Brittany Feldman
Test Engineer at STOKE Space Technologies- Claim this Profile
Click to upgrade to our gold package
for the full feature experience.
Topline Score
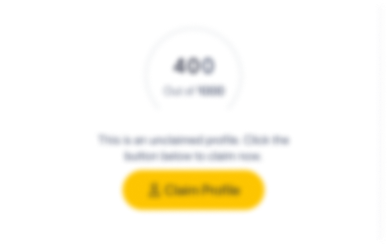
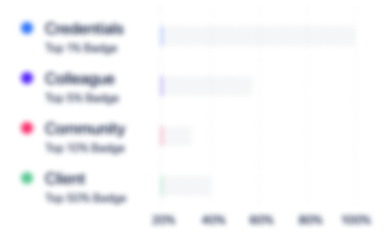
Bio


Experience
-
Stoke Space
-
United States
-
Defense and Space Manufacturing
-
1 - 100 Employee
-
Test Engineer
-
Jan 2022 - Present
-
-
-
BLUE ORIGIN
-
United States
-
Defense and Space Manufacturing
-
700 & Above Employee
-
Lead Systems Engineer and Director of Systems Engineering, New Glenn Stage 2
-
Aug 2018 - Jan 2022
Support Vehicle and Ground System Project Leads by carrying out systems engineering activities in accordance with Blue Origin standards and practices, engaging in tailoring required processes to complete tasks assigned including: • Requirements decomposition, analysis, traceability, and verification • Lead, organize and participate in gated design and production reviews • Streamline systems engineering processes such as the verification process and reduction of requirements • Coordinate changes across vehicle subsystems, stages, engine, and ground systemTeam management • Review resumes, lead interviews, and make hiring decisions for qualified candidates with a variety of experience • Delegate tasking across my team to meet company goals and schedule as well as grow individual team members • Resolve conflicts within and external to my team • Execute performance reviews
-
-
Bar Raiser
-
Jun 2016 - Jan 2022
Serve as non advocate on interviews across the company to insure Blue Origin hires high quality candidates. Train interviewees and hiring managers as needed. Trained new bar raisers. Ram interview debriefs. Served on over 200 interview panels.
-
-
Fluid Systems Test Engineer, Fluids Lab Manager, and Test Team Manager
-
Jan 2016 - Aug 2018
• Responsible for fluid subsystem and component level testing. Includes deriving test requirements from SMC-S-016, develop test plans and procedures from scratch, develop test setups, execute tests, and performing data review. • Continual improvement of document templates, processes, and procedures to increase team efficiency • Troubleshoot hardware anomalies and provide designers with feedback for design improvements • Performed root cause analysis and failure investigations. Some have resulted in design changes to flight vehicles to increase safety and reliability. • Participation in the entire design cycle of fluid systems including system architecture definition, failure modes and hazards analysis, conceptual design, integration, test and mission support. • Experience with pressurized systems > 3000 psia • Experience with cryogenic fluids such as liquid nitrogen, liquid oxygen, and liquid hydrogen • Understand and troubleshoot fluid and instrumentation systems such as valves, check valves, pressure transducers and thermocouples • Perform system hazard analyses and improve test setups to increase safety for personnel and hardware. • Identify opportunities for safety improvements and cost savings during testing. • Developed and taught technical courses in fittings and pressurized system safety • Direct technician and engineering work and coordinate with internal customers. Teams typically consist of two to six members. • Responsible for test schedule and test cost estimation for the fluid subsystem on the New Shepard vehicles which involve more than 250 components. • Responsible for Fluid Systems Laboratory including budget, forecasting and planning lab use, lab expansion, management of technicians, and maintenance of lab equipment
-
-
Integrated Test Operations Engineer
-
Mar 2014 - Dec 2015
• Define and execute tests to verify space vehicles (booster and crew capsule) are ready for launch• Author new test procedures, test plans, and test reports for various vehicle tests with a focus in high pressure testing for pneumatic and cryogenic systems• Incorporate redlines into existing test procedures to increase safety, quality and efficiency of tests• Conduct test readiness reviews and hazard analyses for test operations. Provide list of action items to test team members to increase the safety of the tests for both personnel and hardware. • Maintain test equipment in good working and clean condition. Test equipment includes, but is not limited to, fittings, in-line filters, flex hoses, pressure gauges, pressure panels, seals, cameras, and avionics cables.• Coordinate with groups across the company to define test requirements, execute tests, and test facility usage• Authored 17 test plans and procedures in the first 6 months of employment to test vehicle subsystems and integrated systems• Conducted roll control and escape guidance control system checkouts on the crew capsule one day ahead of schedule.• Led a team of 13 people to complete proof and leak testing of the pneumatic and cryo systems on the integrated PM4 vehicle two days ahead of schedule.• Incorporated redlines and lessons learned into test documentation 3 months ahead of schedule.• Procured and organized test equipment to save over 90 man hours during integrated testing of the first New Shepard vehicle.• Authored contingency planning document for vehicle hot fire and launch for over 150 off nominal situations• Served as an observer for launch rehearsals, provided suggestions to improve launch operations• Served as ground pneumatic system engineer for the New Shepard Vehicle's first flightMissions worked on:New Shepard M1 - April 29, 2015New Shepard M2 - November 23, 2015 (First rocket to vertically fly into space and land)New Shepard M3, M4, M5, M6 - relaunches of same rocket
-
-
-
SpaceX
-
United States
-
Aviation and Aerospace Component Manufacturing
-
700 & Above Employee
-
Propulsion Test Engineer
-
Aug 2012 - Mar 2014
• Operated test console for over 100 engine and stage tests, execute test procedures for leak checks, mechanical and electrical checkouts, and hot fire testing. Console time equated to more than 5000 hours. • Oversaw assembly of engines, engine components, and engine to stage integration. • Analyzed and reviewed data to ensure hardware and ground support systems were operating as expected. • Investigated anomalies and provided instructions to maintain facilities and reconfigure hardware as needed. • Authored procedures for product assembly and disassembly, pre-test and post-test inspections of a test article, and test stand operations. Interacted with personnel to ensure work instructions were accurate, safe, and comprehendible. Responsible for the Merlin Vacuum engine and Falcon 9 Stage 2 acceptance test procedures. • Worked with team members to author test procedure standards used by the entire company • Coordinated with responsible engineers to incorporate design changes to increase safety, system reliability, and workflow pace • Member of the Safety Committee, responsible for implementing safety modification on the test site • Worked with quality assurance group to bring test procedures, test operations, and test stand FMECA's up to AS9100 standards • Co-authored test engineer training documents. Training documents included a week by week schedule, review questions, and tasks for new engineers to learn the ropes. • Tested hardware for 11 successful Falcon 9 flights (flights 3-13)
-
-
-
Purdue University
-
United States
-
Higher Education
-
700 & Above Employee
-
Teaching Assistant for Aerospace Propulsion
-
Aug 2011 - Dec 2011
Assist the professor in academic duties such as holding office hours, answering homework questions, grading homeworks, etc. Assist the professor in academic duties such as holding office hours, answering homework questions, grading homeworks, etc.
-
-
-
SpaceX
-
United States
-
Aviation and Aerospace Component Manufacturing
-
700 & Above Employee
-
Propulsion Test Engineering Intern
-
May 2011 - Aug 2011
• Revised test procedures to improve efficiency, streamline test operations, and meet AS9100 standards • Executed revised test procedures paying particular attention for areas to further increase usability and efficiency by 20% • Investigated options and implemented solution for ground support equipment improvements to the Falcon 9 Stage 1 Stand to automate tank desiccant systems, increasing efficiency and hardware safety • Modified water tank ground support system by adding a tank isolation valve to increase functionality and protect the system during the winter • Led a team of technicians in the installation of thermal and acoustic suppression during Falcon 9 Stage 2 testing. Directed the team on installation of 8 separate custom fit blankets within 48 hours of test execution
-
-
-
United Space Alliance
-
United States
-
Defense and Space Manufacturing
-
700 & Above Employee
-
Environmental Control Systems Engineering Co-op
-
Jan 2009 - Aug 2009
• Led a team of technicians to find and repair a major refrigerant leak in the shuttle's ground cooling system involving isolating and draining refrigerant from vehicle's lines, pressurizing with gaseous nitrogen, and leak checking suspect joints. • Coordinated electrical work on the environmental control systems supporting orbiter processing facility • Operated shuttle ground support equipment during portable purge system verification tests • Modified portable purge unit from shuttle configuration to support Ares 1-X • Supported three shuttle launches and landings at Kennedy Space Center • Member of team that supported four shuttle missions and one Ares 1-X mission.
-
-
-
KBE+
-
Syracuse, NY
-
Engineering Intern
-
Jun 2008 - Aug 2008
• Developed procedures to assemble and disassemble gear dynamometers for maintenance. • Designed alignment tool for the dynamometers and modeled gears and gear box assembly in Solid Works • Developed procedures to assemble and disassemble gear dynamometers for maintenance. • Designed alignment tool for the dynamometers and modeled gears and gear box assembly in Solid Works
-
-
Education
-
Purdue University
Master's Degree, Aerospace Engineering, Rocket Propulsion -
Embry-Riddle Aeronautical University
BS, Aerospace Engineering, Astronautics
Community
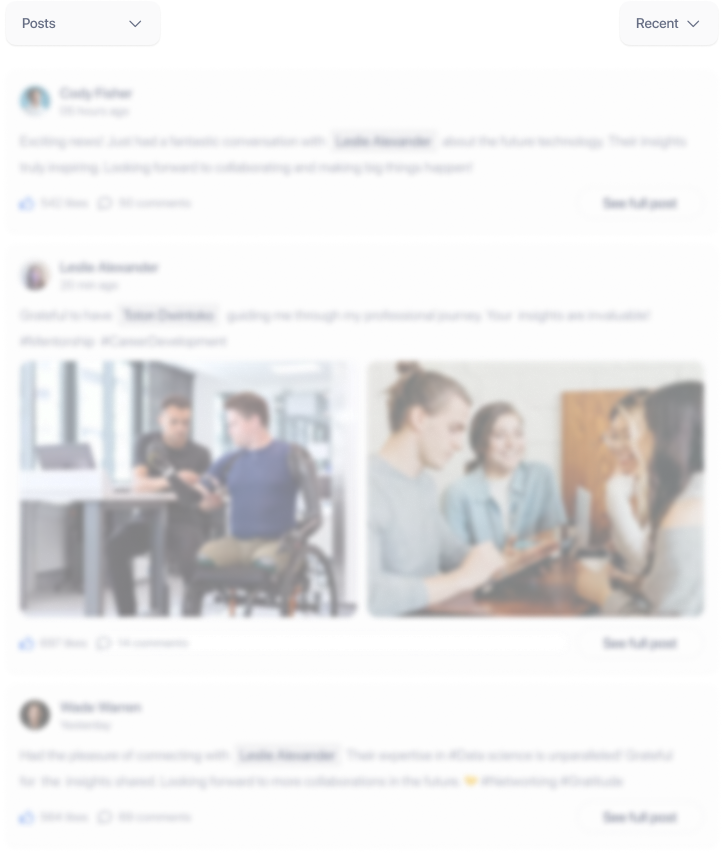