Brian Robbs
Training Coordinator at Transaxle Manufacturing of America Corporation- Claim this Profile
Click to upgrade to our gold package
for the full feature experience.
-
English -
Topline Score
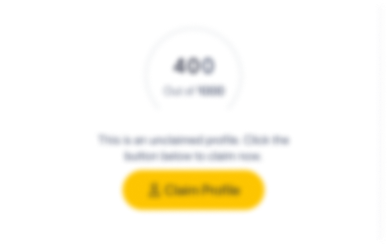
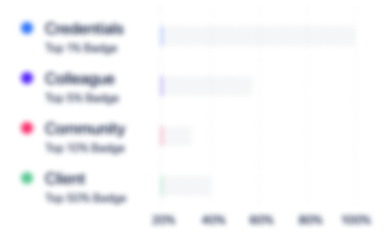
Bio


Credentials
-
Kaizan Leader Training
SCMEP -
Leadership For Leads 1&2
The Employers Association
Experience
-
Transaxle Manufacturing of America Corporation
-
United States
-
Transportation, Logistics, Supply Chain and Storage
-
1 - 100 Employee
-
Training Coordinator
-
Dec 2017 - Present
-
-
Material Flow Coordinator
-
Jan 2015 - Present
• Assists Logistics Manager and Production Engineering Group in the development and implementation of material flow project activities. Coordinates activities and resolves problems in the area of material flow to ensure meeting or exceeding internal and external customer requirements.• Maintains an internal Kanban process by enhancing the following processes:- Establish and maintain first and second locations for parts as needed.- Assist Production Engineering group in identifying kitting and lineside locations for all new parts- Establish tote quantities for all parts presented to kitting or lineside in totes.- Coordinate a repacking process for all parts not received from suppliers in proper packaging or size.• Identifies and drives improvements in all storage areas. Develop ways to increase efficiencies and utilize less space through improved storage methods.• Establishes inventory levels and replenishment strategies to support variable build levels while minimizing material handling costs for all parts kept at TMA. • Updates ERP system with all changes related to location, reorder points, replenishment quantities and all relevant information related to part maintenance. • Establishes and maintains locations for all raw materials that are machined at TMA.• Works closely with 3rd party warehouse to ensure TMA replenishment quantities are established using supplier packaging quantities where possible.• Reviews packaging issues and offer suggestions for improvements that can lead to more efficient ways of handling and storing parts.• Supports Engineering Change and PDP, and follows through with all part changes as far as setup and internal control.- Maintain labels for kitting and monitor racks making changes as needed- Create locations in kitting for new parts- Update ERP system with new part information- Remove obsolete inventory from racks• Performs audits to ensure inventory integrity within the barcode system. Show less
-
-
Utility Line Lead
-
Jun 2012 - Jan 2015
Over day to day operations of utility vehicle production line.• Transports specified material from storage to work area using proper procedures.• Reads and follows “standard operations sheet”.• Has been certified through TMA’s certification process.• Use of gages or other tools required for process control or validation of assembly process.• General assembly per electronic images or assembly instructions.• Operates assembly equipment including hydraulic press and test equipment.• Connects electric wires to terminals of subassembly.• Cleans and maintains organization of work area. Includes cleaning of machines, internally and externally, as required to maintain good operating efficiency.• Assists supervisor and process engineering in developing and implementing process improvements• Assists with associate training• Ensures compliance will all safety policies• Responsible for ensuring all quality standards are met• Assist with driving productivity improvements Show less
-
-
-
Tropical Foods (Tropical Nut & Fruit)
-
United States
-
Food and Beverage Services
-
1 - 100 Employee
-
Recieving Lead & Warehouse Lead
-
May 2008 - Apr 2012
-
-
Education
-
York Technical College
Machine Tool and Die
Community
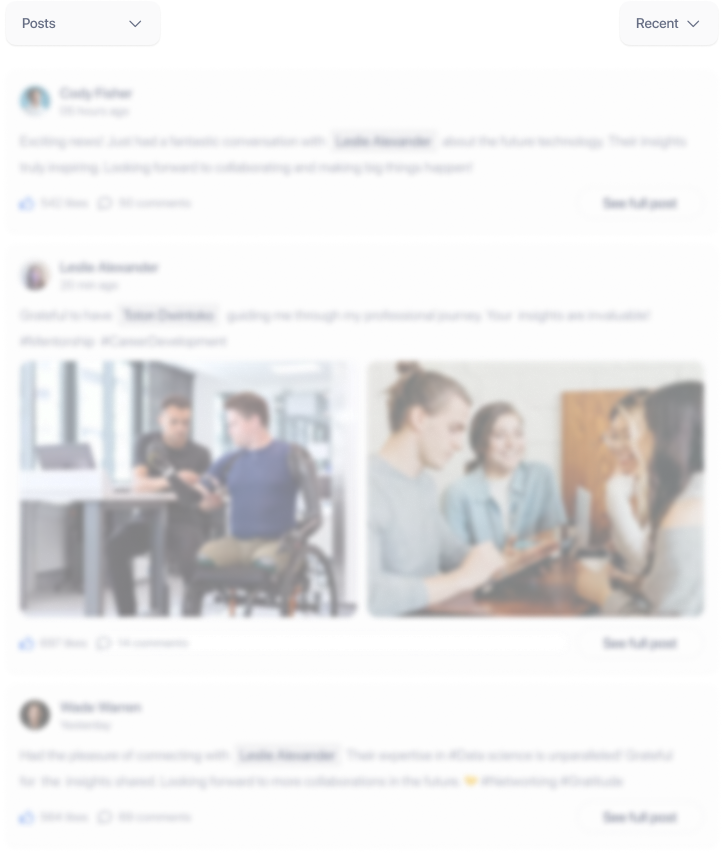