Bruce Bailey
Quality Engineer Manager - Spaceport Operations at Virgin Galactic- Claim this Profile
Click to upgrade to our gold package
for the full feature experience.
Topline Score
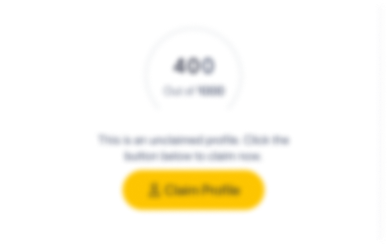
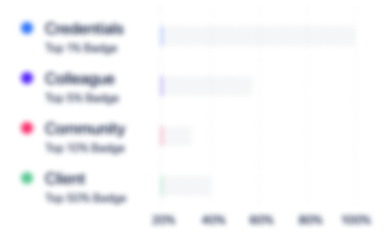
Bio


Experience
-
Virgin Galactic
-
United States
-
Aviation and Aerospace Component Manufacturing
-
700 & Above Employee
-
Quality Engineer Manager - Spaceport Operations
-
Oct 2021 - Present
• Supervised a 10-member Quality Assurance team, maintaining product quality and customer satisfaction while managing responsibilities. • Ensured compliance via AS9102 First Article Inspections management and team oversight. • Implemented 800+ revised processes, managing reviews and amendments. • Presented weekly spaceport chart updates on trend data, ASLTs, and other key concerns. • Collaborated with diverse teams, achieving results through visionary leadership. • Monitored quality metrics proactively, addressing trends in multiple programs. Held title to: QA Chief Inspector, Supplier QE, Supplier QA, Auditor & Trainer: Responsible for Managing nine (9) QA aircraft inspectors. Maintaining timekeeping, Responsible for overall spaceport MRB nonconformance cage inventory, Responsible for: Receiving inspection of deliverables, Responsible for supplier non conformances Internal personnel concerns Review and amend procedures, Responsible for NDT / QA concerns by operations, engineering, manufacturing. The overall site quality of products, services and processes used to maintain the spaceships. Ensuring all the written procedures and work instructions are updated / maintained Providing training for quality processes and implementation Ensuring follow thru of processes Reviewing, auditing and approval of Maintenance Instructions, Final review of all Spaceship vehicle build paperwork, and Engineering Drawings Promoted teamwork among others. Creative problem solver that participated, encouraged teamwork, Customer focus skills - worked with a diverse set of support groups, customers and suppliers. Collaborated with various Virgin Galactic groups to address non-conformance problems with processes and procedures to mitigate issues as well. as avoid maintenance delays and maintain compliance. Utilizes Word, PowerPoint, Excel, Reliance, TipQA… etc. Show less
-
-
-
L3Harris Technologies
-
United States
-
Defense and Space Manufacturing
-
700 & Above Employee
-
Program Quality Engineer Halo Compass Call Crossdeck And Cmmars
-
Nov 2020 - Oct 2021
• Led internal audits for AS9100 compliance, using results to enhance company performance through process evaluations. • Applied 8D Root Cause Analysis for effective corrective actions identification. • Conducted AS9102 First Article Inspections following industry standards. • Streamlined program time management by analyzing task duration, dependencies, resource allocation, and bottlenecks, considering project objectives. • Ensured FAI report completion, verifying inspection data before customer submittal through meticulous oversight of the entire process. • Performed RCCA analyses with Reliability Engineering, Supplier Quality, and Manufacturing Engineering teams. • Planned product realization meticulously, exceeding requirements and considering all factors. • Mastered program chart presentations, showcasing various items (ZDP, NoE, CAR, SCAR). • Served as auditor for HALO, Compass Call, CMMARs programs, maintaining high standard. • Oversaw site quality, services, and processes with subcontractors like U.S Air Force. • Implemented preventative actions through audits, PFMEA's, and cross-functional teams. • Collaborated on product realization in high-tech arena following strict guidelines. • Developed clear procedures and work instructions for streamlined operations. • Analyzed monthly metrics for necessary actions to improve quality standards. • Conducted audits of quality procedures and functions to ensure compliance. • Sustained quality metrics, addressed undesirable trends proactively. • Utilized Lean Six Sigma for continuous quality improvement. Show less
-
-
-
L3 Technologies
-
United States
-
Defense and Space Manufacturing
-
700 & Above Employee
-
Software Quality Assurance Engineer
-
Aug 2017 - Apr 2019
Program assignments included: Risk assessment to support technical project delivery Supporting and conducting ISO 9001 audits Knowledge of US government contract technical products and services Interfacing with technical, management personnel and government (DCMA) at all levels of responsibility Supporting additional models and standards, including CMMI and AS9100 Process development in a highly collaborative environment Provide training support for quality processes and implementation Vibration Lab (GPS III): Floor support: Assisted in initial installation of components for Vibe Lab Quality Engineer for: o Removal and installation of components to change axis settings during X, Y and Z testing o During testing of X, Y, and Z testing Trained multiple Quality Engineers on the processes of Vibe Lab before during and after testing as well as entering and exiting of lab Software (GPS III and OCX programs): Software Quality Engineering (SQA) o Floor support: o Team member for various software installations o SQA witness for script runs (software integration testing, run for record) o Off-line data review (ODR) o After test review of documents to ensure follow thru of processes Mentor for new software personnel Ensures procedures, processes, planning and quality inspection points have been implemented o Reviewing Software Safety Assessments, Hazard Analysis, Safety Assessment Reports, Technical and Operator’s Manuals o Auditing team member to written processes such as Software Safety Assessments, Hazard Analysis, Safety Assessment Reports, Technical and Operator’s Manuals o Experience in Software Development Lifecycles (Agile, Waterfall) Experience working with a military customer. Experience in Process and performance measurement: developing, collecting and analyzing metrics. Experienced in validating Software requirements sell-off and associated tool usage (such as DOORS, RTM, JIRA) Show less
-
-
-
Lockheed Martin
-
United States
-
Defense and Space Manufacturing
-
700 & Above Employee
-
Program Quality Engineer
-
Mar 2015 - Oct 2016
• Improved Quality Management System (QMS) performance through internal audits ensuring AS9100 compliance for Aviation Space & Defense Organizations' requirements. • Streamlined A/MH-6 program by optimizing SOW, PWS, IMS/IMP, schedules, subcontractors, manufacturing, risk management, OBS/WBS, and BOEs. • Managed a team of four as acting QA Lead in the mission-critical AH6 program, requiring exceptional leadership and communication. • Conducted AH6 program audits, ensuring adherence to written processes. • Accelerated task completion with leadership, fostering teamwork among diverse groups, proactively solving problems, and streamlining processes using innovative strategi. • Partnered with LMC & Boeing groups resolving non-conformance problems using Word/PowerPoint/Excel tools; mitigated issues avoiding product delays/compliance concerns. • Reviewed Software Safety Assessments, Hazard Analysis reports, and Technical/Operator's Manuals, ensuring accuracy, effectiveness, and usefulness for the intended. • Planned product realization, managed risks, met requirements on schedule through resource allocation, cross-functional coordination, and progress monitoring. • Ensured adherence to up-to-date industry standards and best practices through meticulous execution of procedures and inspections. • Acted as the on-site Supply Quality Engineer (SQE), ensuring top quality for all products, services, and processes. • Initiated PQDRs to document and address non-conformant government-furnished equipment identified during. • Chaired CAB meetings proactively, preventing issues from escalating, and maintaining open communication. • Collaborated to ensure process conformance across suppliers and customers. • Coordinated NCD/RCCA efforts for high-quality standards and improvements. Show less
-
-
-
GKN Aerospace
-
United Kingdom
-
Aviation and Aerospace Component Manufacturing
-
700 & Above Employee
-
Program Quality Engineer
-
Oct 2014 - Apr 2015
• Resolved deburr issues on plant floor for the F-18 program through hands-on support. • Streamlined F-18 program processes, boosting productivity and procedural adherence. • Addressed nonconformance using 5Y, fishbone methodology, and implemented solutions. • Spearheaded F-15 and F-18 parts management, ensuring efficiency and quality. • Audited F-15 & F-18 gantry processes, ensuring parts accuracy & efficiency. • Collaborated with GKN groups to resolve issues, prevent delays, and ensure complianc. • Created visual aids from updated PS specs/TUIs, enhancing clarity during inspections. • Conducted gap analysis of weld TUIs & PS specs against manufacturing best practices. • Ensured procedure implementation, planning, and build compliance inspections. • Utilized leadership to expedite tasks, maintaining strong team communication. • Established VFT maintenance logbook, enhancing organization & accountability. • Developed strategy for streamlining production processes across departments. • Reviewed relevant documentation for correct referencing in GKN orders Show less
-
-
-
Northrop Grumman
-
United States
-
Defense and Space Manufacturing
-
700 & Above Employee
-
Quality Engineer Supply
-
Feb 2011 - Oct 2014
• Formulated matrix accounting for 80% cash expenditure in ILMD sector. • Mobilized team development by creating Supplier Corrective Action Report process and training primary supplier (KC10) in correct responses/reply times for SCARs. • Reinforced product, service, and process quality in the US Air Force's KC-10 Program subcontract as a Quality Auditor, ensuring every aspect. • Modernized KC-10 audit checklists and integrated nonconformance tags into a central database, meticulously reviewing and updating components. • Customized KC-10 supplier nonconformity tags, developing inventory control for quarantined items, ensuring that. • Streamlined supplier and management communication for KC10 program's SCAR/i-CAR stat. • Initiated 5S time management initiative during aircraft maintenance operations. • Augmented collaboration with Northrop Grumman on non-conformance issues using Word, PowerPoint, Excel, M.E.S., and SAP daily. • Reviewed Software Safety Assessments, Hazard Analysis, Reports, and Manuals, ensuring they met the highest standards. • Elevated conformance by collaborating with stakeholders to verify and validate essential processes and procedures. • Bolstered program management with efficient floor support and interpersonal skills. • Ensured implementation of procedures, planning, and quality inspection in projects. Show less
-
-
-
VOUGHT AIRCRAFT INDUSTRIES INC
-
United States
-
Aviation and Aerospace Component Manufacturing
-
1 - 100 Employee
-
Quality Engineer
-
Jun 2009 - Feb 2011
• Conceptualized and implemented Catia5 model design conformance by interfacing with engineering, supervision, suppliers, and customers in the 787 Dreamliner Program. • Utilized R3, Waterfall, and Insight programs to identify and resolve W/T issues using a systematic approach, including thorough examination. • Directed tracking of Supplier Corrective Action Requests (SCARs), internal requests (i-CARs), and supplier responses in Boeing 787 program. • Served as Boeing 787 Site RCCA coordinator. • Boosted Gulfstream (GIV) Wing Program productivity by updating Foreign Object Debris (FOD) procedures and analyzing tool control and inventory management. • Instituted procedures, planning, quality inspection points in design models for build compliance, demonstrating excellent communication skills. • Partnered with an expert Program Manager, I efficiently created and executed a thorough Foreign Object Debris (FOD) prevention plan. • Collaborated with Vought engineering groups to resolve non-conformance issues during production. • Innovated Notice of Escape (NoE) spreadsheet process development and implementation. • Navigated diverse environments with interpersonal and conflict management skills. • Played a key role in calibrating hand tools in MRB quarantine areas. Show less
-
-
-
Eclipse Aviation, LLC
-
United States
-
Aviation and Aerospace Component Manufacturing
-
1 - 100 Employee
-
Quality Assurance Quality Control Engineer
-
Jan 2007 - Jun 2009
Quality Engineer, – Program management for Process /Supplier control • Developed, evaluated, configured, and verified work sequences, inspection points, and process specifications prior to releasing work instructions. • Interfaced with quality assurance department to meet final acceptance, functional test acceptance, and conformity inspection standards. • Validated serialized parts and dimension measurement documentation and installations. Generated 8130-9 (first article) and statements of conformity following completion and final acceptance of engineering prints. • Member of Materials Review Board (MRB). • Assisted in training of employees on S.A.P. computer systems. • Worked closely with manufacturing to process non-conformance issues and corrective action plans to ensure effective production. • Member of the CAR committee. o Team member in orchestrating aircraft incident information procedures o Team member; Developed inventory control accountability for quarantined items Show less
-
-
Community
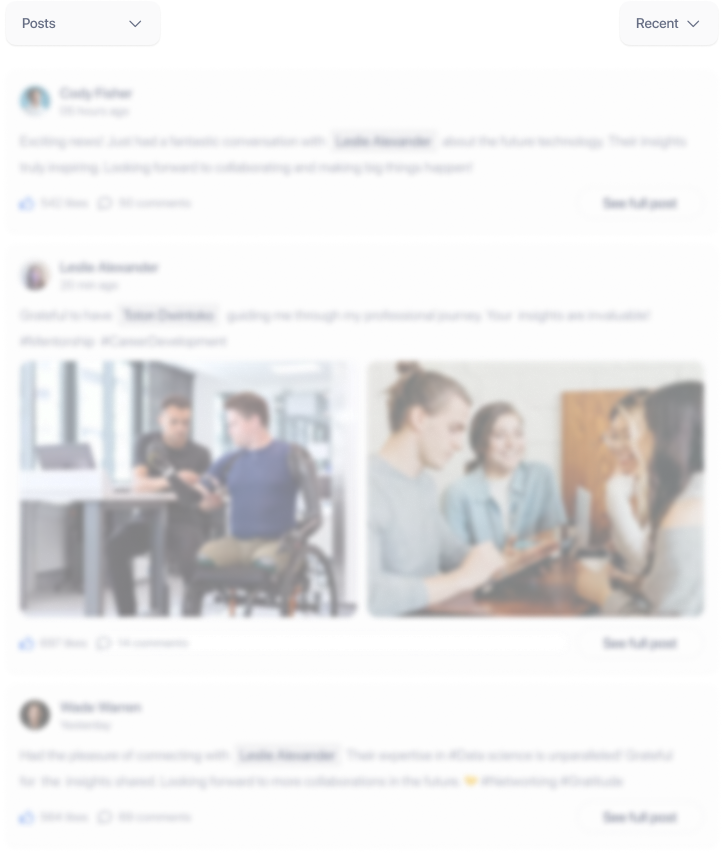