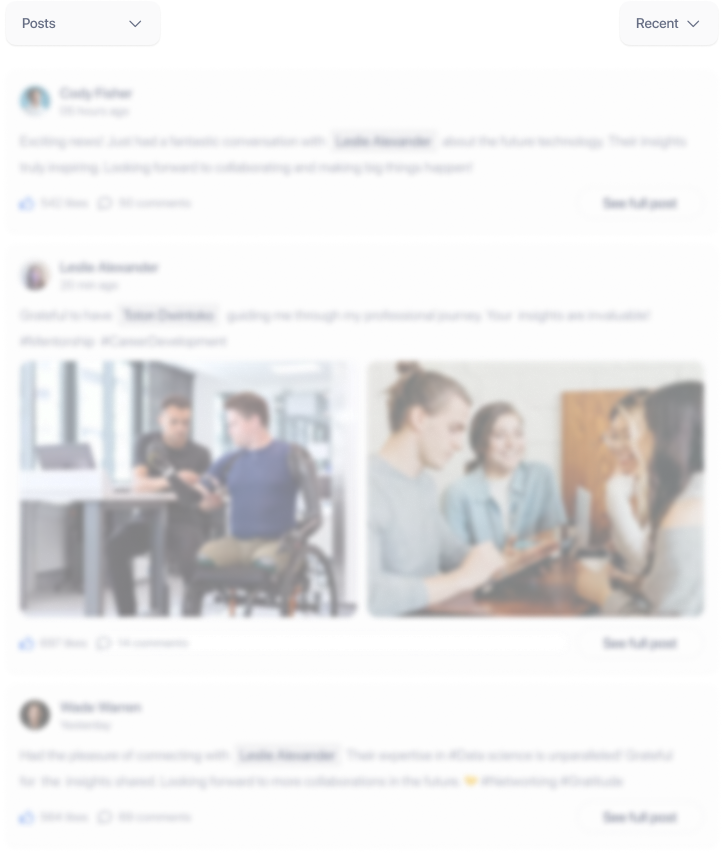