Cameron Klug
Director Of Quality at NuVasive- Claim this Profile
Click to upgrade to our gold package
for the full feature experience.
Topline Score
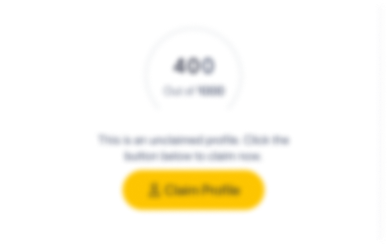
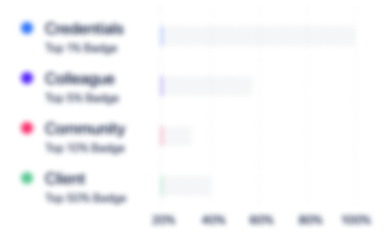
Bio
0
/5.0 / Based on 0 ratingsFilter reviews by:
Credentials
-
ASQ CQE
ASQJun, 2010- Sep, 2024
Experience
-
NuVasive
-
United States
-
Medical Device
-
700 & Above Employee
-
Director Of Quality
-
Sep 2017 - Present
- Maintained and improved on QMS to ensure compliance with CFR820 and ISO13485 (BSI) - Management representative for 3rd party registrars and government agencies. - Quality planning and project planning for large scale projects including M&A and new facility start up. - Diligence for M&A targets. - Change management including PMA supplements and MDR tech files. - Validation Master Planning - Leadership of Corrective/Preventative Action program - Author and facilitate Management Review. - Implement and maintain risk management systems. - Coach, mentor, train, and evaluate a staff of ~60 direct and indirect reports - Develop Standard Operating Procedures and Work Instructions. - Project leadership with cross functional departments like Development, Regulatory, Marketing, Legal, and Clinical affairs. - Strategic planning and establishing quality team goals to align with business goals. - Design Transfer Show less
-
-
-
Avalign Technologies
-
United States
-
Medical Equipment Manufacturing
-
200 - 300 Employee
-
Quality Manager
-
Jul 2016 - Sep 2017
• Maintained and improved on QMS to ensure compliance with CFR820 & ISO13485 (BSI) • Manage Corrective/Preventative Action program (Customer/Internal/Suplier/Preventative) • Manage and maintain validation program. • Author and facilitate Management Review. • Implement and maintain risk management systems. • Coach, mentor, train, and evaluate a staff of 26. (Quality Engineers, Inspectors, Auditors, Technicians, Document and Record Control) • Develop Standard Operating Procedures and Work Instructions. • Review and approve engineering change requests. • Manage quality team goals to align with business goals. • Manage and perform internal and supplier audits. • Asist with design transfer activities. Show less
-
-
-
Parker Hannifin
-
United States
-
Industrial Machinery Manufacturing
-
700 & Above Employee
-
Plant Quality Manager
-
Oct 2014 - Jul 2016
• Maintained and improved on QMS to ensure compliance with ISO9001 registrar (DNV) • Author and facilitate Management Review • Manage Corrective/Preventative Action program (Customer/Internal/Suplier/Preventative) • Supplier Evaluation / Development • Train and facilitate quality culture and data driven problem solving. (PDCA-10 Step) • Implement process validation program • Track trend and facilitate visual management and problem solving for quality metrics. • Implement/Facilitate value added system for managing PFMEA’s • Interface with customers for and manage customer complaint system • Train and coach high performance teams, quality, and manufacturing personnel • Create Procedures, Work Instructions, & Standard work • Review and approve engineering change requests. • Manage quality team goals to align with business goals. • Review RFQs and give feedback to sales team. • Manage customer quality excellence programs. • Perform and manage internal and external audits. Show less
-
-
-
Symmetry Medical
-
United States
-
Medical Equipment Manufacturing
-
300 - 400 Employee
-
Quality Engineer/Supervisor
-
May 2010 - Oct 2014
• Initiate APQP and work with customers, manufacturing engineering and production to manage project launches and ensure successful device transfer • Author and present management reviews • Assist with supplier quality functions (scorecards, improvement plans, SCAR’s, APQP) • Act as team member management representative for audit functions. (BSI, FDA, Customer Audits) • Corporate Administrator for SPC and Qualtrend (Web based Quality Reporting Tool) • Track and trend quality metrics • Develop inspection methods for in-process inspection and first article inspection • Write control plans and (P)FMEA • Conduct statistical process studies • Measurement Systems Analyses • Change management (supplier and engineering change requests) • Champion and manage internal and external CAPA’s • Develop and/or Modify work instructions and/or SOP’s Show less
-
-
-
Ward Corporation
-
United States
-
Individual and Family Services
-
Multiple Positions (Program Manager, Supervisor, Lead Quality Tech)
-
Aug 1999 - Jan 2009
• Oversaw and assisted in the completion of all PPAPs • Six Sigma Project • Set-up and trouble shot programming machining, permanent molding and sand casting. • Direct and prioritize daily goals for 2nd and 3rd shift supervisors, developed machine schedules Gage calibration and MSA. • CMM programming • Oversaw and assisted in the completion of all PPAPs • Six Sigma Project • Set-up and trouble shot programming machining, permanent molding and sand casting. • Direct and prioritize daily goals for 2nd and 3rd shift supervisors, developed machine schedules Gage calibration and MSA. • CMM programming
-
-
Education
-
Purdue University
Bachelor of Science, Industrial Engineering Technology -
Purdue University Fort Wayne
BS, Industrial Engineering Technology
Community
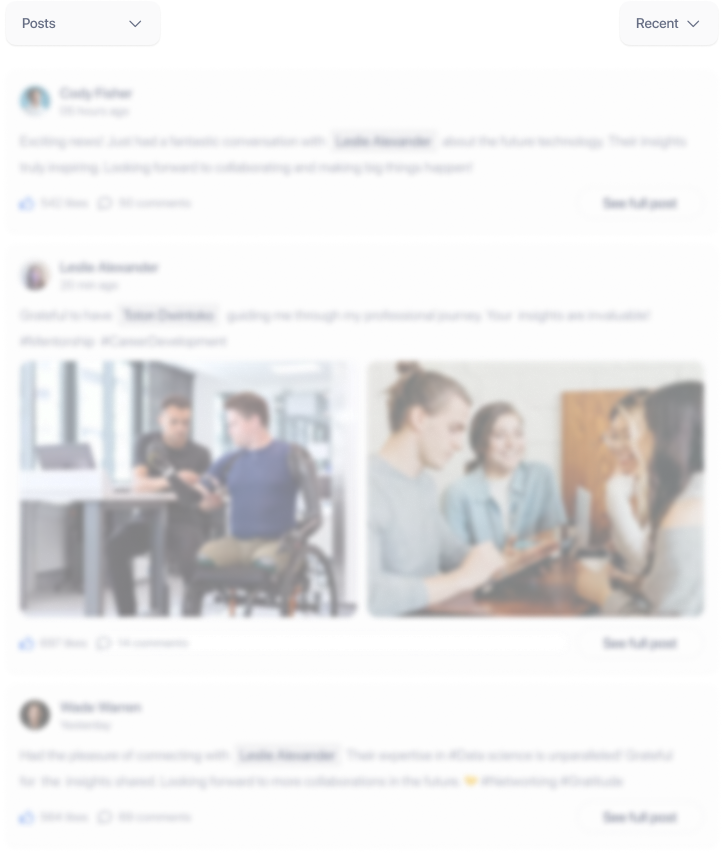