BURAK A.
Product Development Manager at Lavazza Professional UK- Claim this Profile
Click to upgrade to our gold package
for the full feature experience.
-
İngilizce Professional working proficiency
Topline Score
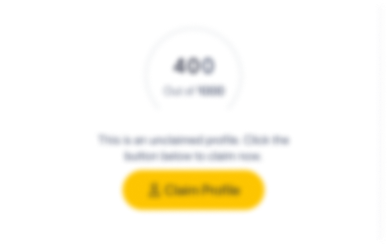
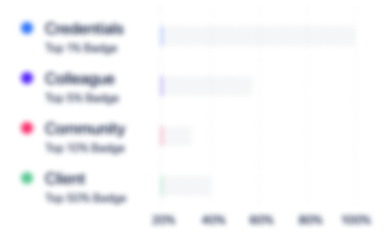
Bio


Credentials
-
PRINCE2® 2017 Practitioner
AXELOS Global Best PracticeJun, 2022- Nov, 2024 -
PRINCE2® Foundation
AXELOS Global Best PracticeOct, 2021- Nov, 2024 -
IBM Data Science Professional Certificate
CourseraJun, 2020- Nov, 2024 -
Six Sigma Black Belt Certification – Level I
Beko GlobalDec, 2017- Nov, 2024
Experience
-
Lavazza Professional UK
-
United Kingdom
-
Food and Beverage Services
-
100 - 200 Employee
-
Product Development Manager
-
May 2023 - Present
-
-
Product Development Engineer
-
Mar 2022 - May 2023
Managing product development projects for Lavazza.
-
-
Project Engineer
-
Jan 2021 - Mar 2022
Managing existing Lavazza coffee machine products projects. Developing projects and designs to maintain single-serve products in the market longer within the expected quality.
-
-
-
Serco
-
IT Services and IT Consulting
-
700 & Above Employee
-
NPD & NPI Consultant / Quality & Assurance Lead
-
Feb 2020 - Jan 2021
Consulting about new product development for new product projects. All design steps. Provide mentoring and guidance to internally(Serco) and externally(Serco’s suppliers) in terms of design, safety, quality, reliability, ruggedised design, product life cycle, benchmark, research and many new product-related issues. There is no standardised test specification in this field. All tests are developed according to research and in house customer behaviour reports. Consulting about new product development for new product projects. All design steps. Provide mentoring and guidance to internally(Serco) and externally(Serco’s suppliers) in terms of design, safety, quality, reliability, ruggedised design, product life cycle, benchmark, research and many new product-related issues. There is no standardised test specification in this field. All tests are developed according to research and in house customer behaviour reports.
-
-
-
Swytch Bike
-
United Kingdom
-
Computers and Electronics Manufacturing
-
1 - 100 Employee
-
Engineering Consultant
-
Mar 2019 - Jan 2020
Using all experience to growth of the business. Responsible for generating solutions for technical and non-technical problems on different projects and process. Involves a range of tasks, including ; • Product & Project management • Life Cycle Management • Manufacturability • Documentation • Industrial Design & CAD Design & CAD Assembly • Rapid Prototyping - Mechanical / Electrical • After Sales & Customer Support • Online Fault Finding Systems (Zing-tree) • Quality & Assurance standards • Test jigs manufacturing • BOM development and management Show less
-
-
-
Beko Global
-
Türkiye
-
Manufacturing
-
700 & Above Employee
-
Technical Project Leader / Senior Research Development Design Specialist
-
May 2018 - Nov 2018
Responsible for providing project planning and management for established initiatives within the company. New product projects which have more than 1 million euro investment budgets for several brands such as Arcelik, Beko, Grundig, Altus, Bloomberg, Altus were managed. Projects are completed to specification, within an established time frame and budget. Experienced in each step in NPD( New Product Introduction) / NPI(New Product Introduction) operations from VOC( Voice of Customer ) to DFM/DFA (Design for manufacture and assembly). Directed recruitment/training/staff development initiatives to maximise productivity and revenue potential through the development of an R&D team. Administered daily operations to ensure were adhered to and understand my team. Cultivated strong business relationships with the customers to drive business development with inner departments or customers. Mentoring and guidance are provided to the whole project team. Show less
-
-
-
Beko Global
-
Türkiye
-
Manufacturing
-
700 & Above Employee
-
Technical Project Leader / Research Development Design Specialist
-
Mar 2016 - Mar 2018
Responsible for new small-scale projects such as feature design for new or current projects, cost reduction, quality improvement, common part usage, speed up the assembly process and put into mass production designed products. Connecting multinational relations with prototype producers to develop samples for significant fairs. Detailed documentation was prepared for 3rd part approval and planned tests for serial approval.
-
-
Research Development Design Engineer
-
Aug 2015 - Mar 2016
Responsible for design-related issues of new plastic, metal and thermoformed parts and design changes according to projects needs. Critical measurement check of first samples of parts and moulder vacation for audit. Generates six sigma projects to shape part design’s future.• 15 parts designed form concept to manufacture. Along with this design session, many DFMEA meeting arranged and documented. As a result of this meeting, best practices archived to provide better designs for the future.• 3 design changes were made due to test results. To eliminate these problems, manufacturing and assembly methods were examined. In one-month permeant solution were developed and tested by each one and provide min. 1 euro cost reduction.• Business trips were made to China to approve 25 plastic injection moulds of the new part. During this journey, each samples critical dimensions were measured, controlled in visual check and assembly issues. Show less
-
-
-
Beko Global
-
Türkiye
-
Manufacturing
-
700 & Above Employee
-
Manufacturing Engineer
-
Mar 2013 - Aug 2014
Responsible for production manufacturing line and projects about scrap reducing, quality improvement, maintenance plans and shift plans. • Developed scrap cause systems that allow easily find out the exact operation points. According to this data, daily/weekly/monthly maintenance plans prepared and developed. • To minimise the on line repair activities continuous education planed. • One paper documents prepared to avoid assembly errors. • Yearly shift and holiday plans prepared for production line workers. • To avoid working accident monthly controls were made and permanent precaution equipment was supplied and engaged. • Extra audit points were specified for both visual and electronic component controls. Show less
-
-
Education
-
Yildiz Technical University
3,15, Mechanical Engineering
Community
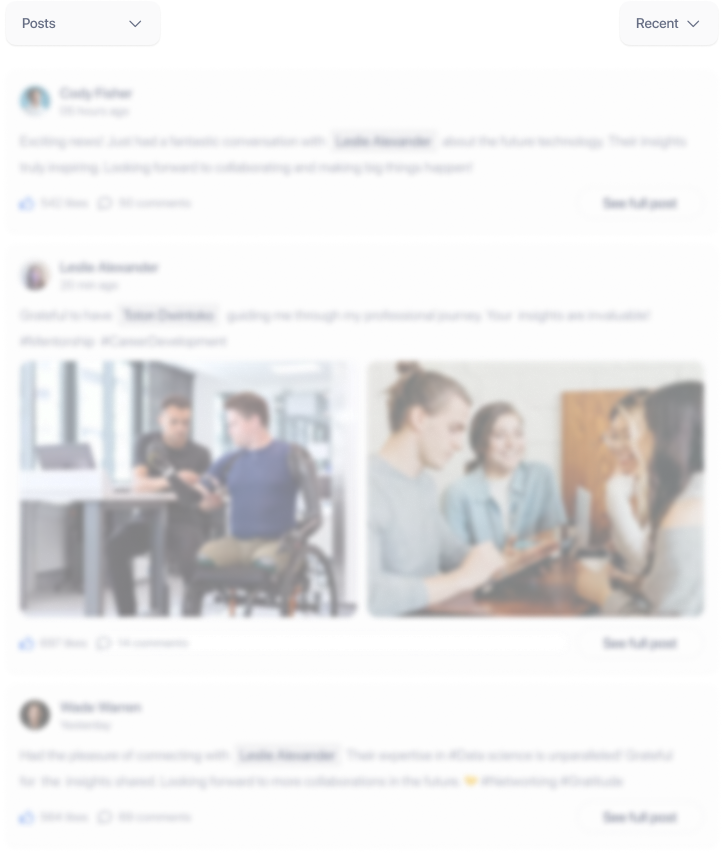