Brian Scheel
at Garon Plastics- Claim this Profile
Click to upgrade to our gold package
for the full feature experience.
Topline Score
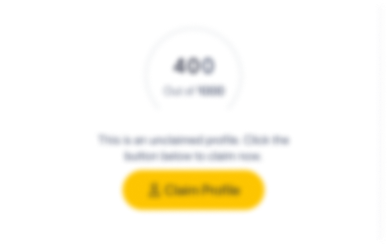
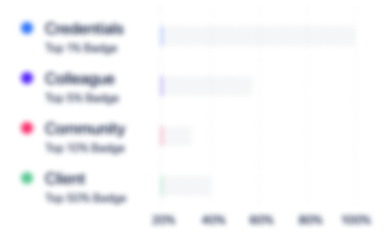
Bio

Don Fisher
I had the pleasure of working with Brian at our facility in Whitby Ontario. At that time Brian was a Process Engineer and I was the Quality Manager. Brian was very knowledgeable, always approachable, and supportive of anyone in need of his expertise. The attributes along with his strong work ethics made Brian a sought after member of any team and a valued member of the organization.

Brett Schnur
Brian was a great hands on supervisor. He knew how to encourage his people and be a buffer to allow his people to grow.

Don Fisher
I had the pleasure of working with Brian at our facility in Whitby Ontario. At that time Brian was a Process Engineer and I was the Quality Manager. Brian was very knowledgeable, always approachable, and supportive of anyone in need of his expertise. The attributes along with his strong work ethics made Brian a sought after member of any team and a valued member of the organization.

Brett Schnur
Brian was a great hands on supervisor. He knew how to encourage his people and be a buffer to allow his people to grow.

Don Fisher
I had the pleasure of working with Brian at our facility in Whitby Ontario. At that time Brian was a Process Engineer and I was the Quality Manager. Brian was very knowledgeable, always approachable, and supportive of anyone in need of his expertise. The attributes along with his strong work ethics made Brian a sought after member of any team and a valued member of the organization.

Brett Schnur
Brian was a great hands on supervisor. He knew how to encourage his people and be a buffer to allow his people to grow.

Don Fisher
I had the pleasure of working with Brian at our facility in Whitby Ontario. At that time Brian was a Process Engineer and I was the Quality Manager. Brian was very knowledgeable, always approachable, and supportive of anyone in need of his expertise. The attributes along with his strong work ethics made Brian a sought after member of any team and a valued member of the organization.

Brett Schnur
Brian was a great hands on supervisor. He knew how to encourage his people and be a buffer to allow his people to grow.

Experience
-
Garon Plastics
-
Australia
-
Plastics Manufacturing
-
1 - 100 Employee
-
-
Mar 2023 - Present
Responsible for the success of the Operations at Garon Plastics. Oversee all aspects of manufacturing, employ Lean methodologies to reduce waste, errors and variability, and manage KPIs to identify trends and implement process improvements. Ensure compliance with regulatory requirements, promote a culture of continuous improvement, and resolve manufacturing issues to ensure our safety, quality and efficiency exceed the expectations of all stakeholders.
-
-
-
Feb 2016 - Present
Responsible for driving internal projects to completion. This includes continuous improvement initiatives with an emphasis on I4.0 and digitization, warehouse, factory and office layout optimization, capital equipment installations and lean manufacturing systems.
-
-
-
Ultra Manufacturing
-
Canada
-
Motor Vehicle Manufacturing
-
1 - 100 Employee
-
Process Engineer - Injection Moulding
-
Jun 2014 - Jan 2015
Recruited by this injection moulding company to provide hands-on experience and knowledge of continuous improvement, process flow and problem solving. Directly responsible for the performance of 15 assembly stations, utilizing injection moulding machines, automation, jig/fixtures, end-of-arm-tools, paint systems and direct labour. Responsible for customer satisfaction and corrective action reports for automotive OEMS including Toyota, Ford and Chrysler. Deployed camera systems and mechanical error proofing methodologies to ensure consistent quality. Redesigned SOPs, critical parts, mechanisms, and actuators to optimize solutions and maximize worker efficacy. Managed component and one piece flow, strategically installing conveyors and chutes within the plant and adjusting workstations to improve ergonomics and ease of work by operators while expediting production. Strategized ways and means for the improvement and automation of production processes and contributed invaluably to error proofing, commonization of parts, and labour optimization throughout the sites assembly stations. Show less
-
-
-
BeneFACT, a part of Business Improvement Group
-
Canada
-
Accounting
-
1 - 100 Employee
-
Technical Consultant - Manufacturing
-
Nov 2012 - Jun 2014
BeneFACT Consulting Group is a team of financial and technical experts dedicated exclusively to helping Canadian companies maximize their R&D refunds. We offer the most comprehensive end-to-end SR&ED claim preparation services in the industry. Responsibilities included: • Analyzing and reviewing clients’ technologies and identification of eligible SR&ED projects • Conducting detailed technical interviews in a specific format with Engineers, Technical Managers, Project Managers, Plant and Operations Managers • Analyzing, synthesizing, articulating and conveying technical information • Working with our financial team to ensure maximized SR&ED benefits are claimed for our clients Show less
-
-
-
ZF Lemforder Pty Ltd
-
Adelaide, Australia
-
Manufacturing Engineer - Chassis Assembly
-
Sep 2011 - Jun 2012
Completed a 10-month contract with this automotive assembly company providing oversight of project management, AutoCAD design, just-in-time (JIT) fulfilment, and just-in-sequence (JIS) processes for the assembly of GM(Holden) chassis and front brake corner parts while continuously sourcing and capitalizing on opportunities for process and productivity improvement. Took the lead in modifying assembly line processes to accommodate new vehicle part models, disassembling new product samples to components to achieve commonization and reduce the risk of errors using new methods and tools. Led a series of continuous improvement projects and chaired routine meetings to maintain adherence with project plans, schedules, and quality standards while promoting team engagement in ongoing improvement initiatives. Coordinated efforts with customers, suppliers, and internal partners to ensure the deployment of the leanest, most cost effective error-proofing methods in order to achieve consistent on-time product delivery. Show less
-
-
-
Woodbridge Foam Corporation
-
Mississauga, Ontario
-
Technical Manager
-
Mar 2011 - Jul 2011
Completed a 5-month contract for the management of manufacturing processes involved in the production of a PolyBLOCK proprietary polyurethane construction block system from incoming chemicals to outgoing finished goods. Presided over budgeting and project management while directing the day-to-day activity of the manufacturing operators and monitoring production rates, staffing, inventory control, shipping and receiving functions. Drove product development changes in tooling, product design and formulation to tailor finished goods to client-specific requirements and coordinated chemical intake to ensure the consistent availability of necessary materials. Implemented LEAN processes and steered continuous improvement initiatives to reduce the level of scrap produced from 15% to 5% by adjusting heating, cooling, venting and clamping mechanisms. Retooled chemical ratios and catalyst packages, fine-tuning agitation times and process parameters to yield a higher quality product and minimize waste. Show less
-
-
-
-
-
Jun 2005 - Jun 2010
Enhanced performance of the Woodbridge Adelaide facility from the bottom quartile to the top quartile in the space of five years in the “Best in Class” World’s Best Practice System measured against 26 global facilities. Undertook a massive tooling standardization project, guiding the process from conception to completion, working hands-on with technicians and engineers to improve standardization from 50% to 100% across 200+ tool variants. Reviewed existing H&S procedures and policies and delivered up-to-date training in hazard identification and emergency response, serving as a subject matter expert in the chemicals used in production of polyurethane foam seating. Planned and administered departmental budgets for chemical usage, equipment, and personnel, assuming authority for candidate interviewing and selection of process engineers and technicians. Secured award-worthy performance through systematic improvements in scrap reduction, chemical usage, repair rate, and variance reduction in the line along with the implementation of standardized tools, processes, and venting patterns. Retooled equipment to achieve optimal performance and chemical delivery to meet the strictest of quality standards while balancing chemical formulations to ensure physical properties met customer specifications. Trained and educated plant engineers and technicians in the chemical processes and catalysts in order to reduce the incidence of defects and variations and in turn drive down labour resources required for high quality foam production. Show less
-
-
-
Jan 2004 - Jun 2005
-
-
-
May 2000 - Jan 2004
-
-
Education
-
Ryerson University
Bachelor, Chemical Engineering -
Ryerson University
Chemical Engineering
Community
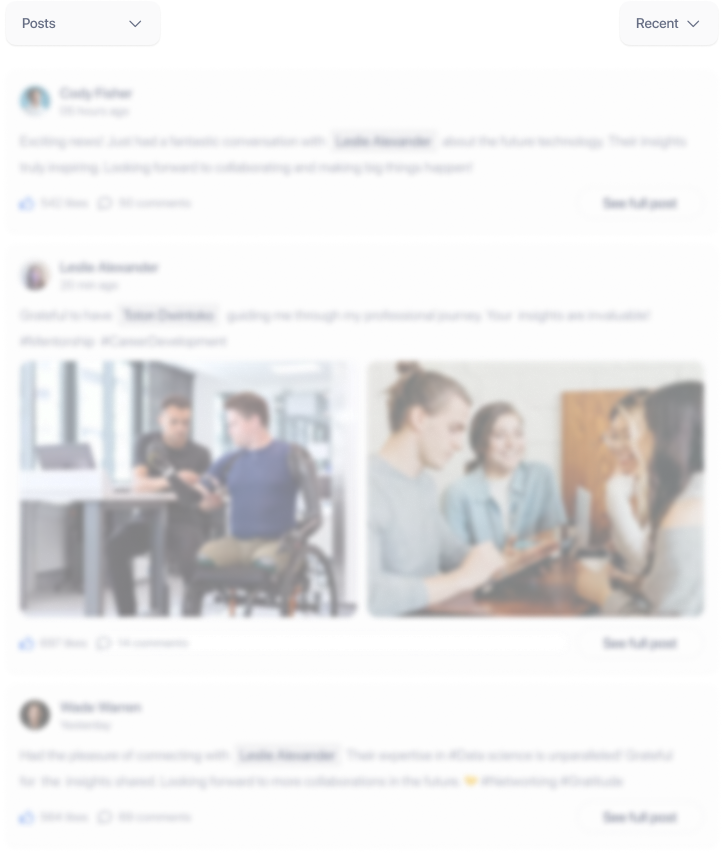