Carl Roush
Corporate Customer Quality Manager at GRAMMER Americas- Claim this Profile
Click to upgrade to our gold package
for the full feature experience.
-
English -
Topline Score
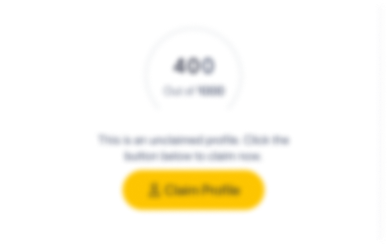
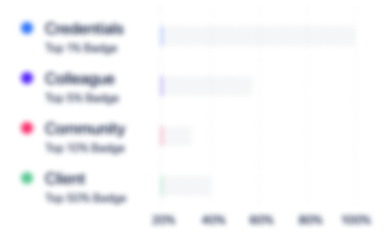
Bio


Credentials
-
Certified ISO/TS 16949:2009 Supplier Auditor
AIAGMar, 2015- Nov, 2024
Experience
-
GRAMMER Americas
-
United States
-
Motor Vehicle Manufacturing
-
300 - 400 Employee
-
Corporate Customer Quality Manager
-
Jan 2022 - Present
I am the direct corporate quality support/escalation contact responsible for two internal manufacturing facilities in NW Ohio, and one facility in Southern Tennessee. I provide corporate scorecard management and tracking for all sites within the US and Mexico who are supplying to Ford, GM and Stellantis. I also provide quality systems and internal database support to all sites within our Functional Plastics division - who are providing injection and blow molded components and assemblies to the automotive industry.
-
-
Corporate Quality Engineer
-
Dec 2019 - Jan 2022
My primary focus during this time was support of one specific plant in Mexico (both remotely from NW Ohio, and significant time spent directly on site in Mexico) during a critical turnaround initiative. During this time, I also championed corporate QMS objectives and provided training and administration of internal quality software to all sites in the region. Additionally, I was the primary escalation for all plants in the Americas region - regarding Ford escalations and support.
-
-
-
GRAMMER Americas
-
United States
-
Motor Vehicle Manufacturing
-
300 - 400 Employee
-
Corporate Quality Engineer
-
Apr 2018 - Oct 2019
Worked as an internal IATF lead auditor, and also supported registrar and customer audit activities for six manufacturing facilities in the US and Mexico.
-
-
Plant Quality Manager
-
May 2015 - Apr 2018
Managed a team of 6 direct reports including quality engineers and coordinatorsQuickly improved customer confidence, recovered all scorecards back into green status within 6 months Reduced customer chargebacks by 80% over my three year tenureLed BG team to become the first IATF certified plant in the organization - March 2018Worked with a diverse customer mix of roughly 15 customers (Ford, FCA, GM, Nissan, and many tier 1 customers such as Valeo, Faurecia, Magna and others)Leadership, coaching and mentoring staff
-
-
Corporate Quality Engineer
-
Apr 2014 - May 2015
Conducted bi-annual internal audits at six manufacturing facilities as well as the corporate offices as an IATF16949 lead auditor.Supported all facilities with 3rd party registrar and customer audits.Worked with all plants to continually improve the QMS and ensure compliance to ISO/TS 16949, ISO 9001, internal and customer requirements.
-
-
Plant Quality Engineer
-
Oct 2009 - Apr 2014
Championed corrective action process for current model quality issuesRepresented TMD at customer and supplier facilitiesTrained quality coordinators/auditors to quality standards & proceduresProduced detailed inspection and assembly instructionsMonitored supply base/issue vendor rejections and chargebacks
-
-
Plant Quality Coordinator
-
Feb 2008 - Oct 2009
Managed internal certification and non-conforming material processes.Supported quality auditors and provided direction as the primary quality contact on the shop floor.
-
-
Press Operator/Back Up Auditor
-
May 2004 - Feb 2008
-
-
Education
-
Owens State Community College
Community
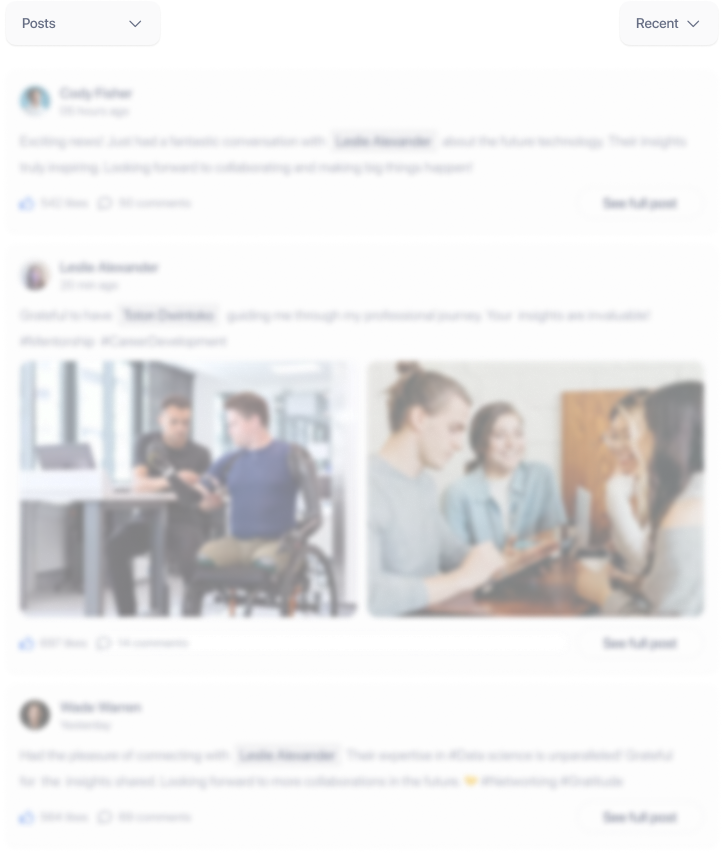