Bruce Zutter
Continuous Improvement/Production Manager at MiTek USA- Claim this Profile
Click to upgrade to our gold package
for the full feature experience.
Topline Score
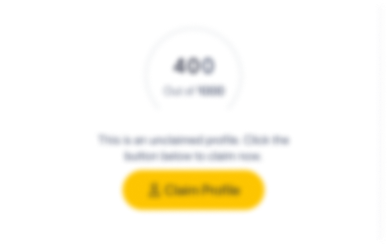
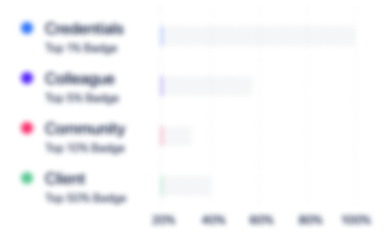
Bio

Tim Bell
Bruce is one of our most active dads at Five Hawks. He is always willing to go the extra mile for his kids, and all the students at Five Hawks. He makes a great DJ for our Family Fun Night!

David Bush
I have known Bruce for 15 years as a friend and as a person I could go to for Prepress expertise. He knows his business and is a true professional in the field. Bruce stays on top of the cutting edge of technology and always seeking to create a better solution. Any company would be fortunate to have Bruce on their team.

Tim Bell
Bruce is one of our most active dads at Five Hawks. He is always willing to go the extra mile for his kids, and all the students at Five Hawks. He makes a great DJ for our Family Fun Night!

David Bush
I have known Bruce for 15 years as a friend and as a person I could go to for Prepress expertise. He knows his business and is a true professional in the field. Bruce stays on top of the cutting edge of technology and always seeking to create a better solution. Any company would be fortunate to have Bruce on their team.

Tim Bell
Bruce is one of our most active dads at Five Hawks. He is always willing to go the extra mile for his kids, and all the students at Five Hawks. He makes a great DJ for our Family Fun Night!

David Bush
I have known Bruce for 15 years as a friend and as a person I could go to for Prepress expertise. He knows his business and is a true professional in the field. Bruce stays on top of the cutting edge of technology and always seeking to create a better solution. Any company would be fortunate to have Bruce on their team.

Tim Bell
Bruce is one of our most active dads at Five Hawks. He is always willing to go the extra mile for his kids, and all the students at Five Hawks. He makes a great DJ for our Family Fun Night!

David Bush
I have known Bruce for 15 years as a friend and as a person I could go to for Prepress expertise. He knows his business and is a true professional in the field. Bruce stays on top of the cutting edge of technology and always seeking to create a better solution. Any company would be fortunate to have Bruce on their team.

Credentials
-
Lean Six Sigma Black Belt
6sigmastudy.comSep, 2012- Oct, 2024 -
Six Sigma Green Belt
6sigmastudy.comJan, 2012- Oct, 2024
Experience
-
MiTek USA
-
United States
-
Construction
-
200 - 300 Employee
-
Continuous Improvement/Production Manager
-
Sep 2019 - Present
• Responsible for developing, planning, and implementing Continuous Improvement opportunities with an emphasis on Lean Manufacturing. • Responsible for developing and training the organization on the introduction of Continuous Improvement/Lean methodology and techniques. • Developed, Educated and Facilitated multiple cost saving initiatives within a team environment. • Champion for Plant Safety and EHS initiatives for the Montgomery facility. • Responsible for developing, planning, and implementing Continuous Improvement opportunities with an emphasis on Lean Manufacturing. • Responsible for developing and training the organization on the introduction of Continuous Improvement/Lean methodology and techniques. • Developed, Educated and Facilitated multiple cost saving initiatives within a team environment. • Champion for Plant Safety and EHS initiatives for the Montgomery facility.
-
-
-
AWT Labels & Packaging
-
United States
-
Printing Services
-
1 - 100 Employee
-
Quality Engineer/Lean Engineer/Safety Specialist
-
Jul 2015 - Jul 2019
• Managed, maintained and audited the CAPA database while providing training on root cause analysis and corrective action effectiveness for both CAR and PAR inputs.• Managed the nonconforming product isolation quality process while initiating and completing investigations into root cause and corrective action plans to resolve any quality issues.• Integral part of ISO 9001-2015 implementation and certification team, performed internal and external audits in compliance with ISO9001-2015 standards.• Developed and managed the document revision and review/approval cycle for technical, process and safety documents along with auditing and updating quality documents that included standard work, work instructions and process flow charts. • Supported the change control process internally and externally as initiated by customers, suppliers or from internal sources in the organization.• Provided knowledge and assistance when developing risk management plans for new products.• Provided guidance and performed audits for the internal and external equipment calibration systems.• Developed and deliver monthly OSHA required safety training for the entire facility, performed and documented scheduled and spot safety audits.• Managed safety incident, near miss incidents and damaged property occurrences while providing preventative action plans to avoid recurrence.
-
-
Lean/CI Manufacturing Coordinator
-
Nov 2013 - Jul 2015
• Responsible for identifying, planning and implementing continuous improvement opportunities with a focus on Lean Manufacturing and Six Sigma methodologies driven by data analysis and KPI's• Developer, trainer and mentor of cross functional process improvement teams on the application of lean tools and concepts which include 5S, Standard Work, Kaizen Events, VSM and Root Cause Analysis methodologies.• Coordinator, Auditor and Performer of daily Gemba walks to ensure compliance to established agreed upon process changes and implementation of efforts to correct variation in process.• Tasked with auditing and updating quality documents that include standard work, work instructions and process flow charts.• Advocating continuous improvement through all levels of the organization and ensuring proper support from each level.• Facilitator of the completion of CAR (Corrective Action Request) investigations and counter measure implementation.• Planner and Implementation Leader of the PAR (Preventative Action Request - employee waste elimination suggestions) system requests through the daily standup meeting format.• Presentation of quality data pertaining to shipping efficiencies and CAR incidents daily at morning production meeting.• Facilitator of the completion of CAR (Corrective Action Request) investigations and counter measure implementation.• Planner and Implementation Leader of the PAR (Preventative Action Request - employee waste elimination suggestions) system requests through the daily standup meeting format.• Presentation of quality data pertaining to shipping efficiencies and CAR incidents daily at morning production meeting.
-
-
-
Corporate Technologies LLC
-
United States
-
Information Technology & Services
-
100 - 200 Employee
-
Service Sales Specialist
-
Jan 2013 - Nov 2013
Part of a progressive Service Sales team providing Fortune 500 Managed IT services for small to medium size businesses. Part of a progressive Service Sales team providing Fortune 500 Managed IT services for small to medium size businesses.
-
-
-
The Toro Company
-
United States
-
Machinery Manufacturing
-
700 & Above Employee
-
Buyer/Parts Coordinator/Associate Supply Analyst (via Randstad)
-
May 2012 - Jan 2013
• Ensured smooth flow of information and materials between Toro and Supply base by effectively coordinating between fellow Buyers/Commodity Managers and Suppliers. • Acquired specific RFQ information from former vendors of the recently acquired businesses and used that information to fulfill part requests from customers. • Used SAP to facilitate the research and ordering process through the accurate inputting of parts and vendor data and the releasing of Purchase Orders and Schedule Agreements based on the needs of the plants and distribution centers. • Expediting the delivery of material from suppliers along with follow up on ETA dates. • Reported on weekly and monthly metrics such as fill rate, backorders, pending orders, financial objectives and other inventory goals with the director level management teams. • Supported the ongoing procurement of service parts in quantities sufficient to maintain the 98% customer service fill rate requirements at a minimum financial investment. • Acted as a point of contact for suppliers with questions related to delivery and receipt of goods.
-
-
-
Thomson Reuters
-
Canada
-
Software Development
-
700 & Above Employee
-
Area Supervisor
-
Mar 2002 - Dec 2011
• Leader of the Print Quality Continuous Improvement project team responsible for performing root cause analysis of problems to identify cost saving initiatives, recommending process/procedural changes, implementing changes and sustaining changes. • Leader of the project team responsible for the planning, implementation and operations of newly acquired print services and equipment for Thomson CompuMark. • Trained and developed a cross functional team to maintain the levels of quality and service associated with the Thomson CompuMark, while continually promoting the use of Lean Manufacturing tools such as VSM of current and future states, 6S and Poka-Yoke and Six Sigma methodologies which included DMIAC to solve problems. • Developer and Implementer of Quality @ the Source program within manufacturing that generated and documented SOP’s to drive continuous improvement and standardization of work practices in the workflow process. • Responsible for communicating with departments and varied management levels throughout the organization as to the current status with regards to scheduled work completed, deterrents that are hindering production, quality concerns with suggested resolutions and continuous improvement efforts. • Maintained a workforce engaged in achieving departmental goals for production, quality, waste and safety. • Leader of the quality project team which implemented a seamless integration of the new quality processes and workflow within the entire manufacturing facility. • Responsible for identifying opportunities, developing strategies, coordinating teams and implementing cost saving initiatives across several areas of the manufacturing facility. • Lead equipment acquisition project team in the planning, purchasing, installing and commissioning of several capital equipment improvement projects.
-
-
-
Tech Services International
-
Minnesota
-
Marketing Area Manager/Territory Sales Manager
-
Aug 1998 - Mar 2002
• Generated revenue and met profit objectives in the North Central Territory (consisting of Illinois, Wisconsin, Minnesota and North & South Dakota). • Project leader that trained and guided field engineers through the sales cycle. • Developed sales plans and budget\profit objectives for the North Central territory. • Negotiated service contracts and equipment sales. • Mentored new employees and was a liaison between the corporate office and the field organization. • Generated revenue and met profit objectives in the North Central Territory (consisting of Illinois, Wisconsin, Minnesota and North & South Dakota). • Project leader that trained and guided field engineers through the sales cycle. • Developed sales plans and budget\profit objectives for the North Central territory. • Negotiated service contracts and equipment sales. • Mentored new employees and was a liaison between the corporate office and the field organization.
-
-
-
Access Corporation
-
Greater Minneapolis-St. Paul Area
-
Senior Service Engineer
-
Jun 1997 - Aug 1998
• Installed, serviced and maintained various pieces of equipment in the pre-press and document archiving environment. • Developed and implemented service level standard operating procedure troubleshooting program. • Installed, serviced and maintained various pieces of equipment in the pre-press and document archiving environment. • Developed and implemented service level standard operating procedure troubleshooting program.
-
-
-
Primesource
-
Greater Minneapolis-St. Paul Area
-
EPS Service Engineer
-
Mar 1996 - Jun 1997
• Installed, serviced and supported high-end graphic systems as well as coordinated service and installation of front-end workstations, networks and fileservers. • Team Leader engaged in outsourcing of equipment service on an overflow basis. • Designed and implemented an electronic service reporting system on the branch level. • Installed, serviced and supported high-end graphic systems as well as coordinated service and installation of front-end workstations, networks and fileservers. • Team Leader engaged in outsourcing of equipment service on an overflow basis. • Designed and implemented an electronic service reporting system on the branch level.
-
-
-
DuPont
-
United States
-
Manufacturing
-
700 & Above Employee
-
Senior Field Service Engineer
-
Nov 1990 - Mar 1996
• Installed, serviced and supported color graphic systems as well as maintained a preventative maintenance schedule for existing equipment. • Reduced calibration time on product line through procedural and process revisions. • Team Lead that coordinated service for problem sites within the region. • Recognized region-wide expert on scanner optics related issues and conventional imaging equipment as lead trainer • Installed, serviced and supported color graphic systems as well as maintained a preventative maintenance schedule for existing equipment. • Reduced calibration time on product line through procedural and process revisions. • Team Lead that coordinated service for problem sites within the region. • Recognized region-wide expert on scanner optics related issues and conventional imaging equipment as lead trainer
-
-
-
DuPont & Fuji Electronic Imaging Company
-
Manchester, New Hampshire
-
Scanner Options Test Technician
-
Aug 1988 - Nov 1990
• Tested and installed optional equipment for color scanning systems. • Developed various test procedures and fixtures to facilitate training. • Organized and updated the release of new software and firmware revisions Additional Training and Recognition • Lean Six Sigma Black Belt Certification • Six Sigma Green Belt Certification • Lean Manufacturing trained – 5S/6S, VSM, Kaizen, QRM and Quality @ the Source • Lean Manufacturing Instructor • Erickson & Co (APS) Analytical Problem Solving/Operative Management trained • Trained in Karrass Effective Negotiating.
-
-
Education
-
Saint Mary's University of Minnesota
Bachelor Degree, Science Business Administration -
New Hampshire Technical Institute
Associates Degree, Science Electronic Engineering Technology
Community
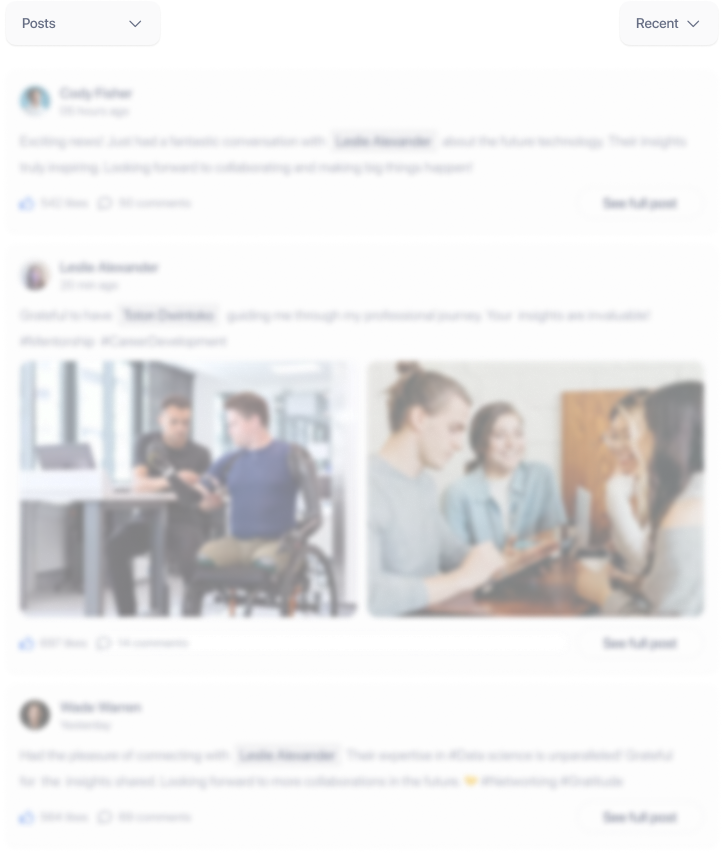