Chad Dalton
Vice President of Engineering at Dessert Holdings- Claim this Profile
Click to upgrade to our gold package
for the full feature experience.
Topline Score
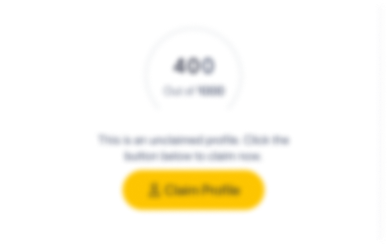
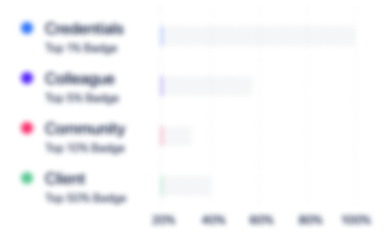
Bio


Experience
-
Dessert Holdings
-
United States
-
Manufacturing
-
100 - 200 Employee
-
Vice President of Engineering
-
Mar 2023 - Present
Fort Wayne, Indiana, United States
-
-
-
-
President
-
Jan 2022 - Present
United States
-
-
-
Aunt Millie's Bakeries
-
United States
-
Food Production
-
1 - 100 Employee
-
SVP of Manufacturing
-
Jul 2019 - Jan 2022
Fort Wayne, Indiana Area
-
-
Vice President Of Engineering / Continuous Improvement
-
Nov 2018 - Jul 2019
Fort Wayne, Indiana Area
-
-
Sr Dir of Industrial Engineering
-
Aug 2016 - Jul 2019
Fort Wayne, Indiana Area Multiple site technical support and improvment responsiblity
-
-
-
Dawn Foods Global
-
United States
-
Food and Beverage Manufacturing
-
700 & Above Employee
-
Sr Technical Services Lead
-
Jan 2006 - Aug 2016
Global Engineering Responsible for multiple site engineering of Capital project for a $1.5 Billion bakery manufacturing company . Managed all capital project funding, approval, tracking and implementation for US operations Managed line and process startups: Automated yeast and cake donut facility High speed automated CPG flow wrapped, automated carton facility 1500 ppm Automated high speed laminate dough counting / packing system 1000 ppm Automated baked cookie… Show more Global Engineering Responsible for multiple site engineering of Capital project for a $1.5 Billion bakery manufacturing company . Managed all capital project funding, approval, tracking and implementation for US operations Managed line and process startups: Automated yeast and cake donut facility High speed automated CPG flow wrapped, automated carton facility 1500 ppm Automated high speed laminate dough counting / packing system 1000 ppm Automated baked cookie line, IW with fully automated packing cells Automated cake decorating line High speed frozen cookie puck line Automated donut facility in Sohar, Oman High speed baked cookie and frozen cookie puck line (Europe) Directed process improvement projects in: Pre deposited muffin (PDM) pucks productivity and process improvements 60% productivity increase Fondant icing process improvements 50% reduction if waste and rework $1.0M saving impact Re engineering of Votated Icing process $650k per yr savings waste reduction Developed in house tooling design to cutting retool cost 50% Developed and built an engineering department from the ground up (Project, Environmental, Packaging, Electrical) Core Team member for a SCM consolidation of manufacturing footprint ($50M impact) Coordinated multiple global engineering projects simultaneous across the world Managed all capital project funding, approval, tracking and implementation for US operations Other Key Achievements: Director of Engineering within three months. Responsible for all capital projects, worldwide project management template, maintenance management, strategic plant initiative for all bakery operations to reduce operating and engineering costs.
-
-
Director of Engineer
-
Jun 2008 - Oct 2010
Managed all Capital expenditures for US frozen products operations Core team member SCM Group managed all new and major expansion and renovation projects
-
-
-
-
Vice President
-
Jun 2005 - Dec 2006
Operations Responsible for Operations, Maintenance, Engineering, Logistics for a $40M cookie manufacturing and packaging business. Directed a Greenfield build cookie project for a national product launch Successfully ramp up production to 80% OEE in 120 days from startup Managed all aspects of the business P & L Reduced Direct Labor by 15% with the use of continuous improvement Increase gross margin from 10% with the use of Business Plan Deployment (BPD) Piloted TPM… Show more Operations Responsible for Operations, Maintenance, Engineering, Logistics for a $40M cookie manufacturing and packaging business. Directed a Greenfield build cookie project for a national product launch Successfully ramp up production to 80% OEE in 120 days from startup Managed all aspects of the business P & L Reduced Direct Labor by 15% with the use of continuous improvement Increase gross margin from 10% with the use of Business Plan Deployment (BPD) Piloted TPM process for all 4 manufacturing lines Show less
-
-
-
General Motors
-
United States
-
Motor Vehicle Manufacturing
-
700 & Above Employee
-
Maintenance General Forman
-
Jan 2000 - Jun 2005
-
-
-
-
General Forman
-
Jan 2001 - Jan 2005
Maintenance Department), Responsible for maintaining and directing all maintenance functions for an aluminum cylinder head casting operation Managed 6 Supervisors, (over three shifts), 2 Reliability engineers, and 85 skilled tradesmen, (union environment) Directed R&M to yield a 15% improvement in through put in 8 months Established standardized work to maintain throughput improvements Trained and implemented Route Cause Analysis problem solving to eliminate… Show more Maintenance Department), Responsible for maintaining and directing all maintenance functions for an aluminum cylinder head casting operation Managed 6 Supervisors, (over three shifts), 2 Reliability engineers, and 85 skilled tradesmen, (union environment) Directed R&M to yield a 15% improvement in through put in 8 months Established standardized work to maintain throughput improvements Trained and implemented Route Cause Analysis problem solving to eliminate failures Implemented the use of condition monitoring, and predictive technologies to predict possible equipment failures Managed all engineering improvements Financial Assistant (Maintenance Department), Responsible for managing and tacking all financial results and initiatives. Manage a $14.5 Million labor and $28.5 Million material budget Developed maintenance financial control and tracking system Integration of payroll hours into preventive maintenance system for tacking skilled trades utilization Trained reliability engineers and supervisors in major downtime failure investigation and institutionalizing of corrections Serve as relief product team maintenance managers Facilitated 24 hour process teams to correct major maintenance initiatives for the production maintenance improvements Reliability Engineer (Lost Foam Casting Operations), Responsible for reliability and maintainability of a molding, casting and finishing operation. Assist in meeting production goals for the most aggressive ramp in General Motors history Develop the Preventive Maintenance System and tracking history Schedule and prioritized maintenance work to meet desired production ramp Analyzed diagnosed and developed solutions for complex equipment and system problems Facilitator for the maintenance team to promote better team performance Participate in several teams to solve major design or engineering constraints Assisted in the creation of a downtime tracking system Show less
-
-
-
-
Project Engineer
-
Jan 2000 - Jan 2001
Process/ Design Engineer Responsible for design and layout of custom material handling equipment, specialty machinery, and preventive maintenance systems for industrial applications. Responsible for fabrication-ready projects to leave engineering Assisted in transition from an AutoCAD - to Solidworks modeling software Layout and implemented 2 large scale preventive maintenance systems Headed a team to build automated stick hanging and storing system Assisted in several… Show more Process/ Design Engineer Responsible for design and layout of custom material handling equipment, specialty machinery, and preventive maintenance systems for industrial applications. Responsible for fabrication-ready projects to leave engineering Assisted in transition from an AutoCAD - to Solidworks modeling software Layout and implemented 2 large scale preventive maintenance systems Headed a team to build automated stick hanging and storing system Assisted in several packaging system layouts with integration of high speed packaging and palletizing Show less
-
-
-
-
Plant Engineer and Maintenance Manager
-
Jun 1996 - Jan 2000
Managed 3 Supervisors, 14 Mechanics, 3 Refrigeration Operators over three shifts Responsible for $1.2 Million R&M budget and $.5 Million Capital budget Developed and implemented a preventive maintenance system and maintenance store room to support a ready to eat packaging manufacturing Initiated and Installed two major product line consolidations and renovation to increase facility output 150% with no hourly labor increase
-
-
Assistant Plant Engineer
-
Dec 1995 - Jun 1996
Managed 6 Supervisors, 45 Mechanics, 5 Refrigeration Operators over three shifts Responsible for $4.5 Million R&M budget Developed and implemented a preventive maintenance system
-
-
-
-
Plant Engineer and Maintenance Manager
-
Jan 1995 - Jan 2000
Directed all functions of a daily maintenance and engineering needs of a refrigerated food processing facility. Managed 5 Supervisors, 24 Mechanics, 5 Refrigeration and 3 WWTP Operators over three shifts Installed New Waste Water Pre- Treatment Plant Renovated and installed, and maintained a 1,100 ton Ammonia Refrigeration System Responsible for $1.4 Million R&M budget and $6.5 Million Capital budget Layout and installed low pressure boiler and steam piping system… Show more Directed all functions of a daily maintenance and engineering needs of a refrigerated food processing facility. Managed 5 Supervisors, 24 Mechanics, 5 Refrigeration and 3 WWTP Operators over three shifts Installed New Waste Water Pre- Treatment Plant Renovated and installed, and maintained a 1,100 ton Ammonia Refrigeration System Responsible for $1.4 Million R&M budget and $6.5 Million Capital budget Layout and installed low pressure boiler and steam piping system Filed and maintained all air, water and waste discharge permits Designed and installed a high efficiency, high pressure hot water system Developed and implemented a preventive maintenance system and maintenance store room for high speed packaging equipment Show less
-
-
-
-
Shift Superintendent
-
Jan 1991 - Jan 1995
Responsible for all shift operations of a 6,000 ton a day Sugar Beet Refining Facility. Managed 4 Leadpeople and 25 Labors in a union environment Delegated over first phase of union grievance process Designed instrumentation and Control Logic System layouts Designed and installed a PLC Real Time Control System Assisted in a total facility renovation in increase production 25% Directed summer maintenance and capital projects
-
-
Education
-
Purdue University
B.S. of applied -
Purdue University
BS
Community
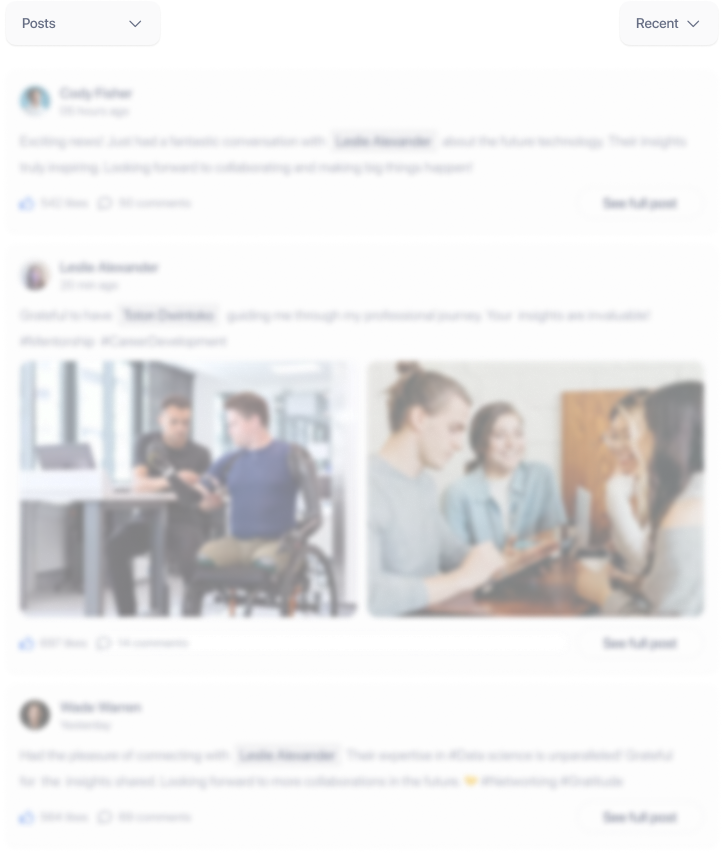