Brooks Jones
Buyer - Procurement Specialist at ATA Aerospace, LLC.- Claim this Profile
Click to upgrade to our gold package
for the full feature experience.
Topline Score
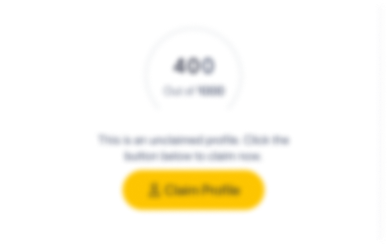
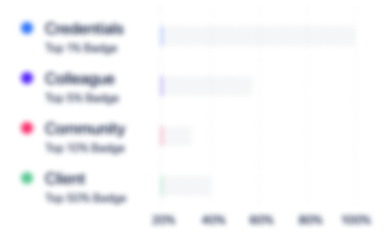
Bio

Eric Baum
Brooks and I worked very closely together managing and fulfilling a long-term, multi-million dollar, high profile commercial aerospace contract for 3+ years. Brooks is cool under pressure and his wealth of experience and vision repeatedly convert complexities into simplicities. He is very easy to work with and always puts his fellow co-workers and business partners first. He is respectful towards others and a man of his word. It was a pleasure to work with Brooks and I wish him the best.

Eric Baum
Brooks and I worked very closely together managing and fulfilling a long-term, multi-million dollar, high profile commercial aerospace contract for 3+ years. Brooks is cool under pressure and his wealth of experience and vision repeatedly convert complexities into simplicities. He is very easy to work with and always puts his fellow co-workers and business partners first. He is respectful towards others and a man of his word. It was a pleasure to work with Brooks and I wish him the best.

Eric Baum
Brooks and I worked very closely together managing and fulfilling a long-term, multi-million dollar, high profile commercial aerospace contract for 3+ years. Brooks is cool under pressure and his wealth of experience and vision repeatedly convert complexities into simplicities. He is very easy to work with and always puts his fellow co-workers and business partners first. He is respectful towards others and a man of his word. It was a pleasure to work with Brooks and I wish him the best.

Eric Baum
Brooks and I worked very closely together managing and fulfilling a long-term, multi-million dollar, high profile commercial aerospace contract for 3+ years. Brooks is cool under pressure and his wealth of experience and vision repeatedly convert complexities into simplicities. He is very easy to work with and always puts his fellow co-workers and business partners first. He is respectful towards others and a man of his word. It was a pleasure to work with Brooks and I wish him the best.

Experience
-
ATA Aerospace, LLC.
-
United States
-
Aviation and Aerospace Component Manufacturing
-
1 - 100 Employee
-
Buyer - Procurement Specialist
-
Mar 2021 - Present
•Perform a variety of buying/purchasing tasks involving materials, equipment, hardware, supplies or services AT NASA Godard Space Flight Center •Responsible for all procurement actions within the limits of Buyer’s authority •Review purchase requisitions •Solicit proposals and quotes from vendors •Evaluate bids and negotiate price, delivery, Milestone Payments •Provide the status of orders to internal customers •Ensure acquisitions are in compliance with company CPSR Policies and Procedures •Archive and maintain purchase agreement files •Support audits on an as needed basis •Coordinate with the Accounting, Quality, Planning, and Receiving Departments as required to resolve issues with Purchase Agreements •Support internal customers with the development of Bill-of-Materials (BOM) Show less
-
-
-
TCOM, L.P.
-
United States
-
Defense and Space Manufacturing
-
200 - 300 Employee
-
Senior Buyer
-
Mar 2020 - Mar 2021
• Works with established subcontractors to procure various services in support DoD contracts RFQ and RFP for competitive price to meet quality standards set forth in QA codes for all machines/fabricated items • Implements contracting strategies and contracts for facilities management, professional services, and other services in support of capital projects for our Customer. • Reviews service reports to confirm services contracted were rendered in full and identify if additional follow up is needed. Forwards recommendations to Supply Chain Manager and proceeds with direction issued • Ensures that all contract administration procedures are followed and executed in a professional manner. • Maintains procurement records, such as items or services purchased, costs, delivery, product quality or performance, and inventories. • Continually tracks ticket statuses to ensure all schedules are adhered to and tickets are completed within compliance parameters. • Maintain records of business transactions and product inventories, reporting data to companies or government agencies as necessary. • Discusses defective or unacceptable services with senior management to determine appropriate action and engage subcontractors to take corrective action. • Maintain/update Costpoint7 adhere to DFAR and DCMA Show less
-
-
-
FILAMATIC
-
United States
-
Machinery Manufacturing
-
1 - 100 Employee
-
Technical Buyer
-
2018 - Mar 2020
Prepare and process requisitions and purchase orders based on demand for standard, custom and stock items Use ERP system to maintain accurate records of goods ordered Negotiate vendor pricing, delivery, payment terms and stocking levels Identify alternate sources for any current supplier, including international Monitor and expedite purchases to ensure timely delivery per production schedule Conduct on-site vendor visits, set up and review vendor performance Propose improvements to the current purchasing system that will improve vendor relationships and lower the cost of doing business Review purchase order claims and contracts for conformance to Company policy Analyze market and delivery systems in order to assess present and future availability Show less
-
-
-
Hughes Network Systems
-
Gaithersburg, MD
-
Commodity Manager / Buyer III
-
Jan 2018 - Jun 2018
Source and obtain direct materials, components, equipment, and services to support manufacturing facility. Analyze MRP/ERP Reports to make buying decisions based on lead time, usage and material availability. Process requisition and purchase orders in a timely manner. Acquire and maintain technical and cost driver knowledge of products purchased. Coordinate purchasing activities with managers and engineering departments to insure quality inventory and schedule goals are met. Source, evaluate and negotiate with suppliers to achieve lowest cost of ownership, quality, and service meet schedule requirements. · Evaluate and measure supplier performance to ensure contractual commitments are met. Maintain positive relationships with suppliers and on-site visits as appropriate. Negotiate contacts for material and equipment purchases in a cost-effective and timely manner. Provide interactive link between corporate logistics, procurement, internal, external customers and suppliers. Show less
-
-
-
IGATE
-
Information Technology & Services
-
700 & Above Employee
-
Lead Senior Buyer
-
Apr 2014 - Nov 2017
• Control of 14 high volume suppliers delivering manufactured sheet metal and machined foorgingds for antithrusters for Boeing, Air Bus Pratt Witney and department of the Navy. • Demands from customers in cost-out and higher quality parts through engineering changes in material and manufacturing have created opportunities in sourcing to make new requirements from our engineering and manufacturing devisions • Cost-out of over $122K on two primary parts in builds for Boeing have been presented for 2015 - 2017 and development of three other material cost reductions are in development LTA, VPA & BPA used to control costs. • Full understaning and operations of Oracle 12 and the Supplier Chain Portaal (through GE) software as well as updating Line of Balance for production and scheduling forr on-time delivery • Close communication facilitated between my suppliers and our accounts payable department has led to faster payments allowing to take advantage of discounts on purchese as well . Show less
-
-
-
QinetiQ US
-
United States
-
Defense and Space Manufacturing
-
700 & Above Employee
-
Staff Buyer
-
Jul 2012 - Mar 2014
• Dedicated to a $27.5M buy for the NASA unit at Goddard SFC and adhering to strict government regulations in sourcing material and service for the James West Telescope system under FAR and DFAR audit principles • Assignment of purchase requisition as well as purchase orders to key personnel to develop best price, cost analysis and teaming subcontracts for implementation of material and services to the government • Devoted to have employees think outside the conventional and take ownership of their positions and empower the individual to make decisions. • Responsibilities toward presentations in multiple formats to facilitate communication to key personnel at all times and summarizing data to be less cumbersome and audience appropriate • Lead on partnership with accounting department to stay informed of the funding regimens for 126 projects per quarter and report data to the directorship of unit and program manager. Show less
-
-
-
Mav6
-
United States
-
Defense & Space
-
1 - 100 Employee
-
Inventory Managment Specialist
-
Nov 2011 - Jun 2012
Supply Chain Management of logistics material for DoD, Air Force contract of hardware and software systems utilized for integration for mission systems. Vendors such as Northrop, Lockheed, Dell, Harris, Crystal, Sun, Cisco, HP and assorted hardware. In charge of development and compiling spreadsheets for System Lead of Weekly Open Order Reports, Exception Reports, Monthly delivery reports Weekly notices sent to suppliers for upcoming deliveries to assure on time delivery of material and keeping communication open with same on issues that may hinder quality or delivery. Receipt of material with assignment of NSN (National Stock Number) for inventory as well as dedication top-level drawings to BoM on each sub-unit on Mission Payload project. Flow down of parts to kits by breaking down to top level, mid level assemblies for project. Have working knowledge of FilePro 11 database system and integration of same with DELTEK and Pentagon ERP systems. Show less
-
-
-
Eaton
-
Ireland
-
Appliances, Electrical, and Electronics Manufacturing
-
700 & Above Employee
-
Buyer
-
Nov 2007 - Oct 2011
Optimize supply chain operation and garner savings through supply chain management of logistics for raw metal material in aerospace production of flex, ducting, couplings, and flanges for key clients, including General Electric, Pratt & Whitney, Boeing, Rolls Royce, Lockheed Martin Optimize supply chain operation and garner savings through supply chain management of logistics for raw metal material in aerospace production of flex, ducting, couplings, and flanges for key clients, including General Electric, Pratt & Whitney, Boeing, Rolls Royce, Lockheed Martin
-
-
-
Shimadzu Scientific Instruments
-
United States
-
Biotechnology
-
400 - 500 Employee
-
International Procurement Specialist
-
Feb 2000 - Jul 2007
Led coordination of component-level and finished products in logistics for shipments to Japan and China from North and South America. Wrote vendor contracts and issued purchase orders. Managed Great Plains MRP system. Ensured compliance with the European Union’s Waste Electrical and Electronic Equipment (WEEE) legislation for 5123 components, listing all hazardous substances by percentage content for each part in export parts list. Increased exports from North America office from $2,500,000 to $8,900,000 and vendor base from 67 to 138 over three-year period. Show less
-
-
-
PACE Worldwide
-
United States
-
Appliances, Electrical, and Electronics Manufacturing
-
1 - 100 Employee
-
Buyer/Expeditor
-
1999 - 2000
Improved quality control and customer satisfaction by initiating use of Lean Manufacturing principles while enabling company to gain high turns in reducing on-hand inventory, as well as the ability to deliver “build to order” products Improved quality control and customer satisfaction by initiating use of Lean Manufacturing principles while enabling company to gain high turns in reducing on-hand inventory, as well as the ability to deliver “build to order” products
-
-
Education
-
TOWSON STATE UNIVERSITY
BS, ENVIRONMENTAL PLANNING/BUSINESS -
Baltimore Polytechnic Instsitute
Diploma, Engineering/Mathematics
Community
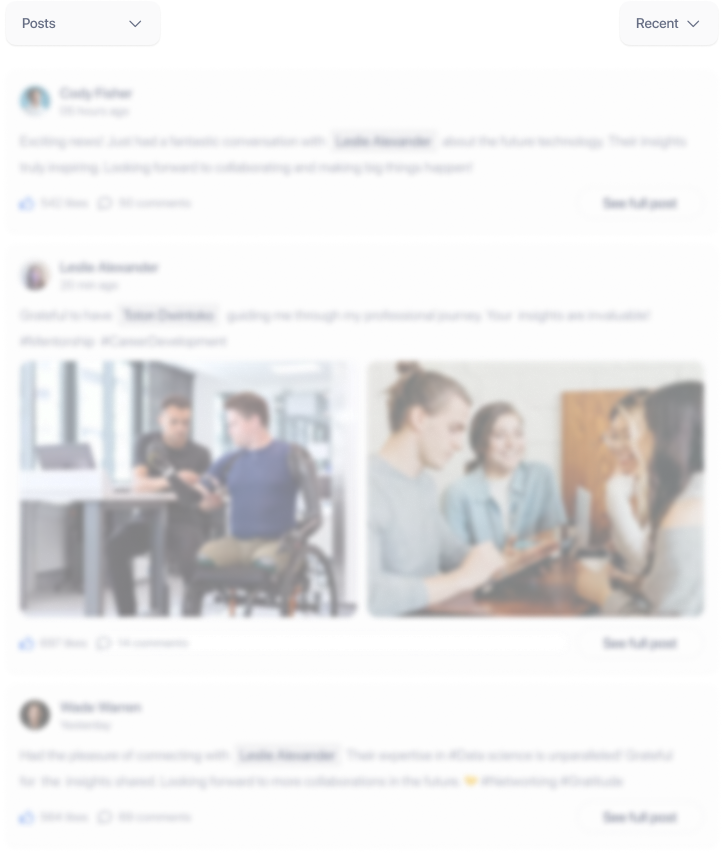