Caleb Burlison
Logistics Manager at ARAUCO - North America- Claim this Profile
Click to upgrade to our gold package
for the full feature experience.
-
English -
Topline Score
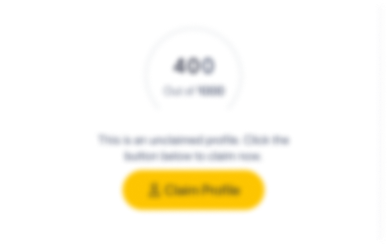
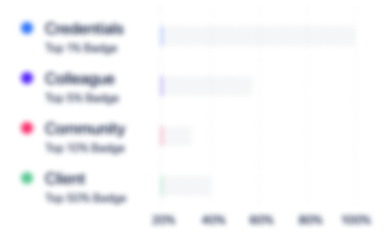
Bio


Experience
-
ARAUCO - North America
-
United States
-
Manufacturing
-
400 - 500 Employee
-
Logistics Manager
-
Oct 2019 - Present
-
-
Production Manager
-
Oct 2017 - Oct 2019
Direct 5 Area Coordinators responsible for 4 process areas throughout the facility and supervision of 136 shop floor employees. Oversee day-to-day performance of two production lines and thermally fused laminate operations. Engage and empower employees to perform at their best and promote a safety-first culture. Ensure safety, quality, and operational metrics of the production line to achieve maximum profitability. Collaborate with Maintenance Manager to improve uptime. Focus on vision of continuous improvement in all aspects of the business, including people, costs, production, safety, environment, quality, image, and customer satisfaction. Participate in yearly budgeting process. Analyze daily, weekly, and monthly metrics. Manage special projects, including capital projects, and assignments handed down by corporate. Play a key role in executing Lean Six Sigma initiatives.Key Contributions:Designed and implemented a successful Team-Based Work Force similar to that adopted by Miller Brewing, Coors, and Proctor & Gamble.Interviewed, hired, and trained a new team of Area Coordinators.Drive mill’s performance, reduce variation, decrease waste, increase speed, and champion a culture of continuous improvement.Consistently achieve budgeted cost of goods manufactured for raw production on a monthly basis.Work closely with Financial Manager to ensure product costing by production line is accurate and aligned with costing models so that accurate data is accessible for potential changes in sales strategy.Make sure production schedules are executed properly with maximum efficiency and the lowest cost possible. Show less
-
-
-
ARAUCO - North America
-
United States
-
Manufacturing
-
400 - 500 Employee
-
Shipping & Logistics Coordinator | Inventory Reconciler | Lamination Shop Floor (2011 to 2012)
-
2011 - 2017
Advanced through a series of entry-level positions to a supervisory role with responsibility over 20 employees within the Shipping & Logistics Department. Communicated company and plant-level initiatives with employees. Enforced attendance and company policy with employees. Participated as secondary scheduler in planning production, demonstrating ability to schedule both raw board and laminate lines. Proficiently navigated SAP systems. Communicated and steered Warehouse initiatives. Worked in conjunction with Finance on reconciliation and inventory activities. Key Contributions: Garnered a solid understanding of basic AAR regulations as well as Transportation regulations. Looked for areas in need of improvement and oversaw initiatives to remedy problems to drive efficiency. Oversaw reconciliation between Manufacturing Reporting System and Epicor ERP. Took ownership of end-of-month inventory and procedures. Recognized as SAP Business Super User. Selected to participate in SAP Project Arrow, North American Design and Implementation of SAP, a two-year initiative in conjunction with Accenture; traveled to all nine company-owned facilities geographically dispersed across the US and trained employees on new system. Implemented functionality of WM Module in SAP. Served as ITF Training Coordinator for business facility roll outs; produced trainings and manuals for business. Continuously identified ways to improve upon product and help drive necessary changes. Show less
-
-
-
Lassen Rv
-
United States
-
Retail
-
RV Service Technician | Cabinet & Finish Assembler
-
2008 - 2011
Hired as Cabinet & Finish Assembler and promoted to RV Service Technician based on performance and desire to advance with company. Provided outstanding service in communicating with and quoting work orders for customers. Participated in the remanufacturing of damaged or neglected RV units. Key Contributions: Gained a solid knowledge of RV models and parts; utilized knowledge to enhance sales. Applied creativity and innovation to engineer redesigns, including customizations, for new and older RV units. Worked closely with customers on the design of purchased RV units. Collaborated with insurance companies and handled work for most insurance claims. Show less
-
-
-
Country Coach
-
Motor Vehicle Manufacturing
-
1 - 100 Employee
-
Area Manager | Assistant Manager | Shop Floor
-
2003 - 2008
Managed production of Cabinet Shop and controlled quality of production. Supervised 28 employees. Interviewed candidates and conducted employee performance reviews. Produced DuPont Corian countertops and assembled/installed cabinets. Read and revised blueprints. Key Contributions: Recognized as one of the youngest area managers within the company. Created and implemented manufacturing procedures and cost-effective strategies for the company. Started up two new manufacturing lines. Consistently maintained on-time production schedule. Acquired experience in both 12v and 110v electrical. Show less
-
-
-
Western Woodworking
-
United States
-
Wholesale Building Materials
-
Entry-Level Cabinet Assembler
-
2001 - 2003
-
-
-
Saint Joseph Catholic Church
-
Religious Institutions
-
1 - 100 Employee
-
Assistant
-
1997 - 2003
-
-
Education
-
Chemeketa Community College
General Studies
Community
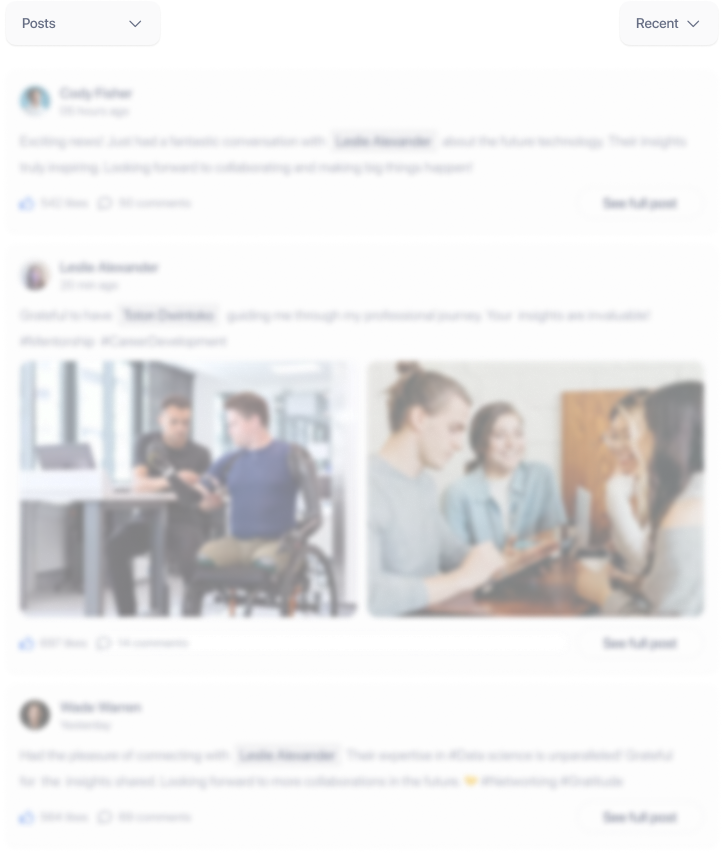