Carlos Cuan Lerma
Supply Chain Network Optimisation Analyst at Ricoh Australia- Claim this Profile
Click to upgrade to our gold package
for the full feature experience.
-
Spanish Native or bilingual proficiency
-
English Native or bilingual proficiency
Topline Score
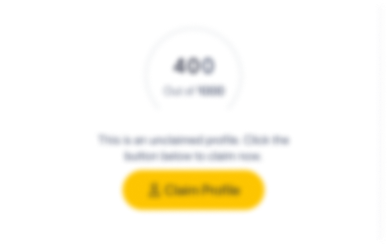
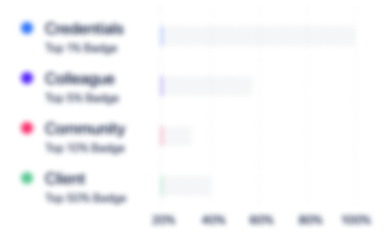
Bio


Experience
-
Ricoh Australia
-
Australia
-
IT Services and IT Consulting
-
400 - 500 Employee
-
Supply Chain Network Optimisation Analyst
-
Mar 2019 - Present
- Project lead for the Spare Parts Optimisation Project. Review and map current processes in conjunction with extensive data analysis in order to develop (and execute) a comprehensive proposal to improve and re-design its current Supply Chain by improving product availability and reducing its footprint across Australia. - Created from ground-up +15 Power Bi Dashboards analysing and providing insights for inventory health, demand/consumption across territories, planning tool, KPIs, transport, etc. to support day to day operations.- Project management activities included training and coaching champions and direct report in each territory on how to leverage newly created reports to streamline better manage their inventories.- Work closely with IT to identify process improvements by automating/semi-automating activities increasing productivity and minimising resources spent on non-value activities. - In parallel to the optimisation project I am the full-time Planner for Spare Parts.
-
-
-
Medtronic
-
United States
-
Medical Equipment Manufacturing
-
700 & Above Employee
-
Senior Supply Chain Analyst
-
Jan 2018 - Mar 2019
- Maintain and improve dispatch performance by building cross-functional relationships with all key stakeholders throughout the company's Supply Chain and our 3PL partner.- Evaluate customer satisfaction performance, investigate issues and implement solutions- Sales and operations planning execution to ascertain focus, alignment and synchronization among critical functions. May-Jul 2018 end of quarter achieved the highest Sales/dispatch KPI in recent years.- Cost reduction and supply chain optimisation by data analysis and prepare reporting with key drivers of the operation
-
-
Outbound Implementation Project Lead (secondment)
-
Sep 2017 - Dec 2017
Support ERP and WMS operational performance- Lead a team troubleshooting orders to maintain dispatch KPIs- Analyse the main 6 data discrepancy categories, using Lean Sigma DMAIC methodology to Deep dive into each root cause and implement corrective actions, 97% misalignment reduction by the end of the project.- Outbound output surpassed previous system on week 2 after go-live.
-
-
Logistics Analyst
-
Jul 2016 - Aug 2017
In addition to the previous transport activities I was assigned with side projects, below are the three main ones:- Support the ERP/WMS/TMS team implementation from the transport point of view, manage and solve challenges faced during the migration and develop multiple manual reports to provide tracking visibility of the entire operation (6 months) - Eliminate the use of manual records and incorporate the return process to the new ERP- Improve levels of service to Home Deliveries by implementing a new carrier/service with improved tracking and delivery options
-
-
Logistics Associate
-
Nov 2015 - Jun 2016
-Relationship management with all carriers providing transport services to the company, performance reviews and customer experience enhancement- Reverse logistics process management and improvement-Escalation point regarding subpar SLAs and urgent deliveries for patients in critical condition
-
-
-
MMMigration & Recruitment
-
Australia
-
Legal Services
-
1 - 100 Employee
-
Independent Consultant
-
Mar 2014 - Nov 2014
-Map current processes and evaluate alternatives to improve operation efficiency. -Implement CRM software in order to centralise all information flows into a single system.-Increase process visibility, simplify report generation and reduce time and costs involved in handling each client’s case. -Re-deploy resources into value generating activities, increase productivity and reduce the need of new staff to better manage the growing number of cases received throughout the year. -Map current processes and evaluate alternatives to improve operation efficiency. -Implement CRM software in order to centralise all information flows into a single system.-Increase process visibility, simplify report generation and reduce time and costs involved in handling each client’s case. -Re-deploy resources into value generating activities, increase productivity and reduce the need of new staff to better manage the growing number of cases received throughout the year.
-
-
-
Johnson & Johnson
-
United States
-
Hospitals and Health Care
-
700 & Above Employee
-
MBA Internship
-
Jul 2013 - Oct 2013
Internship took place at J&J medical device division in North Ryde, Supply Chain project.- Identify changes to improve the productivity and cost effectiveness of a tier structured supply chain - customer service scheme.- Analyse and measure expenditure of key resources such as time and expenses at every stage of the supply chain and suggesting best practice alternatives.- Supply chain modelling and optimisation.- Provide optimal scenarios and present to upper management results and recommendations.
-
-
-
Neolpharma SA de CV
-
Mexico
-
Pharmaceutical Manufacturing
-
500 - 600 Employee
-
International Business Manager
-
Jan 2009 - Dec 2012
- Business development activities in international markets to increase exporting sales throughout the American continent including product selection, capital budgeting and employee selection (12 countries).- Coordinate export supply chain from production to delivery at final destination. - Develop marketing strategies and sales forecasts. - Implement change management programs to switch key areas mindset from being a local company to a international firm and the standards required to compete as such. - Inventory management and data analysis. - Coordinate regulatory, legal and sales teams in each territory.
-
-
-
Walmart
-
United States
-
Retail
-
700 & Above Employee
-
Assistant Manager Supply Chain
-
Aug 2006 - Oct 2008
Positions held within Wal*Mart's Logistics DivisionAssistant Manager USA and Canada Supply Chain Jan/08 - Oct/08Assistant Manager Purchasing Order Control Worldwide Jan/07 – Dec/07 Trainee ISO 9001 project Aug/06 – Dec/06 - Coordinate import process from multiple worldwide origins to Mexico.- Constantly improve lead times and strategic KPIs benchmarked with industry standards.- Achieve fill rate goals throughout all distribution centres and final stores.- Provide customer service for suppliers, custom brokers, transport personnel and solving bottlenecks. - Improve administrative and operational processes related to Wal*Mart's logistic division in order to achieve cost reductions.- Prepare reports, measure processes and develop new working plans in order to detect bottlenecks, solve discrepancies, control, and approve all import purchasing orders in the system. - Implemented ISO 9001 certification
-
-
Education
-
Macquarie Graduate School of Management
MBA, Business Administration and Management, General -
AIPE
Diploma in Project Management, Project Management -
Instituto Tecnológico y de Estudios Superiores de Monterrey / ITESM
Bachelor of Commerce (B.Com.), International Business/Trade/Commerce -
Macquarie University
Diploma/Certificate in (Exchange), Commerce
Community
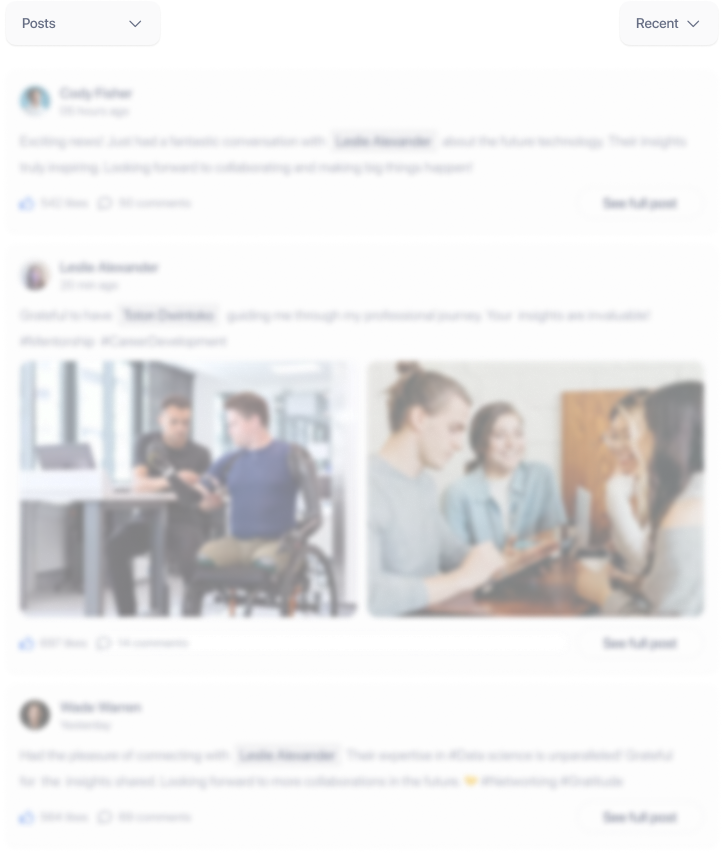