Brian Prost
Process Manager at OCL Architectural Lighting- Claim this Profile
Click to upgrade to our gold package
for the full feature experience.
Topline Score
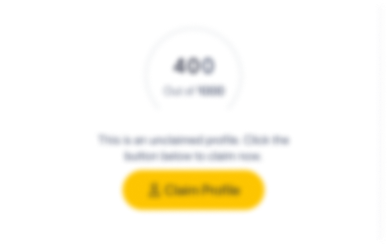
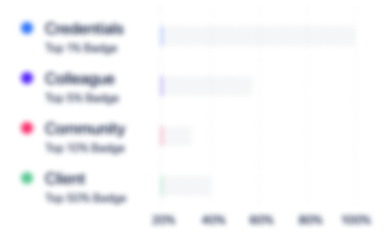
Bio


Experience
-
OCL Architectural Lighting
-
United States
-
Appliances, Electrical, and Electronics Manufacturing
-
1 - 100 Employee
-
Process Manager
-
Jul 2021 - Present
-
-
-
Amazon
-
United States
-
Software Development
-
700 & Above Employee
-
Area Manager
-
May 2020 - Aug 2021
-
-
-
Crucial MRO
-
United States
-
Airlines and Aviation
-
1 - 100 Employee
-
Production Manager
-
Oct 2019 - May 2020
-
-
Production Manager
-
Oct 2019 - Mar 2020
Crucial Unlimited, Wentzville Missouri October 2019 – March 2020 Aviation Repair Shop Production ManagerManaged the contract for United Express Business Class Aircraft CRJ-770 to CRJ-550 airplanes. This included production flow of repair and refurbishing of air craft interiors that included disassembly, body work, tedlar, paint and reassembly.• Implemented and created a process and procedure program in order to meet the airlines cutoff date for delivery • Created a more structured environment for continuous flow in order to meet contract deadlines and avoid loss in revenue • Managed 7 teams of 28 employees • Created a daily goal process for uninterrupted flow• Implemented continuous improvement across the facility and worked hand in hand with employees• Hired, trained and disciplined employees Show less
-
-
-
V. Mueller/ (BD) Becton Dickinson
-
Greater St. Louis Area
-
Production Supervisor / Production Planning
-
Feb 2015 - May 2020
Direct the production of surgical instruments in the machining area while achieving smooth assembly and delivering a quality product. • Daily direction and monitoring of production across Machining • Manage 21 employees distributed across 8 CNC Swiss Lathes, 12 CNC Vertical Machining Centers and various manual machining equipment • 2015-2018 successfully increased the overall machining production from 70,000 pieces per month to 110,000 pieces per month with the addition of fire suppression and ‘Lights-Out’ machining • Coordinate the utilization of CNC Lathes, Mills, manual machining areas, equipment, materials and employees to meet the performance objectives of the Machining Department • Continuously evaluate and make decisions to determine resource requirements, establish department cost savings projects, timelines, and resolve production problems • Participate in daily meetings with the production teams aimed at identifying and resolving process issues quickly to drive cost savings as well as quality and productivity improvements • Responsible for hiring, performance management and review, employee development, leadership and motivation of machining personnel • Responsible for capacity and machining scheduling process as well as leads the implementation of new capacity when needed • Maintained First Pass Yield targets in excess of 95% Show less
-
-
-
PLZ Corp
-
United States
-
Chemical Manufacturing
-
400 - 500 Employee
-
Production Manager
-
Sep 2013 - Feb 2015
Responsible for planning, directing and coordinating production to achieve smooth assembly and a quality product. • Strive to produce the best quality of product for customers • Coordinate with the Scheduling Department to ensure all raw materials are available in a timely manner so there aren’t any gaps in production • Discuss issues with the Maintenance Coordinator in order to make sure all equipment is running properly • Make certain safety processes are followed to minimize safety accidents – hold associates accountable for not following safety rules • Develop and implement SOP’s as well as standard work procedures while creating a training matrix for associates along with the collaboration of other managers on changeover checklists, return to stock procedures, and safety cards • Training of all associates • Handle performance reviews as well as disciplinary actions of employees • Create coaching sessions for performance improvement plans Show less
-
-
-
Cott Beverages
-
Netherlands
-
Food and Beverage Services
-
400 - 500 Employee
-
Operations Supervisor
-
May 2011 - Sep 2013
Supervise unionized hourly work force to ensure maximum efficiencies, inventory accuracy, and productivity levels. Maintain a safe work environment to strive for zero incident safety. • Supervise the daily activities of the workforce while monitoring performance, related to established goals. • Ensure that safety practices are followed to maximize productivity and minimize risk. • Perform periodic shift tours throughout the facility to ensure employee performance levels and audit ready status of the facility. • Conduct meetings with all employees, on the shift, to address upcoming events, hot loads, daily activities, performance from prior day. • Complete required paperwork, including Daily Schedule Controls, Observations, SOP Audits, employee absence reporting, and Production Reporting. • Write SOPs as needed. Show less
-
-
-
United Pet Group
-
Manufacturing
-
100 - 200 Employee
-
Production Supervisor
-
May 2006 - May 2011
Supervised and coordinated the activities of the production floor in the operation of a variety of machine’s that manufactured and produced an assortment of products within the realm of company and government policies. • Lead the facility in 2009 to achieve a new record of quality goods shipped. • Lead production teams in the practice and execution of safety, quality, productivity, cost improvements and employee development objectives. • Drove effective problem solving exercises within core and extended team. • Implemented continuous improvement initiatives to increase team and line performance, effectiveness and efficiency. • Deployed performance management principals and processes. • Worked with Technical Services to streamline changeover procedures, reduce changeover time and improve start-up issues. • Monitored and approved all time and production reporting - reconciled finished goods inventory at the close of each shift, prior to transition. • Managed staffing levels, overtime, and payroll approval. • Adhered to policy and procedure including safety, attendance and standard operating procedures (SOP). Show less
-
-
-
National Cart Company
-
United States
-
Retail
-
1 - 100 Employee
-
Production Supervisor
-
Apr 2005 - May 2006
Supervised a team of 25 associates on the Powder Coat Assembly lines. • Tracked daily production and inventory. • Collaborated with other members of management to develop and put into operation a lean working cell to manufacture a new product and capability. • Communicated daily with other supervisors for product scheduling and to ensure and overall safe environment. • Associate of the month August 2005 Supervised a team of 25 associates on the Powder Coat Assembly lines. • Tracked daily production and inventory. • Collaborated with other members of management to develop and put into operation a lean working cell to manufacture a new product and capability. • Communicated daily with other supervisors for product scheduling and to ensure and overall safe environment. • Associate of the month August 2005
-
-
Education
-
Ashford University
Bachelor of Arts (B.A.), Organizational Management & Health Care Administration -
Coldwell Banker Gundaker School of Real Estate
Certificate/Real Estate Licens, Real Estate Sales
Community
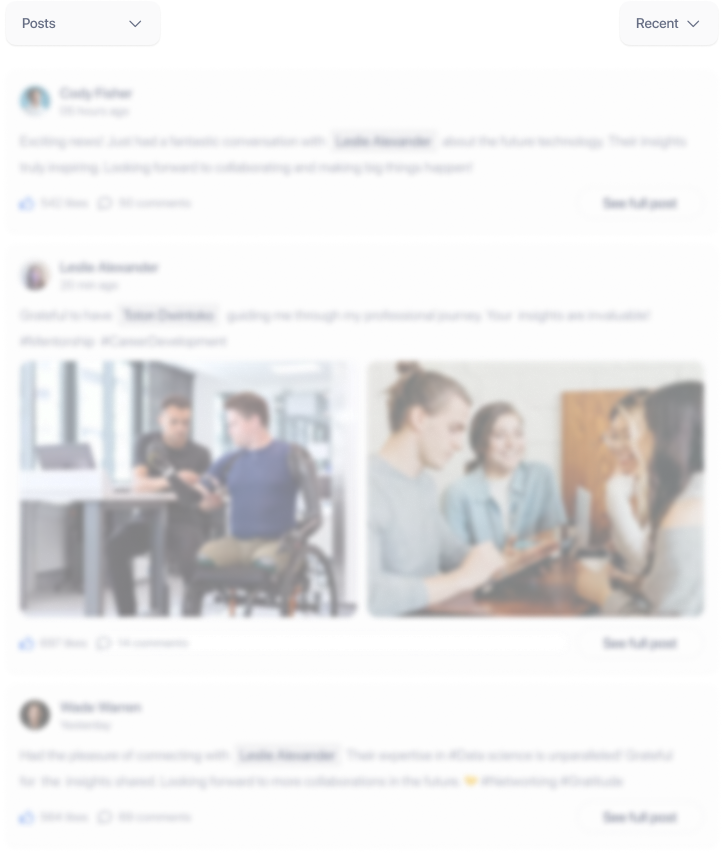